Recent advances in micro-PLCs that support integrated motion, and also drive/controller devices, make it possible to take advantage of high-performance servo motor motion control without breaking the bank.
By Chip McDaniel and Joe Kimbrell, AutomationDirect
Servo motor motion control is a mainstay for many types of machinery and equipment. For example, this technology can be used to operate a conveyor at a certain speed, or to coordinate the motions of multiple motors for indexing, gripping, or physical machine movements through several ranges. Servos are a high-performance solution delivering high torque and speed, over a broad power range, with impressive closed-loop control response.
Implementers understand, however, that employing such sophisticated servo technology usually comes with an equally elevated cost and complexity. This lofty barrier to entry has often prevented designers from using servo technology for many smaller or price-sensitive applications, even when it would be the best technical solution. There has been some relief as vector speed control AC motor variable frequency drives (VFDs) and more advanced stepper motor systems have become available, providing good motor control at a lower price point, but servos are still the best solution in many applications.
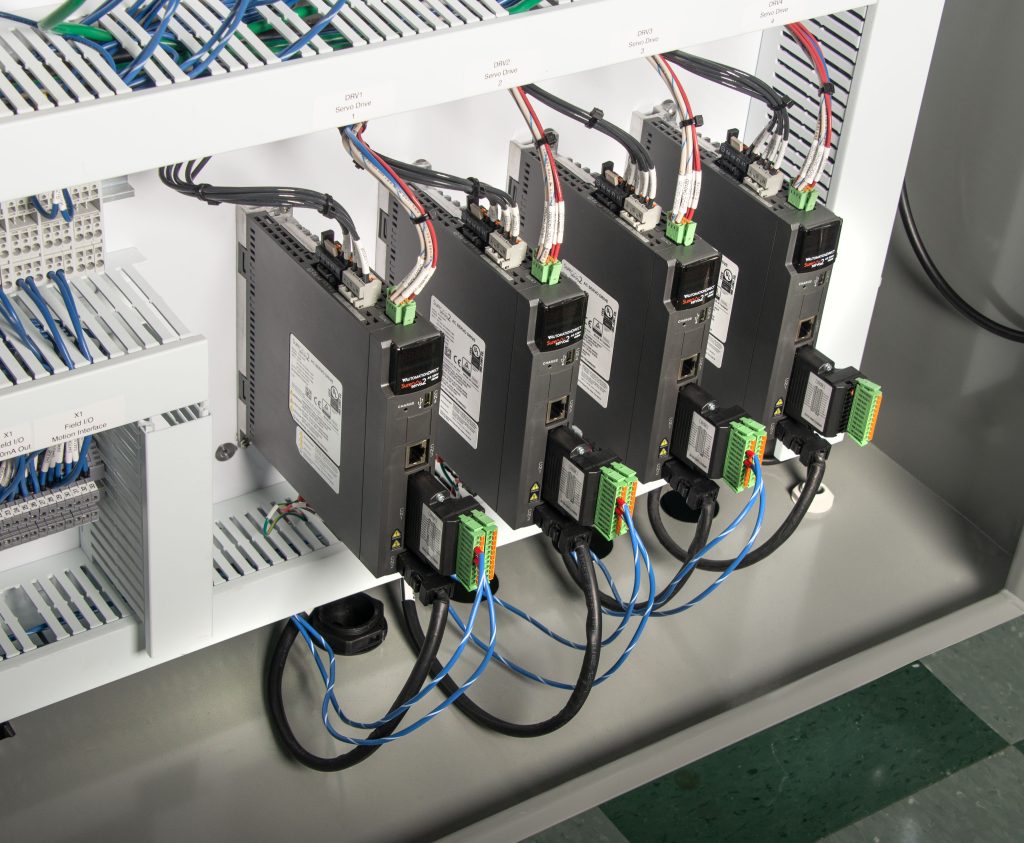
Of course, servo and control technologies have also advanced in many ways, some of which improve the accessibility and price/performance ratio. Designers today may not realize that they have a greater range of options to implement servo motor control, instead of relying on more specialized and complex classic motion control architectures (Figure 1).
