Modern PLCs and HMIs have empowered a big rig customization shop to create increasingly sophisticated automated lighting effects for their customers.
Byline: Dustin Dickerson, Dickerson Custom Trucks
“Less is more” and “function over form” are phrases often associated with the design of objects—anything from office supplies up to buildings or larger—to promote a concept of simplicity, clarity, and essential purpose. However, there are plenty of cases where most people would agree that “more is more.” This idea is often associated with personal expression, such as customized vehicles used to compete at auto and truck shows.
At Dickerson Custom Trucks, our big rig truck customization team works to fulfill our customer’s dreams, creating specialty vehicles that carefully strike a balance between creativity and reliability. Founded in Thorntown, IN in 2008, our projects originally revolved around metal work, painting, chrome, basic lighting, and other accessories. Sometimes the work involved upgrading existing equipment, but in recent years we have modified new trucks. Soon our clients were calling for more, so we began integrating electronics, specialty lighting, and automated control systems into their trucks (Figure 1).
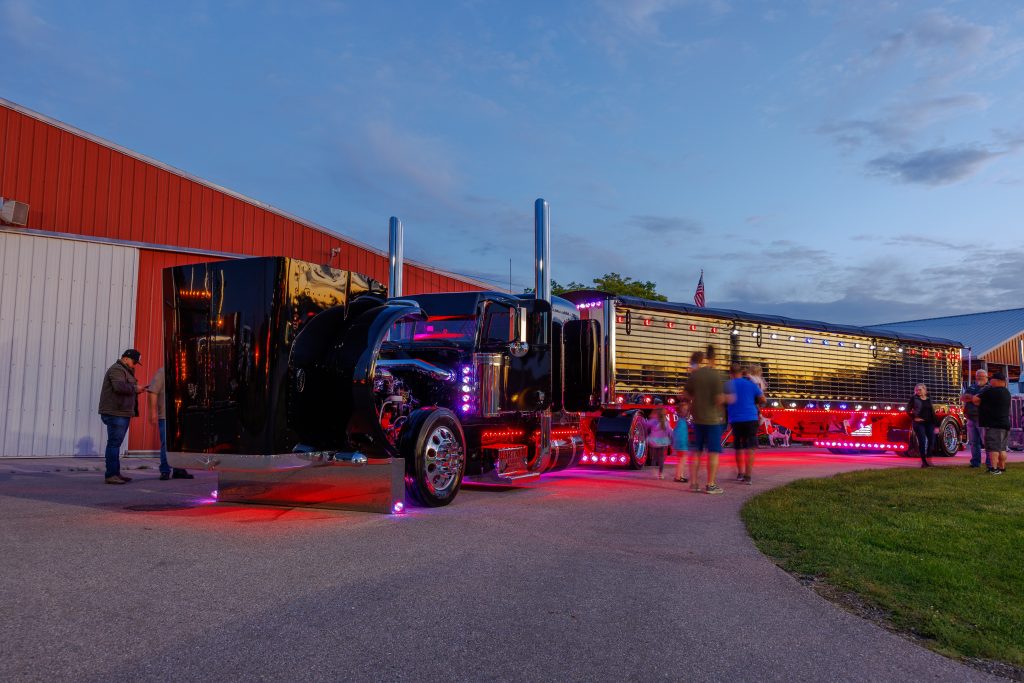
Some big rig owners use these customized tractors and trailers to compete in shows, and others like to promote their business with these highly visible rolling billboards. In any case, the demand for novel truck illumination and automation is surging, and our team is finding new and better ways to create increasingly sophisticated designs based on proven commercial off-the-shelf (COTS) industrial devices.
Upshifting Automation
Our first illumination automation projects were based on industrial-grade programmable logic controllers (PLCs), input/output (I/O) modules, and human-machine interfaces (HMIs). These products were new territory for our team, but we quickly determined that AutomationDirect devices and components had the right range of capabilities and price/performance ratios to meet our needs. AutomationDirect products—such as the CLICK PLUS PLC, C-more HMI, ZIPLink cables/connectors, Rhino power components, and more—were foundational so we could produce attention-grabbing light shows and automation.
We had deep experience with wiring and on-board vehicle systems, so we quickly learned how to cleanly install these automation devices in a control panel, and then install control panels on-board vehicles. Furthermore, the instructive online information, ordering portal, and phone/web support offered by AutomationDirect helped us get up to speed quickly.
The availability of low-power, high-brightness, truck-rated LED lighting from trucking industry suppliers has been a key enabler for performing this work. Our original projects might automate about 100 to 200 lights per vehicle side, creating a choreographed light show. Using PLC ladder logic and drum sequencer instructions, we created multiple types of light shows, with nicknames like chase, knight, pong, flip, race, and more, all selected via the HMI. These innovations helped our clients win shows and achieved plenty of recognition, and it didn’t take long for the marketplace to ask how we could take things to the next level.
More Power
An upgraded lighting automation design would require more, of everything. We wanted not only more colors, but more colors per light fixture. We needed more lights, and the ability to individually control more of them with more I/O modules. We needed to program more PLC sequences, with more complexity. And we needed more options for the HMI user interface.
