Servo motors and drives use feedback to provide accurate position, speed, and acceleration control, making them ideal for demanding machinery and robotics applications.
By Chip McDaniel, AutomationDirect
Servo motor systems are a high-performance motion control technology, able to execute complex motion profiles while delivering high torque output, beyond the capabilities of typical direct current (DC) and alternating current (AC) motors. Therefore, servo systems are found in all types of industrial machinery, robotics, and consumer goods. However, servo systems are generally somewhat more complex and costly than other technologies due to the need for a drive, motor, and feedback elements, combined with more intricate configuration and control requirements.
AutomationDirect offers servo drives, motors, and accessories ranging from 100W to 15kW power output. Servos are rated in watts instead of horsepower because they are sized based on torque requirements. This article identifies the key characteristics designers should understand when specifying and configuring servo motor control systems.
Servo Basics
The primary purpose of an AC servo system is to precisely control the motion of a load. As we will see, systems suitable for industrial use will also have a variety of specific features differentiating them from non-industrial products.
A servo motor can be installed to directly operate a load, but oftentimes they are used in conjunction with a gearbox or other mechanisms to modify the effective output speed and torque—typically to increase the available torque.
Unlike other types of motors, a servo motor cannot be run simply by applying a voltage. Instead, the drive (also known as an amplifier, or sometimes a controller) supplies power to the motor and monitors an encoder, which identifies the position of the motor. With this information, the drive runs the motor as needed to positively achieve the desired motion or hold the target position. Industrial servo motors always have a built-in feedback device, usually an encoder. Using this encoder, the servo drive will know the shaft position within a few arc seconds.
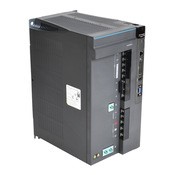
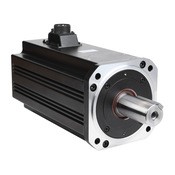
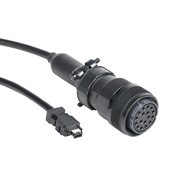
Hobbyist-type and consumer-grade servo motors are available in all-in-one form factors operating at low DC voltages. These compact arrangements of drive/motor/encoder/gearbox are driven by pulse width modulation (PWM) signals and are a convenient way to operate light-duty products.
However, for demanding industrial applications, it is most typical for a system to consist of a drive (powered at 110VAC, 230VAC, or 460VAC – single-phase or three-phase) which in turn operates an AC brushless servo motor equipped with a built-in encoder to provide feedback.
A basic servo drive accepts external commands from an external logic controller—such as a programmable logic controller (PLC)—via pulse signals, discrete I/O, analog signals—or more capable means such as RS-485 Modbus serial communications, or Ethernet using protocols like EtherNet/IP, Modbus TCP, or EtherCAT. Digital communications methods enable full configuration, monitoring and make various control options available.
More advanced servo drives include built-in motion controller logic capabilities that significantly simplify and enhance functionality, with useful features such as:
- Registration: to synchronize the drive with the product/material.
- Electronic camming: to synchronize the drive with other related drives on equipment.
- Flying shear: a common function to synchronize a moving cutter mechanism with moving product to be cut.
- Logic/sequential control: able to perform some functions that an external controller might otherwise perform.
- On-the-fly control mode switching: some tensioning applications switch between speed and torque modes—to switch direction of the load (a flexible saw blade, for example).
- Integration: some controllers may offer features to provide easier integration with the drive.
Modern servo systems provide the highest possible level of performance for precise control of position, velocity, and torque over complex and varying motion profiles. Earlier generations of servo systems could be difficult for end users to specify and configure.
With the introduction of AutomationDirect’s top-of-the-line SureServo2 servo family, there is an emphasis on providing more power and a rich feature set (and at a lower cost) than previous offerings. Free configuration software and helpful diagnostics capabilities are provided so users can easily and rapidly apply servo systems to more applications than ever before.