Read on to find out how all-in-one servo controller/amplifiers, and even small industrial controllers with integrated motion instructions, offer built-in and streamlined ways to add servo motion control to almost any application.
Consolidating Capabilities
A classic decentralized servo motor control system is architected from several elements, including:
- At least one, and often more, brushless servo motors mounted on field equipment, each motor equipped with an encoder to enable precise shaft position monitoring.
- Each motor is powered and operated by a servo amplifier or drive, supplying current as needed to achieve the desired velocity and position, which is detected by the encoder.
- A standalone motion controller, which is programmed to command and coordinate one or more servo drives.
- For a decentralized system, a high-performance communication fieldbus optimized for motion control, or in some cases hardwired signals, may connect the controller to the drives.
- The motion controller will often need to coordinate with other field-installed sensors, and this integration is typically provided by one or more external programmable logic controllers (PLCs).
This architecture is proven, but obviously involves a lot of costly components, design effort, programming, and installation. However, over the years a number of developments with power electronics, computing, and networking have made it possible to consolidate much of this functionality and simplify implementations. For example:
- Various models of servo drives may be commanded via:
- Hardwired high-speed input/output (I/O) signals.
- Using typical serial or Ethernet variants of industrial communication fieldbus protocols, such as PROFINET, EtherNet/IP, or Modbus TCP.
- And/or via a motion-optimized Ethernet protocol such as Ethernet for Control Automation Technology (EtherCAT) connectivity. EtherCAT is standardized under IEC 61158, and it works over standard Ethernet architectures to deliver deterministic cycle times so that accurate synchronization essential for motion control can be maintained among all communicating devices.
- Some servo drives now have significant on-board motion control capabilities, and can be coordinated with each other to a degree.
- Some standard PLCs incorporate some motion control capabilities using hardwired I/O signals, or may offer motion control modules to coordinate a few axes, or can communicate motion information to servo drives using a typical industrial fieldbus.
- A select few entry level or basic PLCs can perform up to three axes of motion control, using the most popular instructions needed to cover a wide range of applications and can command servo drives using hardwired I/O.
- For demanding applications requiring motion and PLC control, a specialized PLC with native motion-optimized communications such as EtherCAT is a good choice for handling up to 16 or even more total axes of coordinated motion.
The traditional decentralized architecture remains an option for some exacting applications, but these newer architectures are of particular interest for making motion control practical for smaller and more cost-sensitive applications.
Making the Move
Once designers are aware of the many servo motion control options, selecting the right products is a matter of understanding application needs.
Basic Motion Control
Any drive-based servo controller, and some PLCs, can provide the basics of motion control, including the ability to perform:
- Single servo control, and potentially to join one or two additional axes for X-Y or X-Y-Z control.
- Homing operations, so the driven equipment can be moved to a known starting position.
- Velocity moves, commanding a servo to accelerate and decelerate to achieve a target speed.
- Position moves, commanding one or more coordinated servos at the necessary acceleration, deceleration, and velocity to reach a target location.
- Motion profiles, such as trapezoidal and S-curve, which reduce the jerk on equipment and payloads as servos change speed.
These fundamentals cover a wide range of application needs, so designers may find that with a capable servo drive/controller they can completely achieve their motion control goals. Or, if there is some other associated external I/O, a micro-PLC combined with servo drives can be a complete motion control and automation solution, at a fraction of the cost and complexity associated with more traditional architectures.
Enhanced Motion Control
When more than basic motion control is needed, a servo drive/controller will need some additional features. Here are some considerations that would prompt a designer to select a servo drive/controller instead of a more basic system:
- Internal indexing: this is the ability of the drive/control to store a series of pre-configured moves in memory, which can be activated by logic, communications, or command signals as needed.
- Standardized modes for common operations (Figure 2), such as:
- Gantry: a feedback strategy optimized for common X-Y and X-Y-Z operations.
- Encoder following (also known as axis-and-a-half or electronic gearing): a function where a servo drive moves a motor based on the input from an external encoder position, or based on the encoder output of another drive, so that the motor speed and direction are an immediate reflection of the encoder signal (or a ratio thereof).
- Flying shear: commonly used to make clean cuts on moving material.
