A variety of analog signals must be transmitted to a PLC for monitoring and control, with each processed to ensure correct operation.
Winn Paulk, the Automation Controls Group Product Manager at AutomationDirect, wrote an article for the November 2018 issue of Processing magazine titled Configuring analog devices to integrate with PLCs. All programmable logic controllers (PLCs) are connected to some field devices, says Paulk.
Whether it is discrete input signals, analog signals or via a communications protocol — the PLC must have data from external devices to control and monitor a process.
Analog inputs are complex because analyzers, instruments and other devices produce a wide variety of signals.
Common types of analog variable inputs to a PLC include:
- Temperature
- Pressure
- Flow
- Level
- Weight
- Speed
Temperature signals are probably the most popular and include thermocouples, resistance thermal devices (RTDs) and thermistors. Thermocouples offer fast measurement speed and are often the lowest-cost solution.
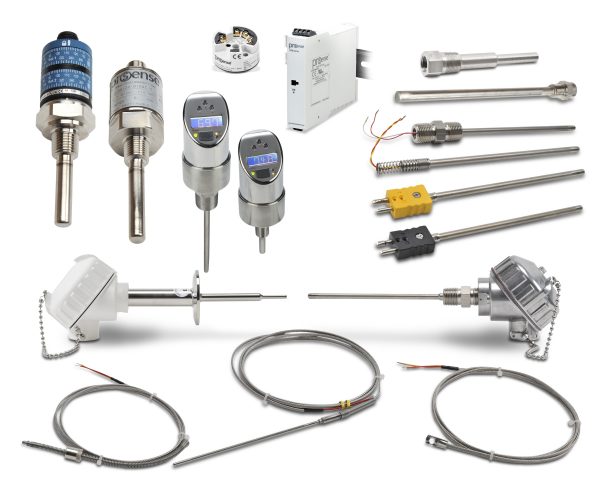
RTDs have a more limited temperature range, but are more accurate and repeatable. A thermistor, a thermally sensitive resistor, also has a smaller sensing range when compared to a thermocouple, making it more useful for commercial than industrial applications.
Pressure is another key process signal. Air pressure and compressed gas measurement are very common. Fluid pressure, such as hydraulic and water, are other popular measurements. While most pressure transducers come in voltage and current configurations, others use digital communications to send a scaled value.
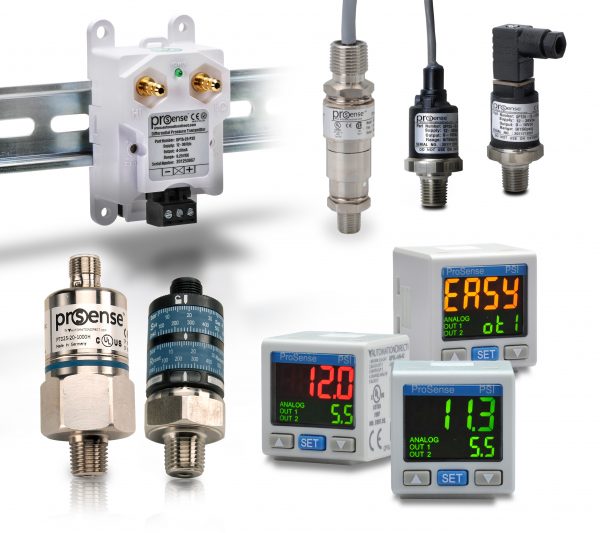
Flow measurement of liquid media offers reliable flow detection via a switched, pulsed output from an inline device, or via an analog output proportional to flow rate with a transmitter. Flow transmitters often use a sensing principle based on differential pressure, which can be fast and precise. Mag meters operate using current-carrying coils to generate a magnetic field to measure flow rate of conductive materials in a pipe.
Level transmitters are often installed on tanks and vessels, and many different types are available including radar, differential pressure and ultrasonic.
Weight is another process signal monitored by a PLC. The signals originate from load cells or strain gauges. Process signals proportional to speed are available using tachometers and encoders.
Signal Types
Process signals are transmitted to a PLC in a variety of ways including discrete, analog, specialty modules and communications. Most flow, level, pressure and load cell device outputs are analog, typically current or voltage such as 4–20 mA, 0–10 Vdc or +/-10 Vdc. For other signal types, accommodations must be made at the PLC.
Specialty PLC input modules are available for thermocouple, RTD and thermistor signals. Other specialty modules include high-speed input modules with timer, counter, pulse/direction and quadrature signal functions.
Digital communication options are also available such as serial, EtherNet/IP, IO-Link, EtherCat and others. The main advantage of digital data links is the ability to send data in addition to the process variable including secondary variables, diagnostics and calibration information.
Once a process signal is properly received at the PLC, it often needs processing and handling including filtering and scaling. Raw signals can be scaled in the PLC, often using dedicated function blocks. PLCs are often equipped for this, Paulk says.
Some PLC modules provide calibration or other converting functions within hardware configuration parameters. A PLC program can also be written to calibrate a process signal device, and to prompt the operator to perform the needed steps to complete the calibration.
Boiler Monitoring and Control
One application utilizing a wide variety of process signals is a wood-fired or biofueled boiler.
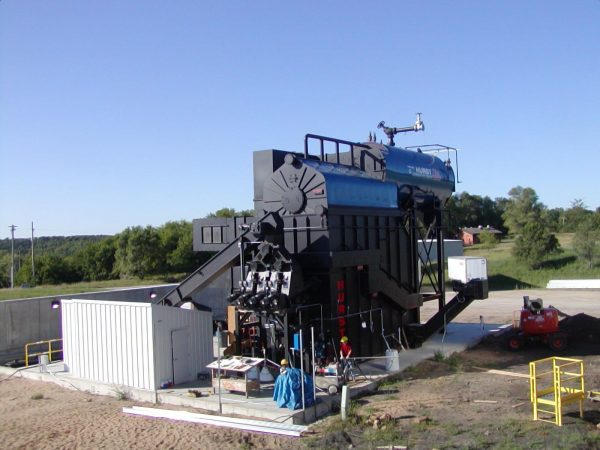
Pressure is an important process signal in boilers for monitoring and controlling steam demand and header pressure. A PLC monitoring boiler pressure will also probably monitor other variables such as temperature, level and flow.
The PLC monitors many temperature sensors for makeup water, water fed into coils, steam temperature and temperature drop at several locations throughout the boiler.
Level sensors are used to monitor chip and sawdust levels to ensure enough solid fuel is available. The PLC also monitors the level of a water tank used for makeup water, and the level of condensate tanks.
Flow of water through several parts of the boiler is monitored as well. Air flow may also be monitored to detect issues such as blockages, and to help fine tune the process.
Paulk says all these sensors need to be connected properly to the PLC:
Correct signal levels and PLC hardware must be used to make connections to analog devices. The specifications of all the devices involved must be carefully checked, and signal processing will often be needed to monitor and control the process.
To read more articles about Control & Signaling Devices, click here.
Originally Published: December 2018