By Chip McDaniel, Automation Expert & Education Specialist, AutomationDirect
Human resources departments call the phenomenon the “grey tsunami.” They’re referencing an historic U.S. retirement surge of 4.1 million Americans a year. Manufacturing, in particular, is taking a big hit as industrial engineers, equipment operators, maintenance and repair technicians, plant managers, and others in supporting roles join those retirement ranks. With the sector accounting for about 8.5% of all U.S. employment, that implies nearly 350,000 people are retiring from manufacturing annually.
Meanwhile, reshoring manufacturing driven by the global, post-pandemic supply chain shortages as well as government initiatives such as the Inflation Reduction Act and the CHIPS Act are creating new manufacturing jobs faster than they can be filled. The Boston Consulting Group estimates that more than 90% of North American manufacturers have moved back at least some of their production or supply chain in the last five years, with even more planned in the next five years.[1]
Even with the help of advanced automation to shore up the loss of their skills and experience, the industry still needs trained people at every level, from the shop floor to the top floor, as the saying goes. And lots of them. In fact, the U.S. Census Bureau estimates that by 2030 about 2.1 million manufacturing jobs will go unfilled across the nation.[2]
Understanding the Manufacturing Skills Gap
Today’s manufacturing skills deficit is growing for several reasons. First, not enough young people are training to replace those retiring. Many seem to have little interest in working in factories due largely to misconceptions about the grime or danger associated with such jobs many decades before they were born.
Next, there seems to be a mismatch between what schools teach students regarding qualifications necessary for modern positions within manufacturing industry vis-a-vis actual demand placed on these workers by their employers today. That’s especially true considering breakthroughs made possible through automation and artificial intelligence (AI).
At AutomationDirect, we believe technologies such as these, along with data analytics, 3D digital twins, 3D printing, the Industrial Internet of Things (IIoT), and others, can make manufacturing careers much more interesting and rewarding. But as these technologies have found their way into manufacturing over the past decade, the gap between required knowledge areas in large-scale production processes has widened significantly. These days, companies also need individuals with traditional engineering abilities who are also proficient in data analysis or high-level programming languages such as C++, Python, Java, and others.
Such an elevation and expansion of needed skills is due to advancements in computerized systems, which have become integral to production, relying on specialized software embedded in hardware such as computer vision, robotic arm controllers, web servers, sensors, actuators, motors, pumps, and valves.
Augmented reality (AR) and virtual reality (VR) are also finding their way into plant environments, paving the way, along with robotics, to so-called cyber-physical systems.
At the same time, older technologies like pneumatics, hydraulics, electronics, electrical systems, control engineering, and power transmission remain essential and need engineers, operators, and technicians who know how to design, run, and maintain and repair such systems.
Close the Gap: What Manufacturers Can Do
Manufacturers are responding to skills shortages in several ways. One, of course, is using more automation or AI to handle tasks that needed human interaction and oversight before. While this approach can handle many repetitive manual tasks much faster and with fewer errors, it won’t replace workers altogether. Instead, it serves a complementary function by freeing up staff time for more strategic thinking around innovating processes and solving problems.
Still, to enact this model successfully, employee skills must change to become compatible with these new ways of working. It’s why many manufacturers have started investing heavily in retraining and up-skilling existing staff members who may find themselves using such tools in their jobs more and more.
Enrich Engineering and Other Plant Roles with Automation
For decades, automation has been associated with manufacturing job losses. But, at the same time, it has also opened new opportunities for engineers, machine operators, technicians, and other plant staff to enrich their jobs — an outcome that will continue — and to work more collaboratively than ever with greater operational visibility.
For example, engineers will always be needed to optimize process and discrete production models in terms of quality, efficiency, costs, and safety. While programmable logic controllers (PLCs) will remain a core technology in factory automation, next-level production optimization will increasingly involve big data analytics, algorithm development and machine learning, digital twins, AR and VR, to name a few of the technologies that are revolutionizing manufacturing.
They’ll also be using sophisticated tools and engineering methodologies such as computational fluid dynamics, kinematics modeling, and “cobots” among many others. Cybersecurity will also remain a high-level priority, not only because production shutdowns are disruptive and costly but also because they can threaten life safety inside plants as well as outside them.
Climate change is another area where engineers can use automation, for example, to support decarbonization efforts. Sustainable production practices that reduce energy usage and material waste will also demand sharp process engineering skills oriented toward innovation and supported by creative, out-of-the-box thinking.
