Industrial-grade products provide a path for this student organization to develop a space-capable rocket.
Byline: Oleg Khalimonov, Space Concordia
Many are familiar with the phrase “it isn’t rocket science.” But today more than ever, sometimes it is rocket science. SpaceX and other organizations have made rocket launches and space exploration commercially viable and almost commonplace, but there is still a great deal of work to do.
For about 15 years at Concordia University in Montreal, Canada, a student society called Space Concordia has provided an opportunity for students to work on projects in rocketry, spacecraft, robotics, and more. The organization equips students with valuable technical experience that employers value. While the university supports Space Concordia, the program is also partly funded by industry sponsorships.
The work is quite sophisticated, as would be expected in a space-grade program, but several aspects are based on very fundamental and practical principles, including the use of proven industrial-grade products and equipment to create a fit-for-purpose solution.
Combustion Complexity
For about six years, the team has been developing the Starsailor, a 42-foot, bi-propellent, pressure-fed reusable rocket designed to lift a 143-pound payload straight up and back down for a non-orbital flight (Figure 1). With a 76-mile-high apogee, the rocket will technically reach space, which is relatively rare for launch vehicles in academia. The team is also developing Trailer Tom, a mobile engine test stand, and Bigger Ben, a 72-foot-tall launch tower.
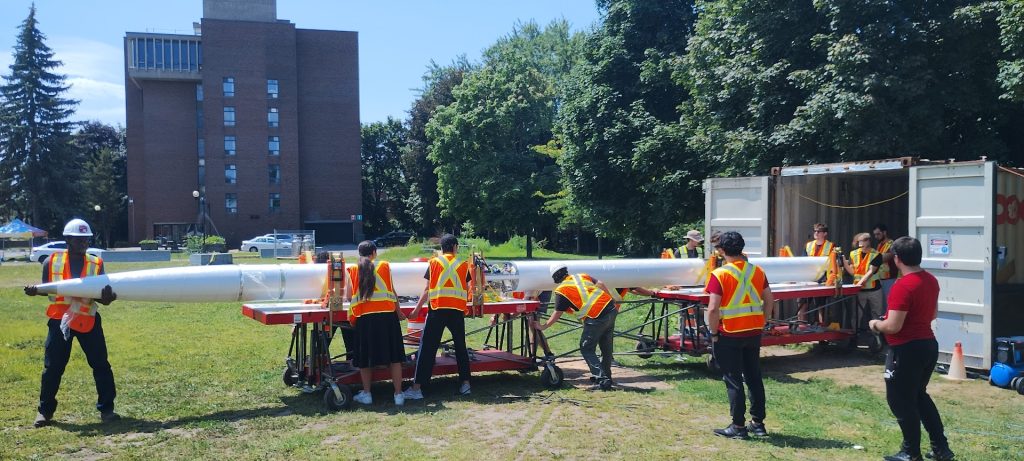
Because the 8,000-pound force rocket engine is fueled by a combination of liquid oxygen and liquid kerosene there is a significant amount of complexity loading, storing, and unloading these materials on both the ground-based and rocket-based systems, and also handling them during flight. Liquid-propelled rockets require careful design, control, and monitoring of valves, solenoids, sensors, and related systems, and it is rare for student rocket projects to undertake the development cost and learning curve required for success.
Practical Specifications
The Space Concordia team faces the same considerations that governments or large companies do for this type of work, including development and approval of procedures, and compliance with environmental, health, and safety provisions.
For safe handling of the liquid fuel and oxidizer, the team developed requirements for vessels, valves, lines, and fittings with regards to pressures, flows, and temperatures. Many of the valves and other mechanical equipment are operated using nitrogen gas-driven actuators, which are controlled using smaller solenoid valves to provide the necessary operating forces (Figure 2).
