A team of students at the UMass Amherst College of Engineering recently completed a capstone project to allow remote monitoring of a wind turbine. This team of mechanical engineering students consists of five students, each with an area of primary responsibility: Jay Sant; Team Lead, Ryan Sullivan; Design Lead, Thomas Haley; Analysis Lead, Jack Drummond; Evaluation Lead, and Bennett Macgregor; Fabrication Lead. The project was partially funded with a sponsorship through the National Small Wind Turbine Research Project coordinated by REpowering Schools. AutomationDirect was pleased to be able to provide most of the industrial control system components for the project.
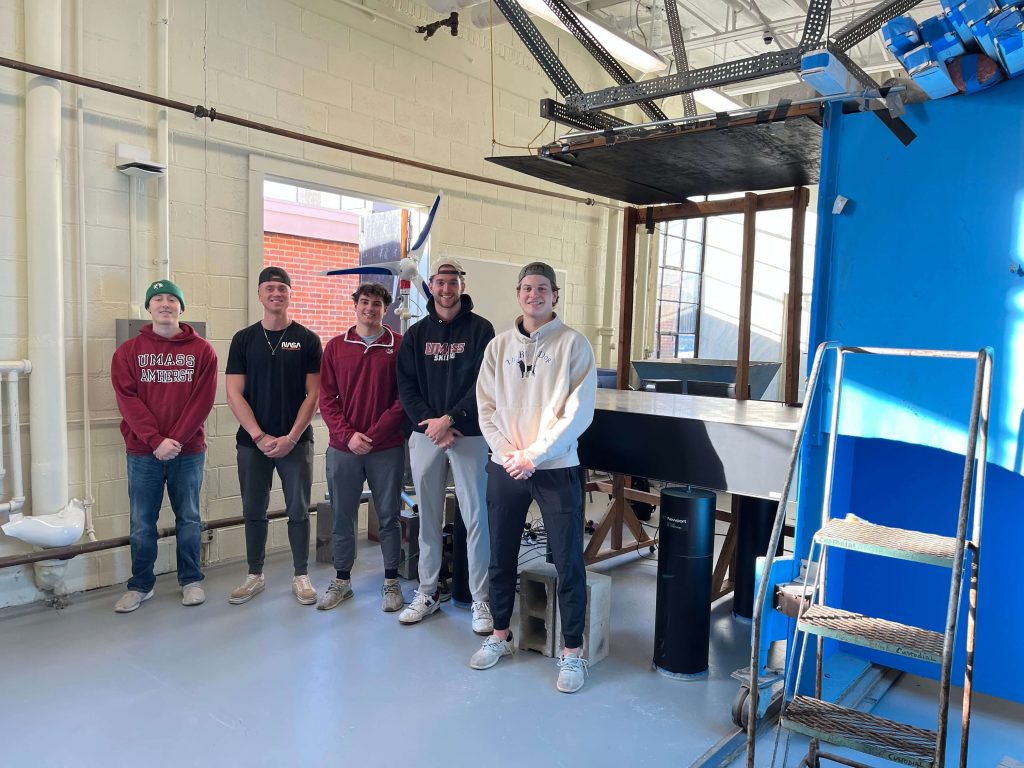
The team’s objective was to use industrial commercial-off-the-shelf (COTS) components to develop an autonomous data-logging system to remotely monitor, test, and evaluate small-scale turbine performance and operating conditions. They point out that wind turbines experience frequent maintenance needs due to the large number of mechanical and electrical components and often a harsh operating environment. They are confident that a remote data-logging system will enable scheduling of predictive maintenance, and eliminate the need to be on-site to conduct testing, reducing both travel time and costs.
The team started with a commercially available wind turbine from Primus Wind Turbines. The unit is capable of producing roughly 90 amp-hr per day with a 12 mph average wind speed. The wind turbine output is fed to a 24VDC battery pack. This self-contained, self-powered system is then also used to power the remote monitoring system. A Rhino® DC-to-DC converter is used to assure constant 24V supply to the control system even as battery voltage varies considerably depending on the level of charge in the “pack”.
