Sensors and transmitters convert a variety of physical properties into discrete and analog signals for use by automation controllers. AutomationDirect offers an assortment of these devices for use in the design and operation of machines and processes to create reliable, robust and consistent automation. It may only take a small change in a physical property to cause a machine fault, so detection of any variations can prevent problems and optimize the machine.
While there are many physical properties that can be measured and detected by sensors and transmitters, this blog will take a quick look at ten of them. Applications for these sensors and transmitters will also be covered briefly.
Is a sensor a transmitter?
While often used interchangeably, we’ll consider a sensor a discrete device such as an overtemperature switch. A transmitter, on the other hand, reads continuous values and converts them to an analog signal such as 4-20 mA or a fieldbus signal. A temperature transmitter is an example, but a transmitter could also be a digital pressure switch combining both analog and digital signals.
These sensor and transmitter signals typically connect to PLCs HMIs, SCADA systems, data loggers and the Industrial Internet of Things.
Ten physical properties detected by machine sensors and transmitters are:
- Temperature
- Pressure
- Flow
- Level
- Current
- Voltage
- Presence
- Distance
- Position
- Speed
Sense the Heat
Temperature control and monitoring is a popular function on a machine, and an adjustable temperature switch works well in overtemperature and thermostat-like applications. Sometimes that’s all that’s needed, but more complex control and monitoring often requires thermocouples and RTDs connected to transmitters, or to an appropriate PLC input modules.
Thermocouples and RTDs typically output a millivolt signal, so a temperature transmitter is used to extend the signal range using a 4-20 mA scaled analog output. These signals are easily calibrated and work well in ovens, tanks and machine processes.
Feeling the Pressure
The air preparation unit and related pressure switch is an important part of the pneumatic system. If pneumatics are used on a machine, the air must be clean and dry, and its presence must be sensed. A simple digital pressure sensor works well, with an adjustable pressure set point and local indication of the actual pressure. Some of these pressure switches have adjustable set and reset pressure levels for control of a compressor or pump.
A pressure transmitter and its related analog signal can provide more precise and adjustable control. These transmitters can be used for compressor monitoring, gas and leak detection, and monitoring vacuum levels of pick-and-place vacuum cups. Differential pressure monitoring is also an option for monitoring air filters, HVAC static pressure, clean room access, and draft pressure in ovens and dryers.
Feeling the Flow
Paddle wheels or a floating ball are often used to indicate flow. Flow switches use a spring-held piston lifted by fluid flow. The piston position is then sensed by an inductive sensor. These switches often include manual adjustment for an adjustable fluid flow setpoint. Common applications include verifying machine tool coolant water flow.
If actual flow needs to be monitored, a flow transmitter is used to provide an analog output proportional to flow. A common way, among many, to measure flow is through measurement of differential pressure before and after an orifice plate.
Is it Half Full or Half Empty?
Float level switches are a simple, low-cost option to monitor liquid level. Choose carefully with these float switches as they are available with many mounting configurations and material construction. Tank level sensing is an obvious application for these devices, and these devices also work well as a backup sensor for high-high or low level applications to prevent spills or running a pump dry.
Level transmitters provide continuous measurement or monitoring of liquid and provide a 4-20 mA analog output signal, often by sensing the hydrostatic pressure created by the height of a liquid above the device in a variety of tanks. A non-contact method, using an ultrasonic liquid level transmitter, is better for glue, paint and other similar applications.
Current and Voltage
While current and voltage detection or measurement use different sensors, their purpose is much the same, which is to sense if power is on in AC and DC circuits. A current switch combines a current transformer or hall effect sensor and a signal conditioner with a limit alarm to create an adjustable or fixed trip point. Power on-off status, overcurrent conditions and jams on conveyors are common applications.
Current transducers add the ability to measure actual AC current, true RMS current or DC current. These devices work well for monitoring operation of VFD and SCR controlled loads. They can also provide true RMS current to monitor battery bank charging or load current in DC applications.
Voltage transducers are particularly useful in detecting under voltage or phase loss conditions in 3-phase circuits. Overvoltage conditions, cause by excessive motor regeneration for example, can also be detected to help identify and avoid motor and drive issues.
Detect Presence, Distance, Position and Speed
Photoelectric sensors are very popular for presence detection. Inductive sensors are popular as well for sensing a variety of metal objects, especially ferrous ones. Capacitive sensors have some special capabilities to see through paper, plastic or cardboard—and to detect liquid. And ultrasonic sensors can detect just about anything regardless of the material or its characteristics.
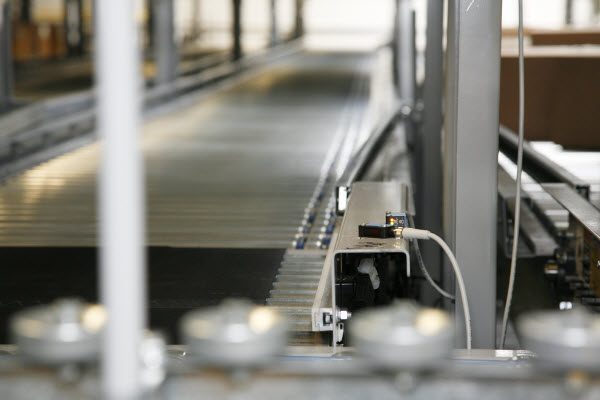
Accurate detection of presence can be used for distance measurement. This extends to the use of laser distance measurement transmitters to provide a wide range of measurement. Short-range distance sensors, < 5mm, have resolutions below 8 µm. Measurement ranges over 10 m are available, and while resolution suffers at these ranges, its’ still sufficient for many machine and gantry applications.
Although any of the sensors above can sense a position, an encoder is a common choice to detect rotary and linear position. Velocity and direction monitoring are also available when using encoders. Encoders are available in two common configurations, incremental and absolute, with several output options. Motion sensing is its strong point, often required in machine tools and multi-axis positioning applications.
Many sensor and transmitter choices are available for detecting or measuring just about any physical property. Create a design that uses these devices on your machine, equipment or processes; connect the devices to an advanced controller; and quickly realize improved system operation.
For more information, please see the article A Primer on Sensors for Machine Automation in the March 2017 issue of Machine Design, authored by Chip McDaniel, technical marketing, AutomationDirect.