Kinetic art is a medium that incorporates movement and motion into physical objects. If you have ever considered automation to be more of an art than a science, this robotic sculpture is must-see.
Byline: NGC Karen
With a career focusing on mechanical engineering roles for medical devices, I have not followed a traditional artist’s trajectory. Personal life experiences have prompted me to embark on a journey to create something truly unique—a kinetic art installation that blurs the line between woman and machine. In this article, I explore the challenges I faced, the solutions I devised, and the outcome of my passion project.
Inspiration from Adversity
My journey began with a personal struggle, dealing with a chronic autoimmune condition which requires on-going physical therapy to manage. The repetitiveness of exercises after nearly two decades sometimes leaves me feeling rather robotic. Inspired by the contrasting idea of infusing humanity into robotics, I envisioned creating a robot that could mimic human movements and even “breathe”, leaving a physical tribute to an invisible illness.
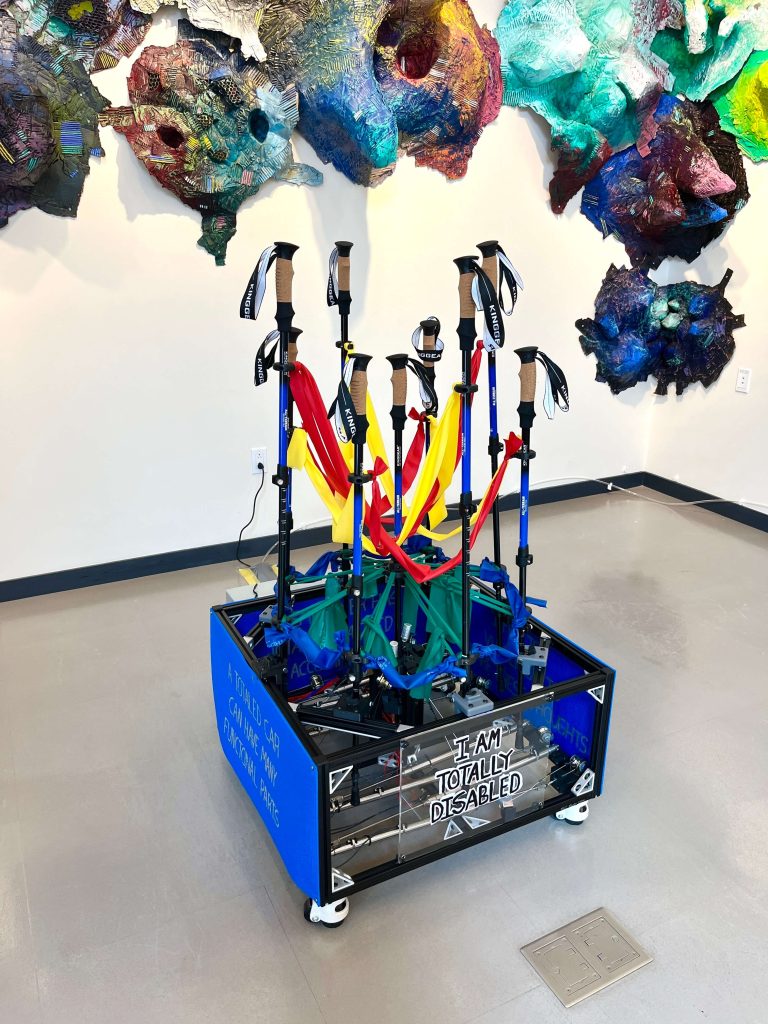
My professional life involves designing and building life test fixtures, which serve to test products by operating features tens of thousands of times. A master’s degree in mechatronics—including a deep-dive into programming and electronics—provides the technical expertise for my professional work, and also to bring my art vision to life. By combining a working knowledge of solenoids, actuators, and controllers with a creative flair, it would be possible to turn this passion project into a reality.
The concept was to apply automation principles to animate trekking poles with resistance bands, which are both aids for activity and physical therapy. The installation, titled Totally Disabled, began to take shape (Figure 1).