- Rotary indexing: used for assembly, tool changer, and filler equipment with fixed distances/angles between stations.
- Basic registration: detect product variations in-motion and correct single-axis motion to compensate.
- Event-based logic control: some models of servo/drive controller have sufficient programming capability to incorporate a degree of additional control logic and I/O, without requiring an external PLC. This capability is useful for related operations, like acting when sensors are triggered, or operating a holding brake.
- Safe torque off (STO): while not specifically a motion instruction, STO is a fail-safe functionality which simplifies designs because no additional hardware or programming is needed to incorporate emergency stop functionality.
- Communications: a servo/drive controller can accept hardwired I/O, but some models are able to transmit/receive signals and motion commands over Ethernet using industrial communications protocols, like Modbus TCP or EtherNet/IP industrial, so they can be closely integrated with upstream/downstream or supervisory PLC systems.
- Built-in auto-tuning to optimize motor operation with the drive, and an integrated software oscilloscope so users can compare commanded operations with actual movements for commissioning and troubleshooting (Figure 3).
- Ability to use incremental encoders (which require homing after every power cycle), and also more capable absolute encoders which maintain their positioning indefinitely once homed.
Figure 2: The AutomationDirect SureServo2 series servo drives include a built-in motion controller with intuitive configuration software, so users can configure common and advanced applications, such as the rotary shear table shown here.
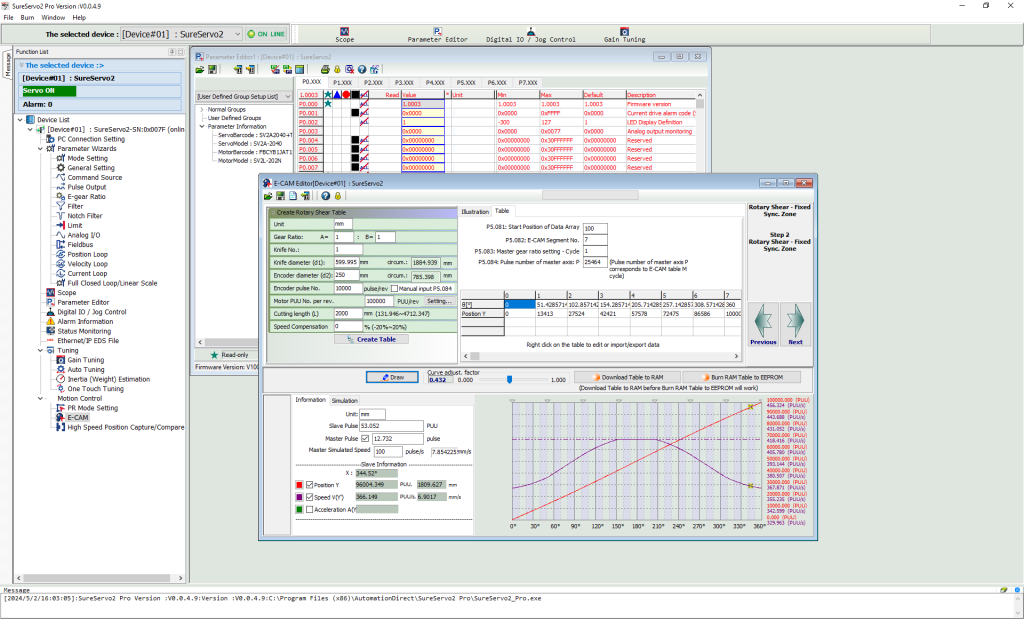
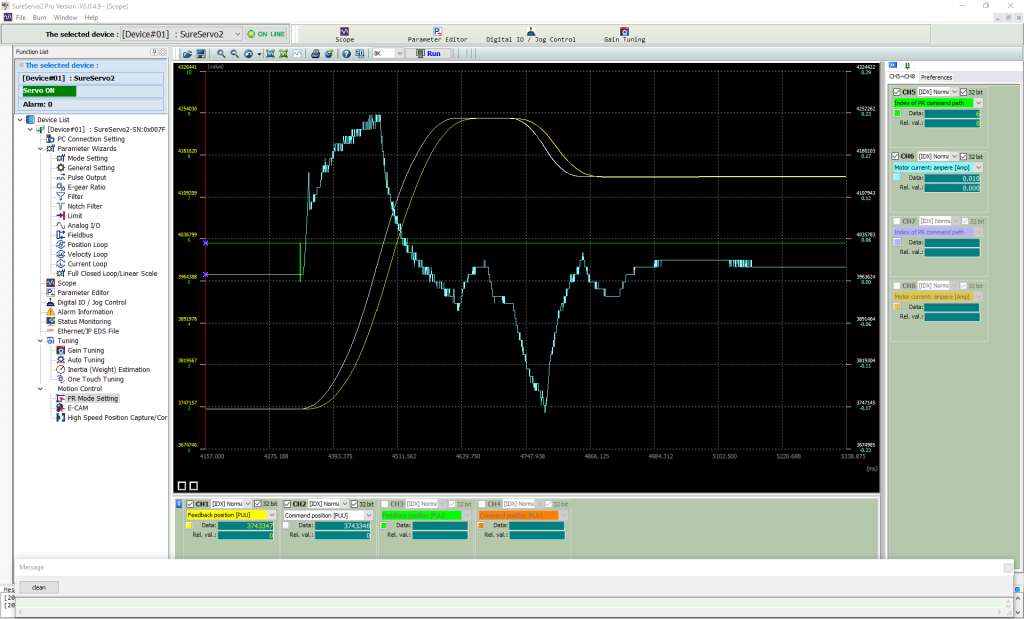
Mid-Tier Motion Control
