To help meet COVID-19 needs for sanitizing wipes, an HVAC contractor used their multiple-discipline experience and AutomationDirect products to quickly create automated filling machines.
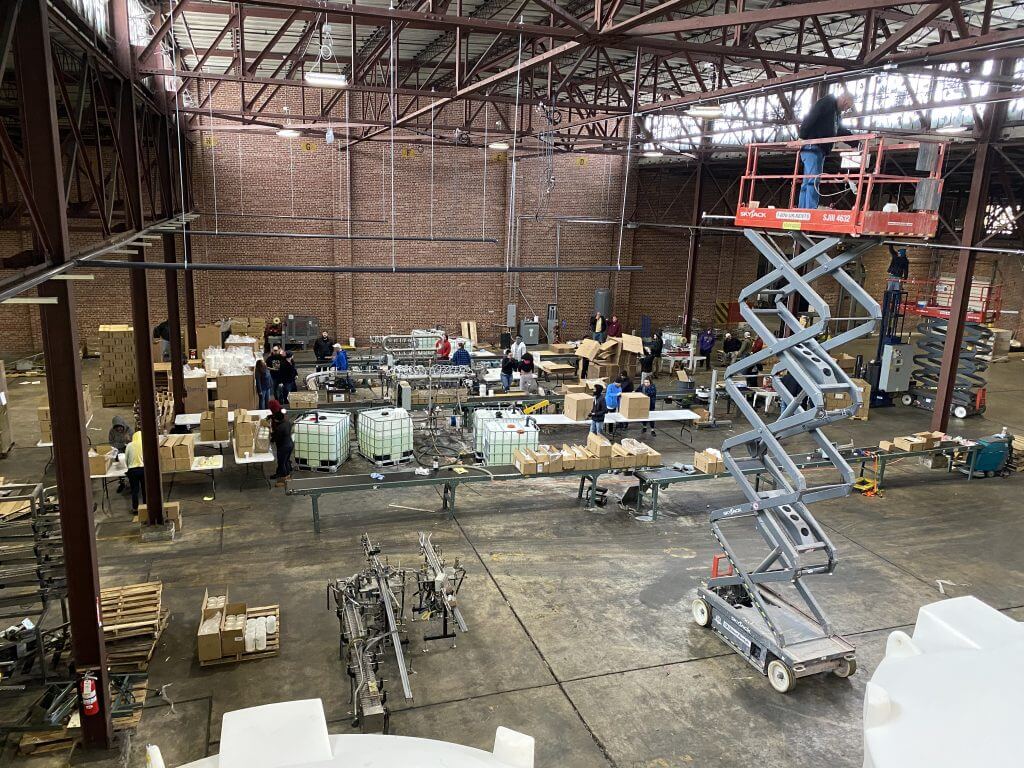
In the midst of the COVID-19 pandemic during the summer of 2020, a St. Louis manufacturer wanted to utilize available factory space to produce pails filled with sanitizing wipes. They engaged with their longtime HVAC partner Rock Hill Mechanical Corporation (RHMC), and they were able to quickly develop the necessary automation and instrumentation systems using AutomationDirect products. Two members of the RHMC team, Josh Stefaniak and Blake Young, wrote an article published by Hydraulics & Pneumatics in June 2021 titled Quickly Filling the Need, describing how they developed these projects.
