The SIDirect program connects end users of all sizes with systems integrators ready to support their automation needs, spanning a variety of technologies and processes.
By: Jeff Payne, AutomationDirect
Every manufacturing business must make choices about supporting their machines, production processes, and personnel. Careful application of the right automation technologies and skillsets in each of these areas yields the best overall results.
When it comes to the personnel aspect, it was historically common for larger enterprises to cultivate fully-staffed in-house engineering and maintenance groups. There are many benefits to this approach, as these companies could curate internal knowledge of the best ways for designing, installing, supporting, and maintaining all aspects of the manufacturing process.
However, it is well understood that hiring, retaining, and training experienced technicians and engineers is a challenge, especially considering evolving automation technologies. In fact, smaller operations simply cannot carry this kind of staff, even though they have the same needs as bigger companies to support and upgrade their production systems. In-house team members require continued education to support the application of newer technologies needed to run the business optimally. This problem is compounded by the number of specialties within the broad field of automation, such as motion control, vision systems, and data analytics. The cost of these efforts adds up, but the alternative of building up a large “technical debt” by not keeping up with technology is undesirable for any company.
For these and other reasons, many companies now choose to outsource some or all of their maintenance and engineering, often by partnering with systems integrator (SI) firms. There are some pitfalls to watch out for, but in many cases outsourcing can provide the most cost- and technically-effective way to keep the facility running in top form, while taking advantage of the most appropriate new technologies.
Outsourcing Options
There are clear benefits to supporting all maintenance and engineering efforts internally, especially for larger companies. Chief among these is that one or more team members are readily available to support production. Additionally, the entire team develops specific and intimate knowledge of production machinery and processes, including the best design practices, modification possibilities, and maintenance procedures fit for the company, providing a great degree of efficiency.
Smaller businesses and startups tend to run very lean, although they still have plenty of dreams and ideas about how to grow their operations, develop continuous improvements, and increase overall efficiencies and profits. In many cases, they can leverage YouTube videos and other internet resources along with easy-to-use AutomationDirect products to conduct a large portion of their own automation work.
However, whether a business is large or small, there are often cases where the automation needs simply require a skillset or team size not available in-house. These companies may fear, rightfully, that outside SI firms and technical specialists brought in “cold” will be unable to proficiently support existing systems or perform new project work without a detailed history of the operation. In spite of this fear, many manufacturing organizations already outsource a degree of their automation needs. For example, most of these companies use various original equipment manufacturer (OEM) machinery, which employs specialty automation.
Seeking SI Skillsets
When it comes to automation requirements for an overall production facility, or even for the case of retrofitting, troubleshooting, or upgrading portions of the operation, engaging SI services can be a great advantage. These engagements can be arranged in many ways, such as through an ongoing contract, per project, or on a time & materials basis.
By definition, SIs specialize in a variety of automation technologies needed to integrate a range of systems. Some SIs focus on specific processes, while others are generalists. The former bring deep and particular experience to a project, while the latter can apply concepts from other industries to provide novel solutions. Because SIs perform automation work on a daily basis, they are current on the latest best practices, products, certifications, and regulations (Figure 1).
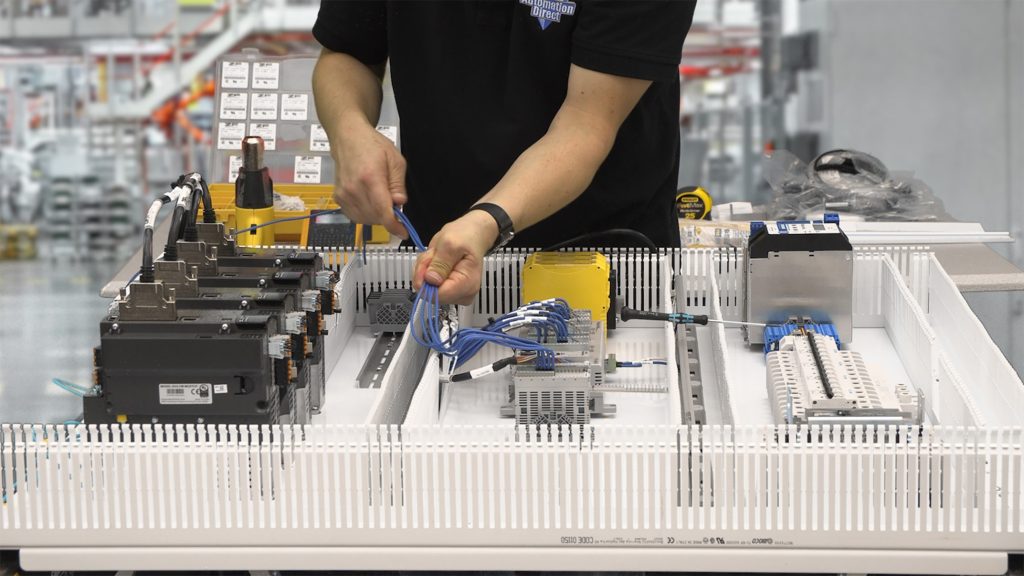
Some SIs concentrate on just instrumentation, networking, control logic, visualization configuration, databases, or analytics, while others span many of these disciplines. Correspondingly, SIs come in many sizes. While some provide plant-wide turnkey installations, others work on a specific type of machine or process, or will jump in to help fill a precise void.
