So the story starts with you looking at a plant full of equipment, some new, some old, with the operators working hard to meet production requirements. If your safety sign reads: “We Have Worked 1 Day(s) with Zero Accidents”, then maybe it’s time to review and improve your plant safety program.
It’s everyone’s responsibility to work carefully and report unsafe conditions on the plant floor. In particular, personnel working around machines must be aware of and protected from hazards created by point-of-operation, pinch points, rotating machinery, flying debris and sparks.
Plant summer shutdowns and holidays are a great time for maintenance folks and engineers to plan for machine and process upgrades. Safety upgrades are appropriately sized projects to complete during these shutdowns—but the work must be carefully identified, defined and scheduled to be successful. Another key component to success is involving operators and maintenance techs every step of the way, as they are on the front lines where hazards are most pronounced.

Safety starts with the right plant culture, which creates awareness and prioritizes safety over production.
Safety can then be improved through this five-step program:
- Review and document plant safety requirements
- Perform a risk assessment on all machines
- Order and install signs identifying hazards
- Identify and install new safety components
- Train operators on new requirements and designs
Be Safe, It’s Required
If your facility doesn’t have safety requirements, the first step is to create them. But in most cases, safety requirements exist and just need to be reviewed, updated and disseminated to all plant personnel. Proper plant policy, standards and requirements go a long way toward promoting vigilant workers.
Assess Machine Risk
A key to improved safety is to identify, analyze and remove hazards. From a machine safety and related electrical standpoint, there are many potentially hazardous situations such as boom, crush, zap, burn and cut. Lots of online information is available regarding risk assessment, allowing you to make a proper assessment and answer these three questions:
- What are the hazards?
- How can the hazard hurt personnel?
- How can the hazard be removed or controlled?
Answering these questions for all machines in your facility will likely identify many areas for safety improvements. Make a list and start going after the low hanging fruit, and continue until the tree is picked clean.
I See Safety
With a safety mindset in place, it is important to identify specific hazards with signage. Not only do signs remind workers to think about safety every day, they also point out hazards that may go unnoticed. Whether it’s chemical, electrical, personal protection, personal awareness or machine safety—all hazards must be identified.
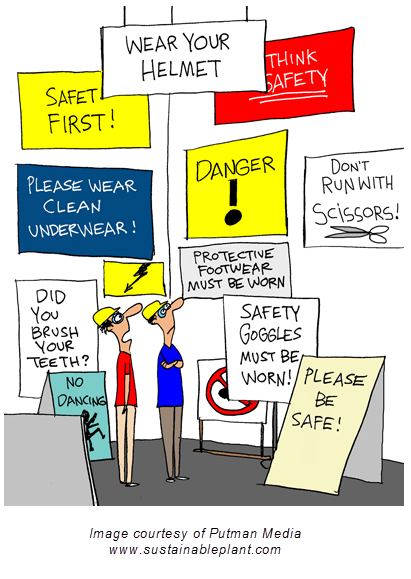
OSHA and ANSI Z535-2011 standards exist to present safety and accident prevention information. There are hundreds if not thousands of signs available for purchase, but don’t go crazy as too much of a good thing will overwhelm operators and maintenance techs.
Review Designs, Install Components
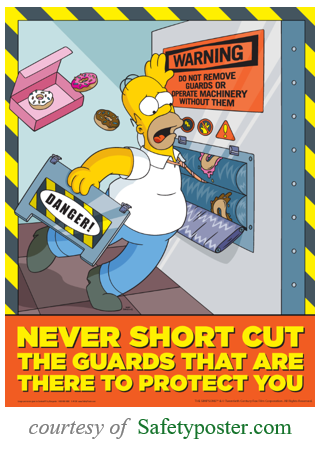
The risk assessment will likely show that some machines have had safety systems modified, adjusted, bypassed, disabled or removed.
It will also probably show areas requiring installation of new safety components. In both cases, the safety systems must be brought up to date, either by restoring original designs, or by adding new components.
Typical safety design and maintenance improvements projects include:
- Improve point-of-access control using a light curtain
- Install two-hand control on assembly equipment
- Upgrade poorly designed guarding
- Replace troublesome guard safety switches
- Improve guard mechanical design and safe-state monitoring
- Add emergency stop pushbuttons
Remember, some safety systems are disabled by operators because they are poorly designed, and in these cases it’s better to improve upon the design instead of just restoring the machine to its original state.
Train Operators
Because the plant operators and maintenance techs were involved from the get go, training on the new safety regime should primarily consist of review. It’s imperative to make sure everyone in the plant is on board and fully aware of all changes and upgrades, as even the best designed facilities can become unsafe with untrained or careless workers. Emergency response training should also be included in these review sessions.
Whether it’s a new corporate push for safety or simply a continuation of existing practices, actively identifying areas to improve safety and implementing corrective measures is a never-ending yet necessary process.