Pulling Together Parts and Pieces
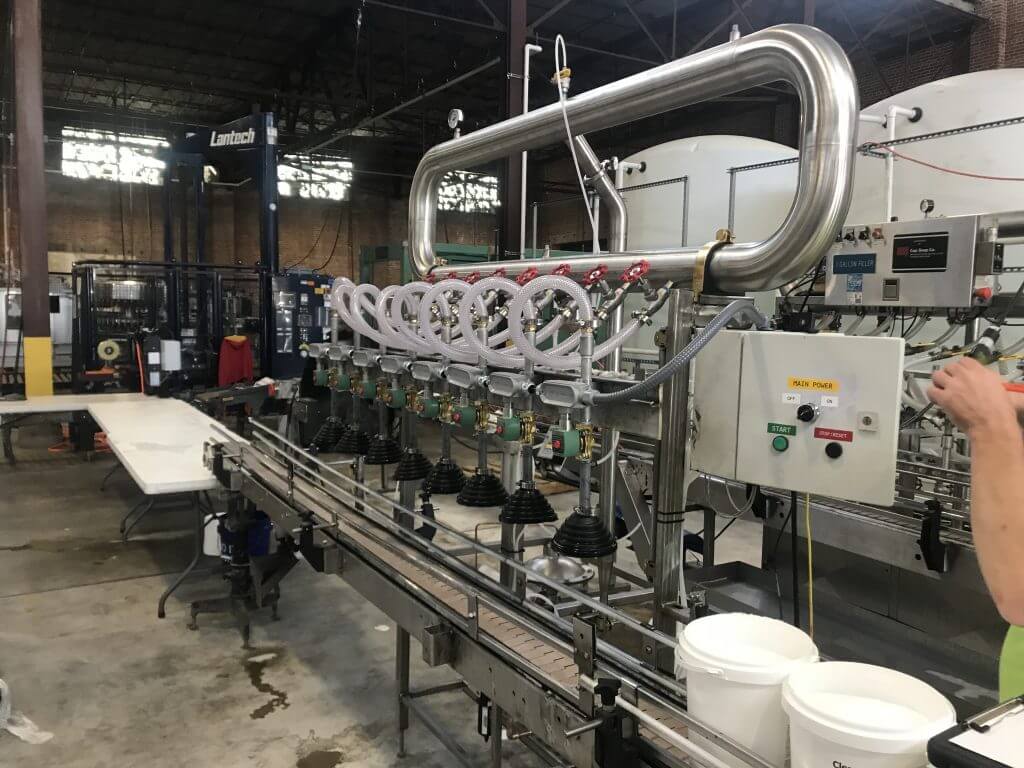
The project would rely on some preowned water jug filling equipment sourced by the manufacturer, repurposed to quickly fill pails instead. However, the first two machines were in disrepair and needed extensive rehabilitation. Even though the RHMC team did not specialize in machine automation, they had an extensive background in the mechanical, electrical, and automation expertise required to perform HVAC and facility automation work.
For the first machine, RHMC removed an old PLC and added hardwired switches, relays, and timers. This resulted in a functional, but largely manual, filling process. Improvements were made on the second machine, where RHMC salvaged what they could and then added an AutomationDirect CLICK PLC, supplemented with other parts and fittings.
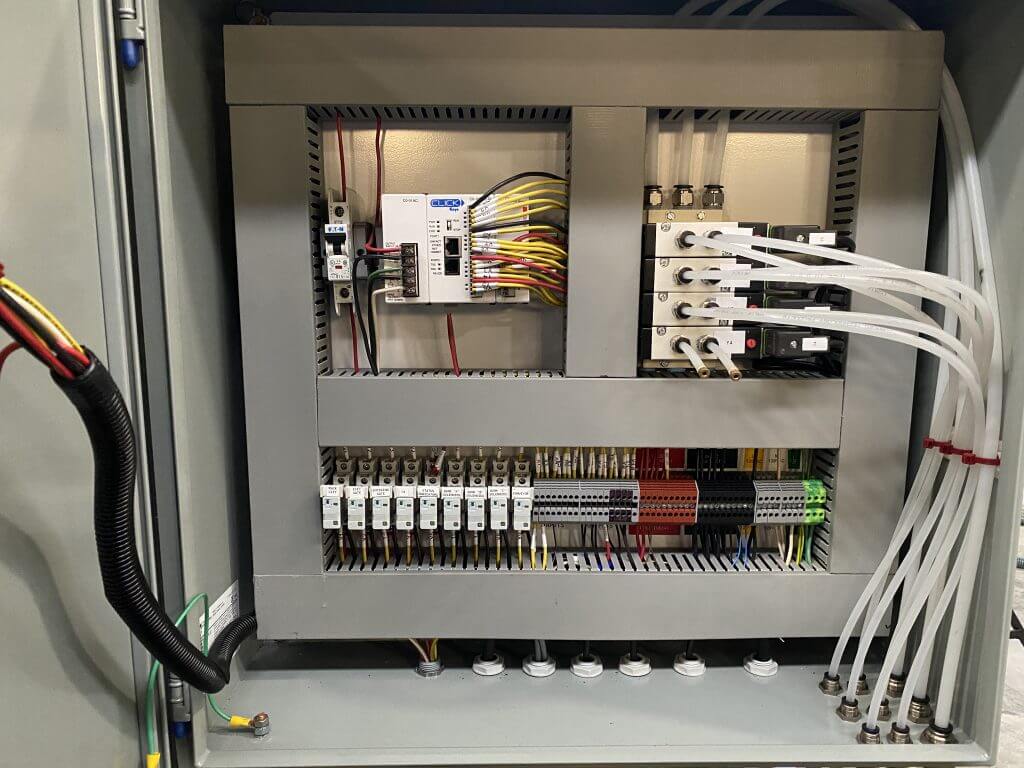
Based on the success of these two machines, the manufacturers commissioned RHMC to create three more filler machines from the ground up, using knowledge gained from the first two builds—and increasing the automation to include associated conveyors, box/tub handling, a supply manifold, and movable filler heads.
