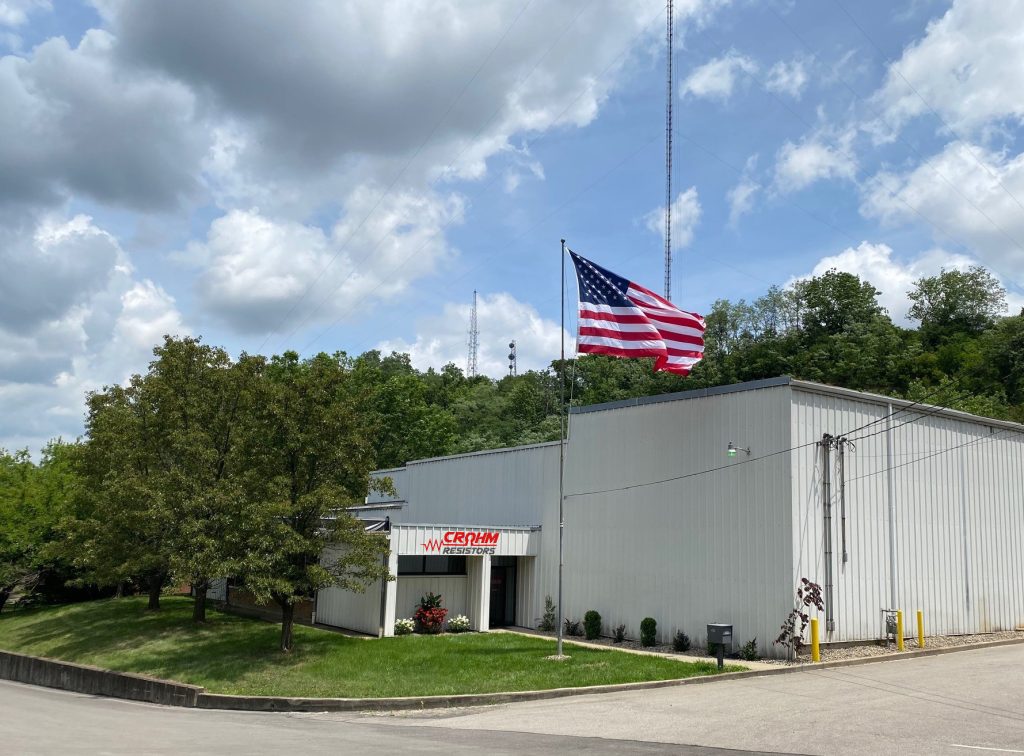
When you hop on a thrilling amusement park roller coaster, Ferris wheel, or pendulum ride, you probably don’t think about what makes it stop when it’s time to do so. More likely, you are relieved to finally get on the ride after standing in a long line! And chances are good that you don’t wonder what helps control speed in golf carts, locomotive trains, or transit systems.
However, Crohm, LLC, a resistor manufacturer based in Cincinnati, Ohio, thinks a lot about what’s needed to make these kinds of rides and vehicles stop smoothly. That’s because its high-quality resistors are used to control the speed and torque of variable frequency drive (VFD)/motor installations in these types of rides and many more systems.
You May Not Know Crohm’s Name, But You Rely on Their Resistors
While the Crohm organization is fairly new, the company’s team has more than 100+ years of combined knowledge of designing and manufacturing power resistors for various applications has enabled them to produce superb products that companies around the globe rely upon. Since its inception in 2019 by Mike Crowe and his sons Clay and Chad, the company has focused on producing top-quality power resistors and grounding systems. It has grown quickly since its founding. In 2021, Rusty O’Hara and Jason Waters joined Crohm as partners. Before that, they worked with Mike at other resistor companies for over 30 years.
“We are committed to offering the highest quality power resistors in the industry at prices that exceed our customers’ highest expectations,” said Rusty O’Hara, Crohm Sales Manager. “We strive to produce the industry’s best resistor products at our ISO9001 registered Cincinnati factory at a fair price. We focus on providing and producing great service and customer satisfaction and are one of the few resistor companies still manufacturing all of our products in the USA.”
Braking Resistors, Neutral Grounding Resistors, and Grounding Systems
Crohm’s major product line is dynamic braking resistors, neutral grounding resistors, and grounding systems. Braking resistors help control the speed and torque characteristics of variable frequency drive/motor installations. Electrical drives control the speed, torque, and direction of a downstream device, most typically a motor. VFDs provide speed control for AC motors such as those used in conveyors, fans, pumps, and shop tools. DC drives provide variable speed control for DC motors, making them ideal for applications requiring low-speed control, torque, and power.
Braking resistors dissipate a motor’s excess energy during deceleration, which prevents damage to the drive from overvoltage. They are often used in VFD systems – such as those in trains, elevators, and cranes – to do three things:
- Slow down or quickly stop a motor by draining excess voltage
- Feed excess energy into the VFD to boost voltage on the DC bus
- Protect more expensive components, such as the control system
“We offer a full line of braking resistors that are drive-specific to all the major manufacturers of variable frequency drives,” O’Hara said. “Our engineers also take pride in creating custom designs to a meet a customer’s very specific requirements, such as ohm, watts, horsepower and voltage, duty cycle, and braking torque.”
AutomationDirect offers Crohm VFD brake resistors featuring NEMA 1 enclosures and installed thermal switches in many popular resistance values from 3.7 to 400 ohms and power ratings from 240 Watt to 18 KiloWatt. The enclosures protect users from injury and the resistor from accidental damage, while the thermal switch helps protect the drive and resistor from thermal overload.
“The ohm value of a braking resistor should exceed the minimum ohm value published for a drive or braking module. Installing a braking resistor with an ohm value that is too low will cause harm to the drive or braking module. We collaborate with customers to ensure their resistors meet their intended application needs,” O’Hara said.
Crohm’s standard units feature CW wire-wound or CE edge-wound resistors installed in an indoor screened enclosure with a galvanized finish and connected with all stainless-steel bus bars. The resistors are wired to a terminal block in a compartment separate from the resistors or near the bottom of larger-size free-standing enclosures. The resistors are wired using high-temperature silicone or Teflon-coated wire and high-temperature lugs.
Crohm’s standard outdoor braking resistors feature a louvered enclosure with special ventilation components added to the top of the enclosure to ensure proper cooling. Its outdoor units feature all stainless-steel external hardware.
The company also offers other accessories and options. These include protective enclosures for indoor and outdoor applications and custom-engineered assemblies with factory interconnections and terminations. In addition, they offer thermal overload protection and powder coating or all stainless-steel construction.
Neutral grounding resistors and grounding systems are used to limit the ground fault current in a power system, offering invaluable protection to the system while removing critical arc flash hazards from personnel.
Crohm also produces resistors for numerous other applications, including transit systems, locomotive trains, off-highway mining trucks, golf carts, crane and hoist control, and even amusement park rides.
The Next Five Years of Serving Customers
Crohm is focused on steadily growing its business by offering quality products manufactured in the U.S. with quick deliveries and cost-effective pricing. One way it is doing that is by earning key certifications for its products.
In 2024, the company completed cCSAus certification for its entire line of braking resistors and just recently completed the UL / cUL certification for our neutral grounding resistors.
“We continually work with many customers throughout the world, constantly listening and improving designs to better meet their needs and expectations,” O’Hara said. “We have a large line of standard products and many custom designs to meet a wide variety of applications.”
The Crohm team is proud of its products and how customers rely on them for their important applications, such as transportation, amusement rides, and manufacturing systems.
“We look forward to continuing to grow during our next five years and beyond,” O’Hara said. “It is rewarding to serve our customers’ needs and have them hard-earned trust.”