Applying the right barcode, RFID, and vision technologies addresses the increasing demand for data-driven manufacturing, improved quality control, and compliance with track-and-trace requirements.
By Larry Reynolds, AutomationDirect
Automation systems routinely use a variety of sensors to detect the position, motion, weight, and many other physical characteristics of products and other targets. This type of monitoring is essential for controlling the associated equipment and machinery. But increasingly, it is becoming just as important for tracking and traceability purposes to more thoroughly identify target items and provide supplementary information. This type of sensing requires more specialized detection devices and supporting software.
Extended identification information can be accessed in a variety of ways, including barcodes (both 1D and 2D), radio frequency identification tags (RFID), and vision systems. These technologies are widely available throughout the commercial and manufacturing sectors, but when they are used for industrial applications, it is important for designers to select products adapted for these challenging environments. Another consideration is that in past years there has been significant cost and complexity to implement these technologies, but those barriers are now significantly reduced.
Fortunately, the latest industrial identification technologies for barcode reading, RFID, and vision systems, are now packing advanced capabilities into compact, economical, and easy-to-use form factors, making it practical to add these functions to more applications.
Identification Essentials
End users, systems integrators (SIs), and original equipment manufacturers (OEMs) are finding an increased need to use identification technologies to identify items they are handling, and to obtain additional quality control information.
Manufactured or transported goods may have barcodes or RFID tags directly on them, or on the equipment moving them, which can be used by the automation system to track, direct, and event-log their motion through a process. Typical barcode and RFID identification systems require tags or markings—which are available in a wide variety of formats—affixed to the target product or component. They also need a device capable of reading the tags, and a way to communicate that information to a supervisory system for processing or association with a database.
Vision identification systems may be used to read barcodes, but many versions are capable of much more advanced inspection functions for quality control and other purposes. Some vision sensors can perform image processing on-board, while others require more complex external systems. Camera and visual processing capabilities improved in recent years, and it is now very common to use vision systems for detecting the alignment, size, color/quality, labeling application, and even the orientation of parts of the target, such as a cap or a subcomponent.
