Andrew Waugh, Product Manager, Sensor and Safety Products at AutomationDirect.com, wrote an article for the September 2018 issue of Design World titled Wide and Narrow Views of Position Sensors, here’s a summary.
Limit switches, photoelectric switches and laser sensors all provide position sensing, but depending on the application some shine and reflect better. Waugh points out that there are many options and technologies to consider when specifying the use of these presence sensors in automated machines.
There is much overlap in functionality of these sensors, and there are also some selection considerations as each device has its advantages and disadvantages.
Mechanical limit switches are used in industrial automation systems to detect presence or position. Physical contact with the switch actuator, usually adjustable, activates these electromechanically- operated devices.
Photoelectric sensors, also called photo eyes, detect object presence or distance using light. Operation combines a light source from an emitter with and a receiver that detects changes in light intensity reflected by the target object.
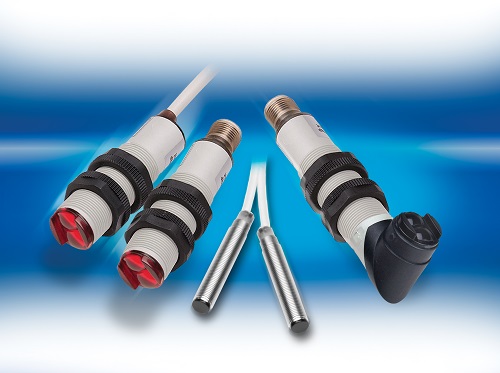
These AutomationDirect photoelectric sensors detect object presence or distance in a wide range of industrial applications, and typically contain all required optics and electronics in a single unit.
Laser sensors operate like photoelectric sensors but with a much more focused light source to detect presence or measure distance, depending on the configuration. Laser photoelectric sensors detect presence. Laser distance sensors measure distance, as the name implies.
The Tried and True Limit Switch
Limit switch actuators are available in many forms including an adjustable arm or a plunger, each mechanically linked to an electrical switch block inside the housing.
Purely mechanical in operation, most limit switches use linkages and movement of the sensed object to operate the switch contacts. Heavy-duty contacts are common in limit switches, enabling switching of higher currents than other presence and position sensing devices.
Limit switches must touch an object to detect it, which limits sensing distance to the travel distance of the switches rotary lever arm or plunger-type actuator. However, this short sensing range provides reliable detection of an object regardless of its color, shape or size. Care must be taken to ensure the object touching and activating the actuator roller or plunger does not damage it.
When looking at presence sensors’ repeatability, or repeat accuracy, it is important to understand when it’s needed because many sensors don’t excel in this area. For applications where a high degree of repeatability is needed, precision touch limit switches are available with an accuracy of 5 microns or less.
Diffuse, Retro-Reflective and Through-Beam Photoelectric Sensors
The typical light source used in the emitter, or sender, of a photoelectric sensor is visible red or infrared. The light is reflected by the object, and then collected by a receiver where the intensity is measured. These emitter and receiver elements can be installed in the same housing or in different housings.
Diffuse and retro-reflective configurations are available when an emitter and receiver are integrated together. Diffuse sensing bounces emitted light directly off an object and back to the receiver in the same housing.
A through-beam photoelectric sensor uses a configuration where the emitter and receiver are in different housings. Through-beam photo eyes provide the longest operating distances since the emitter shines light directly to the receiver.
Laser Sensor Operating Principles
Laser distance sensors are available in diffuse, background suppression and retroreflective types. These sensors provide accurate distance measurements using CMOS or transit time technologies.
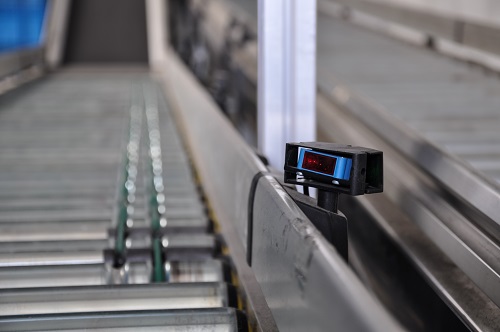
Both short-range CMOS—and this long-range, time-of-flight Wenglor photoelectric laser sensor—are often used in material handling applications.
Laser light is focused, keeping it in a narrow beam over long distances. The light color is also held to a narrow spectrum. This well-controlled light source can be triangulated or pulsed, with each emission or pulse measured to enable distance readings.
Both photoelectric and laser sensors have a sensing range from close to far. Adjustable light intensity and sensing thresholds help tune this range. This wide and adjustable detection makes the photo eye a popular choice for presence detection, and it has an excellent sensing range-to-size ratio. As the sensing distance increases or a more accurate or a smaller spot size is needed, laser becomes a popular choice.
Mechanical limit switches have moving parts that can wear out, so the speed of actuation must also be limited, making it unsuitable for high-speed applications. The electronics in both photoelectric and laser sensors enable fast switching operation. With operation speeds from 25 Hz on the low end to thousands of times per second, high-speed applications are possible, and the number of actuations is not a concern.
Applications Touch, Light and Laser
There is much overlap in the application of limit switches, photoelectric sensors and laser sensors, so carefully check the device’s specifications; how it will fit into an application; and how it will be used. Limit switches are just one of the many solutions to use in automated applications, but they are a simple and rugged choice for presence sensing, providing reliable detection of many components or parts.
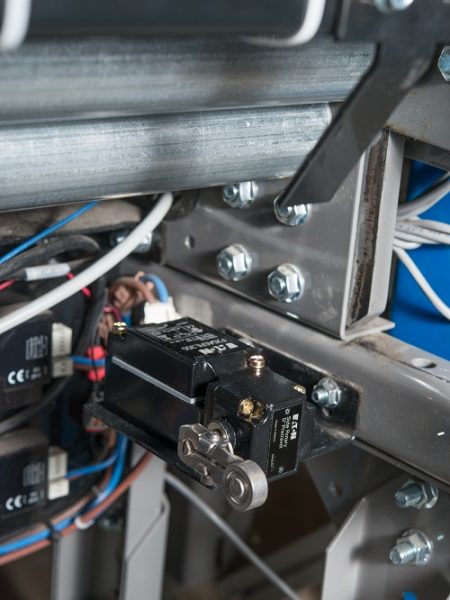
A very common application for a limit switch is detecting the closed position of a conveyor lift gate.
Photo eyes are probably the best general-purpose position sensor. They have a longer sensing range than other presence sensing options such as inductive, magnetic, capacitive and ultrasonic. Available in a wide range of configurations and housing sizes, they fit well in many applications.
Lasers are best for precise measurement of distance in applications where the part or component can’t withstand contact with a mechanical switch. Close, far, dusty or clean—they work well in most environments. They also work well for small part detection, much better than the other two technologies.
To read more articles about discrete sensing, click here.