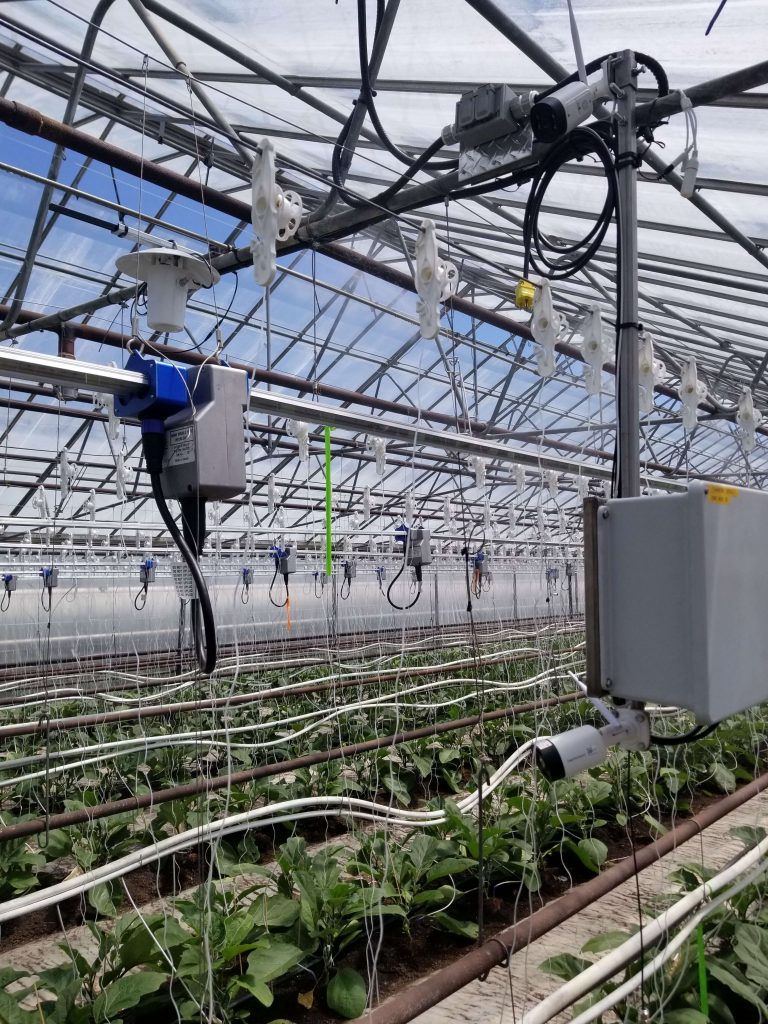
This greenhouse automation startup shows how AutomationDirect controllers are a flexible platform for connecting cloud-based artificial intelligence to practical operations manufacturing automation.
Connecting AI concepts to age-old agricultural operations using modern IoT methods is the ambitious undertaking of Kenneth Tran and his team at Koidra. The resulting “artificial intelligence of things” (AIoT) is yielding positive results for optimizing greenhouse control, and it is applicable to all types of manufacturing systems.
In a January 2022 Control Design article co-authored by Kenneth Tran of Koidra and Quade Digweed of Agriculture and Agri-Food Canada, titled How To Grow Disruptive Automation With AIoT, the team discusses how a new class of industrialized controller helped them create an AIoT application, which is extendable to support many other types of automation projects.
Farming the Future
With an education in computing and math, and practical experience implementing industrial automation systems, Ken was uniquely positioned to recognize the potential of AIoT. He founded Koidra to overcome the roadblocks he saw with integrating advanced AI with standard PLCs, HMIs, and SCADA systems.
Traditional PLCs are reliable workhorses, but ladder logic is not ideal for integrating with some higher-level systems. Software engineers working with advanced AI are most familiar with modern programming frameworks, but often lack some fundamentals needed for safely performing real-time control.
The team decided to target greenhouse control as an attractive proof-of-concept due to the reasonable required response times, multiple types of variables for control/monitoring (lighting, ventilation, humidity, irrigation, etc.), and other reasons. Advanced greenhouse control is an interesting test bed for AIoT because it requires the application of significant physics and science knowledge, and the use of many intertwined variables.
