Because industrial automation systems often remain in service for decades, it is important to select a hardware/software supplier and integration specialist familiar with performing incremental updates as needed.
By: Randy Ames, Ames Electrical Consulting, Inc.
Repair or replace: a conundrum familiar to owners of appliances, consumer electronics, cars, homes, and also industrial processing facilities. For a typical car owner, replacing a vehicle instead of repairing it is more a question of cost than risk. But for entities using industrial automation, the equation includes both cost and risk because existing equipment must be ripped out and superseded by something else, which involves downtime and the possibility that the new system won’t work as well, or at all.
At Ames Electrical Consulting, Inc. in Greenfield MA, the team is familiar with designing and installing brand new automation systems, ripping and replacing legacy systems that are end-of-life, and updating existing systems which just need a few improvements. Depending on the situation, Ames brings this experience to help their clients in industries as varied as water/wastewater, nuclear power generation, food & beverage manufacturing, and also heavier manufacturing—such as rubber, steel, paper, and plastics.
When a smaller wastewater treatment facility realized that the pump controls for lift stations throughout their service area were using an older human-machine interface (HMI) product that was now obsolete and unavailable, Ames was engaged to help perform an update that preserved as much of the existing installations as possible, yet provided useful new functionality.
Staying Afloat
Pump station controls are a common form of automation used throughout industry. While there are some standardized and dedicated automation controllers for this service, a great number of installations are operated using more flexible programmable logic controllers (PLCs), programmed as needed for each application to provide monitoring, control, and data communication. This is because there are countless variations for the mechanical equipment with regards to number of pumps, speed controls, level sensing, wet well geometry, control strategy, and other factors, and many agencies prefer to standardize on certain makes and models of product to address these needs.
Another reality is that these installations must typically remain dutifully in service for decades, and there is usually no call to upgrade unless there is a failure, additional capabilities (often in the form of improved data connectivity or remote monitoring/control) are called for, or if the parts become obsolete.
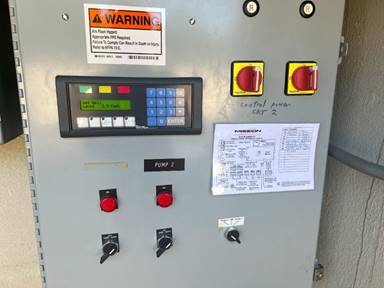
The latter case represented the situation for a wastewater treatment facility in Connecticut. They had numerous pump station control panels using AutomationDirect DirectLOGIC DL205 series PLCs, with HMI capability delivered using AutomationDirect OptiMate OP-1500 operator panels (Figure 1). The PLC product family was first introduced over 30 years ago and sold by AutomationDirect (formerly PLCDirect) and is a little long in the tooth today, but these controllers still perform just as well as they had on day one and replacement parts remain readily available, so there has been no reason to touch this part of the automation system.
For the HMIs, the original operator panels used a 2-line by 20-character monochrome display, a few LED indicators, and some basic number and entry buttons. While basic, this was just the right amount of functionality for the application when it was originally developed. However, these models were eventually retired with no direct replacement, as industry transitioned to display-based touchscreens. Because the PLC controls were well-liked and remained supportable, the facility needed to find the best path forward to replace just the HMIs, while keeping the pumping operations afloat.
Keeping it Simple
The Ames team was engaged to evaluate the situation, beginning with a survey of the typical physical installations and how the PLC and HMI code worked. Because Ames has been in business for over three decades and regularly performs this type of retrofit work, they maintain older laptops and software so they can work with any vintage of devices. In this case, a laptop with serial ports, running Windows 2000, facilitated looking into the older HMI.
It was quickly confirmed that there was a minimal-impact upgrade path to preserve existing functionality—and provide some additional capabilities—with low risk and quick implementation times by procuring and installing current-generation AutomationDirect C-more touchscreens. Physically, this would be an easy swap, just requiring a larger hole cutout and an adapter plate (Figure 2).
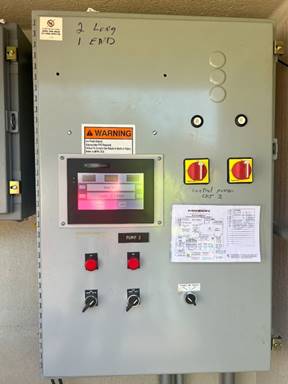
From a software standpoint, all the text messages were stored in the older HMI and displayed when they were triggered by the PLC. For the initial migration, messages would need to be replicated in the new touchscreen using a multi-state indicator (Figure 3). In addition, it was now easy to add other functionality, such as live water level readouts, and moving forward the facility has a platform which will support other enhancements.
Although Ames was already familiar with many AutomationDirect projects, this was their first project converting these specific older style HMI’s to the current generation platform. Having the Optimate programming software available on their older laptop, Ames was able to install the customer’s program and begin to reverse engineer the project. As expected, the AutomationDirect website and technical support provided an abundance of helpful information and made it easy to select and order the new HMIs platform, the C-more.
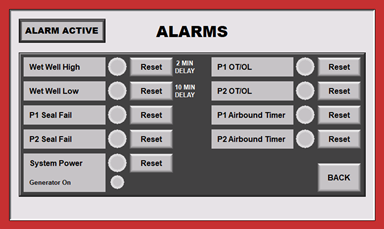
Since the team had previously used the C-More HMI in many different applications, and the free development software had an intuitive interface, they were able to start HMI configuration immediately. Along the way, they also used online help resources and videos to help them find and implement any needed functionality. The HMI was easily adaptable to this project to provide a similar look and feel to the original obsolete HMI, including maintaining the exact wording for the alarms and notifications, as well as the same locations for the original buttons and indicators. This resulted in minimal training needed for the facility operators, allowing them to quickly gain comfort with the new HMI.
The team was able to pre-test the configuration in their office, and then deploy it to the first pump station in coordination with the wastewater facility, to avoid outages. With the first migration installed and operational with a flawless cutover record, the facility is expecting to upgrade the remaining 18 pump stations as soon as possible.
Trusted Support Makes the Difference
Just as Ames provides reliable support services to their clients, the design team has found over the years that AutomationDirect is a trusted and reliable hardware and software supplier. Some of Ame’s clients specify what products must be used for projects, but in cases where AutomationDirect is not specified and there is flexibility, the team relies on AutomationDirect as a key supplier, in part because they know that support is available, free, and helpful, which is not true with some other product lines.
All photos courtesy of Ames Electrical Consulting, Inc.
About the Author
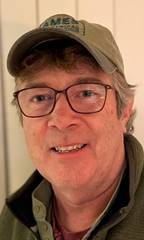
Randy Ames is the founder and president of Ames Electrical Consulting, Inc. in Greenfield, MA. Mr. Ames has an Electrical Engineering degree from Wentworth Institute of Technology, and is a Licensed Master and Journeyman Electrician in MA, VT, and NH. Ames Electrical has assisted large and small customers around the globe and continues to solve problems with all sorts of machinery and equipment, by servicing, designing and building custom electrical industrial control systems. You can find them on the web at www.ameselectrical.com