AutomationDirect also offers the LS Electric brand of servo systems with models from 100W to 7.5kW. LS Electric servos offer many of the most requested features at an even lower price point.
The following table lists some notable differences of the AutomationDirect servo product lines:
SureServo2 | L7C Basic | L7P Intermediate | iX7 Advanced | PHOX DC | |
Motor Power Range | 100W to 15kW | 100W to 1kW | 100W to 7.5kW | 100W to 3.5kW | 100W to 300W |
Input Power | 1Φ: 110/230VAC 100W-2kW 3Φ: 230VAC All 3Φ: 480VAC 400W-15kW | 1Φ: 230VAC | 1Φ: 230 to 2kW 3Φ: 230/460VAC All | 1Φ: 110VAC to 400W 1Φ: 230VAC to 2.2kW 3Φ: 230VAC All | 24-80VDC All |
Bandwidth (velocity loop) | 3.1kHz | 1kHz | 1kHz | 1kHz | 1kHz |
Motor Encoder Resolution | 16,777,216 ppr (24 bit) | 131,072 ppr (17 bit) | 524,288 ppr (19 bit) | 524,288 ppr (19 bit) | 262,144 ppr (18 bit) 524,288 ppr (19 bit) |
Encoder Output | Line Driver, up to 19.8 Mpps | Line Driver | Line Driver & Open Collector | Line Driver, up to 6.5 Mpps | Line Driver, up to 6.4 Mpps |
Absolute Encoder | Yes (with included battery) | No | Yes (with included battery) | Yes (with included battery) | Yes (with included battery) |
Pulse Input (PLS/DIR, CW/CWW & AB quadrature modes) | Yes | Yes | Yes | None | Yes |
Max Inertia Mismatch | Up to 50:1 match | Up to 20:1 match | Up to 30:1 match | Up to 30:1 match | Up to 30:1 match |
Safe Torque Off (STO) | Yes | No | No | Yes | Yes |
Electronic Camming (E-Cam) | Yes | No | No | Yes: via EtherCAT® | Yes: via EtherCAT® |
Registration | Yes | Basic | Basic | Yes: via EtherCAT® | Yes: via EtherCAT® |
High speed capture/compare | Yes (5µs) | No | No | Yes: via EtherCAT® | Yes: via EtherCAT® |
Communications Available | ModbusRTU (built-in) ModbusTCP & EtherNet/IP (optional) | Serial: RS-422 Modbus-RTU (compatible with RS-485) | Serial: RS-422 Modbus-RTU (compatible with RS-485) | EtherCAT® or ModbusTCP | EtherCAT® |
Applying Servo Systems
There is a significant amount of detailed theory associated with servo drive and motor operation, but designers generally only need to determine the necessary overall physical and performance characteristics to specify a servo system. AutomationDirect provides free servo-sizing software to assist users in determining the correct motor and drive for a given application. Key considerations include:
- Reflected load inertia.
- Torque and speed requirements.
- Physical and environmental constraints.
Reflected Load Inertia
Servo motors are available in low-inertia models offering speeds up to 6,000 rpm, and medium- or high-inertia models with speeds up to 3,000 rpm. Servo tuning also plays a role in how aggressively the drive seeks to command the motor response.
Any rotating system experiences inertia associated with the driven load and any interposing transmission elements. All load inertia must be determined and translated into an equivalent inertia as if it was directly attached to the motor shaft (driven load). Mechanical transmissions can dramatically impact the amount of driven load inertia reflected to the motor shaft. Then, a suitable motor must be selected to accommodate the reflected load inertia.
