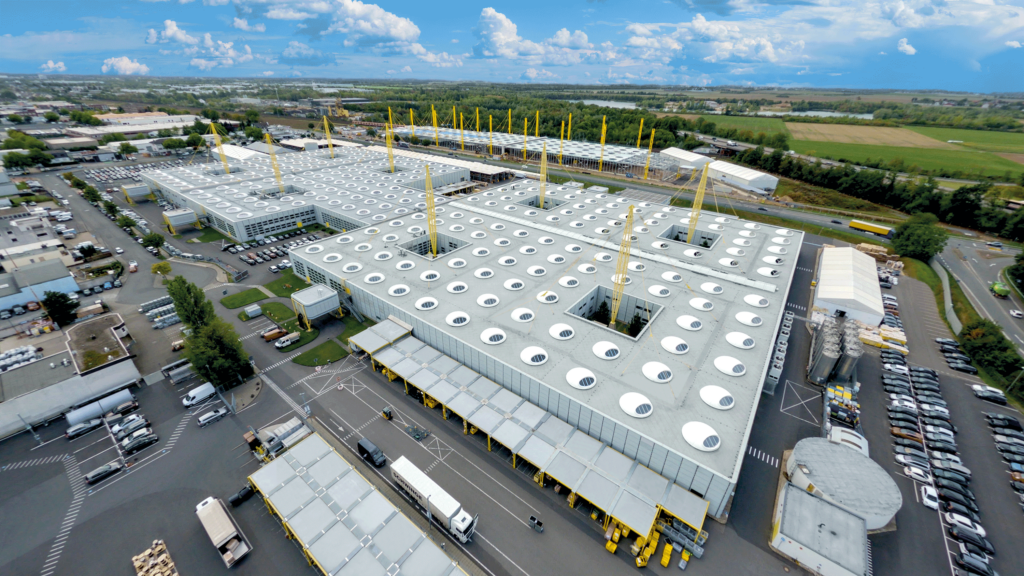
Around the world, 1964 was a pivotal year: Beatlemania was taking hold, Tokyo hosted the 18th Summer Olympics, humankind was preparing for space travel, and the World’s Fair in New York offered a peek at amazing innovations. That’s also the year when Günter Blase founded igus® – a complex technical polymer components supplier – in a double garage in Cologne, Germany.
For the next 20 years, igus focused on supplying those components to its customers. Then, in 1983, the company added reinforced plastic cable carriers and injection molded polymer bearings to its offerings and established a sales engineer network. Those additions began driving significant growth in igus’ products, size, and industry influence.
Today, igus remains a family-owned and operated company. It employs 4,500 people at its headquarters in Germany and at 35 subsidiary companies around the world. The company also has partners in another 80 countries. It now develops and manufactures high performance motion plastics that reduce downtime, increase service life, and save costs for moving applications.
It opened its U.S. company in East Providence, Rhode Island in 1985. Today, 500 people work in the that location that serves as the North American headquarters and distribution facility. Those employees manufacture select energy chain components, custom cables, custom and standard metal brackets, and adapter plates. They also conduct high velocity assembly and packaging of energy chain and iglide® products and conduct testing for ReadyChain® systems.
Focused on Motion Plastics
igus has four motion plastics product lines: e-chain® cable carriers, chainflex® continuous-flex cables, iglide® dry-running bearings, and drylin® linear bearings and guides.
AutomationDirect sells igus lead screw-driven and belt-driven linear slide actuators. They can be used as single-axis slides or can provide an economical means of creating high-performance XY or XYZ gantry systems. The SAW series lead-screw driven actuators offer a low-cost linear motion solution with travel distances from 50 to 750 mm, widths of 74 and 108 mm, and a 25mm pitch screw. ZLW series belt-drive actuators provide a longer travel axis with lengths from 200 to 1000 mm and widths of 74 and 90 mm, driven by a 70mm pitch belt. Drive couplings and mounting accessories are available to fit small NEMA framed motors and AutomationDirect’s SureServo motors.
igus products are used in many applications in the automotive, automation, material handling, and packaging industries. In the material handling industry, its e-chain® cable carriers and drylin® linear guides for shelving systems are used for pallet storage and retrieval machines, highly dynamic automatic mini-load, and mini-load and multi-shuttle systems.