Applying identification technologies for industrial applications—whether on a machine or elsewhere on a manufacturing line—requires designers to address several physical installation aspects. The targets must be oriented properly, sensors need to be mounted at the appropriate distance but protected from vibration and mechanical damage, and acceptable lighting is needed. Some devices may be hardwired to associated control systems, but more commonly the sensors will use industrial communications protocols over a network connection because of the type and volume of data which must be transmitted.
For these and other reasons, identification systems have historically been costly, complex, and difficult to integrate, especially for vision-based technologies. The latest generation of technologies has overcome each of these problems, enabling end users, SIs, and OEMs to easily incorporate identification capabilities into any machine or system.
Detection Details
Several advances in the identification space have made the technology more accessible. Sensing devices have become more compact, with improved on-board processing, and connectivity over common Ethernet using standardized protocols. This makes it far easier to install the sensors, wire them to the host system, and take advantage of PC- and browser-based tools to configure, commission, integrate, and maintain them. The following are some specifics about various technologies.
Barcodes
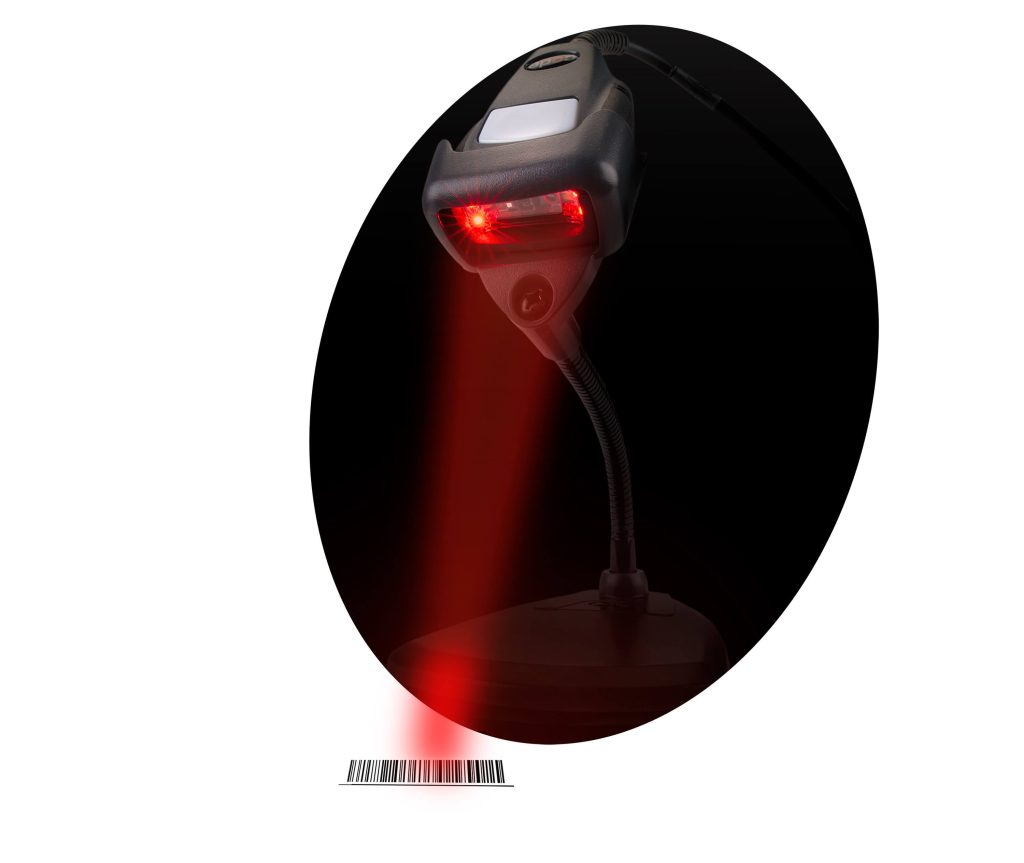
Barcodes and their associated scanners are probably the most typical industrial identification systems (Figure 1). A barcode may be printed on a label or product, or even engraved or embedded on a target. Laser-based scanners were originally the most common, but today optical-based version—which effectively take a picture of the barcode and then analyze it—are very capable but can be more susceptible to lighting issues and dusty conditions. Handheld scanners can be used by workers for production or spot-checking purposes, but machine-mountable form factors are typically used for industrial manufacturing applications.
Because the barcode formats and communication protocols are largely standardized, designers should look for suppliers offering a range of form factors to meet their needs. Handheld barcode scanners are available in both general- and rugged-duty versions, with selection depending on the environment where they will be primarily used. For machine-mountable versions, designers should consider scanners with:
- Built-in lighting
- An alignment laser and autofocus system to simplify setup
- Various communication protocols
- Free configuration software with wizards and one-touch teach capability
- An onboard logic engine to perform a degree of data pre-processing
RFID Tags
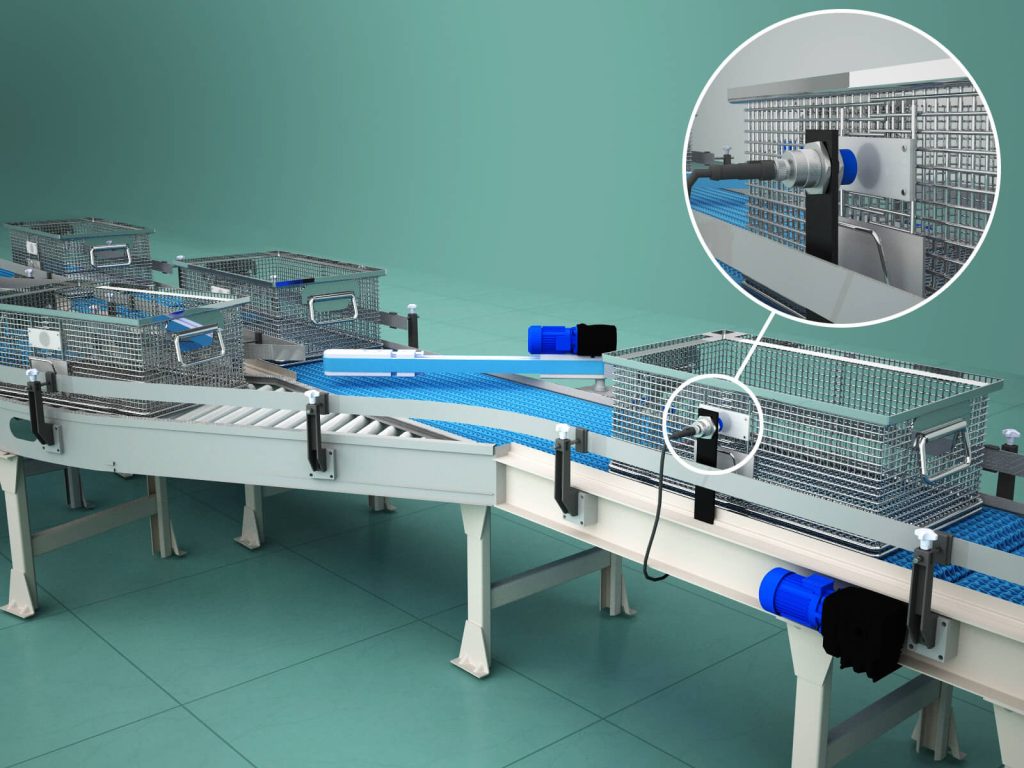
While barcodes can be used on actual portions of operating equipment, such as product carriers or tooling, an RFID tag offers some additional advantages because it has both fixed and user-accessible memory (Figure 2). Therefore, the tag can carry a static serial number—similar to the license plate of a car—and the user application can also read/write dynamic data as the tag goes by a scanner. This, for instance, can be useful to record what the equipment is carrying as it is loaded, or to identify when it is unloaded.