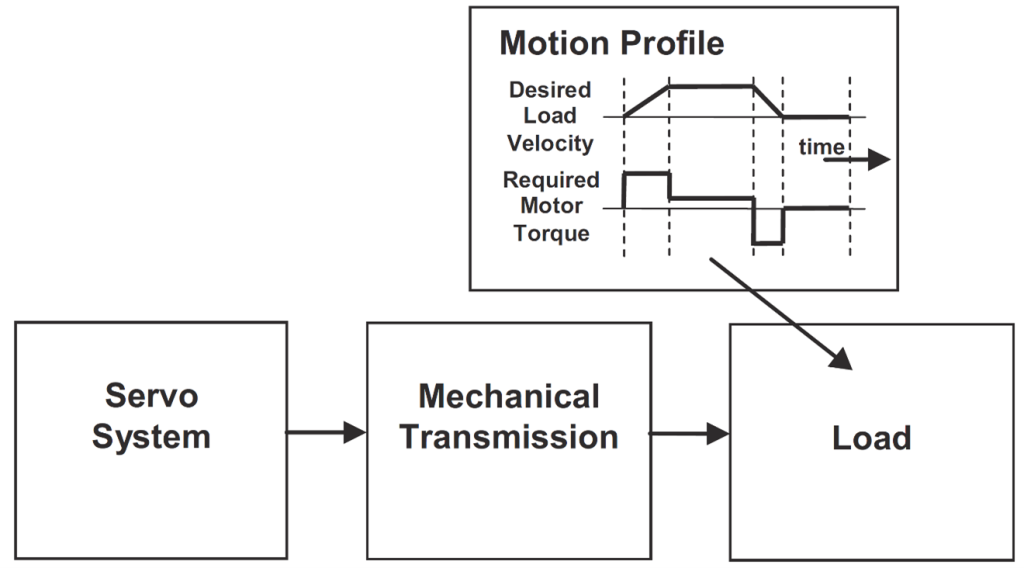
For the best system responsiveness, designers should seek to keep the reflected inertia low because high-inertia systems will have a lower responsiveness, or bandwidth. For systems requiring the best response, applications will benefit from keeping the load-to-motor inertia ratio as low as possible, and ideally under 10:1. Systems with ratios as high as 200:1 can be implemented, but with correspondingly lower responsiveness.
There are several good ways to determine the reflected inertia of a given system. Many CAD packages can determine inertia quite accurately—assuming the mechanical model is accurate, and that the proper materials densities for each component have been specified. Estimates can be created based on the rough geometry of the load, and there are simple equations for determining the inertia of individual or multiple combinations of typical geometric shapes like a cylinder or sphere. One online source for such equations is https://calcresource.com/moments-of-inertia-table.html, and there are many others.
Note that an estimate is fine, because it just takes a rough idea of the inertia in order to determine if the mismatch is below 50:1, or 10:1, and so forth. The AutomationDirect VisualSizer online tool, can assist in modeling the load accurately enough to determine the inertia so that a motor can be selected.
Torque and Speed
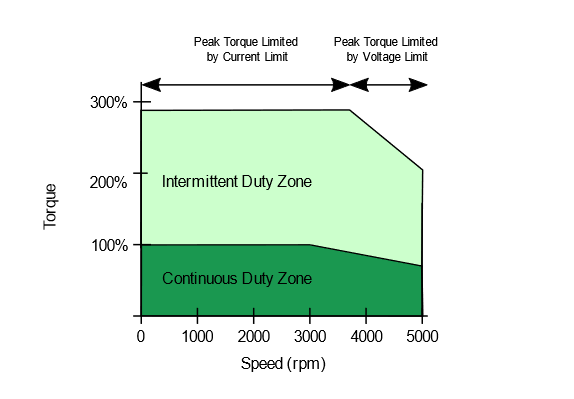
Servo motor systems carry a continuous and an intermittent operating torque rating. With knowledge of the desired motion profile, the mechanical transmission, and the load, it is possible to determine the required continuous torque, peak torque, and motor speed. The required torque values must fall within appropriate ratings of the system.
