Jeff Payne, the Automation Controls Group Product Manager at AutomationDirect, penned an article titled Product Design: Incorporating Commercial Technologies into Industrial Controllers for the February 2018 issue of Control Engineering. The article looked at some of the commercial off-the-shelf or COTS technologies used in industrial controllers.
These technologies include Ethernet, FPGAs, USB, MicroSD and others. These advances are used to improve price/performance ratios, shrink form factors, and add new features to industrial controllers such as PLCs—providing benefits to both designers and end users. Jeff discusses how these technologies were used during design and development of a new industrial controller: the AutomationDirect Productivity1000.
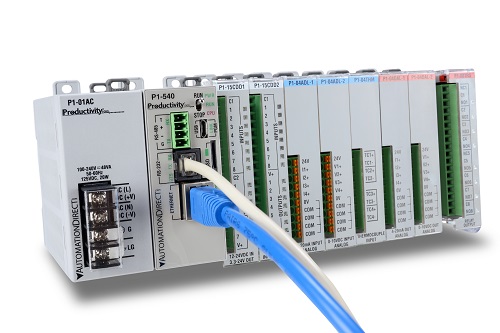
PLCs Benefit from Mobile Technology
Mobile technology is a huge driving factor greatly impacting industrial control system designs. Manufacturers continue to make smartphones, tablets and other devices ever thinner, smaller and more powerful. The technologies they use are trickling down into the industrial arena, with many of the components meeting the specifications required for industrial use.
Payne points to 3.3 V components used in mobile devices as an example. In the past, mobile device components ran on 5 V or 12 V. Switching to 3.3 V reduces power consumption and heat generation. By using lower supply voltages internally, only 15 watts are needed to power a fully loaded Productivity1000. That leads to smaller power supplies, and reduced cooling requirements.
The demand for onboard memory in commercial devices is also working its way into PLCs.
Designers need to pack more memory into smaller areas to handle a variety of applications. About 15 years ago, industrial controllers typically had about 10 kB or 15 kB of onboard memory. This was only enough for executing some ladder logic and a couple of PID loops, and even high-end controllers could only run about 16 PID loops.
Payne continues by pointing out that now, not only is there plenty of memory to store program code, but to also store documentation. Many modern controllers also provide a memory segment for historical data storage.
COTS Technologies in Industrial Controls
According to Payne, several COTS technologies are used in industrial controllers, including:
- Ethernet
- USB
- FPGA
- MicroSD
Ethernet and USB are two features that provide benefits to both the product designer and the end user. Ethernet communication is standard on many modern automation controllers, creating an open system for communications with a wide variety of I/O, field devices, HMIs, higher level computing systems, etc.
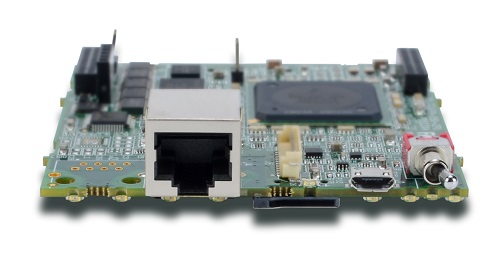
As a user, you likely have experienced the benefits of Ethernet. With this method of communication, a single port can connect to multiple devices, using multiple protocols if required, all while providing programming access. Modbus TCP and EtherNet/IP are just two of many intelligent Ethernet protocols available to connect devices to controllers.
Both Ethernet and USB communications make it easy to connect peripheral devices, and simplify wiring and setup. In addition to plug-and-play capability, the USB 2.0 Micro B connector has a smaller footprint than its predecessor.
Field-programmable gate arrays (FPGA), used by some controllers, are fast and reduce required space by combining multiple general-purpose chips into one custom-programmed chip. For onboard data storage, COTS provide more capacity at lower costs.
MicroSD cards provide a low cost and simple way to expand onboard memory. The ability to expand an industrial controller’s memory to store up to 32GB of historical data on a removable microSD card is a requirement for many applications.
Controllers Developed in U.S.
Payne told an interesting story about how AutomationDirect’s new Productivity1000 industrial controllers were designed in the U.S. It had always been the plan to expand the Productivity line with this small controller, but a low price point was required. However, AutomationDirect wanted the Productivity1000 to have many of the features of the larger PLCs in the Productivity family.
To do this, the company started with the largest-scale controller in the product family, the Productivity3000, to set the baseline for the new product. From there, they worked their way down through the market segments to the small and medium size micro-class controller (Productivity2000), and then into the smaller stackable controller (Productivity1000). AutomationDirect wanted to ensure scalability of the controller platform from the beginning by designing a family of controllers scalable from the top to the bottom. It was also important for all the controllers to use the same programming software as this would simplify coding of all the controllers for their customers.
The Productivity family of controllers has some overlap of pricing, capabilities, I/O capacity and so on—but with the new Productivity1000, the two goals of a lower price and smaller footprint were met. The DIN-rail space in a control enclosure is prime real-estate, so it must be used wisely. Development followed a path trod in the past by AutomationDirect.
AutomationDirect had prior success with their BRX Micro PLCs, also called bricks, and stackable micro brick Click Series PLCs, and this guided development of the Productivity platform of controllers. This new generation of controllers is designed in Tampa, Florida, with manufacturing in Taiwan. The firmware and software are also developed in the U.S. AutomationDirect worked with FACTS Engineering as the hardware design arm for the new Productivity platform.
Payne continued with some of the history behind controller development at AutomationDirect, with good partners playing a critical role.
FACTS Engineering has been a technology partner of AutomationDirect since the beginning, in the early days of PLCDirect and the DirectLogic PLCs where they were designing analog and specialty communication modules. This made them a natural selection for design of the next generation of controllers, including mechanical design, board layout and some of the firmware work.
Like many firms, AutomationDirect found partnering to be the best method for development, as opposed to doing everything in house. Like FACTS engineering, Koyo Electronics, Japan is the design and manufacturing arm for most of the original DirectLogic PLCs and the newer CLICK PLCs. Likewise, HOST Engineering, Johnson City, Tennessee, designed and manufactured the Do-more and BRX PLCs. This allowed each company to focus on what they knew best, develop their own roadmaps and produced the desired result.
COTS technology is making new controllers more cost effective and smaller. At the same time, it makes the controllers more capable by adding protocol conversion, data storage and other capabilities.
For more articles about programmable control, click here.
Originally Published: March 2018