Therapy in Motion
Totally Disabled utilizes a series of resistance bands arranged artfully on trekking poles. The poles expand and retract in an intricate twenty-minute choreography, mimicking the human work required to manage invisible disabilities.
Motion is generated by eight Nitra pneumatic cylinders operated by Nitra solenoid valves controlling the flow of compressed air from a manifold (Figure 2). A small air compressor fitted with a Norgren pressure regulator supplies approximately 60 psi to the system. Pneumatic cylinders provide linear motion to the poles via steel cables and pulleys, in turn causing the resistance bands to stretch. When air is released from the cylinders, the resistance bands contract and pull the trekking poles back to their rest position. The arrangement moves through a programmed choreography, holding various positions for a brief time.
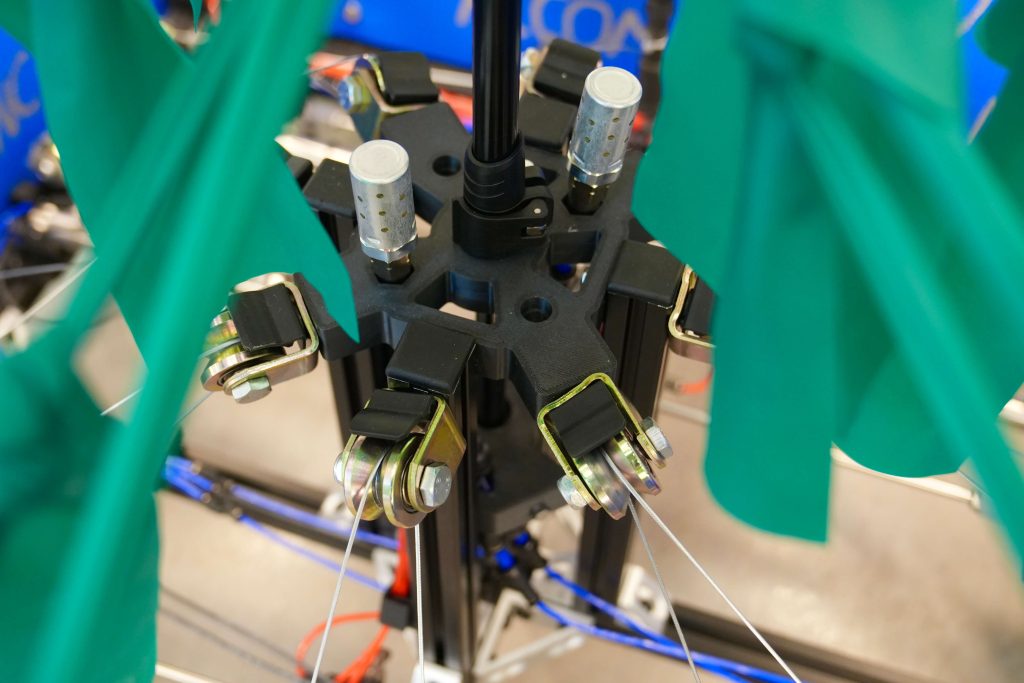
As an added feature, pneumatic tubing routes the air out of the sculpture via aluminum exhaust silencers to endow the sculpture with a form of breathing that sounds similar to the “huff and puff” that a winded human may experience while exercising. The original prototype incorporated large, double acting valves which produced correspondingly loud and distracting clicks. To achieve the desired effect, single acting miniature valves were ultimately selected.
If the pneumatics are the lungs of the sculpture, the control system provides the brain. For this project, I selected the AutomationDirect ProductivityOpen P1AM-100, an industrial-grade open-source processor with a compact form factor. The platform is extremely versatile, suitable for programmers with limited industrial experience, and compatible with Arduino Integrated Development Environment (IDE) for writing and compiling code. Arduino allows developers to write and upload code using a streamlined version of C++ and utilizes stackable shields—pre-configured circuit boards designed for specific functions such as Wi-Fi or LCD displays—to easily expand the functionality of the controller. The ProductivityOpen family not only consists of controllers, but also includes a complimentary line of industrial shields, I/O modules, and power supplies, all of which were used for this project (Figure 3).