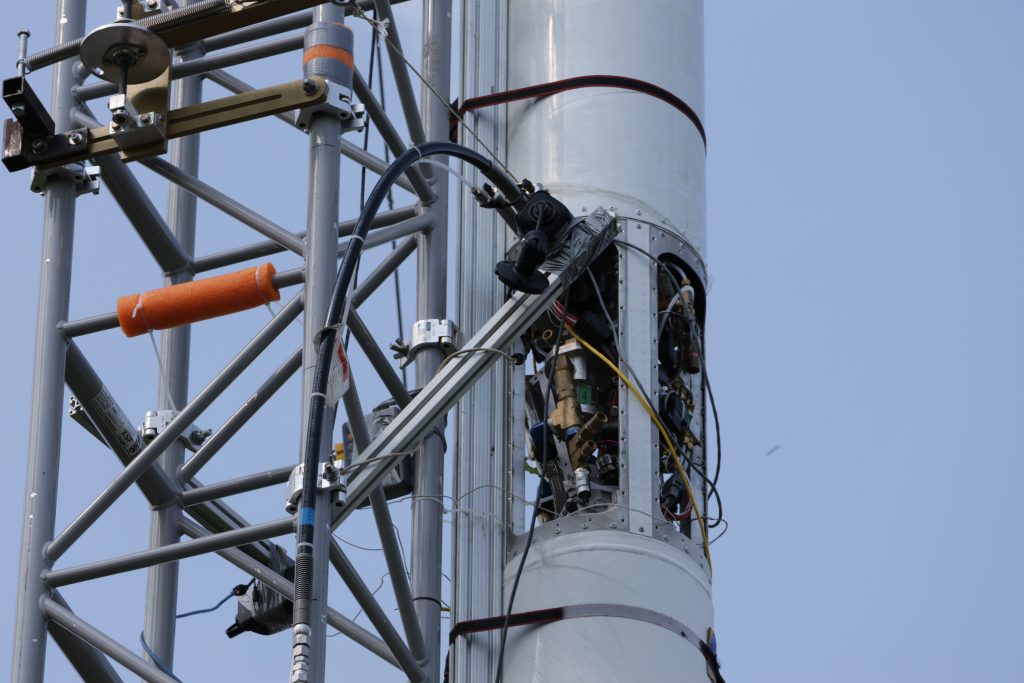
Most operations are remotely controlled using hardwired switches or a digital controller, which required significant design, fabrication, and installation of control panels (Figure 3).
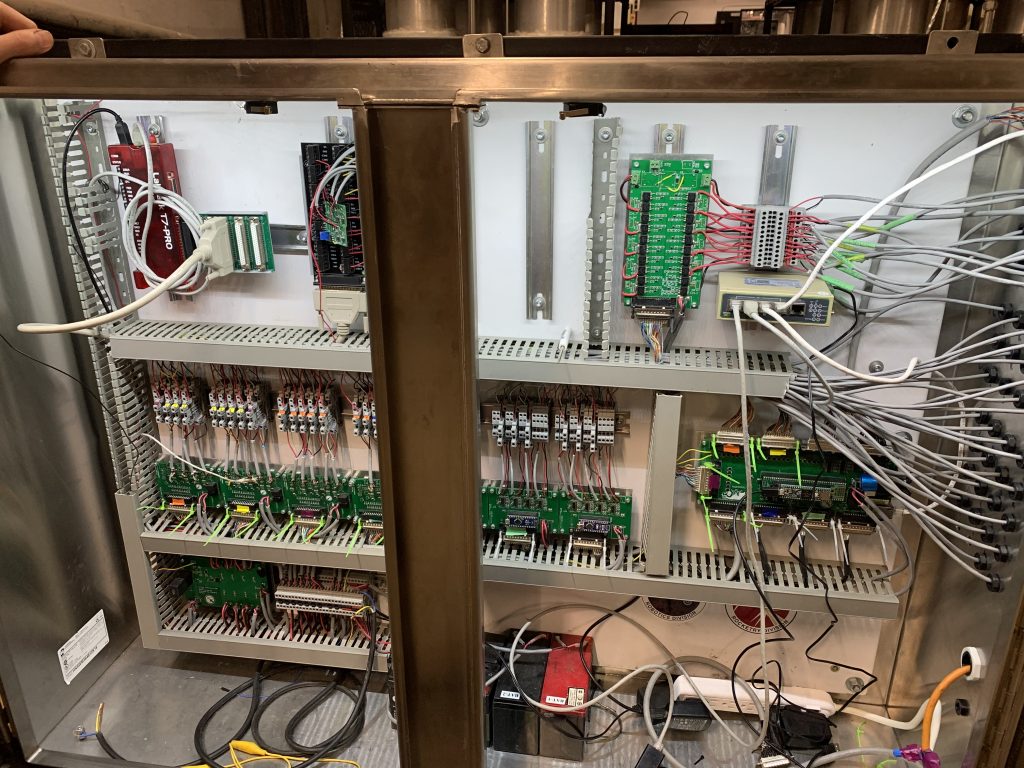
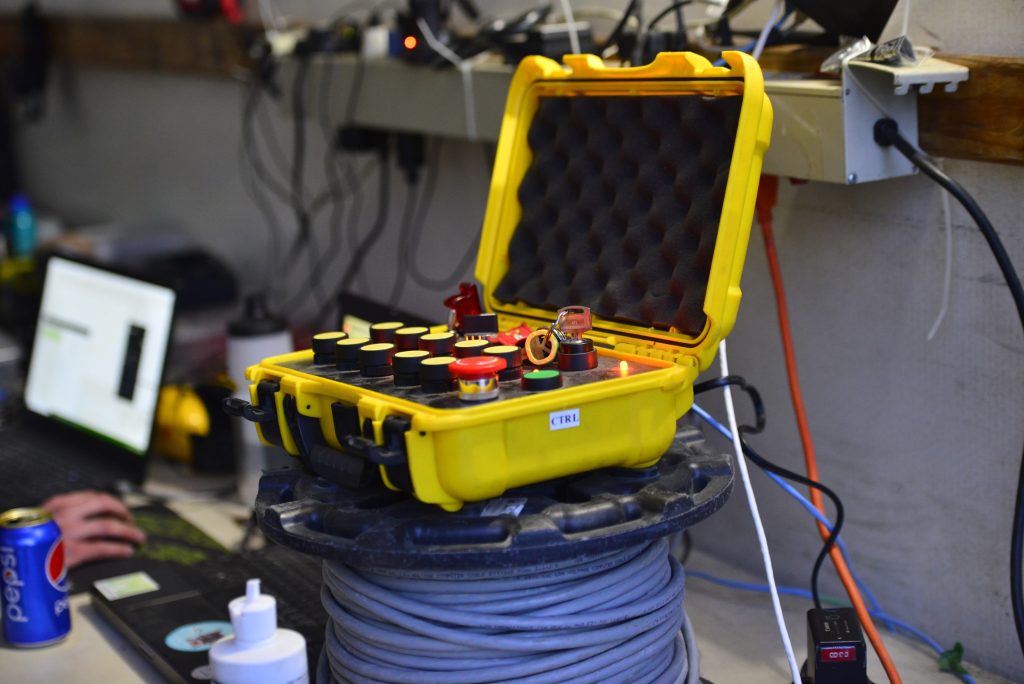
Figure 3: The ground-based Trailer Tom and Bigger Ben equipment each use a significant quantity of commercial off-the-shelf products, such as those available from AutomationDirect.
While massive aerospace corporations can specify custom products and highly-engineered solutions, a student-run organization must be far more cost-conscious. Fortunately, the team has found that a wide variety of commercial off-the-shelf (COTS) components developed for industrial applications work well in the rocketry project (Figure 4).
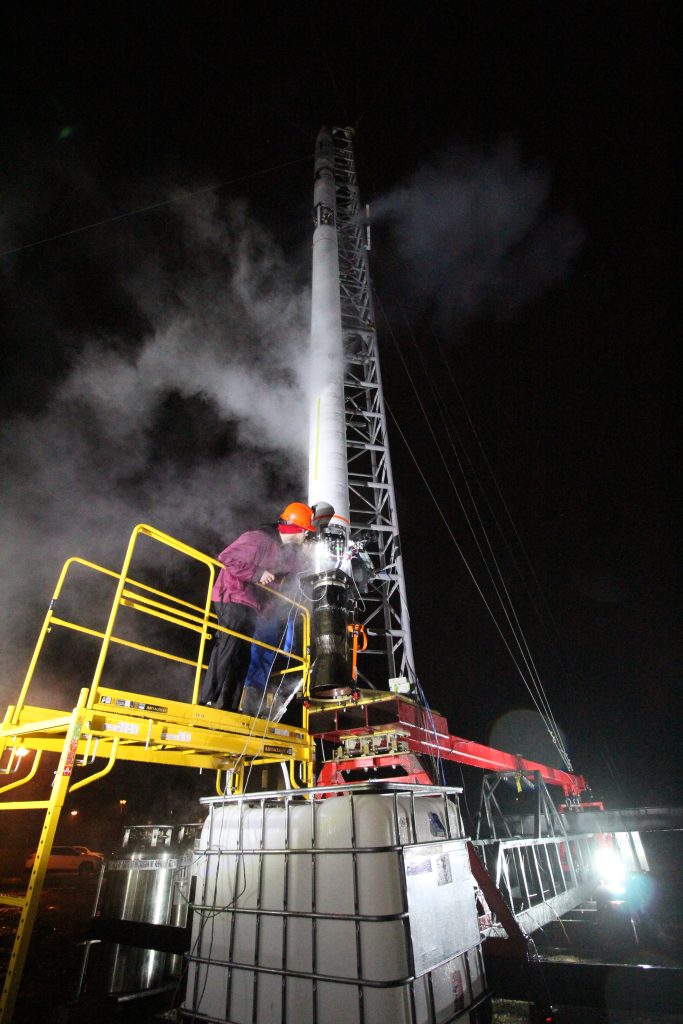
They were able to specify a wide range of products right out of the AutomationDirect catalog, with a variety of components performing admirably in both the ground support and rocket systems, including:
- Pneumatic actuators, tubing, fittings, and accessories
- Solenoid valves and accessories
- Sensors
- Cables, conductors, and associated fittings
- Ethernet networking devices and cables, both for copper and fiber optics
- Buttons, switches, horns, terminal blocks, relays, power supplies, and other control panel devices
The AutomationDirect website provides a clear way to investigate a wide variety of products, enabling the team to determine the technical details, cost, availability, and options available for each component. In some cases, AutomationDirect worked with Space Concordia team members to identify the best-fit products. The website also hosts a complete range of helpful materials, including data sheets and support videos.