Mechanical transmission devices—such as leadscrews, rack & pinion mechanisms, gearboxes, pullies, and timing belts—are used to change the motor speed and torque transmitted to a load, and they can also translate rotary motion to linear motion. Transmissions acting as a speed reducer provide a mechanical advantage, so a motor can operate a load at a lower speed but higher torque, while being able to reject load disturbances. Gear reduction has the added benefit of lowering a portion of the reflected inertia (the portion of the load inertia attached to the output shaft of the gearbox). The inertia of that portion of the load is reduced by the square of the gear ratio! Just be sure to add-in the inertia of the gearbox itself (or other gear reduction system).
SureServo2 and LS Electric servo motors feature keyed shafts that can be used with keyed couplings, or with “servo-grade” clamp-on compression style couplings. The former are lower-inertia, but the latter offer better stiffness. AutomationDirect recommends that coupling safety factors be chosen as at least 1.25 over the peak torque requirement of the application.
Physical and Environmental
Servo motors can be mounted in most any orientation, and transmissions can allow the use of a smaller motor. Transmissions also provide options for repositioning the motor to a more advantageous orientation, whether that is in-line, right angle, or parallel mounting.
Most servo motors offered by AutomationDirect are rated IP65, suitable to withstand low pressure water jets, but a few are rated IP67 to withstand temporary immersion. The shaft seal should not be immersed in oil. AutomationDirect servo motors use convection cooling and may require heat sinks (the frame of a machine is usually more than adequate), but designers should ensure that the motor environment will allow the cooling features to function.
Other Configuration Considerations
Although the previous items represent the main servo system considerations, there are several other features and technical specifications that designers should address. All of AutomationDirect’s AC servo systems can handle almost any user need with the following:
- Cables: Connectorized cables for power, encoder, and brake connections make it easier to install and service servo motors. AutomationDirect offers a wide range of ready-made lengths, with continuous flexing versions (if needed) to support any application.
- Command options: The servo drives include optically isolated discrete inputs and outputs, and may offer analog inputs and outputs, for interfacing with external controllers, devices, and sensors. The drives work with the built-in motor encoders, or they can be integrated with a secondary/auxiliary encoder on the driven equipment for true closed-loop control
- Automatic tuning: Servo drives must be tuned for optimal operation with the motor. AutomationDirect’s servos offer several tuning methods: fully manual tuning, assisted tuning where the drive can be tuned as the motor moves, normal automatic tuning used for point-to-point moves, and one touch automatic tuning which works without any motion (static analysis). SureServo2 has a fully digital velocity loop response up to 3.1 kHz to ensures precise control and easy tuning. LS Electric includes auto-tuning features also, but the bandwidth is only 1.0 kHz.
- Setup/diagnostics: SureServo2 and LS Electric drives can be configured, monitored, and diagnosed using a built-in keypad/display, or with PC-based software. Firmware is field upgradeable, ensuring the drive can always be upgraded to the latest operating system.
- STO: Safe torque off (STO) is built-in with SureServo2 and with certain LS Electric drive families, so there is no need to install bulky external contactors to disconnect power during emergency stop conditions.
- Oscilloscope: The free configuration software offers built-in oscilloscope functionality to let users monitor command signals and operating values so system operation can be optimized, and timing problems can be diagnosed. SureServo2 offers an 8 channel scope; LS Electric offers 4 channels.
- Holding brake: Servo motors can be ordered with an optional 24VDC spring-set holding brake, which acts as a safety feature holding the motor in place, even when power is removed. Note that this brake is only to be used for holding position (typically while system power is off), and not for decelerating the motor.
- Built-in motion controller: Servo drives accept traditional commands from external host controls, but some incorporate a true built-in motion controller. SureServo2 allows up to 99 index moves to be pre-defined and stored for execution when triggered, and internal motion can consist of incremental or absolute moves, sequenced as needed with delays. LS Electric can do 64 index positions.