PLC Performance
RHMC regularly works with building automation systems but had not created PLC projects from the ground up before this engagement. However, they found the AutomationDirect CLICK PLC and free software easy to use, with an excellent price/performance ratio. By using some online resources and AutomationDirect YouTube videos, the team quickly designed and built the control panel and developed the PLC program.
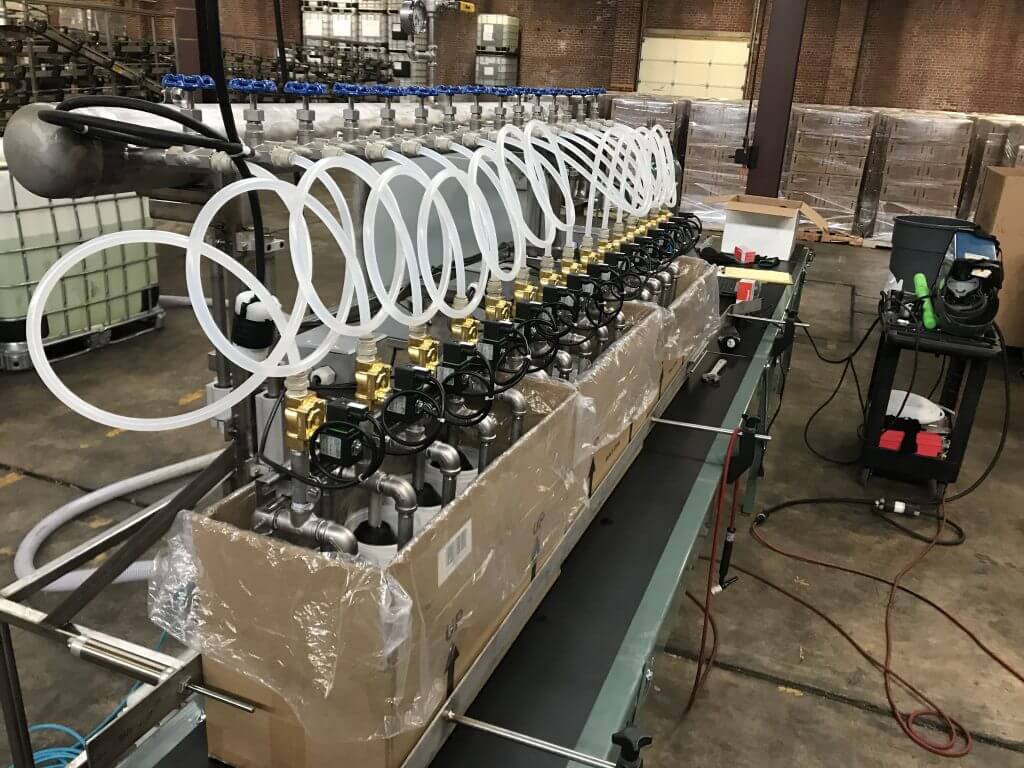
Due to the aggressive timeline, the third machine was built and tested on the factory floor to exactly meet the client needs, and it was quickly put into production. The project was scaled up as machines four and five were created and put into service at the rate of about one per month.
For each machine, RHMC was able to make mechanical and automation improvements while quickly responding to client requests. For example, the initial machines filled pails individually and required operators to load the pails into cases. Later machines were updated to accept cases with the pails already in them and to fill those pails while they were in the case, speeding up throughput and making handling easier for the operators.
Using AutomationDirect PLCs and other devices enabled RHMC to support their customer on a time-critical project that also benefited society. PLC-based automation was key to quickly developing and improving these systems, and it has helped RHMC expand their expertise and grow their business.
Check out the AutomationDirect.com website today to explore products that can help your company control its own automation destiny.
Read more application stories here!
All figures courtesy of Rock Hill Mechanical Corporation