Of course, there are some applications where a full-blown motion controller architecture is needed. Users can choose a traditional motion controller connected to many drives using a motion-optimized communication protocol, or a specialized controller which incorporates high-performance motion functions. Modern PLC controllers are perfect for this type of motion control while also handling the rest of the I/O requirements for many machines. Furthermore, these PLCs can store all the motion related parameters, which simplifies the control scheme, and facilitates maintenance and repair strategies. These devices enable:
- Multi-axis control, ranging up to 16 axes, coordinated in groups of up to 4 or 8.
- Exceptionally rapid response times: with position updates to multiple axes in the 1ms range.
- Native EtherCAT connectivity for streamlined integration with many types of servo drives.
- Electronic camming: to map motions for epicyclic motion.
- Multiple interpolation modes: circular arc interpolation, linear interpolation, helical interpolation, ellipse interpolation.
- Switching control during operation: position/speed control switching, speed/position control switching, position/torque control switching.
Motion Control without a Complex Control Scheme
Servo motors driving equipment directly or through reduction gearboxes and other mechanisms are clearly a fast, powerful, and accurate way to achieve automated motion. The technology is well-established, but for too long its cost and complexity have reserved it only for relatively high-end applications.
This has changed with the availability of combined motor servo drive/controllers as these components provide significant programmability and other features, all incorporated right on board. Also, mid- and top-tier PLCs, and even select micro-PLCs, now include essential motion control instructions and capabilities. Using these newer technologies, it is possible to build effective motion control into more applications than ever before, at an appropriate price/performance ratio, while simplifying design and support efforts.