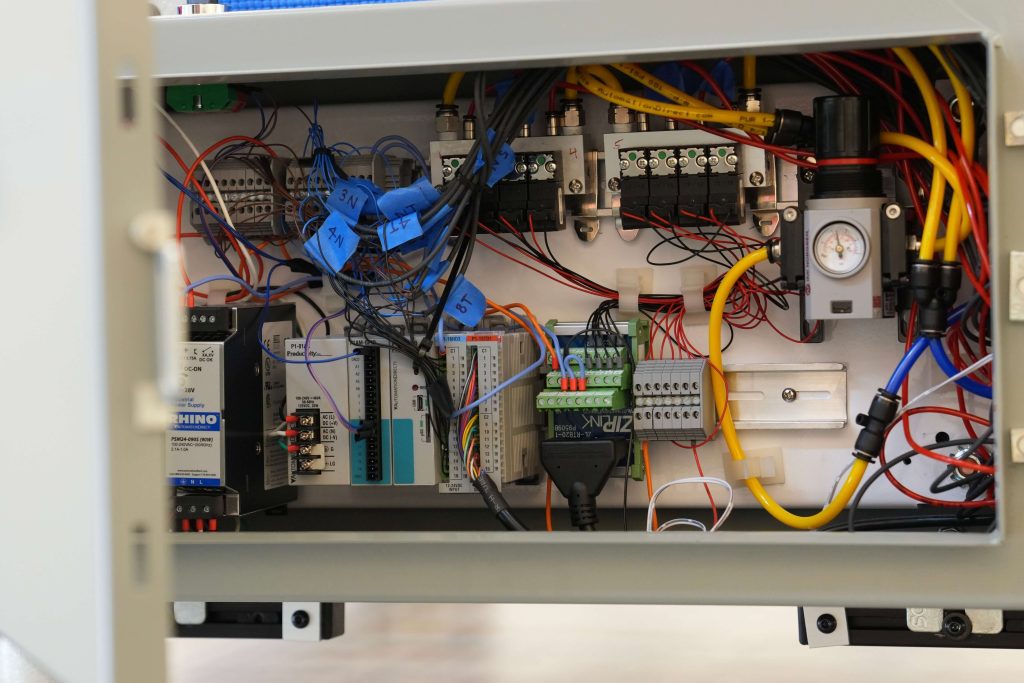
As with any control system—even for an art installation—safety is always paramount. The sculpture needed to be designed in such a way that the electrical controls would be contained when displayed in a gallery and the system would default to a safe state if any electrical or mechanical components failed.
Pneumatic cylinder extended and retracted positions were monitored using magnetic proximity position sensors. Two were installed on each of the eight cylinders to achieve positive closed loop control. For example, if a resistance band were to snap, become loose, or get stuck, the position sensors will monitor the status of the cylinder and immediately stop in a safe manner when an anomaly is detected (Figure 4).