The first step was to create our own light fixture. Previous projects had used COTS button lights commonly available to industry LED lights—LED versions that are far better, brighter, and more energy efficient than traditional incandescent versions—which could operate in common red and amber Department of Transportation (DOT) colors in dim or bright modes. These lights could also have one alternate non-DOT color—such as green, blue, purple, pink, or white—which is used only when the vehicle is not operating on public roads.
For new projects, our team developed a novel “watermelon” light assembly, which could still operate in a basic DOT mode, but could also be used in a show mode with multiple colors. Our first example provided the necessary brightness with pairs of red, white, and blue LEDs, all driven by individual signals for a total of three PLC outputs, per light. This color arrangement was selected to support the theme and name of the rig, which is “American Dream” operated by Hartman Farms.
To drive the lights, we needed far more I/O than before, and this time we wanted to avoid expense and space consumed by interposing relays. Therefore, we moved up to an AutomationDirect Productivity2000 PLC, with one local 11-module and two remote 15-module groupings (Figure 2). This gave us about 41 discrete output modules, and we selected the 15-point versions which can drive 1A per point at 12VDC, plenty of power to directly drive the LED lights. ZIPLink modules and cables provided a compact and organized way to terminate the 45,000 feet of wire routed throughout the rig. Two compact control panels were designed and built. The main PLC panel is housed on the truck and has one local rack of I/O driving the truck lights, while a second panel for remote I/O is located above the trailer axles to operate the trailer lights. An Ethernet cable connects the two panels.
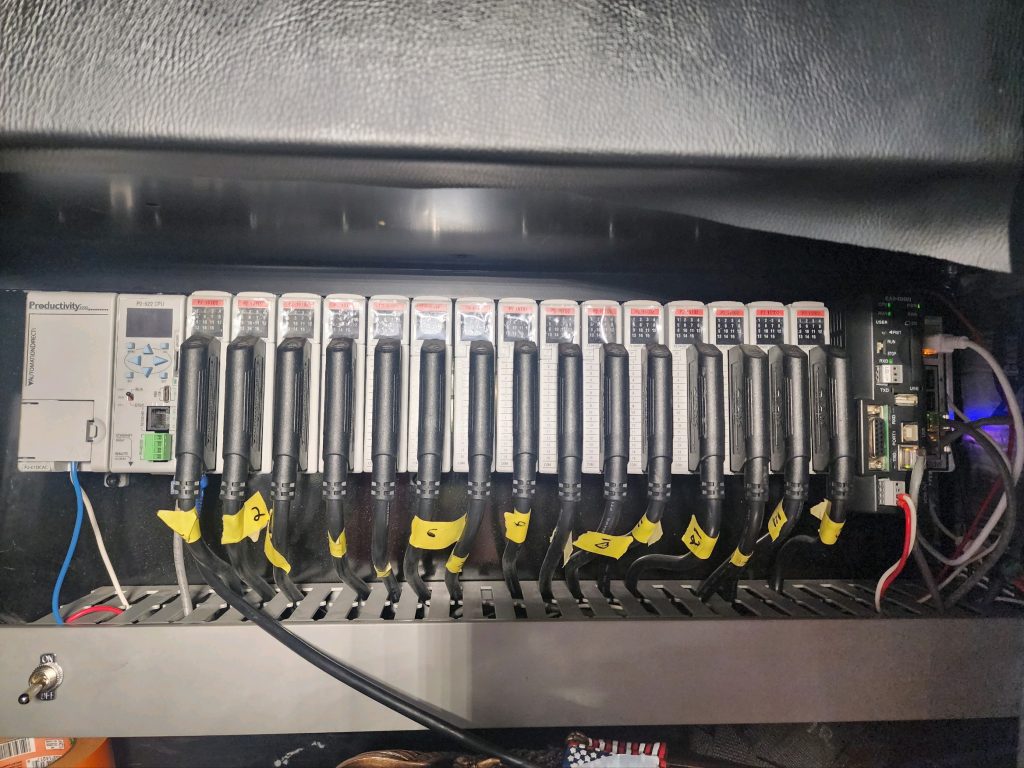
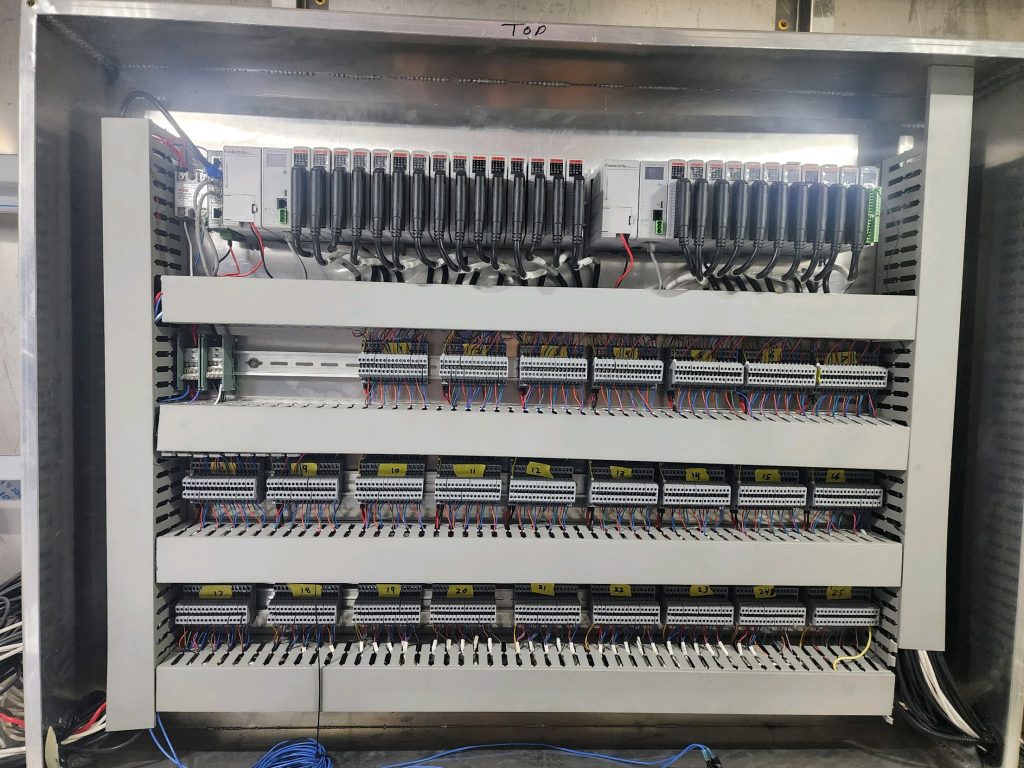
Combined, we now had 615 discrete outputs to drive lights. Because each output is wired to run four lights (mirrored in pairs on the left/right of the truck and trailer), we are effectively automating 2,460 lights. Everything we had learned on earlier systems using AutomationDirect CLICK PLUS PLCs directly applied to the programming in the Productivity2000. There are many lighting patterns—which could also be called sequences or shows—which operate the truck and trailer lights in various ways. The operator can choose a single show, or a cycling combination of many shows.
