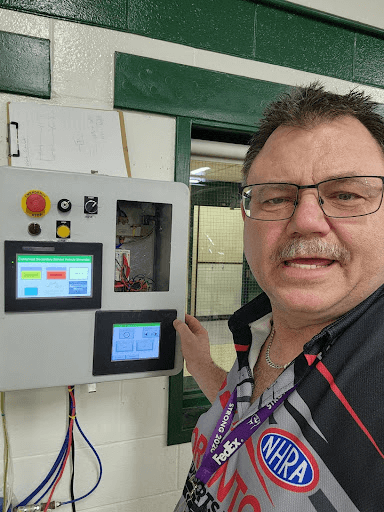
Students in Belleville, Ontario, Canada, have found a way to combine their passion for video games with the industrial controls coursework they are studying at the Centennial Secondary School. The team of 11th and 12th year students was guided by their instructor; John Harpell, an electronics and automation controls veteran with thirty years of experience.
The result of this effort was the creation of a vehicle simulator, similar to the “full motion race simulator”, or “racing cockpits” that are commercially available for gamers and race car drivers alike. The difference here: the fully gimbaled motion platform (with car seat) was designed and built by the students, and is controlled by pneumatic actuators and an industrial PLC. The “driver” sitting in the seat operates a USB-connected steering wheel and pedal cluster sourced from the video game world. The USB signals for the steering and pedal action are fed to both the PC that controls the on-screen visuals, AND to the PLC, which controls the ‘pitch’ and ‘roll’ of the seat, to give the rider/driver realistic feedback of acceleration, braking and the lateral g-forces of various vehicle maneuvers.
The Leap into the Unknown
One of the biggest challenges of the project that Harpell and his students faced was identifying and interfacing the USB signals to the PLC. This required not only an understanding of PLC controls but also a deep dive into the mechanics of USB gaming interaction.
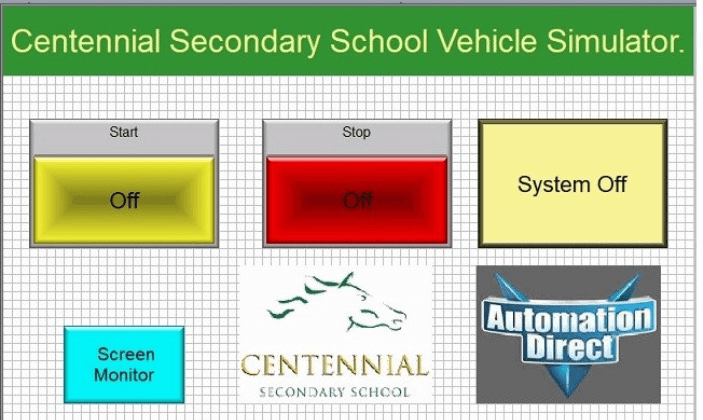
Control Components
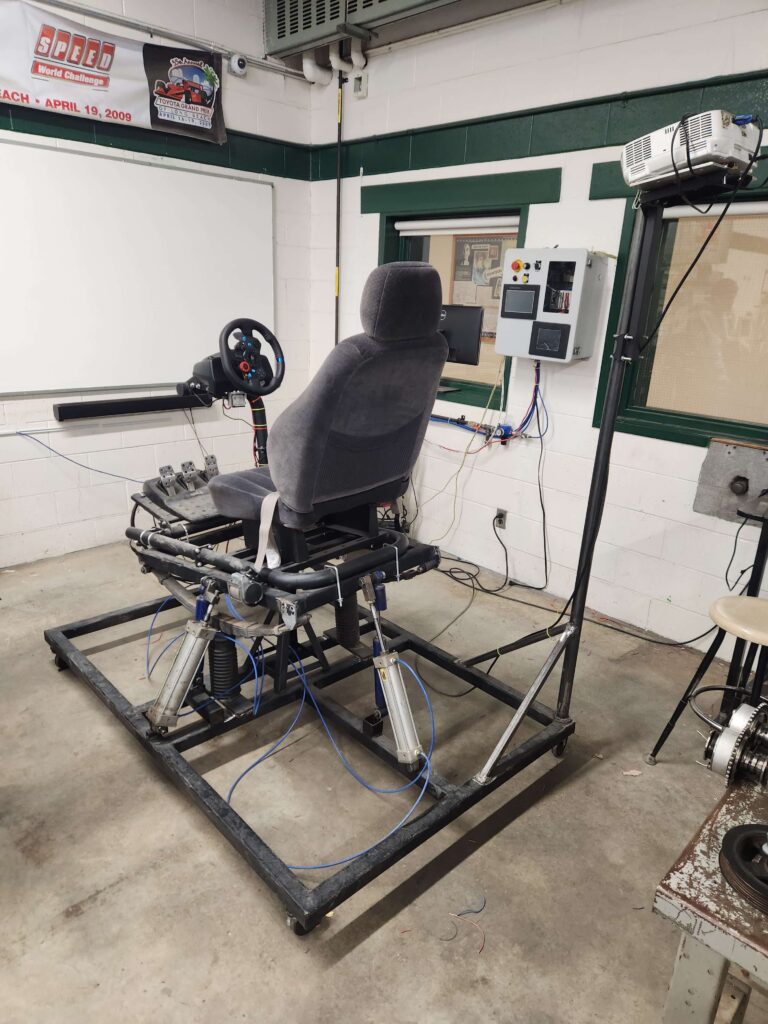
The control system uses a pair of C-more touch panel HMIs connected to a CLICK PLC from Automation Direct. Numerous momentary, toggle and e-stop buttons are employed along with a key switch for critical and safety functions. The prime movers for the motion platform are a pair of large pneumatic cylinders (12-inch stroke) which are controlled by the PLC via 4-way directional control valves.