Designers need to recognize that RFID read/write transceivers must be located within an appropriate distance to the tags they will interact with. This distance requires thinking about many factors such as the surrounding environment, the technology and frequency of the device being used, antenna sizing, and installation geometry. Read/write modules are available in many different housing styles with various environmental protection ratings. As with barcode readers, an industrial protocol such as EtherNet/IP is now common, and the IO-Link protocol is also a newly popular connectivity option.
Vision
Vision is where the greatest identification technology gains have been made in recent years (Figure 3). The earliest systems required expensive and finnicky cameras, connected to dedicated PC-based systems. Certainly, these high-end systems continue to be improved and available. But there are newer categories that can fulfill many of the most common manufacturing requirements:
- Vision sensor: An intelligent self-contained device that can be taught to recognize images representing proper target qualities. In normal operation, the vision sensor acquires a target image and compares it in real-time with the baseline image, providing a pass/fail or good/no-good result, or even making more complex decisions. These types of sensors are ideal for verifying fill level, cap orientation, label presence, and/or color.
- 2D camera: A device with high-resolution sensor and associated lighting, optimized to capture images which are used to reliably perform inspection—including quality aspects such as contours and “blob analysis”—to determine shape features such as presence, number, size, and location of elements. These capable cameras can do much of the work that previously required much higher-end devices.
- 3D vision sensor: A device that applies time-of-flight or similar point technology from the sensor to the image to measure the distance of numerous points within the field of view. This type of sensor can be used to determine the volume and surface area of a target.
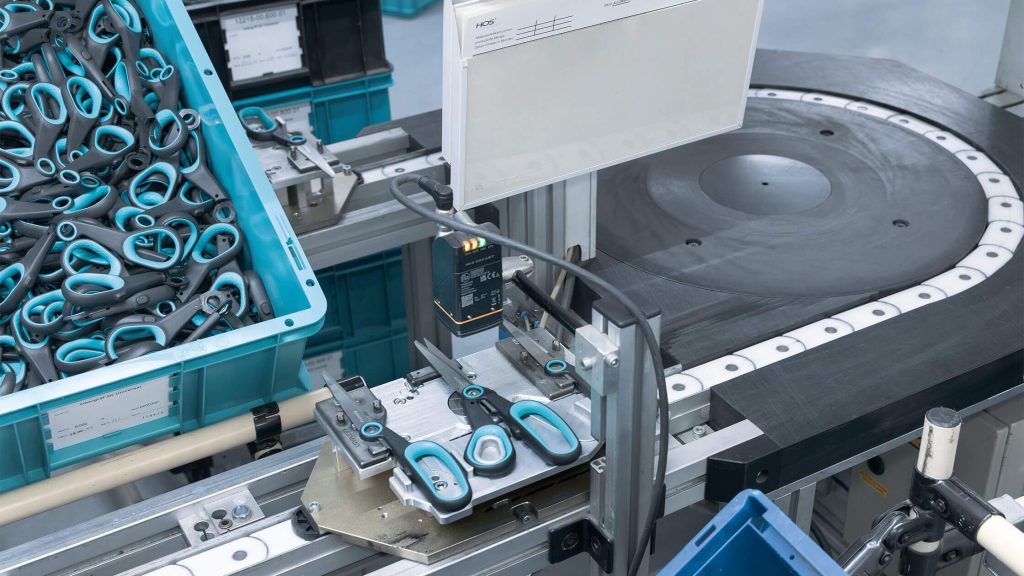
Accessible Identification is within Sight
With the increased demand for data-driven production, product specialization, and improved manufacturing tracking/tracing, industrial identification has become fundamental for machine and processing automation. Barcodes, RFID tags, and vision technologies are all proven ways to carry out a variety of identification tasks, and each offers certain performance benefits depending on the application.
