Process skids are used in many industries and present a host of automation challenges, each of which can be met by using the right controller hardware and software.
Jeff Payne, the Automation Controls Group Product Manager at AutomationDirect, wrote an article appearing in the September 2018 issue of Processing magazine titled Effective Process Skid Automation. Please find a summary below.
Process skids are created by taking various processes and fitting them onto a skid. These processes are often smaller versions of large-scale plants, for example a wastewater treatment skid processing 5,000 gallons per day, as compared to a municipal wastewater treatment plant processing millions of gallons per day.
Describing a wastewater treatment skid, Payne says it, “…must operate accurately and reliably at flow rates of 5 to 100 percent of capacity. Most process skids will have one or more PID loops, and many have extensive requirements for communications and data handling.”
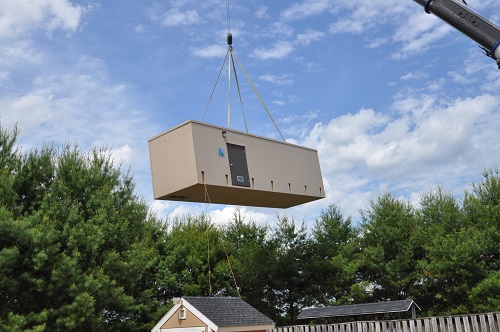
This wastewater treatment system is contained on a single skid and delivered to a job site ready to run.
Payne says many process skids have demanding automation requirements because of the complexity of onboard operations, regardless of the number of I/O points.
Pick the Right Family
Perhaps the most important requirement for a process skid controller is scalability, often best accomplished by selecting a family of programmable logic controllers (PLCs). Using a family of PLCs allows the process skid builder OEM to scale from small to large applications with the same base hardware platform, and with the same PLC programming software.
This is important because many OEMs build process skids to handle a wide range of production, and it is much more cost-effective to closely fit the PLC cost and capabilities to the application requirements, as opposed to using a one-size-fits-none approach.
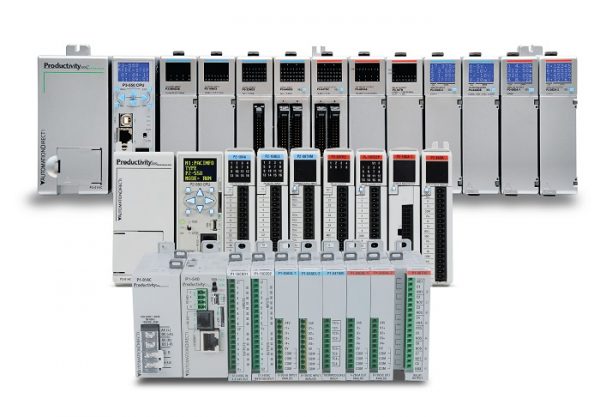
Selecting a family of similar PLCs for process skid automation, such as AutomationDirect’s Productivity series, allows designers to closely match PLC capabilities to skid requirements.
If the right family of PLCs is selected, each controller can be programed using the same software. In the best case, the software will allow the entire application program to be created before the PLC is selected. Payne says this allows the designer to select the PLC with just the right capabilities, and no more.
A family of PLCs will typically use the same I/O, with the higher-end PLCs in the product line sometimes offering more options. This simplifies design of the control panel because wiring to and from the I/O will be similar in all cases, and it also reduces stocking requirements.
One of the main reasons process skids are growing in popularity is the ability to test the skid prior to shipment. This is important Payne says, because of where skids are installed.
Process skids are often located in remote sites and are expected to run unmanned. This means the PLC must have the ability to securely communicate over the internet. This requires an Ethernet port and support for hardwired, satellite and cellular communications.
One of the most common remote connectivity options is browser-based access to a PLC’s built-in web server.
Another option for remotely accessing the PLC is a built-in web server. Enabling this feature provides a quick look at the PLC health by viewing system tags. It also provides the ability to view, download or delete data log files currently on the removable memory device, preferably at USB drive or microSD card.
To monitor just a few data points, an app is often the best solution. An app allows the user to connect a mobile device such as a smartphone or tablet to remote PLC systems using Wi-Fi or cellular network connections. The remote user can monitor tags preconfigured for remote access inside the tag database of the PLC program.
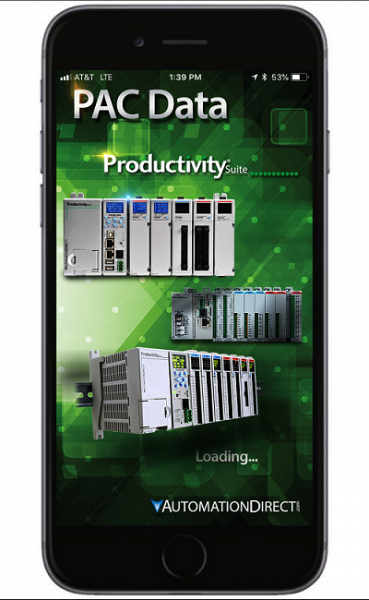
The AutomationDirect PAC Data app runs on any Apple smartphone or tablet, providing remote access to the company’s Productivity Series of PLCs.
Playing Well with Others
Another popular application for process skids is in existing plants, which requires tight integration between the skid’s PLC and the plant’s control system. If multiple process skids are supplied to a plant by one OEM, then communications among the PLCs on each skid will often be needed.
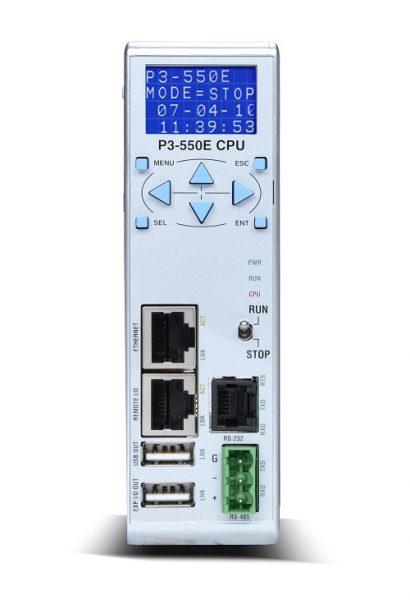
Process skids are often installed in existing plants, requiring tight integration with existing control systems. This AutomationDirect P3K PLC addresses these requirements by providing a variety of communication ports including two for Ethernet, RS-232 serial, RS-485 serial and USB.
In applications where skids are integrating with existing applications or other skids controlled with Productivity Series PLCs, quick integration can be implemented via the proprietary ProNET network to quickly and easily share data among PLCs. Payne sums up:
Process skids have unique controller requirements in terms of scalability, real-time control, remote operation, integration with other control systems and data handling. The right controller, usually a family of PLCs, will allow skid builders to satisfy these requirements in a cost-effective manner while minimizing startup and commissioning time.
To read more articles related to PLCs, click here.
Originally Published: December 2018