Note: For the student’s safety, most of the control components are powered by 24 volts. A large 24 volt Rhino DC power supply is the only AC powered device in the system. Harpell specified the Rhino specifically for it’s built-in foldback protection with auto recovery.
Crafting the Simulator: A Tale of Innovation and Collaboration
The project required careful planning and execution. The students designed a robust frame capable of supporting the combined weight of the cockpit, a student and a car seat—approximately 400 lbs in total. Under Harpell’s guidance, students welded and machined parts to create a steel frame that promised both stability and flexibility. The simulator’s realistic movements were achieved through the use of automotive suspension techniques and components, to provide a realistic driving experience.
Engineering the Experience: Safety, Engagement and Learning
The development of the simulator demanded not only technical skills but also a focus on safety. To ensuring that the simulator was safe, the team focused many discussions on protective measures. Safety solutions included meticulous inspections for sharp edges, enclosing potential pinch points like coil springs and pneumatic shocks, and implementing key controls for adult supervision. Additionally, the use of rubber boots over coil springs and an emergency stop function were crucial in addressing safety concerns while simulating the dynamic movements of a car.
Student engagement was at the heart of this project, with classmates actively participating in the assembly and setup, contributing valuable insights into software choices and hardware upgrades. This hands-on approach deepened their understanding of the technical aspects and fostered a sense of ownership and pride in their work.
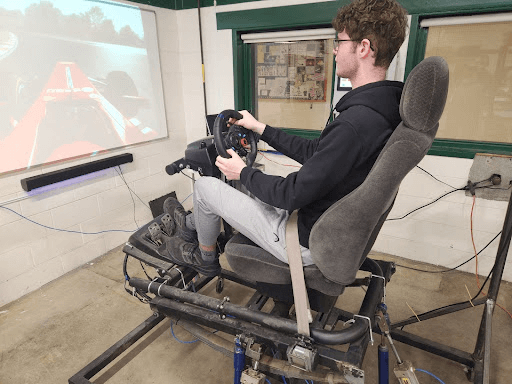
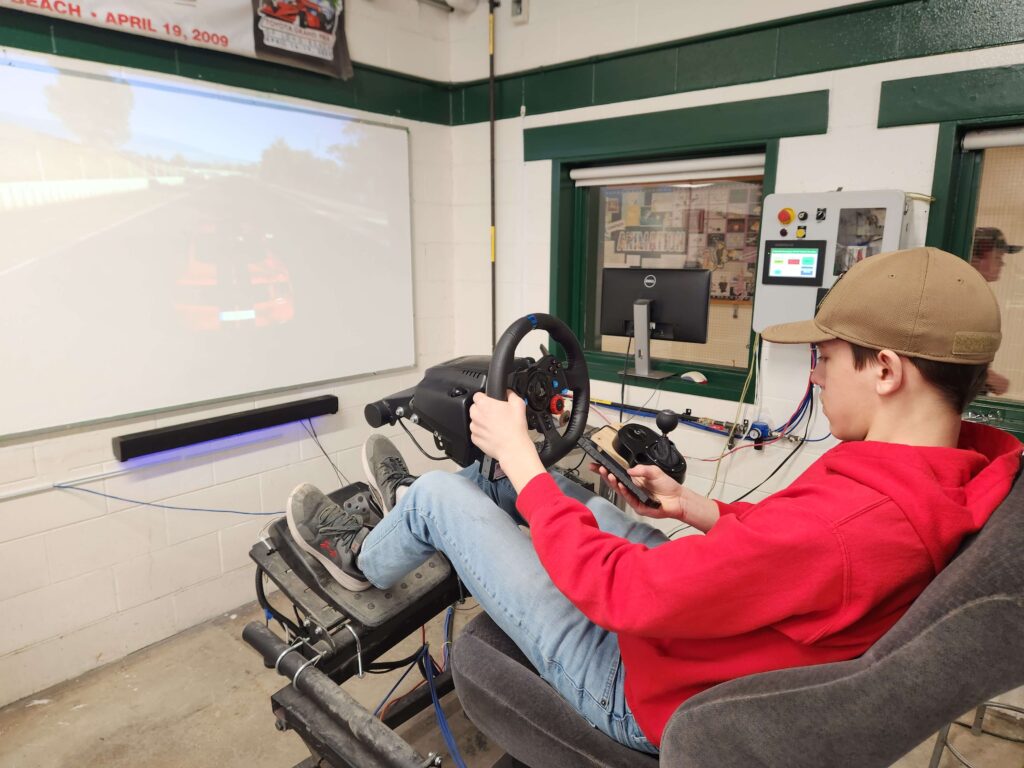
A Startling Reality: The Dangers of Distracted Driving
A key educational aspect of the simulator was its role in highlighting the dangers of distracted driving. By simulating real-world scenarios, students experienced firsthand the potentially devastating consequences of taking their eyes off the road, even for mere seconds. This component of the project served as powerful learning, driving home the importance of road safety.
The Final Reflection: A Project of Passion and Progress
This project exemplified the potential of combining traditional educational methodologies with the video game experiences that engage the students. Hopefully it will encourage other educators to reimagine the boundaries of learning, proving that with passion, creativity and collaboration, the possibilities are limitless.