Qualified SIs supply knowledgeable and experienced personnel with great skills and abilities to supplement a manufacturing company’s personnel to keep operations running smoothly and optimally.
The AutomationDirect SIDirect Program
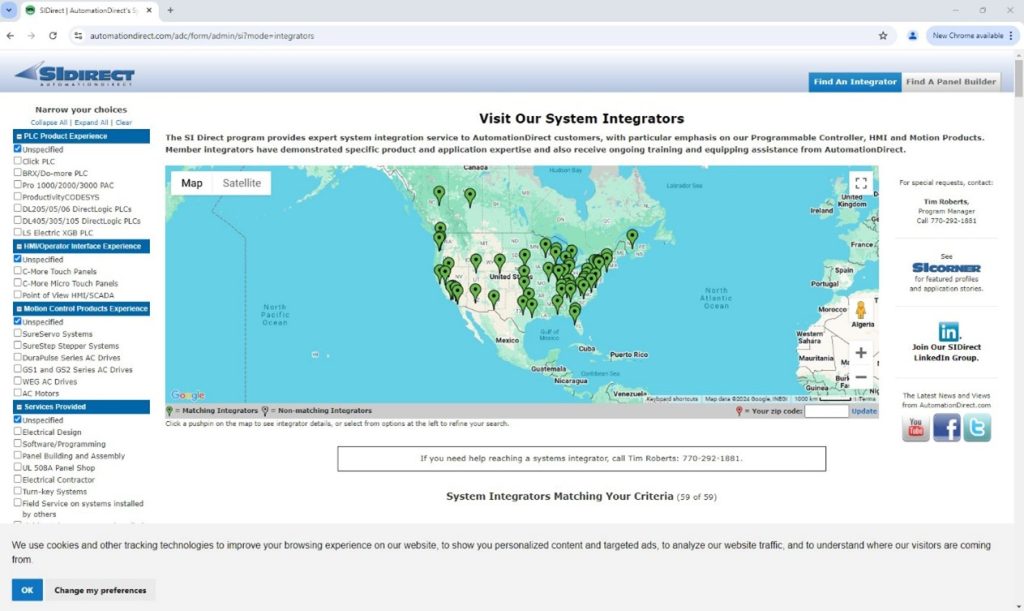
Recognizing these needs among end users, AutomationDirect created the SIDirect program in 2005. AutomationDirect already maintains a massive portfolio of automation hardware, software, and accessories, and many end users order just about everything they need for automation projects directly through the website. However, for end users looking for additional help, the SIDirect program matches you and your needs to qualified experts with a working knowledge of these products.
The SIDirect interface, with a quick overview map display, is a readily available way for end users to identify where best-fit SIs are located, as most companies prefer nearby providers. The faceted search function allows filtering by a specific domain of technological expertise, such as PLCs, HMIs, motion control, and more (Figure 2).
There is no substitute for experience. Every SI in the SIDirect program is vetted by staff at AutomationDirect to verify the credentials to install and program specified automation hardware and software. These SIs possess the skills and knowhow to design control panels and wiring diagrams that meet industry standards and regulations, including UL 508A and the National Electric Code (NEC) (Figure 3).