Factory Fundamentals Can Serve in Space
While only a select few automation projects qualify as actual rocket science, every automation project deserves to be outfitted with top-quality and high-value components. Since 1994, AutomationDirect has been in the business of supplying end users of any scale with the reliable products, support, and value they need to create innovative solutions on Earth, and now in space.
Space Concordia has put AutomationDirect products to ample use throughout the Starsailor project, and it will soon complete a 30 second full-power engine test fire. The next steps will include final vehicle tests and preparations to launch from Churchill, Manitoba. You can see the team’s previous tests on YouTube here:
The team would like to thank AutomationDirect for all the support throughout this process, and it looks forward to the continued relationship.
All figures courtesy of Space Concordia
Author Bio
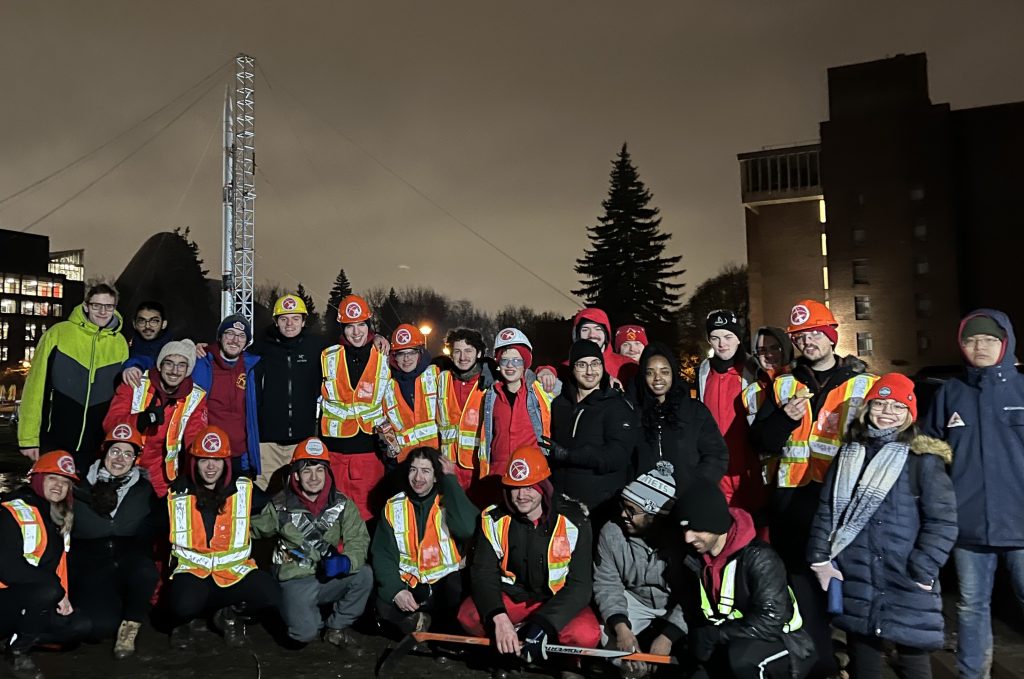
Oleg Khalimonov is the Starsailor program director for Space Concordia at Concordia University in Montreal, Canada. He supervises a team of about 80 students as the multi-year project progresses.