Industry has a seemingly endless variety of machine and process control applications, and a correspondingly wide range of controller choices. When selecting a controller, there are many similarities and some differences to consider. And, while some controllers will control just about anything, others may be more suited for a particular task.
The main controller choices include programmable logic controllers (PLCs), programmable automation controllers (PACs), and industrial PCs (IPCs). Within these controller types there is a wide range of functionality as well, from low-end to very advanced.
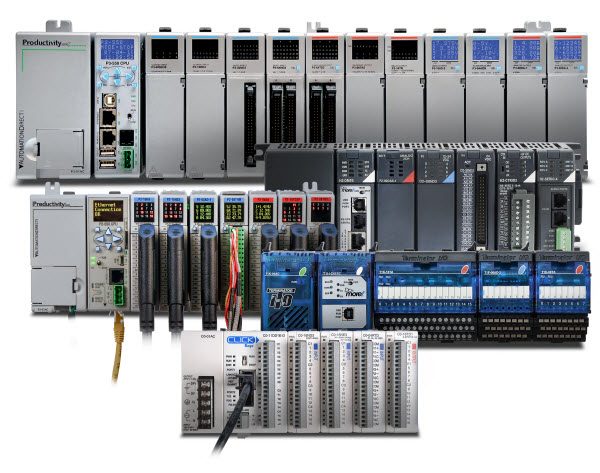
Controller Types
The tried and true PLC started replacing relays about five decades ago, and it remains a popular choice. Whether configured as a fixed I/O brick PLC or an expandable rack-based system, it’s suitable for automation applications small to large. It has adequate communication capabilities and is often programmed in ladder logic, with other options available. It’s a competitively priced and an easy-to-support option for machine control.
A PAC is an advanced PLC controller, separating itself from a PLC with its more advanced hardware and capabilities such as expanded data logging and communications. It also has more programming options due to use of the International Electrical Commission (IEC) 61131-3 programming standard’s multiple languages.
The IPC is basically a PC for industrial use. It operates much like any PC and provides a high level of processing power, communication and data storage. With most offerings, reliability concerns due to unstable operating systems and other issues are a thing of the past.
Feature Talk
Specifying a controller’s features (Table 1) is easier if you understand the need and desired results of the application. Determine what you must have, starting with the basics such as communications, protocols and I/O counts. Then consider some of the more advanced features you’d like to have such as integration capabilities, advanced programming, extensive data handling and sophisticated cybersecurity.
Table 1: Typical Features Found in Industrial Controllers*
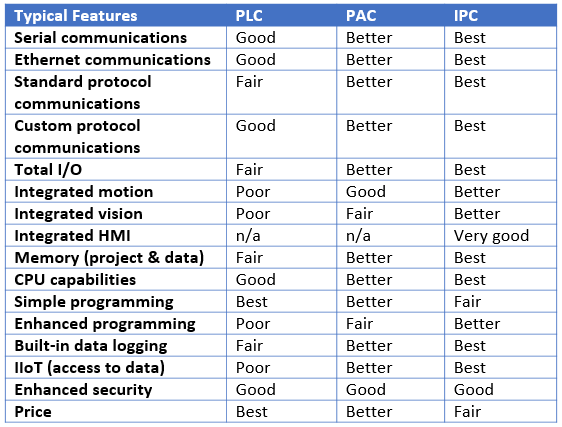
*All rankings are subjective, your results may vary
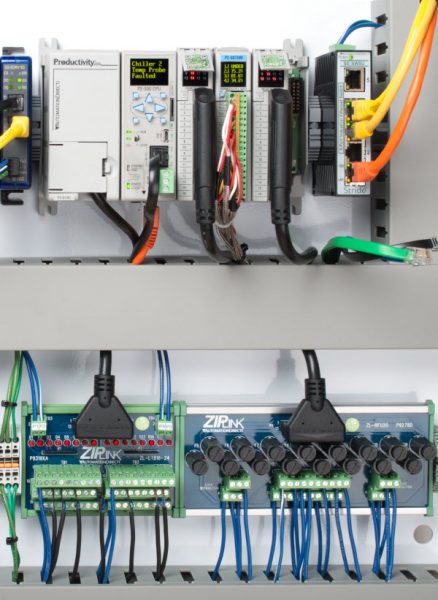
Serial communication is still popular in industrial applications for providing connections to many standard RS-232 and RS-485 devices using popular protocol such as Modbus RTU. However, Ethernet is becoming more popular and is really a must for most new applications. Ethernet enables Industrial Internet of Things (IIoT) and other web-based applications, and also provides communication using Modbus TCP, EtherNet/IP and other leading industrial Ethernet protocols.