Sprouting a Solution
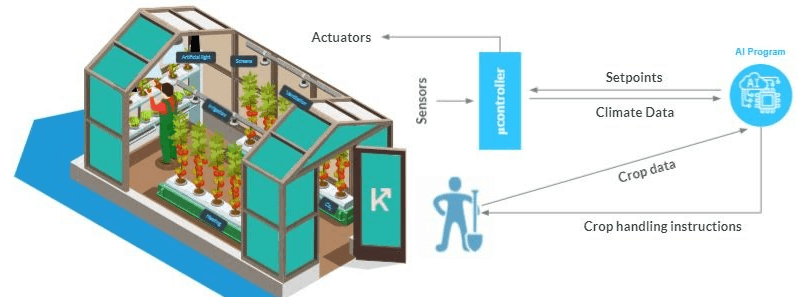
Koidra was born as an AI company and intended to perform macro control using cloud-based AI. However, they needed a robust local control solution at the edge, with an ecosystem of products backed by a reputable vendor with industrial experience.
After much research, Koidra selected the AutomationDirect ProductivityOpen controller family as the basis for their standardized control panels, which they dubbed “µcontrollers”, for a number of reasons:
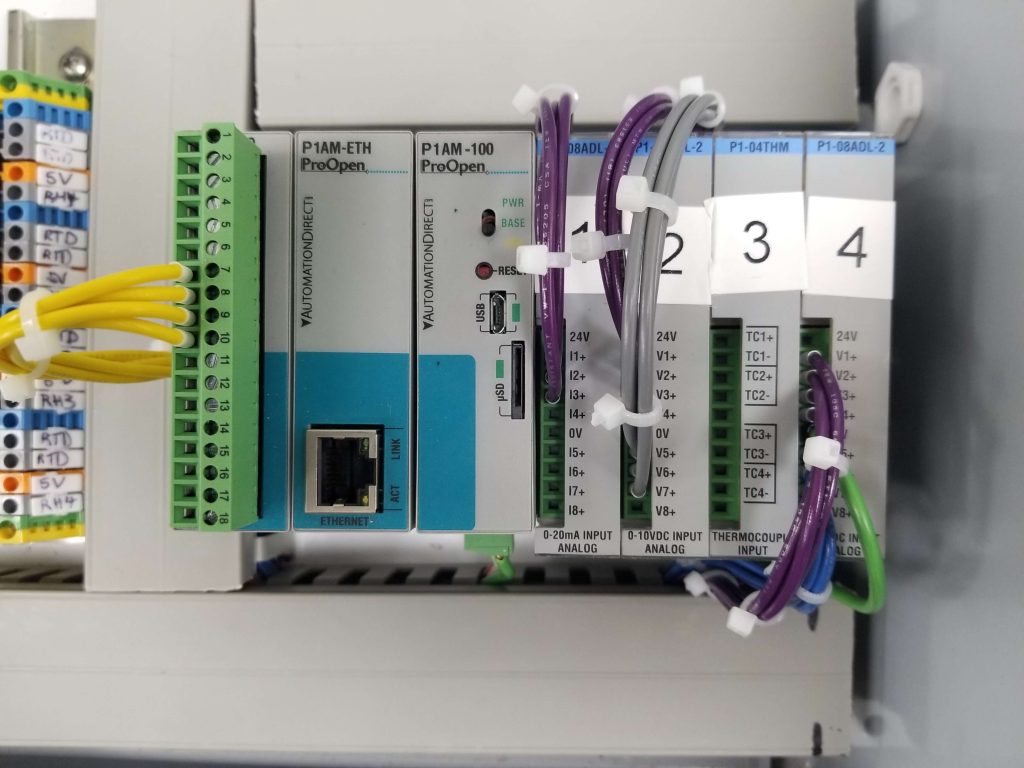
- Arduino compatibility
- Packaged in an industrial form factor with appropriate industry ratings
- Uses industrial I/O modules from a proven line of products for typical voltage/current levels
- Ability to communicate using specialized protocols like SDI-12 and I2C, which are common for environmental sensors
- Integrates with Arduino shields
- Enables developers to program in familiar languages like C++ using common software source control methods
Growing the Application
The hardware stack includes µcontroller panels connected to a variety of sensors, each chosen to optimize cost and accuracy. The diverse types of instrumentation include automotive CO2 sensors, industrial infrared thermometers, research-grade photosynthetically active radiation sensors, soil moisture sensors, and others.