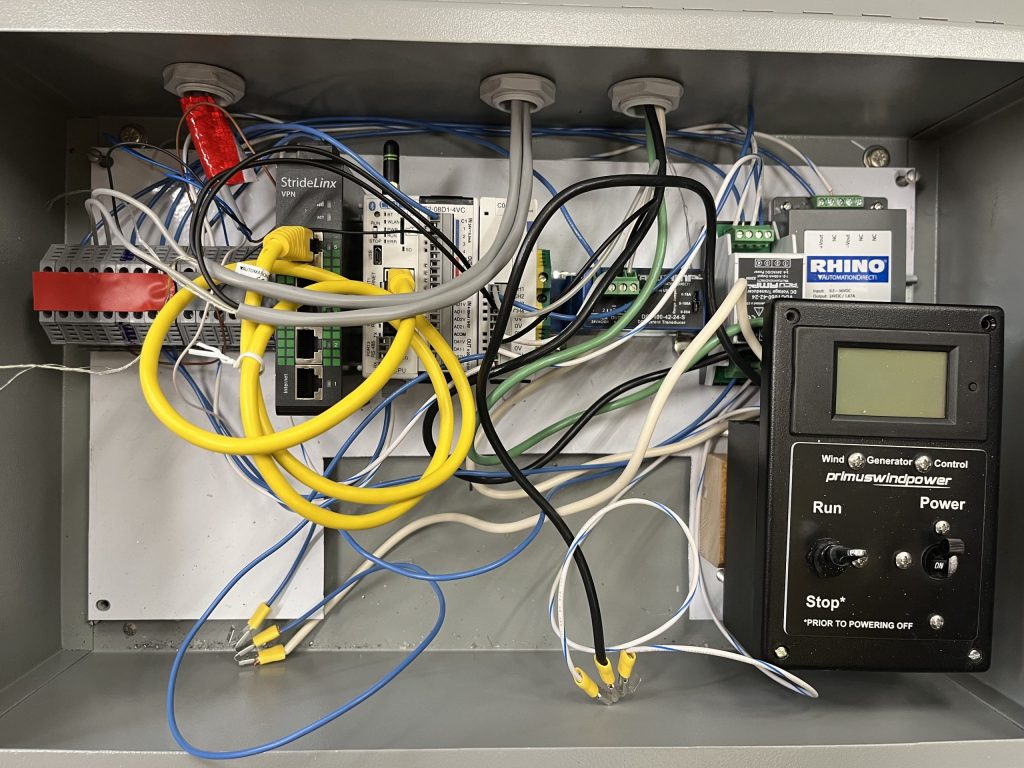
The team specified and procured several sensors to provide continuous feedback about the performance of the system. A discrete photoelectric sensor is used to read the speed of the turbine, with a pulse rate of once per revolution. An anemometer also provides a discrete signal when the wind speed is within the “cut-in” and “cut-out” range (7mph and 90 mph, respectively) of the wind turbine. Analog signals (4-20mA) are obtained from an accelerometer attached to the turbine shaft as well as from an AcuAMP® current transducer reading the electrical output of the turbine and an AcuAMP® voltage transducer reading the level of charge in the battery pack.
These sensors all feed data into a CLICK PLUS® PLC from AutomationDirect. The CLICK PLUS® is a low cost, easy to use PLC, which has been configured with a ‘CPU option slot module’ to handle the discrete signals and has a ‘stackable I/O module’ to accept the analog (4-20mA) signals. The CLICK PLUS® is connected via a point-to-point Ethernet connection to a StrideLinx® Pro industrial VPN router (SE-SL2011) also from Automation Direct. Along with a remotely mounted antenna, the StrideLinx® router provides a wireless-cell-tower-bridge to the internet – with a low-cost, monthly fee based on the number of data points uploaded per hour. This simple VPN connection allows anyone with the IP address and proper credentials to remotely monitor the system from any location that has an internet connection (browser based). The students routinely access the data (i.e. to demonstrate their project) via their cell phones.
