Managers and business owners everywhere are always looking for ways to keep operating costs down to stay viable in a highly competitive world. And for many industries, automation has become that way. Investing in a control system application can provide lower operational costs and therefore higher bottom lines. But your return on investment can be even greater if you have a qualified, well-trained maintenance staff capable of keeping you up and running. Developing your own in-house PLC knowledge base through PLC training will protect the gains you have made with automation and I’ll give you five examples how.
1. Technological Advances
As with any technology, the second you purchase it, new advances are around the corner to make it obsolete. The ever-improving aspect of technology, specifically PLC technology, is a good thing if you have the personnel to keep up with it. PLCs are improving in many aspects including efficiency, size, cost, and usability. Having a well-trained staff and keeping them up to date on PLC technology allows your control system to serve you in the best way possible.
2. Limiting Downtime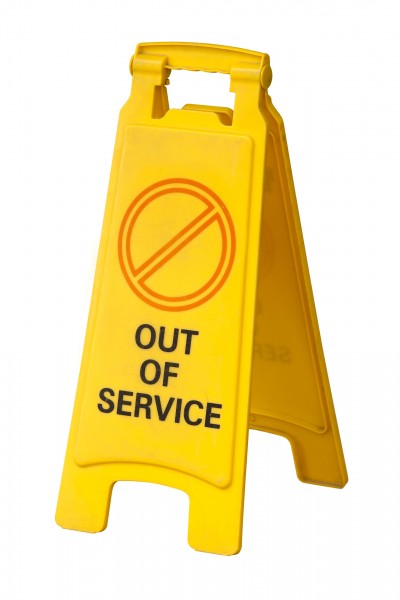
Let’s face it, things happen. Parts wear down, they malfunction, they overheat and sometimes they just break. If an issue arises with your control system, downtime can be much longer than necessary if you need to bring in outside personnel to repair it. Having internal personnel at-the-ready will reduce downtime and could ensure your production has around the clock support. And not only that, but your internal personnel will have the expertise on your specific system and the knowledge of your facility, including policies and procedures, that no outside contractor will have.
3. Repair and Improvement Costs
Another benefit of keeping a well-trained staff, is the money you can save on repairs and improvements. Having the know-how to repair your own equipment internally gives you more control over labor costs as well as the costs of replacement parts. Shopping around and buying in bulk are two things you can do to reduce the cost of replacement parts that an outside contractor might not do. And what about process improvements? Do you really want to have to bring in a contractor to change the fill level in your bottling process? What if you just wanted to add one more EStop to your conveyor line? Get the PLC training you need so that simple code changes and improvements like these don’t become cost prohibitive.
4. Proprietary Processes
Competition is a major factor in business decisions and many facilities that automate do so in a way to give them a competitive advantage. Keeping proprietary information confidential to maintain this advantage is a big reason to keep your control system engineering in-house. Training your internal personnel is one way to help safeguard any sensitive information, such as new product development, that may otherwise be compromised.
5. PLC Security
Computer security has become one of the most important priorities in our computerized age. Security breaches can cripple companies and cost millions to undo. Home Depot, Target and Sony Pictures have all seen their profits, stocks and reputations impacted by security breaches. “But I’m not in that type of business”, you say. Well my answer to that is Stuxnet. If you are unfamiliar with that term, I’ll explain. Stuxnet is a malware worm that was designed to target Siemens PLCs in Iranian nuclear facilities. Unlike the breaches with Home Depot, Target and Sony, this malware wasn’t designed to steal information but rather to destroy equipment. Once Stuxnet was loaded on the computer it was looking for, it began altering PLC code and issuing commands that destroyed centrifuges. While doing this, Stuxnet hid itself from detection by sending back normal operating signals. This virus is considered a highly advanced virus and is thought to have been designed specifically for Iranian targets. And it is believed that this virus entered the nuclear facility from a USB drive brought in from outside sources. Although you would probably not see such a highly advanced virus at your facility, it illustrates the vulnerabilities that come with bringing in outside contractors and their equipment. An in-house, PLC-trained staff can effectively remove the inherent security risk posed by outside sources.
As these examples show, PLC training can give your facility the knowledge needed to maintain the cost savings that was achieved through automation. If you are interested in learning more about PLC training but don’t know where to start, we can help. See how at the link below.
[hozbreak]
[hozbreak]
Need some advice on places to look? Check out these 5 ways to learn more about PLCs.