Dedicated HMIs can do many of the same things as industrial PCs, often making them the best choice for automation applications.
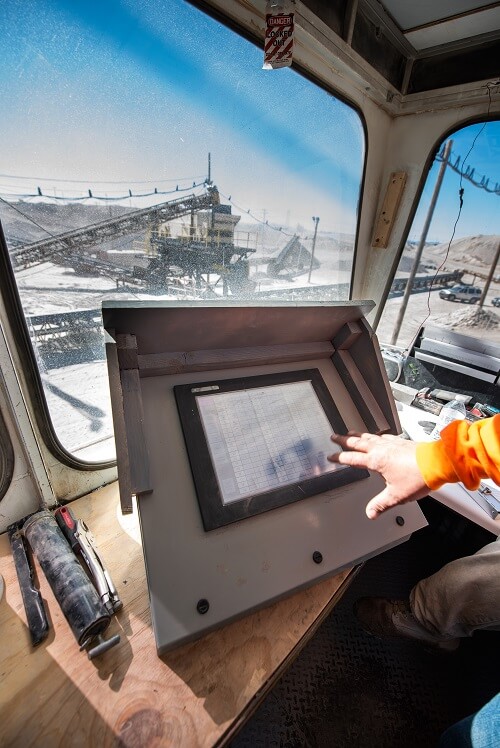
Bill Dehner, technical marketing engineer for AutomationDirect, wrote an article for the August 2020 issue of Control Engineering titled Embedded HMIs Excel in Automation Applications. Here’s a summary, click on the link above for the full text.
Human-machine interfaces (HMIs) are the way we interact with our phones, vehicles, automation systems, and more. In the case of cars, HMIs have progressed from mechanical devices like a stick shift, to electrical devices like a headlight switch, to digital implementations like a touchscreen.
Today’s industrial automation systems commonly use digital HMIs hosted on industrial PCs (IPCs) or built-for-purpose dedicated HMIs, which are sometimes known as embedded HMIs. Following are some considerations for choosing the best HMI platform for your application.
HMI History
When the first mission-specific digital embedded HMIs became available, users could easily, economically, and compactly supersede the functionality previously provided by dozens or hundreds of hardwired switches and indicators. Updates could be performed via software changes, without the need for rewiring or new panel cutouts. As technology evolved, HMI functionality could later be accomplished using software hosted on general-purpose PCs, IPCs, and even mobile devices. Performance and capabilities improved, but at a cost.
The Case for IPC HMIs
PCs used as HMIs take advantage of the latest hardware advancements and computational functionality to allow extensive flexibility. However, users must carefully choose IPC platforms with a suitable display form factor, and with components able to survive the often-harsh industrial conditions. Once deployed, the operating system and all applications need to be managed and updated for operational and security issues.
Embedded HMIs as a “Just Right” Solution
Embedded HMIs are offered in convenient panel-mount form factors, often as all-in-one touch screens. They are constructed for industrial environments using components designed and sized specifically for the task. Their embedded operating system means they can be rapidly deployed, often right out of the box.
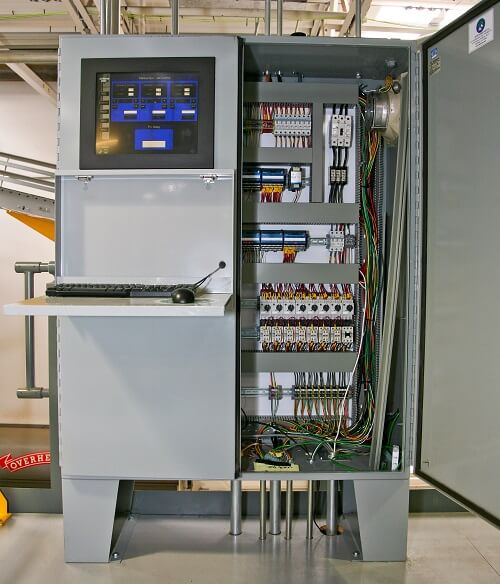
Development software for embedded HMIs is low cost or even free, and their standalone configuration means they are less likely to need updates once in service. Although IPC-based HMIs usually have more capabilities than embedded HMIs, there is a lot of common functionality delivered by both, such as:
- Ability to communicate with many target device types using popular industrial protocols
- Rich variety of graphical objects and animation
- Support for remote connectivity
Less can be More
With advances in mobile computing, many times there is less need for a factory floor or control room HMI. In these cases, embedded HMIs are even available in “headless” versions, where all HMI visualization is provided via mobile devices.
The best HMI solution for complicated and large automation scenarios is likely to be IPC-based, even though the overall lifecycle cost of using an IPC-based HMI exceeds that of an embedded HMI.
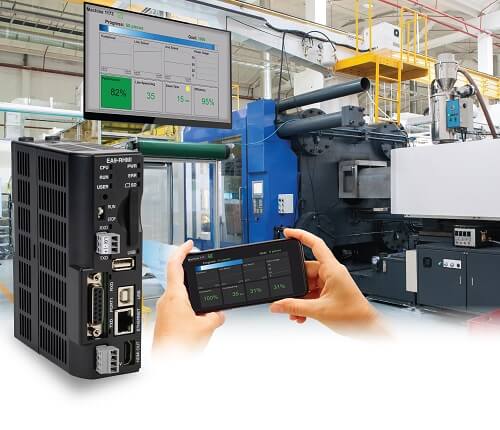
However, it is also clear today’s embedded HMI platforms provide comprehensive functionality, often approaching an IPC HMI. They feature all the most common HMI visualization functions, and also deliver other services like data, event, and alarm logging.
Designers should consider the features they need in the context of initial and sustaining costs to see if an embedded HMI is the best fit for their next project.