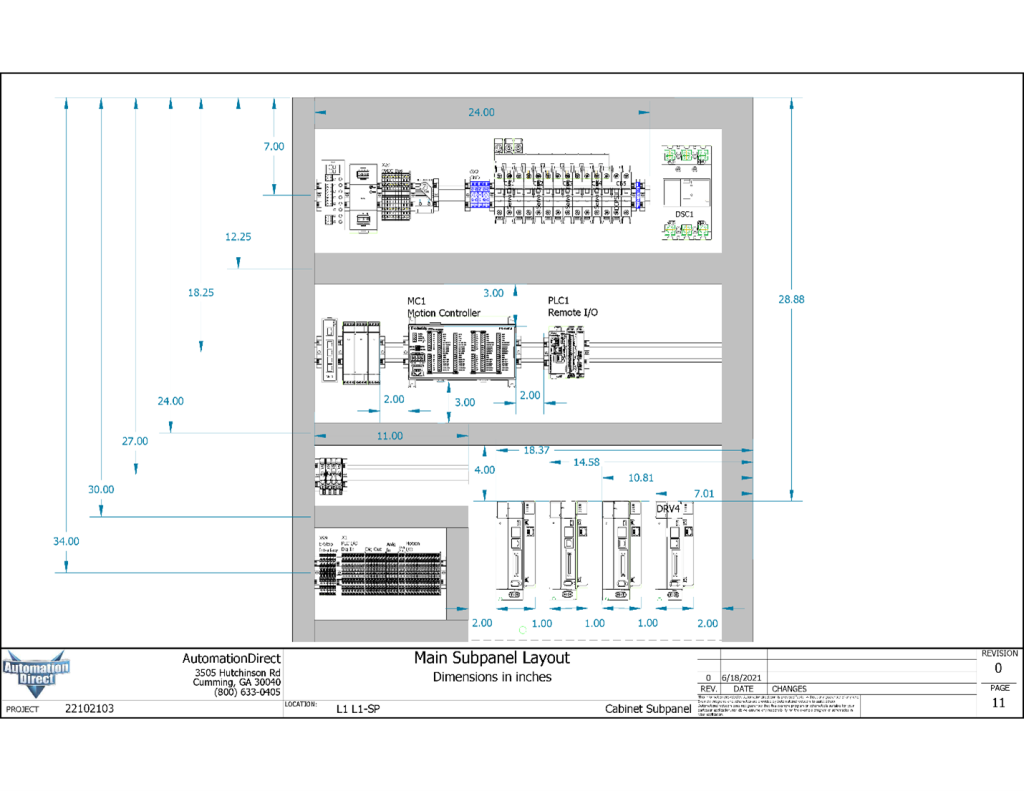
Consider motion control, for instance – it is a relatively complex specialty within automation controls programming, but is now more tightly integrated into modern PLCs than ever before. Motion control designers must have a solid understanding of the PLCs, servo motors and drives, motion controllers, encoders, mechanisms, and other products needed to implement these systems. These experts must also understand mechanical principles of operation and the relationships between speed, torque, acceleration, deceleration, and regenerative energy. Motion can be linear, rotary, or a combination of these movements, coordinated independently, relatively, or absolutely. Even though modern motion control products substantially streamline the effort required to develop a solution, there are extensive fundamental principles required to stand up these systems reliably!
Today in 2024, over 40 out of the SIDirect program’s 59 members across the United States and Canada are experienced in motion control using AutomationDirect hardware. Odds are, if you have a motion control application—or any other automation specialty for that matter—the SIDirect program can connect you with one or more SIs ready to partner on a solution.
Flexible Automation Support for the Future
Automation technology has advanced rapidly over the decades, providing amazingly expanded capabilities and performance. Many developments have reduced the implementation costs and simplified support compared with older technologies. However, the field includes many specialties, and it is nearly impossible for any one person or even a team to be adept in them all.
AutomationDirect products, and the SIDirect program, provide a reliable way for end user companies of all sizes to supplement staffing and leverage automation technologies to their fullest. Engaging an SIDirect member significantly improves the speed at which organizations can accomplish projects and tasks of all sizes, whether small upgrades, entire production lines, or anything in between.
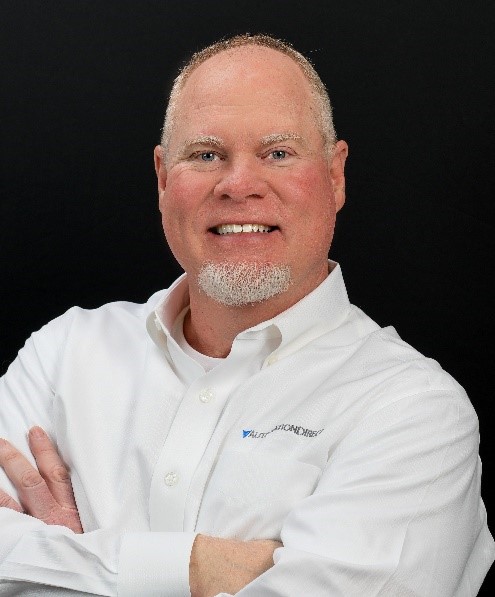
Jeff Payne is the Director of Business Development at AutomationDirect. Prior to this role, he spent almost 20 years as a product manager for PLCs, motor drives, soft starters, and motors. Before joining the company 25 years ago, he managed, designed, programmed, installed, maintained, and repaired a wide variety of highly automated equipment. He has been working in the industrial automation field for nearly 35 years and earned a degree in Industrial Systems Technology and Industrial Automation from Lanier Technical College.