This student team gained valuable STEM experience by developing an underwater remote operated vehicle, and they accelerated their efforts by using commercially available industrial-grade components.
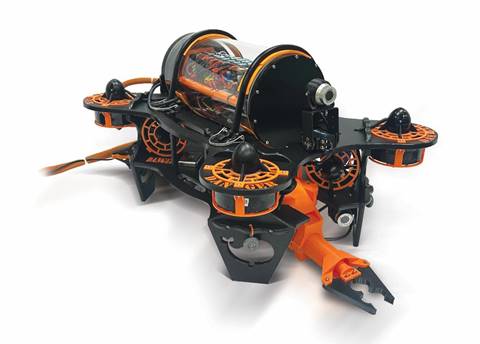
By: Geoff Gardener, North Paulding High School
Exploration of both the deep sea and of outer space share a lot in common. Both are extremely unforgiving environments where it is very expensive to create manned vehicles to carry out missions. As automation has become more capable, robotics and unmanned remote operated vehicles (ROVs) are used to execute much of this work (Figure 1).
Blue economy is a broad term given to any activities associated with developing and preserving the marine environment, covering activities as varied as fishing, aquaculture, renewable energy generation, mining, and more. Research organizations, salvage operators, the military, and commercial companies need ROVs to perform a variety of tasks in marine environments, and sending ROVs in place of human divers is safer. ROVs can be controlled remotely by human operators, and most will have some degree of on-board automation. Designing and building these ROVs is a specialized endeavor, combining mechanical, automation, and other skillsets.
To develop young talent to support this field, Monterey Peninsula College—via a grant from the U.S. National Science Foundation—has established a program called the Marine Advanced Technology Education (MATE) Center. MATE promotes marine engineering by inspiring and challenging students to learn and creatively apply STEM skills for solving real-world problems. This story relates how our team of students compete annually in MATE by applying industrial-grade technologies from AutomationDirect to develop their critical thinking, collaboration, entrepreneurship, and innovation skills so they can become part of the Blue Economy and other similar technology-based endeavors.
Whale of a Project
Part of the program is the MATE ROV Competition, which offers five different contest classes, each based primarily on skill and not strictly by age group. At North Paulding High School in Dallas, GA, a number of students make up the “WhaleTech” team. Some of them have participated up to seven consecutive years, starting in middle school.
Each year, the competition organizer publishes challenges and mock mission profiles simulating real-life conditions, with various restrictions. For example: dive to a pipeline simulation at a given depth, strategically remove a “bad” pipe segment, replace it with a new section, and bring the bad portion to the surface. The team builds a ROV to meet those challenges, and along the way they must act and present themselves as a professional company. They develop technical documentation, conduct research, select products, learn and follow safe practices, assemble and test the ROV and subcomponents, and even do a bit of marketing.
With a new mission each year, the team generally disassembles and uses part of the prior year’s robot. They build on previous successes, adapt to new requirements, and create new assemblies and mechanisms. Some assemblies are prototyped and custom-made using 3D printing, machining, and other techniques. However, just as the overall design is based on proven concepts to a great extent, the team also relies on commercial off-the-shelf (COTS) components where possible to avoid time consuming and technically risky experimentation. In fact, industrial-grade COTS components work very well in this service.
Immersed in the Details
Many ROVs look a lot like aerial drones, with propellers arranged to provide thrust in various directions. Just as aerial drones use propellers to provide constant lift and control motion, an underwater ROV does the same, but it can also use an additional mechanism to adjust its buoyancy. Cameras and lights are common on ROVs, and many also have robotic arms and manipulators to perform tasks. Many of the monitoring and control needs mirror the types of functionalities needed by industrial automation control systems.
For the 2024 competition, the WhaleTech team needed to develop a well-controlled ROV with an extensible gripper. The buoyancy mechanism, gripper, cameras, propellers, and other components would need to be supported and arranged in a chassis, which meant that some design effort would have to be in parallel and iterative to achieve the functionality and create an integrated form factor. As part of the process, the team used cardboard mockups and 3D printing, and then they created many structural elements cut out from high density polyethylene (HDPE).
The buoyancy engine is used to actively alter the buoyancy of the vehicle so the ROV can rise, descend, or stay at a fixed depth (Figure 2). It does so using a sealed cylinder to compress the fixed air volume, displacing it with water, which results in changing the overall density of the apparatus.