To verify performance of their remote monitoring system, the team utilized a vintage wind tunnel located on the Amherst campus to gather precise measurements of the system at various wind speeds. As a sanity check, the students started by verifying readings from the monitoring system with the factory specifications of the turbine – and the readings were within the expected tolerances. The wind turbine also shipped with a local readout, which displays real-time data – and the data available over the StrideLinx router shows complete agreement with the relevant power measurements from that device (within +/- 5%) – at all the wind speeds possible in the 1970s-era wind tunnel.
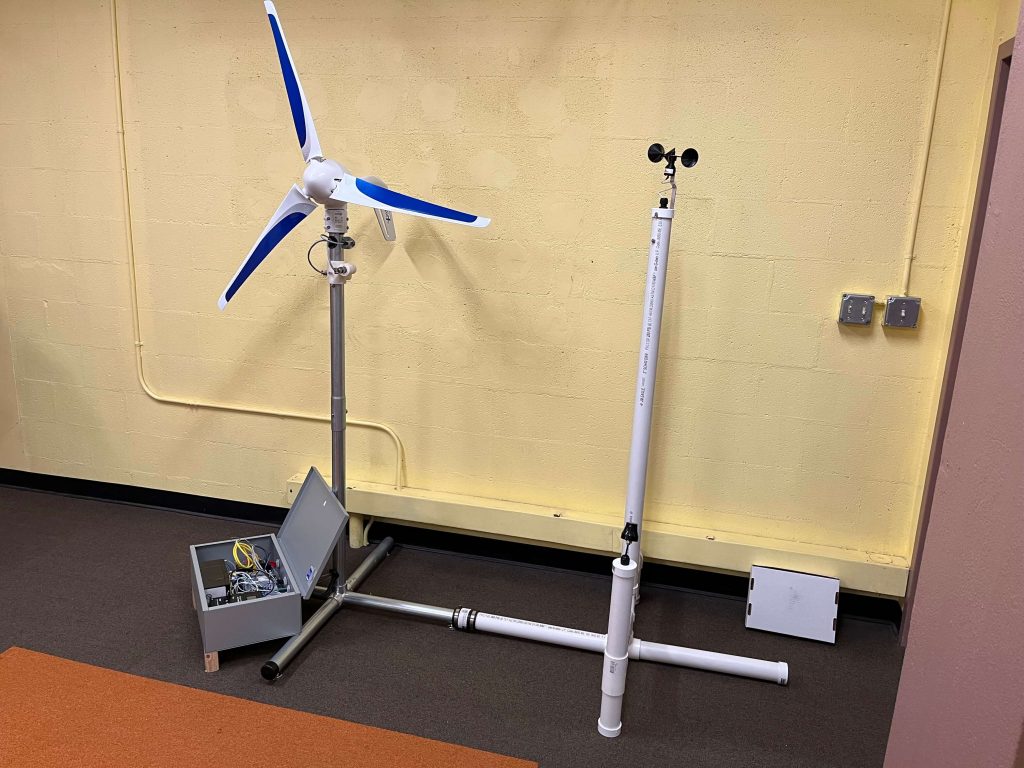
The team presented their fully-functional system at the annual MIE Senior Design Showcase and Competition at UMass Amhearst at the end of the 2022 fall semester. Each student team’s work was evaluated by eight judges from within the Mechanical and Industrial Engineering (MIE) department, additional UMass faculty, and by local business leaders and entrepreneurs. The judges scored the teams on their ability to capture the needs of their customers, convert those needs into engineering specifications, apply engineering analysis to generate multiple designs, and choose an optimal design. These semester long projects also required fabrication of the design and evaluation of how well the prototype met the original customer needs.
The wind turbine team won first place in the competition.
As of this writing, the team (along with their sponsoring professor: Jim Lagrant) are traveling to the Distributed Wind 2023 Business Conference in Washington, DC to present their project to a national audience.
The Mechanical and Industrial Engineering department at UMass cultivates strong relationships with industry to offer real-world challenges for its Senior Design Project course. To learn more, please contact Jim Lagrant, Professor of Practice in Manufacturing: jlagrant@umass.edu.