In particular, barcoding and RFID tagging are very mainstream at this point, but vision systems for industrial applications have expanded their reach greatly in recent years. Developments of the past few years mean that a wide range of vision capabilities are now much more accessible for all types of end users, SIs, and OEMs.
Designers will benefit from working with suppliers who offer all these technologies, along with associated accessories, such as brackets, cables, and lighting. With a range of options at hand, it becomes more straightforward to apply the best-fit identification products to meet the price and performance demands of any application.
All figures courtesy of AutomationDirect
About the Author
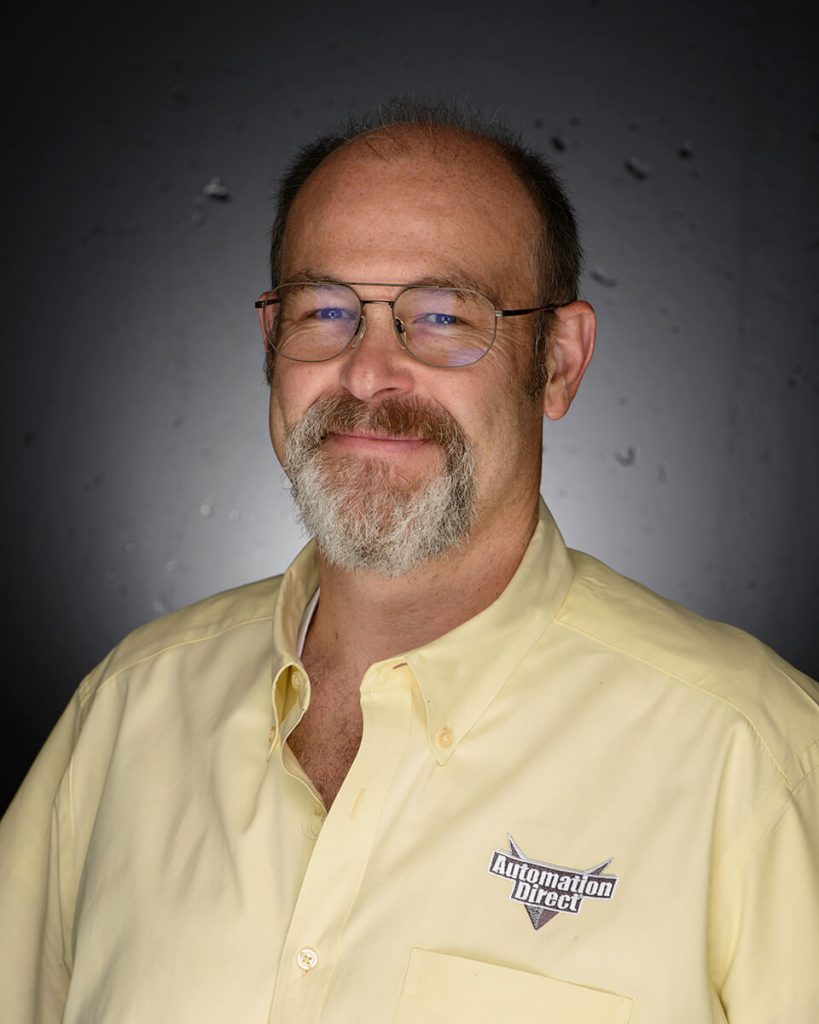
Larry Reynolds, Product Engineer, Safety Components, AutomationDirect
Larry Reynolds is a Product Engineer for Safety Components at AutomationDirect and started his career over 30 years ago. He has served in many industry roles such as technical specialist, radiation safety officer, plant safety officer, project manager, control designer, and system integrator, and has also specialized in safety applications for automation systems. Larry holds a Bachelor of Engineering degree, is a certified PMP (Project Management Professional) and holds a Functional Safety Engineer certificate from TÜV Rheinland, #15983/18, Machinery).