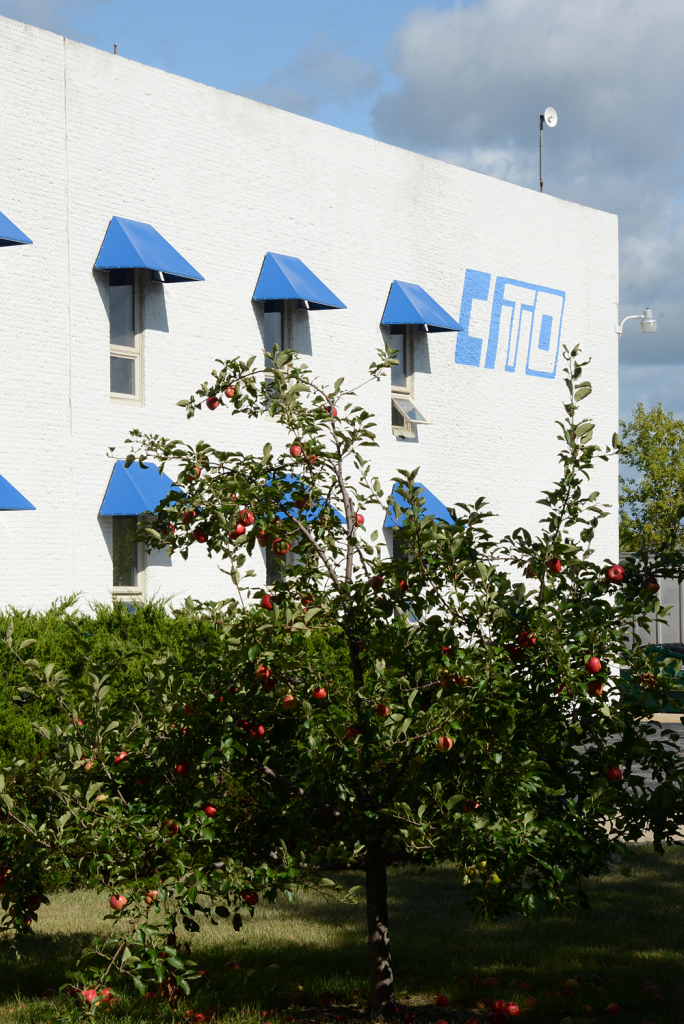
At the London International Exhibition in 1862, Alexander Parkes introduced the world’s first man-made plastic. His creation launched the beginning of the plastics industry, which would grow exponentially during the next 100 years to serve both manufacturers and consumers in many ways.
In 1965, Horst Wieder founded CITO Products, Inc. as a toolmaking, machining, and machine-building company. Fifteen years later, CITO, which stands for Cooling for Industry and Tooling Optimization, introduced PulseCooling™ technology to the skyrocketing plastic processing industry. This technology is used to precisely meet the heating and cooling requirements of each molding cycle.
As the industry moves to higher part complexity, more cavities, thinner walls, larger molds, more difficult-to-process materials, tighter processing parameters, and better inspection equipment, CITO Products is with them. PulseCooling™ uses a mold surface temperature controller which uses calculated pulses of cold water to cool the mold. This method has been proven to give the highest part quality and the greatest production yield at the lowest cost.
Specifically, it provides plastics processing companies with previously unobtainable benefits, including:
- Direct control over mold surface temperature, not just the waterline
- Quick warm up as just the molding surface reaches temperature versus the entire mold
- Higher production output comes from full flow, turbulent cooling with cold water
- Higher quality parts are ensured due to gradient dissipation during the soak period
- Optimized molding cycle comes from feedback of mold surface temperature
- Thermal drift is eliminated
A typical installation requires a temperature sensor inserted in the core and cavity side to “read” the mold surface temperature profile. This provides the PulseCooling™ controller with vital processing information. CITO Products also offers process controllers, process solenoid valves, and flow components to the injection molding, blow molding, and extruding sectors of the plastic processing industry to complete the technology.
Focus on Quality and Service
From its beginning, CITO Products has been family-owned and operated and manufactures its products in Watertown, Wisconsin. It also does tooling, fixturing, test equipment, and final inspections there.
“Our goal is to manufacture components and systems that truly improve the quality and profitability for customers,” said Max Wieder, Plant Manager. “Having all manufacturing, testing, inspection, and training in one place gives us full control of the manufacturing process and ensures a high-quality product for our customers.”
Its StackFlow™ product line complements the PulseCooling™ to provide the pulse-controlled water flow to the various circuits of the mold. The InLine™ Manifold allows pre-plumbing and pre-testing of flow and leakage, along with fast mold changes. The RotoFlow™ visual flow turbine is used with the FlowReadout™ for flow measurements. The ThermoFlow™ Analyzer measures flow in GPM or LPM and also gives temperatures (BTU) calculations.
In addition, CITO Products makes stackable StackFlow water valves, components, flow indicators, flow readout, sensors, anodized aluminum manifolds, and fittings and hose to help manufacturers achieve better cycle times, higher quality parts, and energy savings.
Modular Process Valves and Manifolds Available at AutomationDirect
AutomationDirect offers the CITO StackFlow series of modular process valves and manifolds.
“Customers love StackFlow valves because they are versatile, provide cooling for many applications, and are easy to assemble and disassemble,” said Max Wieder. “Each valve has a screen and can be combined with a flow indicating window or turbine, and any combination of modules and port sizes can be installed with a minimum of plumbing.”
The StackFlow system of high-flow, robust components can stack together to form a valve bank assembly. Each module includes common inlets at each end and an outlet discharge at the bottom. Manual and solenoid valves and distribution blocks can be included in the same assembly. Port adapters are sold separately, allowing multiple threaded connection options to the inlet or outlet port. Flow control outlet port adapters allow fine-tuning fluid flow out of the discharge.
End caps can be placed at one of the inlets and act as a blanking plate or include a temperature or pressure gauge. The new manifolds are rugged general-purpose models with 4 to 8 stations and come with a blue or red anodized finish. Standalone check valves, flow indicators, and numerous modular process valve accessories are also available.
“Our product offerings can work alone or together to help plastic processing manufacturers optimize their processes and improve profitability. We can help companies design specific solutions for their particular needs,” said Max Wieder.
Future Product Plans
CITO Products is constantly exploring energy-saving alternatives and will continue to work with our current and future customers to meet the ever-growing demands of the plastics industry. We strive to stay up-to-date with current manufacturing technology and processes to guarantee we continue to produce the highest quality and most efficient flow products and process controllers in the market. Our main goal for the future is to make PulseCooling™ known as an industry standard to increase energy savings across the world.