Controller I/O, integrated motion and vision should be carefully reviewed for each application. Features such as memory for the logic program, data files, tag names and descriptors for the program should be considered, as well as CPU capabilities including scan times.
Programming capabilities almost always include the popular ladder logic language. With more advanced applications, other programming choices such as structured text, functional diagram and instruction list may add flexibility.
Some controllers include built-in data logging. This data is happily consumed by the IIoT with the proper connections through Ethernet and the internet. Because of this increased data storage and delivery, along with remote access, security is built-in to some controllers. This is typically in the form of usernames and passwords. All these features come with a price, so users must shop carefully.
The Best Controller for the Application
Certain controllers work better in some applications than others (Table 2). However, there isn’t really a perfect controller for an application since there is so much feature and capability overlap, especially considering the convergence of the PLC and PAC.
Table 2: Capabilities of Industrial Controllers in Typical Applications
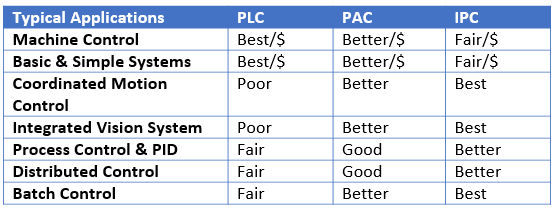
*All rankings are subjective, your results may vary
The PLC is a great fit in many machine control applications, which is where it started as a relay replacer decades ago. Small brick PLCs work best in applications where low cost is paramount such as small machines. Larger PLCs have many of the capabilities of the PACs.
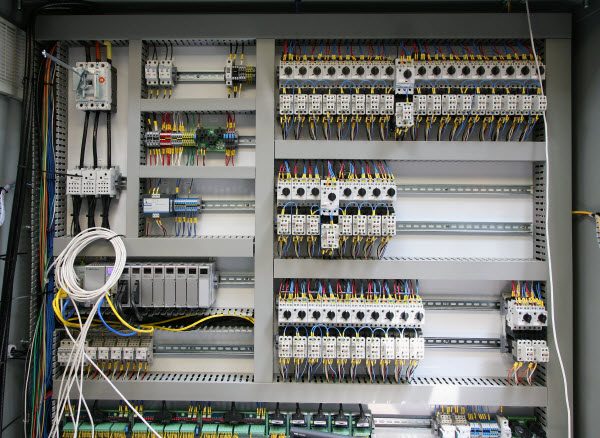
The PAC is a bit of overkill for small applications, but it has the required power and performance for medium to large machine automation applications. It works well with high-end coordinated motion and integrated vision applications, especially where multiple axes and multiple cameras are used. It also provides a high level of PID control for multiple loops.
The IPC is best suited for medium to large applications especially process, distributed and batch control applications. Applications with extensive data storage and communication requirements are a good fit, as with a server connected to multiple PLCs and PACs.
There are many choices for a control solution, so it takes time to determine which controller works best. Understanding the application is important to specify just what’s needed without going overboard.
For more information, please see the article How to choose the best controller for each application in the January 2017 issue of Control Engineering, authored by Jeff Payne, a Product Manager at AutomationDirect.
To read more articles about programmable control, click here.
Originally Published: January 2017