Proper motor sizing precludes equipment failures, ensures efficiency and reduces maintenance issues
Bryan Sisler, a product manager for drives and motors at AutomationDirect, authored an article for the August 2019 issue of Plant Engineering titled Three Steps to Size Motors. Following is a summary, please click on the link above for the full text.
Electric motors, when implemented properly, are an efficient way of providing motion for machines and equipment, whether coupled directly or used with gearboxes and other mechanisms. There are many makes, models and styles, with AC motors being a popular configuration and the focus of this article. Designers can’t just bolt on the cheapest version that fits or inefficiencies and operational problems will result. This article examines how to size AC motors for an application based on environmental conditions, operational requirements and available power.
Benefits of Getting the Right Motor
Properly sized motors not only function reliably with the least wear and tear, but they deliver the best energy efficiency. High efficiency motors cost more initially, but that cost is typically offset by lower operating costs over the motor’s lifetime.
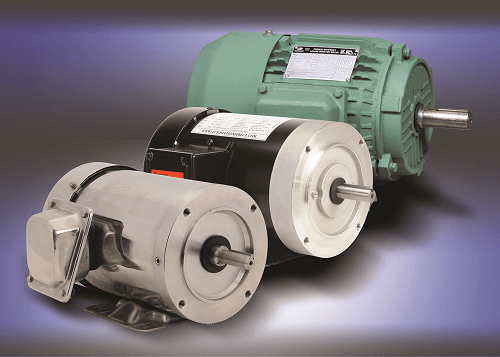
Heat is a prime reason for motor failure. Excessive heat from motor windings, bearing friction, process equipment or poor airflow can damage motor insulation and lead to problems. Improper installation such as misalignment or excess vibration can also damage the motor and associated equipment. Proper motor selection and installation avoids both issues.
Steps for Motor Sizing
The motor sizing process for a given application breaks down into three major steps:
- Investigating the load operating characteristics
- Considering the operational environment
- Planning for the available power supply
Bryan describes the balancing act when performing these steps:
Motor sizing steps should generally be performed in this order, but each factor relates to and affects the others. Properly accounting for these considerations and selecting a motor based on them results in selecting a motor that can carry out the work needed without having a shortened life due to premature winding, insulation or bearing damage.
A motor’s basic job is to spin at the commanded speed regardless of the load. Bryan proceeds to describe two common types of loads.
For constant torque loads—such as conveyors, cranes and compressors—the required torque does not vary much with speed, although the horsepower does vary with the amount of work being performed.
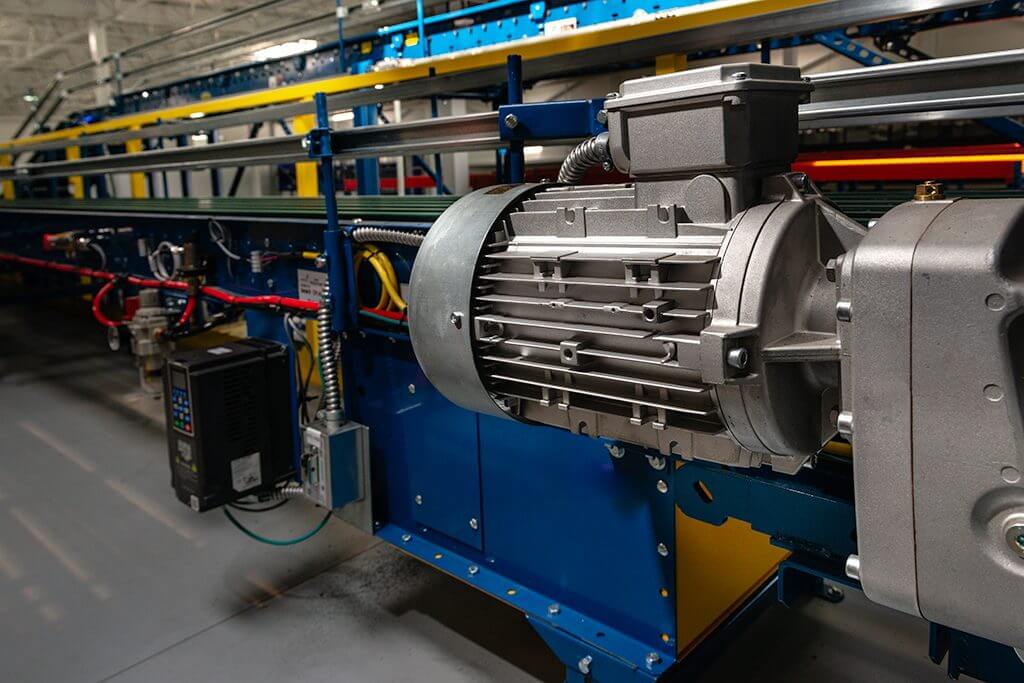
Variable torque loads, such as pumps and fans, experience torque that changes with speed. Motors for these loads should be sized for the highest, or peak, loading, according to the following formula.
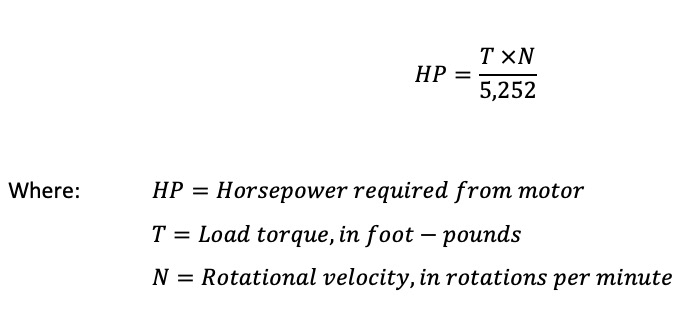
Using a variable frequency drive for adjusting motor speed is convenient for optimizing operation and can save energy. However, designers need to ensure the motor won’t run so slow that it can’t cool itself, and the motors themselves must be inverter-duty-rated.
Another consideration for sizing motors is how often they must run and stop, known as the duty cycle. The more frequent the stops and starts the more stress, which can be addressed by oversizing the motor.
Consider the Environment
Motors must be selected to survive temperature, moisture and contaminant conditions. Three popular styles are:
- Open drip-proof (ODP)
- Totally enclosed fan-cooled (TEFC)
- Totally enclosed blower-cooled (TEBC)
As the labels suggest, enclosed motors offer more protection then open motors.
Plan for the Available Power Supply
Selecting the operating voltage usually comes down to using what is available at a site, and Bryan offers the following additional guidance:
But where there is a choice, a higher operating voltage improves motor longevity. This is particularly important in smaller motors where the mass, fan construction and insulation systems may not adequately offload heat. A 3-phase motor is more easily reversed than a single-phase motor and is thus preferred for applications requiring forward and reverse operation.
Typical Applications
Bryan lists some typical motor choices for leading applications:
- Single-phase or 3-phase ODP motors:
Machines, conveyors, pumps, fans and air compressors. - 3-phase TEFC motors:
Same applications as for ODB motors but used for wet or dirty locations. - NEMA premium efficiency inverter duty TEBC motors:
Gear reducers, pumps, machine tools and other direct-coupled equipment installed in damp, dusty or dirty environments where long life and ultra-high efficiency is required. - Jet pump motors:
Specialized for jet pumps, well pumps and other liquid pumping applications.
Successful Motor Sizing Strikes a Balance
For any motor application, there are often multiple options to address the issues of load, environment and power supply. Following the steps in this article will help end users choose the best technical balance while minimizing initial and operational costs.