Make the Most of Current Workforces
An important strategy that manufacturers are using to close the skills gap is workforce retention as well as upskilling and reskilling their current plant staffs. Skills required in manufacturing — engineering, operations, maintenance, and management — are continuously evolving as automation becomes more extensive alongside the other advanced technologies mentioned.
Upskilling. This refers to enhancing the existing value-adding capacities of plant employees so they can meet these evolving demands, especially as a plant adopts new technologies. Training courses aimed at improving digital literacy skills, data analysis abilities and automated system management competencies can help achieve this objective.
Reskilling. This involves training an employee on entirely different job skills after their existing skills have become redundant or not needed any longer within the same company or elsewhere due to the introduction of fresh approaches and systems into operations.
For example, a worker whose job requires manual “clipboard data gathering” could learn how to monitor and optimize automated systems. Or plant technicians who are accustomed to scheduled machine maintenance during planned shutdowns and break-fix repair models can study and help to implement AI-enabled condition monitoring of machine health that supports more proactive and efficient predictive maintenance models.
Retention. Of course, both upskilling and reskilling require personnel who are willing to learn new ways of doing their work. Plant management should work with their HR partners to assess each employee and, working with each one, develop continuous learning plans that can help advance their careers in meaningful ways such as more responsibility and compensation. The results will be greater job satisfaction and retention, the latter protecting the often-substantial investment a company has already made in an employee’s working tenure.
To these ends, AutomationDirect offers manufacturers a vast online collection of free training materials, such as our Learning Library, plus video tutorials and a YouTube channel to help engineers and technicians learn new skills. The latter provides specific solutions and how-to steps to complete complex tasks. Our free PLC Handbook is available for download to users who want a thorough introduction to this core manufacturing technology.
What’s more, we have partnered with InterConnecting Automation (ICA) to make hundreds of their PLC training videos available for free. ICA offers both training equipment and certificate programs through which trainees can be hands-on with a “PLC trainer” following the video instructions and completing tests at set milestones to earn the certificates.
Attract New Engineering Talent
Across the manufacturing sector, young engineers are invaluable to closing the industry’s skills gaps not just today but in the future. However, getting them involved can be a challenge and keeping their talents onboard once they’re hired can also prove hard. Competition for them will rise alongside growing demand for their increasingly sophisticated skills.
That’s why more and more manufacturers are creating new recruitment strategies to attract well-qualified candidates. Often social media platforms such as Twitter, Facebook, and Instagram are used where career opportunities can be shared widely among potential candidates who may not have seen them elsewhere.
Virtual career fairs have also emerged as an effective recruitment tactic that allows employers to interact directly with students from different universities, thereby increasing the chances of finding suitable recruits for their various job openings.
Another retention strategy would be through mentorship programs connecting experienced professionals in different fields/industries with upcoming talents, providing guidance and support networks through which they meet other people doing similar things, thus gaining additional insights into what is done best.
Encourage Aspiring Engineers in Higher-Ed – And Even Earlier
AutomationDirect supports numerous educational programs at the university level as well as at post-secondary technical schools and vocational high schools. We can provide instructors with product donations and generous product discounts so they can competently and confidently teach the many advanced technologies the manufacturing sector is increasingly using.
Available products include selections from our four PLC families, human-machine interfaces (HMIs), variable frequency drives (VFDs), servo and stepper systems, plus networking and fieldbus products. We also offer free software so instructors don’t have to deal with licensing restrictions or determining which of their school’s PCs will run certain copies of a particular software package.
They can simply install the software at will. But even more valuable, the students are welcome to install the software on their personal PCs, which can untether them from the lab to work on their projects whenever and wherever they want. They can then return to their school’s lab to test their code with actual hardware. Here are just a few of the free software packages available:
- CLICK PLC Software
- Do-more PLC Software
- Productivity PLC Software
- LS XG5000 PLC Software
- CODESYS Development System
In addition, AutomationDirect supports competitive robotics programs from the elementary grade level up to high school and college programs. Starting with sponsorship of a single high-school team in 2005, this program has grown to include over 200 teams in practically every school in AutomationDirect’s home of Forsyth County, a northern suburb of Atlanta with 42 schools serving over 55,000 students. And, earlier this year, we announced the winners of the FIRST Robotics Competition 2024 Digital Animation Award, which we have sponsored for many years.