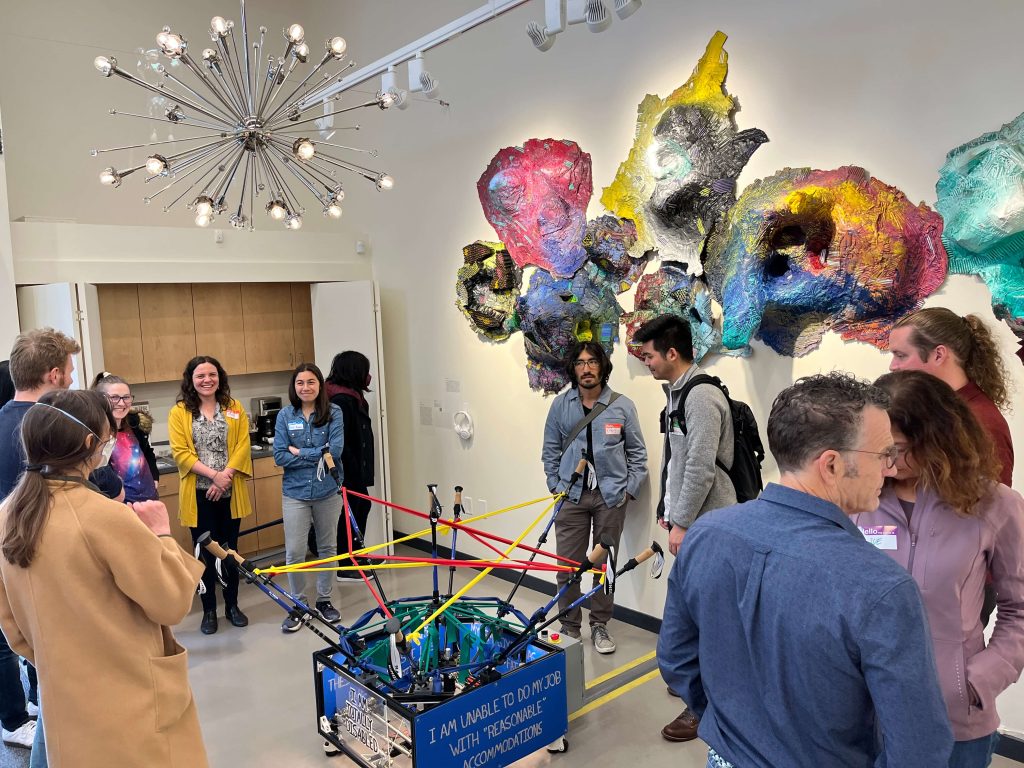
This project was my first opportunity to design a control panel intended for permanent use, because my life test fixtures are typically constructed on foam core structures for in-house use only. Everything from the enclosure and subpanel to circuit breaker, DIN rail, wiring and connectors, grounding and isolation equipment, and legend plates had to be procured. The ZIPLink wiring solution was particularly helpful for quickly connecting the controller and I/O in a secure, cost-effective manner that withstood transport to and from the gallery.
With the system running regularly while the gallery is open, maintenance had to be factored into the design. An illuminated pushbutton serves as an e-stop and a three-position selector switch provides additional ease of operation for placing the work in automatic, fully extended, and fully retracted modes. These features allow resistance bands to be periodically inspected and tightened as needed. In fact, when a steel cable that connected a trekking pole to a pneumatic cylinder frayed, it was easily replaced by a fellow engineer as I assisted remotely via video support.
To make it easy to transport for display, the sculpture was built on heavy-duty swivel casters. Once in the desired location, the casters can be locked preventing unintended movement of the base.
Sourcing Supplies and Soliciting Support
I was already familiar with AutomationDirect through my professional work, so it was natural for me to turn to this company for my art project. Collaborating with AutomationDirect not only led to a positive buying experience, but also yielded invaluable support.
With a variety of components to source, AutomationDirect’s website proved to be exceptionally useful and user-friendly. Navigating through the intuitive site organization, I even discovered complementary parts and accessories which were new to me. The filtering feature, conveniently located in the left-side product menu, proved invaluable, enabling me to refine product searches and swiftly pinpoint part numbers by selecting from a range of product-specific categories.
One of the most helpful features was the real-time pricing and stocking levels. I could adhere to a tight deadline by quickly identifying parts that were readily available within schedule and budget. Unlike some companies where you have to contact a representative for price and availability, AutomationDirect’s transparency empowers customers to make informed decisions regarding component selection without delays.
The range of support options for selecting and integrating parts was impressive. I posted questions in the AutomationDirect Community Forum and utilized their phone support. The forum provides a way to connect with other users and was particularly helpful resolving an issue with whether I would need to use a hardware-based interrupt in the programming. Datasheets, user manuals, and online videos provided comprehensive information. Phone representatives were knowledgeable, able to quickly answer questions, and provide assistance with part selection.
