Once only suitable for sheltered office installations, Ethernet media and protocols can now efficiently serve and future-proof a variety of industrial applications.
Once upon a time (think 1980s), Ethernet was a relatively specialized computer connectivity technology, administrated by experienced gurus under highly-controlled office settings. Since then, technology and performance have advanced incredibly, and much of the world’s population uses wired and wireless (Wi-Fi) Ethernet in their everyday lives.
Networking has likewise been essential for industrial automation purposes, also as early as the 1980s, but technologies intended for this service have always needed to meet several requirements:
- Form factors and installation methods suitable for field environments (ease of installation, withstands environmental temperature/dirt/moisture/physical conditions)
- Robust resistance to electrical noise from power feeds, motors, contactors, and other sources
- Sufficient bandwidth and responsiveness
The earliest operations technology (OT) approaches to digital communications and networking were specialized—sometimes proprietary—and limited, but several versions became viable, depending on the use case. Eventually, however, economies of scale made it possible for Ethernet information technology (IT) to dominate throughout all levels of industrial automation communications.
Networking Progress in the Factory
Any network requires connecting two or more devices with each other so they can communicate. In a commercial or consumer setting, networks allow computers, printers, cloud resources, and more to interact with each other.
On an industrial machine or in a factory, networking requires both OT and IT aspects. From an OT standpoint, devices like programmable logic controllers (PLCs) need to work with each other and with “lower level” input/output devices, and other smart devices such as instruments and variable frequency drives (VFDs) (Figure 1). From an IT standpoint, those same PLCs and other devices need to communicate with “higher level” human-machine interface (HMI) and other computing resources, potentially using the internet to reach cloud-based assets. In addition, industrial control system (ICS) applications typically prioritize responsiveness and reliability due to the real-time nature of monitoring and controlling physical devices.
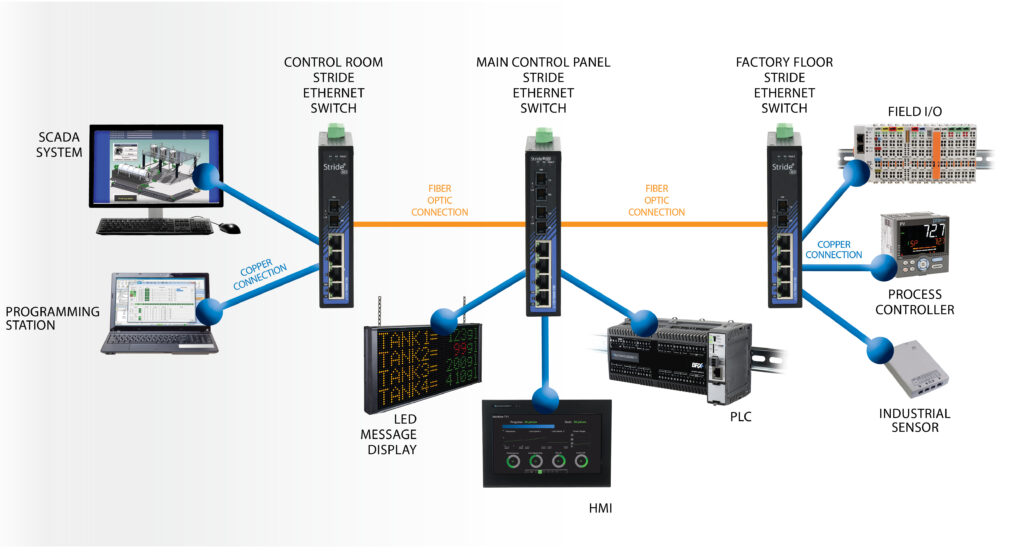
Figure 1: As Ethernet has evolved with capabilities enabling widespread adoption for industrial control systems, AutomationDirect has expanded their Ethernet-capable product portfolio to include PLCs, HMIs, field I/O, Ethernet switches, and much more.
OT communication packets for ICS applications tend to be small in size, but they demand responsive near-real-time and deterministic operation because they are interacting with real-world equipment and processes. IT communication packets are larger in size and generally have a slightly lower speed requirement. Therefore, original OT communications media and protocols—such as RS232/422/485 serial, Modbus RTU, DeviceNet, and others—were specifically adapted to meet OT needs and are collectively called “fieldbuses,” but they simply were not adequate for IT.
As a commercial off-the-shelf (COTS) technology founded in the IT realm, Ethernet as first standardized in 1983 as IEEE 802.3 was not immediately a good fit for OT applications in either a media (physical connection) or protocol (digital connection) aspect. Cables and fittings were not easy to install for industrial environments, and determinism was lacking. This changed as improvements became widely available, so that the media and protocol problems originally making Ethernet problematic for industrial applications have largely been solved. Designers now have a useful range of solutions available, as listed below, so they can select one or more as the best fit for each need.
Media
- Coaxial cable transitioned to twisted pair cable and RJ45 modular connectors.
- Fiber optic options became practical for extending beyond copper cable distance limitations.
- Communication speeds increased from 10 Mb/s to 100 Mb/s to 1 Gb/s, and beyond.
Protocols
- The basic Ethernet TCP/IP protocol, suitable for general-purpose use, was supplemented by several industrial-specific protocol options, initially supported by industrial automation vendors, but now by independent standards organizations, such as the FieldComm Group.
- For OT use, EtherNet/IP, PROFINET, Modbus TCP, and EtherCAT (in addition to other more specialized versions, such as HART IP, DNP3, and BACnet) have risen in prominence to meet a variety of application needs, even including high-speed motion capabilities formerly reserved for use only with specialized digital communications. Some protocols are optimized for power utility or HVAC industry applications.
- For IT use, OPC UA and MQTT represent two popular methods, with some overlapping capabilities but also optimal use cases for each. These protocols address the need for contextual data exchange and security at this level.
While most OT and ICS applications are time-sensitive to some degree, certain applications are more so. For instance, high-speed motion control of robots and other servo-driven equipment usually demands timely communications, especially when coordinating motion among many axes or other actuated equipment.
For motion applications, a protocol called Ethernet for Control Automation Technology (EtherCAT) was originally developed by Beckhoff Automation in the early 2000’s (they then donated the rights so that the protocol could be standardized under IEC 61158). EtherCAT works on standard Ethernet architectures, using a single master device to initiate a datagram frame which is sequentially passed through associated network nodes (Figure 2). This messaging structure eliminates data “collisions,” enabling short deterministic cycle times of less than 100 µs so that accurate synchronization can be maintained among all communicating devices.