- External motion controllers: External controllers are needed to provide multi-axis operation among multiple servo drives. ProductivityMotion controllers are an excellent choice for operating up to 4 axes of coordinated motion. Do-more has very capable motion control options. CLICK PLUS PLCs can do up to 3 axes of simple motion control. LS Electric PLCs have many high-level motion-specific capabilities and support IEC standard-based languages.
- Gearboxes: SureGear precision gearboxes easily mate to SureServo2 motors and are available in as many as 7 gear ratios, depending on the motor. They use industry-standard mounting dimensions, include the necessary hardware, and feature best-in-class backlash of just 5 arc-min. LS Electric also offers custom matched gearboxes and up to 3 gear ratios per motor. All gearboxes are sized to accept full rated torque and speed from the mating servo motor, so the designer doesn’t need to apply torque limits (or risk damage to the gearbox). AutomationDirect provides a great selector tool for choosing gearbox/servo motor pairs.
Selecting the Right Servo Control System
The high-performance nature of servo systems can intimidate users seeking to specify and configure them. AutomationDirect has worked hard to make servo products flexible and easy to use, so the technology is accessible for all types of end users and applications. AutomationDirect offers many resources—including both a SureServo2 servo system selector tool and an LS servo system selector tool, along with full specifications, documents/drawings, and videos—all accessible through the website, and support staff are ready to help designers identify the right solutions for their applications.
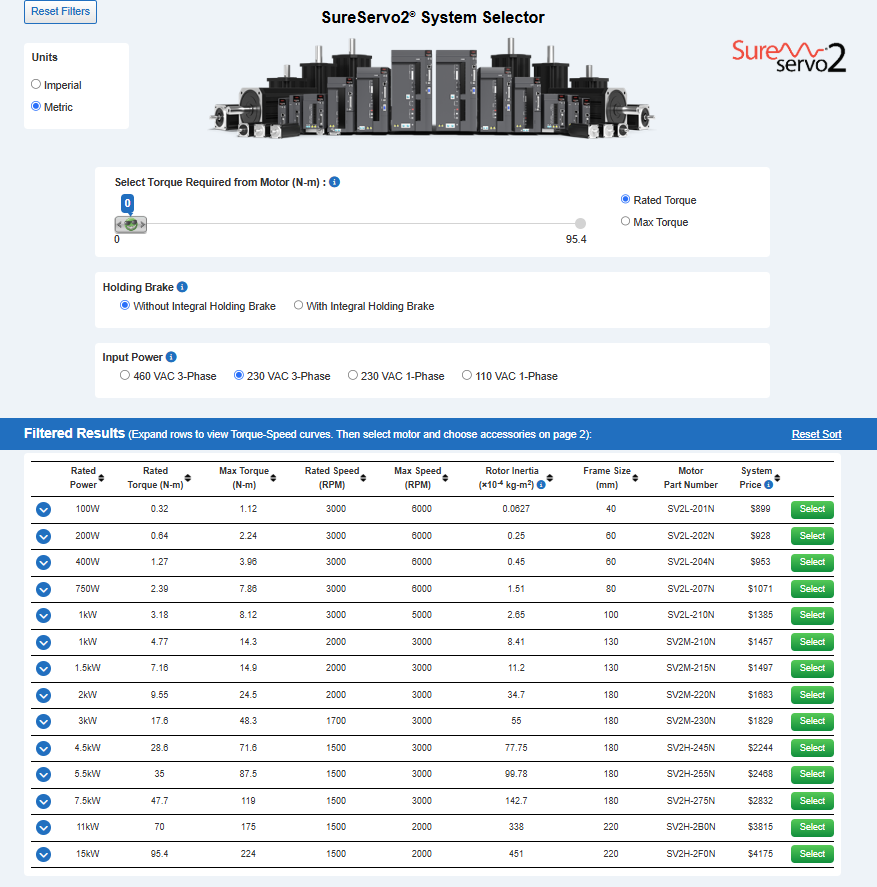
Figures all courtesy of AutomationDirect unless otherwise noted