Ultimately, a majority of the components for Totally Disabled were sourced through AutomationDirect. From the controller and electrical components to the pneumatic and structural elements and even enclosure and wiring accessories, AutomationDirect offered high-quality, robust, and cost-effective parts that were ideal for this project.
Getting Social
The disability that inspired this project occasionally posed challenges. At one point, in lieu of celebrating my birthday with a traditional party, I enlisted friends and family to help with the project, and I was excited that more than 30 people joined me in support. Despite the fact that many of my support team did not have an engineering background or perhaps even much hands-on experience, many pitched in by helping with CAD, 3-D printing parts, assisting with assembly and testing, and offering moral support.
After the sculpture was installed at the gallery, a functional issue occurred, and I was unable to travel there. However, I successfully guided a friend through downloading an updated program to the controller, truly demonstrating the platform’s user-friendly nature.
Moving Forward
This project has been inspirational for me, blending engineering and creativity in a unique way. As with any engineering project, it is sometimes necessary to trim features to meet deadlines. Facing a tight timeline from the art gallery, this project was no exception. However, I am encouraged by the reception of this project, and look forward to creating both updated and different works in the future.
Totally Disabled is featured in the Radical Resilience exhibition at Ruth’s Table Gallery in San Francisco, CA. The kinetic art will be on display through June 7, 2024.
All figures courtesy of NGC Karen and Ruth’s Table Gallery
About the Author
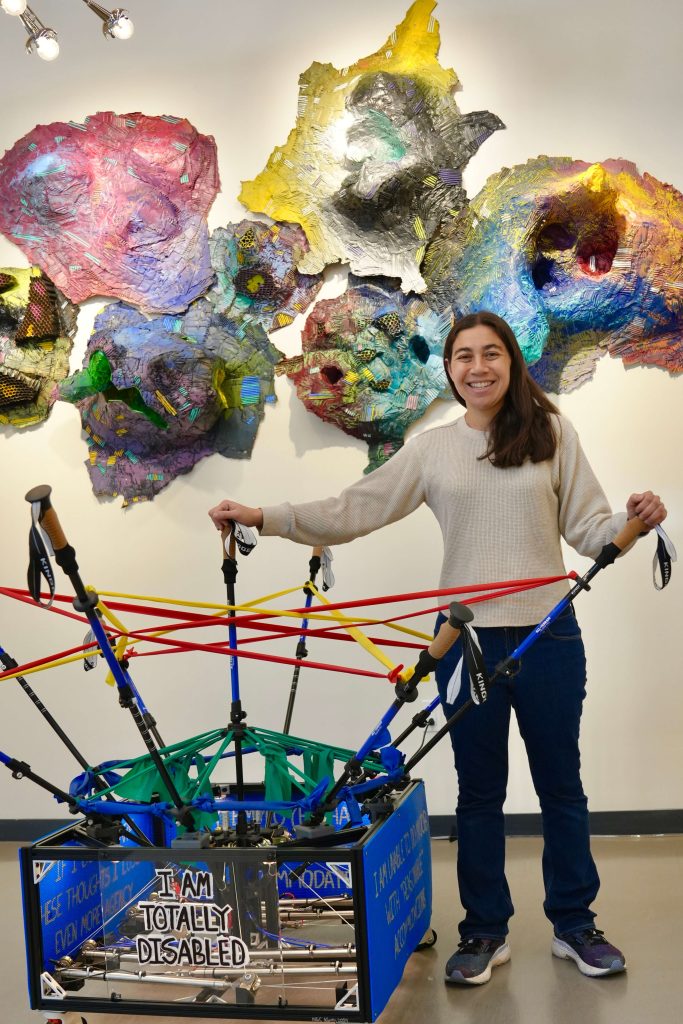
A Bay Area native, NGC Karen holds degrees from Stanford University in Product Design (B.S.) and Mechanical Engineering (M.S.). Her art focuses on exploring the intersection of her identities as artist, engineer, and disabled.