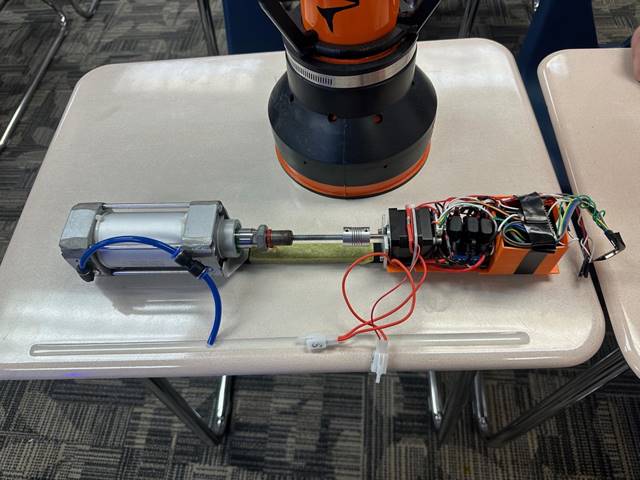
After selecting an industrial-grade cylinder, the team needed a powerful yet controllable way to actuate the piston portion via a linear screw drive mechanism. The initial idea was to spin the drive screw using a servo, which is powerful but can be costly. After some trial and error, and investigation of technologies readily available from AutomationDirect, the team found that a stepper motor could do the job admirably. A stepper motor can continuously turn in either direction and be commanded in increments as small as 1.8 degrees per step, driven by an AutomationDirect SureStep stepper drive commanded by an Arduino nano. A stepper motor draws no power when idle, it works well within the available power budget, and there is no rebound when the target position is achieved. The buoyancy engine is also outfitted with a pressure sensor used to store depth data into the on-board computer, and a wireless transmitter to communicate this information to the surface computer for a graph display when the ROV surfaces.
Similar design considerations applied to the gripper assembly, also known as the claw or manipulator (Figure 3). In this case, an AutomationDirect SureStep rotary stepper motor driving a screw shaft provides the motion to extend or retract a mechanism, which in turn opens or closes the gripper. Because this assembly must articulate, it is connected to the controller using a watertight flexible cable.
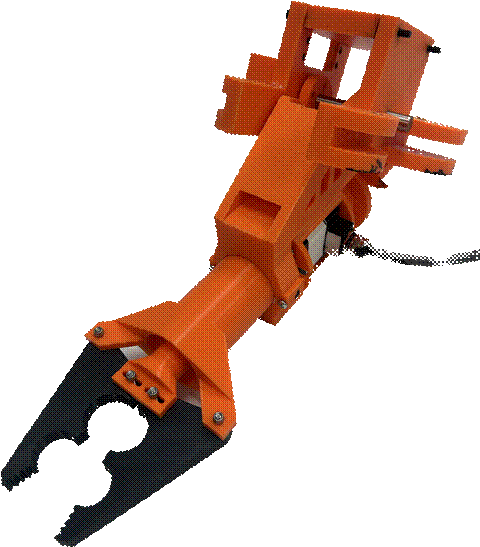
In previous competitions, the team had experienced issues with umbilical cables—running from the ROV to the surface—that were not flexible enough to allow precise movements in the water, or were insufficiently shielded and therefore susceptible to electromagnetic interference (EMI). To solve these issues, the team researched cables on the AutomationDirect website and found products with better flexibility and improved resistance to electrical noise. AutomationDirect offers a wide range of cables, available on spools and/or as cut-to-length.
Throughout the design process, the WhaleTech crew found the AutomationDirect website information and support team to be extremely helpful. They could rapidly browse through a wide variety of products, researching and discovering what would work best for their applications. Technical data sheets were only a click away, and a few times they used phone support to iron out other details.
Industry Advances Science
AutomationDirect has a long history of supporting student STEM efforts, and this underwater ROV project exemplifies just how important it is for industry to support education. The AutomationDirect portfolio of high-performance sensors, motors, controllers, visualization devices, installation components, tools, and much more has helped countless individuals, project teams, and companies innovate an incredible variety of solutions, while remaining within budget constraints.
As a result of their design and execution efforts, the WhaleTech team won first place in the Ranger class of the 2024 MATE ROV Competition. While some members are graduating and moving on to new work and educational endeavors, a new crew will assemble next year and work to build upon their successes.
All figures courtesy of North Paulding High School
Author Bio
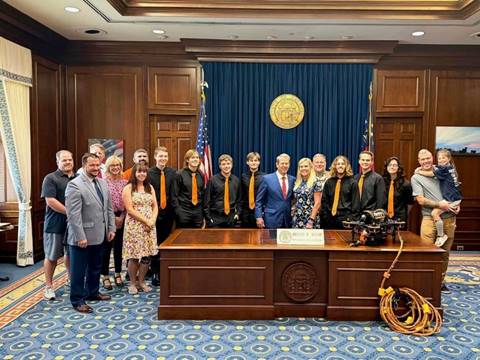
Geoff Gardener is a Geometry teacher at North Paulding High School, and the head coach and school sponsor of the WhaleTech team. Geoff, with the help of Rocco Leach who is an industrial automation engineer at a local beverage plant, leads the group of students forming the WhaleTech MATE ROV Competition team. In 2024, the team won first place in the Ranger class. After their victory, the team was invited to meet with Georgia Governor Brian Kemp at the State Capitol in Atlanta.