Using ProductivityOpen and AutomationDirect’s software stack enabled the team to deploy a new datalogging and automation project with relatively little deployment time and at low cost.
Visualization, analytics, reporting, and dashboards are available via web and mobile apps.
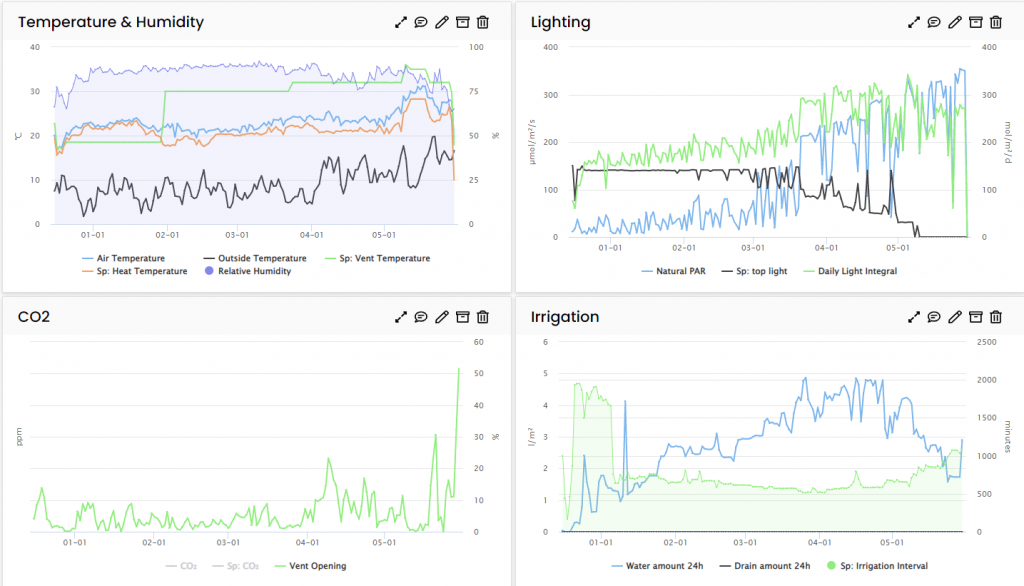
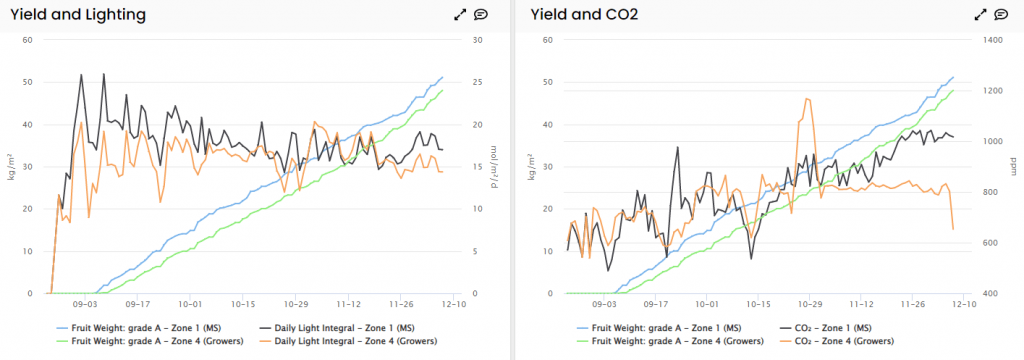
A Rich Harvest
The team now has proven results for growing eggplants, and from garnering awards in international challenges. The approach of using modern Arduino-compatible industrial controllers makes it easy to integrate cloud-based AI with all types of real-world systems, and it will be key to accelerating adoption and creation of these types of advanced solutions.
All figures courtesy of Koidra