We also support the state and national organizations which coordinate these types of competitions. Such programs excite students and give them a glimpse into the worlds of engineering, automation, and manufacturing. It’s an open secret that “building a robot” is a hands-on way to teach math, science, physics and other STEM (Science, Technology, Engineering and Math) disciplines in an extracurricular activity.
Students are flocking to these challenges. While we don’t expect them all to enter the field of robotics, any interest generated in scientific and related endeavors, such as STEM-related fields, is a plus. And many of the robotics teams are run like a business with marketing operations, accounting specialists, and fundraisers, plus the mechanical and electrical teams who actually design and build the ‘bots. So, there are many opportunities for students to learn valuable business skills in many other areas as well.
Conclusion: Creating Future-Proof Workforces
AutomationDirect would like to challenge readers of this article and their companies to get involved with these programs. Existing teams throughout the country can use your help and new teams can be formed very easily. Companies can support competitive robotics in many ways: cash sponsorships are always welcome. Some companies may be able to donate robotics and automation parts.
Perhaps most important are the mentors, coaches, and parents who assist the teams. Does your company have engineers who can mentor a few hours a week? Can your company allow mentors to be onsite at the school or at the offsite “build space” to coach and assist the students? Does your company have some extra office or warehouse space where the team could meet and build? These are concrete, tangible ways to get involved today, and their positive impacts on workforce development can be nearly immediate. At AutomationDirect, we employ many interns (both summer and afterschool) who are team members of these local robotics teams and have hired several after their college graduation. Programs such as these can also engage students who might not aspire to be degreed engineers, but they can certainly lend a hand on many engineering projects. We invite readers to join us in supporting workforce development across manufacturing to make the most of today’s talent and to cultivate the talent needed tomorrow.
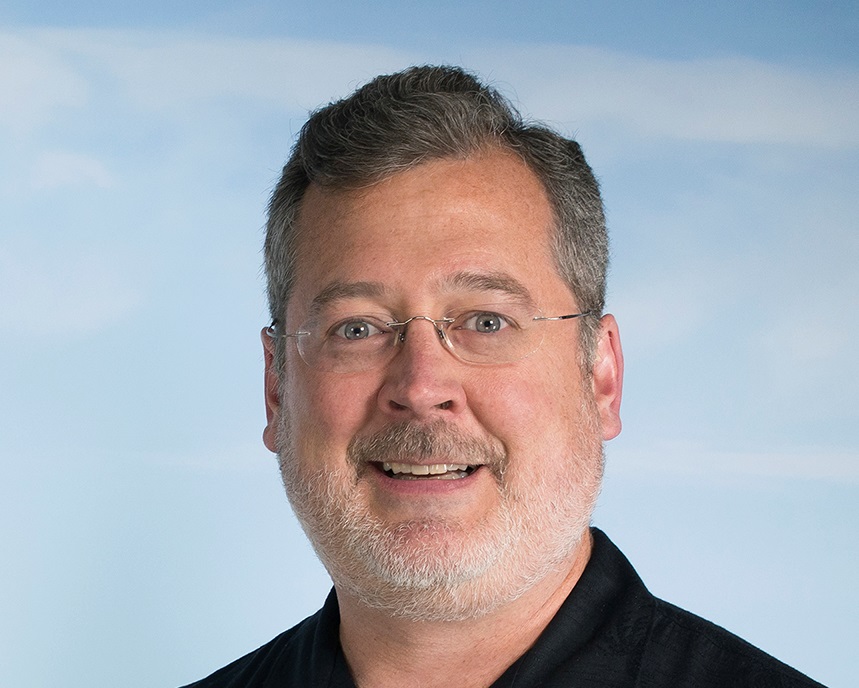
A 1990 graduate of the Georgia Institute of Technology, Chip McDaniel has a passion for education: “I handle the many requests our company receives for educational donations and assistance. I direct corporate philanthropic efforts with local, state, and national educational programs to promote STEM initiatives at all levels. Assisting students and schools is one of the most rewarding roles of my career.”
[1] More Than 90% of North American Companies Have Relocated Production and Sourcing Over the Past Five Years. Boston Consulting Group. September 21, 2023.
[2] Adam Grundy. Manufacturing Faces Potential Labor Shortage Due to Skills Gap. United States Census Bureau. September 29, 2023.