In the automotive industry, igus iglide® bearings have been proven to last eight times longer than metal products, and they reduce costs by up to 40%! They dampen vibrations, are resistant to dirt and corrosion, and are embedded with solid lubricants to eliminate the need for external oil or grease. They can be found in seat lighting, seat adjustment, pumps, transmissions, and steering systems.
For the packaging industry, igus products help companies comply with the highest hygiene standards and process packages precisely, fast, safely, and reliably. Their maintenance- and lubrication-free machine parts made of high-performance polymers are used in tray sealing, dosing and filling, boxing, tubular bag packing, and forming, filling, and sealing machines. They are also used in pharmaceutical packing, weighing and inspection technology, and strapping machines. They are cost-effective, save installation space and weight, are maintenance free for 24/7 use, and are easy to assemble.
Testing for the Future
igus conducts extensive product testing under real-world conditions in a 41,000 square feet facility in Cologne, Germany. It compiles the test data and makes it available via online tools and service-life calculators that enable customers to find the best material and components for their application.
“We test between 1,500 and 2,500 new products every year,” said Frank Blase, CEO & Entrepreneur. “We will continue to invest in expansion in the coming years, thanks to the opportunities for growth provided by modern materials. This helps set us apart and is part of how we help customers be successful.”
Passionate About Serving Customers
Speaking of customers, igus is well-known for its focus on them.
“We often refer to customers to as the sun – the center of the igus solar system,” Blase said. “Like the sun, the customer gives us light and energy. Light in the form of ideas. Energy in the form of money.”
He noted that igus teams organize themselves around the customer, sometimes spontaneously, to get new ideas and wishes off the ground quickly. Leadership sees itself as a satellite that picks up and passes on signals inside and outside the system from employees, customers, suppliers, and politics.
Blase said, “As a company, it is our job to provide our colleagues with the means and atmosphere in which they enjoy working. Away with the bosses. The customer comes first. Everyone is a manager. We want our customers to say, ‘Whoa, they are good!’”
In North America, igus has sales engineers available in every major metropolitan area. It offers on-site technical support in 24 – 48 hours from its technical sales associates located in 21 U.S. states, one Mexican state, and two Canadian provinces. In addition, it offers customer service from 8 a.m. to 8 p.m., late shipping, no minimum orders or cut charges, and free CAD designs with quotations.
“We want to quickly implement their ideas and meet their unique specifications, even if that requires product and solutions innovation,” Blase said.
Supporting Employees and Fostering Future Engineers
In addition to providing customers with reliable, high-performance products and superior service, igus emphasizes open communication and learning among its employees. It runs a learning factory to help place the right people with the right qualifications in the right spot in its production process.
“Our innovative strength and rapid implementation of ideas are the basis of our success,” Blase said. “We encourage our team members to address anyone and express criticism honestly. This encourages fresh ideas and helps us stay in constant motion ourselves.”
In addition, the company offers employees the opportunity for regular training through igus Academy. Learning areas include languages, behavioral and sales training, lean management, design and marketing tools, leadership training, and more.
The company also takes pride in fostering students’ mechanical design ideas. Through the Y.E.S. (Young Engineers Support) Program, igus donates free products to robotics competitions, schools, and hundreds of thousands of students throughout the world.
Committed to Sustainability
As a plastic components producer, igus places its focus on reducing its environmental impact. In fact, its mission is to improve all types of motion with motion plastics while maintaining a carbon-neutral footprint and being the easiest company to work with.
“We have worked hard to be able to recycle and reuse 99% of our plastic waste,” Blase said. “We also have switched to exclusively green electricity and climate-neutral gas and aim to reach CO2 neutrality by 2025.”
Growing for the Future
igus looks forward to continuing to serve customers and to driving motions plastics innovations to propel their success.
“We have been an innovative company from the beginning when my grandfather founded the company in a garage,” Blase said. “We are committed to using our innovative materials to develop creative solutions for customers and to exceed their expectations through quick and reliable service and look forward to doing that for the next 60 years.”