When automating machines or processes, picking the right controller hardware is important, and the application often drives the selection process. However, the programming software can make development, startup and operation easier—and is therefore an important factor in the buying decision.
Jeff Payne, the Automation Controls Group Product Manager at AutomationDirect, wrote an article titled How To Select the Right Factory Automation Controller for Your Application, which ran in the January 2018 issue of Control Engineering magazine. In the article, he explained some of the requirements to consider when selecting a controller for use in an application to ensure both the hardware and software are future proof. He also noted how the software programming platform can play a big part in the success of the project.
There are three families of controllers for machine or process automation: programmable logic controllers (PLCs), programmable automation controllers (PACs) and industrial PCs (IPCs). Many of the features and functionality among these controller types are merging.
“While the PLC was first to the game as a relay replacer, and it remains the best choice for small- to medium size-applications, its capabilities are growing as new technologies are adapted. Many lower-end models use ladder logic programming, which is sufficient for most applications. More expensive PLCs allow the use of function block and other IEC 61131 languages.”
PACs often have the extended capabilities required for some safety, motion and vision applications. The IPC does as well, and may be a better choice for advanced applications requiring the simultaneous use of multiple programming languages. Within each family of controllers, vendors usually supply a range of products.
“Regardless of which controller family is chosen, vendors offer a wide variety of controller form factors within each family, from small to medium to large. For example, AutomationDirect offers the Click, Do-more and Productivity family of controllers—with capabilities expanding as one moves from the top to the bottom of the figure below.”
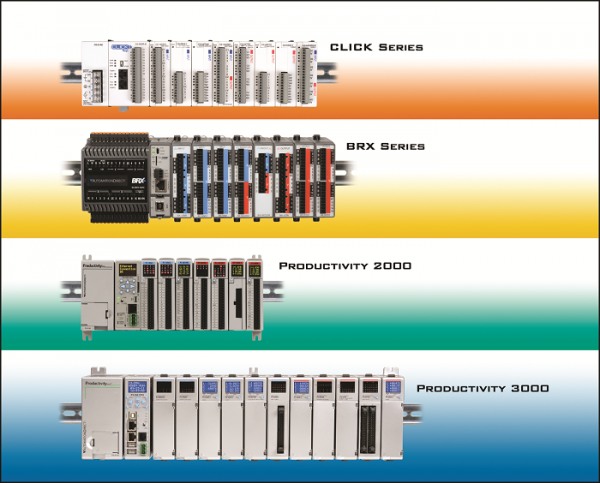
Controller Selection Thoughts
Payne points out that it’s not just the controller specifications that should be considered, but also the application requirements, along with plant personnel capabilities and future scalability (Table 1).
Table 1: Key Controller Selection Considerations
- Automation experience of plant personnel
- Number and type of I/O
- Required control functions: closed-loop PID, motion, high-speed, etc.
- Communication options
- Data collection requirements
- Special function requirements
Some facilities are more automation savvy than other, an important factor in the selection process.
“If plant personnel are new to PLCs, then a small and simple controller, such as an AutomationDirect Click, is a good choice. These types of controllers are the easiest to use, but can be easily expanded, and have many of the features of larger PLCs.”
Defining the Application
The first step is to carefully list all requirements, especially the more complex ones, such as motion control.
“In addition to discrete machine and analog process functions, some PLCs have evolved to perform complex tasks such as motion and PID control, such as this AutomationDirect Productivity 2000. This type of controller can handle complex applications such as precision motion for example a high-speed packaging line using registration alignment or synchronized velocity control with encoder feedback.”
Servos and variable speed drives may complicate things, so make sure communication to the drive to command speed, position or torque is available. Ensure Ethernet and the proper digital communication protocol are also available.
Data collection is a must in many applications.
“Fortunately, many controllers, even the new small PLCs, have not only communications built-in—but also data logging, web server access and email capabilities. The ability to write data to micro SD cards is another feature worth having in many cases, along with web server functionality and remote access.”
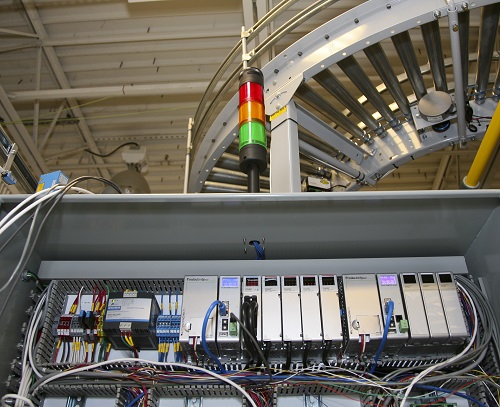
Software Selection Criteria
Typically, software programming takes about the same amount of time as the electrical design effort on an automation project. However, the programming software can have a big impact on the time and level of expertise needed to complete the project. Some controller programming software packages are easier to use than others. Consider the items in Table 2 when evaluating software.
Table 2: Controller Programming Software Considerations
- Ease of programming
- Preferences and comfort zone
- Time and money investment
- Training resources available
AutomationDirect’s Do-more Designer is a popular controller software programming platform for the line of Do-more PLCs. This programming environment provides ease of programming via extensive multimedia help topics to assist the programming effort.
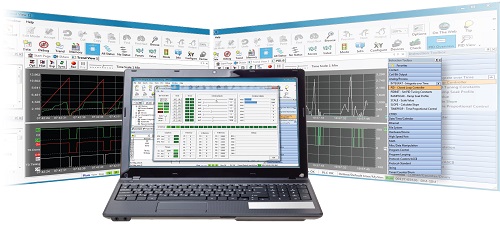
User manuals must exist online and be easy to access. The Do-more Designer software platform has over 130 videos embedded within it, along with libraries of technical information.
Testing is another important function, and capabilities in this area should be included in the controller programming software.
“The programming software should include the ability to view PID loop response and motion profiles, and to simulate other functionality in software. Built-in project simulators can be a huge timesaver allowing code to be tested without the hardware present or before being downloaded to an existing system.”
Spend the time to check out the hardware and software considerations. AutomationDirect’s web site is a great starting point because it contains information regarding all the hardware and software you need for a successful automation project for a wide range of applications and requirements.
AutomationDirect hopes this blog provided you a brief overview of controller considerations, along with the benefits of modern controller programming software. If you want to know more, check out our programmable controllers’ overview and software products’ overview.
To read more articles about programmable control, click here.