Figures all courtesy of AutomationDirect unless otherwise noted
About the Authors
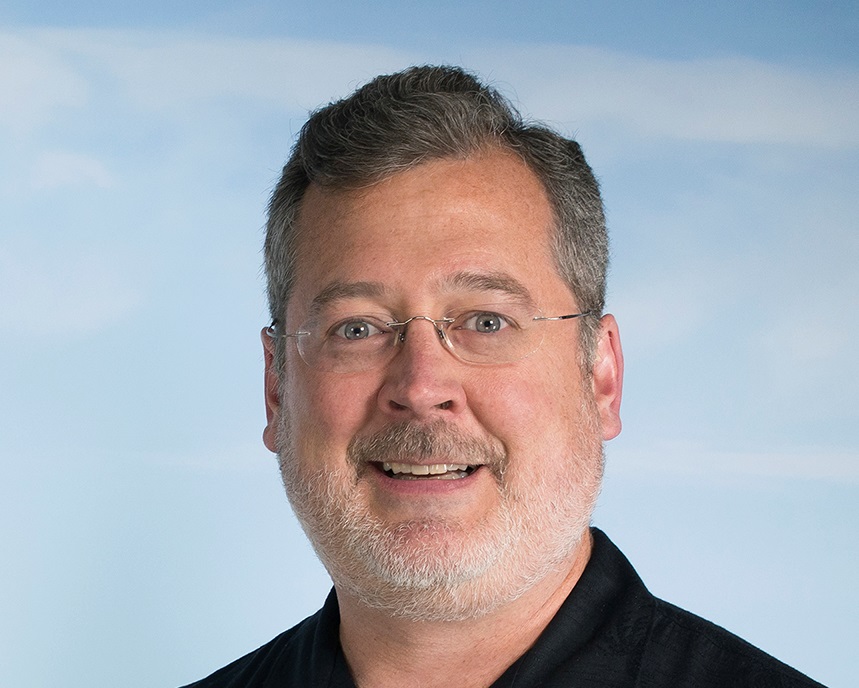
Chip McDaniel works in technical marketing for AutomationDirect and is a graduate of Georgia Tech. His decades of experience in the industrial automation field include designing, building and commissioning multi-axis servo systems, as well as the marketing of a wide range of automation products.
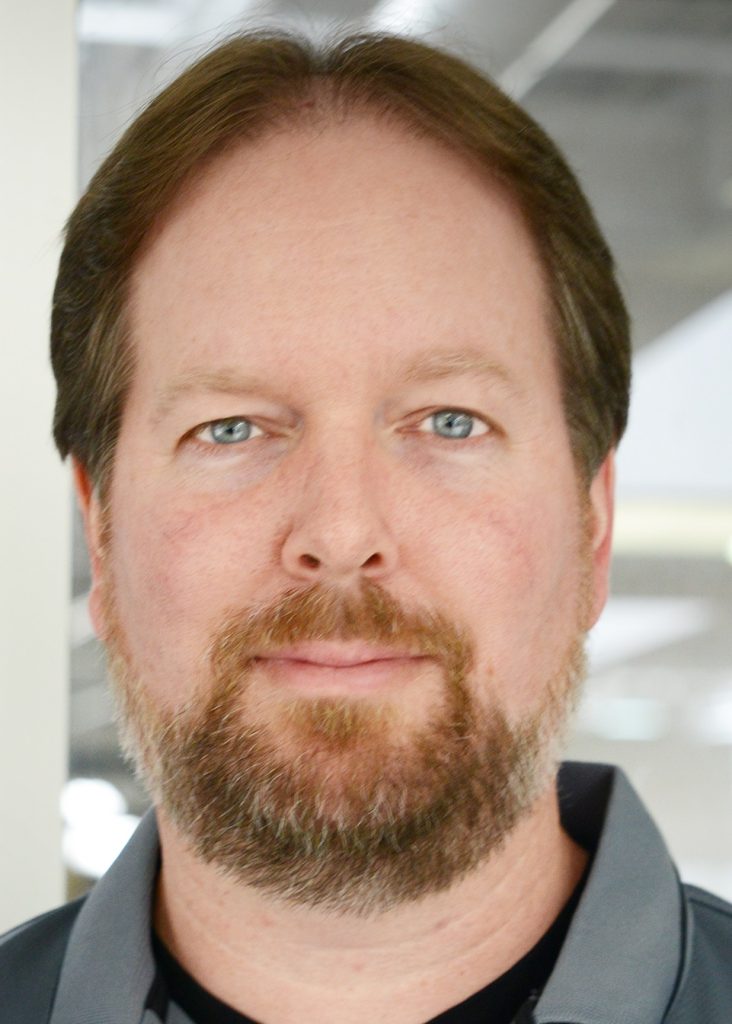
Joe Kimbrell is the Product Manager for Motion Control Products at AutomationDirect. He has over 25 years’ experience with automation, motors, drives, motion control, and servos, and has worked as engineering manager at a packaging OEM and at a multi-axis motion control integration firm. Joe holds a BSEE degree from Georgia Tech.