Getting the Show on the Road
With so many operating options, we knew we needed to provide an enhanced user experience beyond a typical fixed HMI localized in one spot. Therefore, we selected an AutomationDirect C-more EA9 series “headless” HMI, in conjunction with a Wi-Fi router. The headless HMI can operate a local display or touchscreen, but we chose to configure an iPad with the C-more app, so the user can control and monitor all the functionality from anywhere in or around the rig (Figure 3).
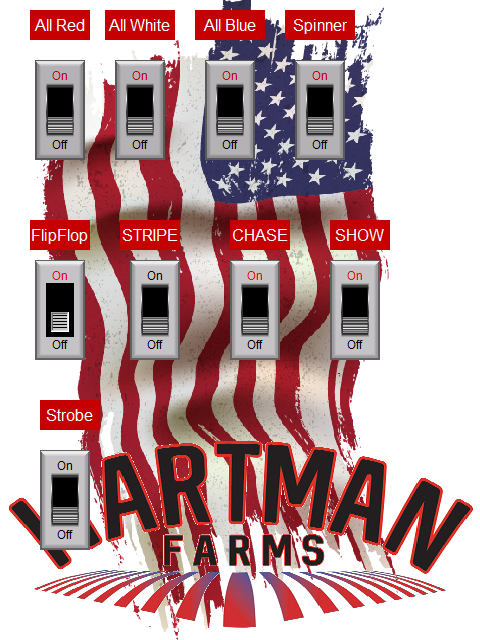
Wireless connectivity is also convenient for our team to connect with the PLC and HMI for development and testing. As a future upgrade, we are considering the use of an AutomationDirect StrideLinx VPN router with cellular connectivity so we can support our customers anywhere mobile data service is available, and perhaps exploring web browser connectivity.
Fast Lane to the Future
Dickerson Custom Trucks was founded in the physical metalworking, assembly, and painting of big rigs. Moving into digital controllers, user visualization systems, and the associated programming and configuration of these devices was initially a leap for our team. However, to deliver on our “built, not bought” motto for our customers, it was essential that we pursue all avenues of innovation.
When we initially investigated our options and selected AutomationDirect as a prime supplier, we were rewarded with a quick learning curve and impressive results. Using AutomationDirect PLCs, HMIs, and other devices to automate truck lighting is not the normal application for these products, but they excel in our application. Furthermore, the range of products in the portfolio has supported our work to execute bigger and better projects.
Our team will continue to refine and expand the capabilities of big rig automation. Future projects will move into the truck cab, providing extensive on-board control and monitoring via a dashboard interface. AutomationDirect is an outstanding technology partner for our team, and it has empowered us to accelerate our customization work into entirely new areas for producing industry-leading truck customization.
All figures courtesy of Dickerson Custom Trucks
Author Bio

Dustin Dickerson is the founder and owner of Dickerson Custom Trucks in Thorntown, IN. He has been in the truck building business for about 15 years and welcomes the opportunity to create innovative designs with his clients.