Modern variable frequency drives incorporate several control modes to help users fine-tune operation for various applications.
Kevin Kakascik, Technical Marketing Engineer at AutomationDirect, wrote an article for the June 2020 issue of Processing titled Choosing VFD Control Modes. Here’s a summary, click on the link above for the full text.
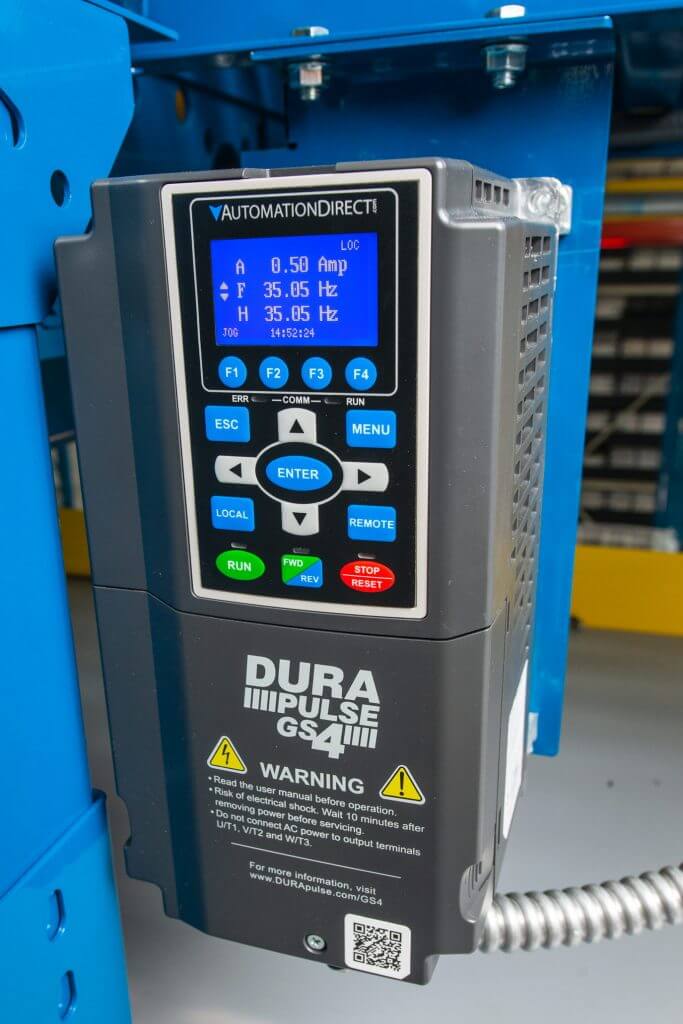
Variable frequency drives (VFDs) always require certain parameters to be configured for voltage, current, and the associated motor to properly control the load. There are two main control modes—volts per hertz (V/Hz) and sensorless vector (SV)—each of which play a key role in operational performance. This article describes these modes and offers some guidance on selecting the right one.
VFD Basics
VFDs modulate the voltage and current supplied to a motor to vary the speed and torque. First, the rectifier portion of the VFD converts AC line voltage to a DC bus voltage. Second, the inverter portion uses the DC bus voltage to generate a varying AC output voltage and current.
Commonly, industrial motors in North America operate at 100% speed (which is typically 1,800 rotations per minute) when driven with a nominal line voltage of 480Vac three-phase at 60Hz. Of course, other voltages and speeds are possible. Motors used with VFDs should always be rated as “inverter duty” or “VFD-rated,” which means they have thermal and electrical properties sufficient for this service.
Traditional VFD Control: V/Hz
The classic V/Hz control mode simply varies voltage and frequency in a linear matter, so with a power supply at 240Vac and 30Hz the example motor would operate at 50% speed. This is a straightforward and easy to implement control mode, but it does not include any feedback, so motor speeds are not extremely accurate and may slip under load. One VFD can drive many motors using this mode, and it works well for many applications like centrifugal pumps, fans, and material conveyors.
Sensorless Vector Provides Higher Performance
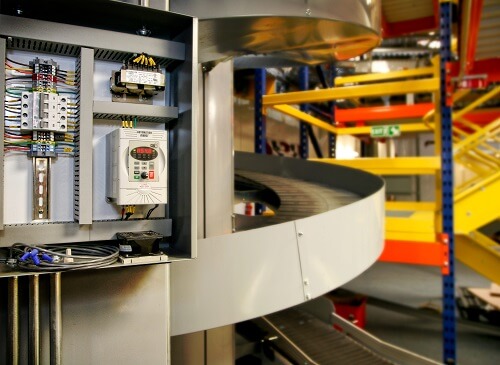
A VFD capable of SV operation is not exactly “sensorless”—it just monitors the voltage and current of the connected motor to mathematically determine the speed with sufficient accuracy. With this information, a VFD can operate in a “virtual” closed-loop mode and deliver higher starting torque, accurate speed control under varying loads, low-speed operation down to 1%, and up to 200% of rated torque for brief periods. This mode is best for applications where high accuracy is required like printing lines and textile manufacturing, but only one motor can be connected to a VFD in this mode.
Applications Determine the Better or Best Mode
Modern VFDs include many advanced features such as on-board logic control, PID loops, and numerous parameters and operating modes.
SV is a more recent development and will provide the best performance for most applications where there is one motor associated with each drive. For good control where the best accuracy isn’t needed, V/Hz is a quick and easy choice.
With some basic knowledge, users can select the best operating mode for their application.