It may be tempting to size a variable frequency drive (VFD) based on horsepower alone. Did you know there are six other factors you should take into consideration to ensure that you specify the correct AC drive for your application?
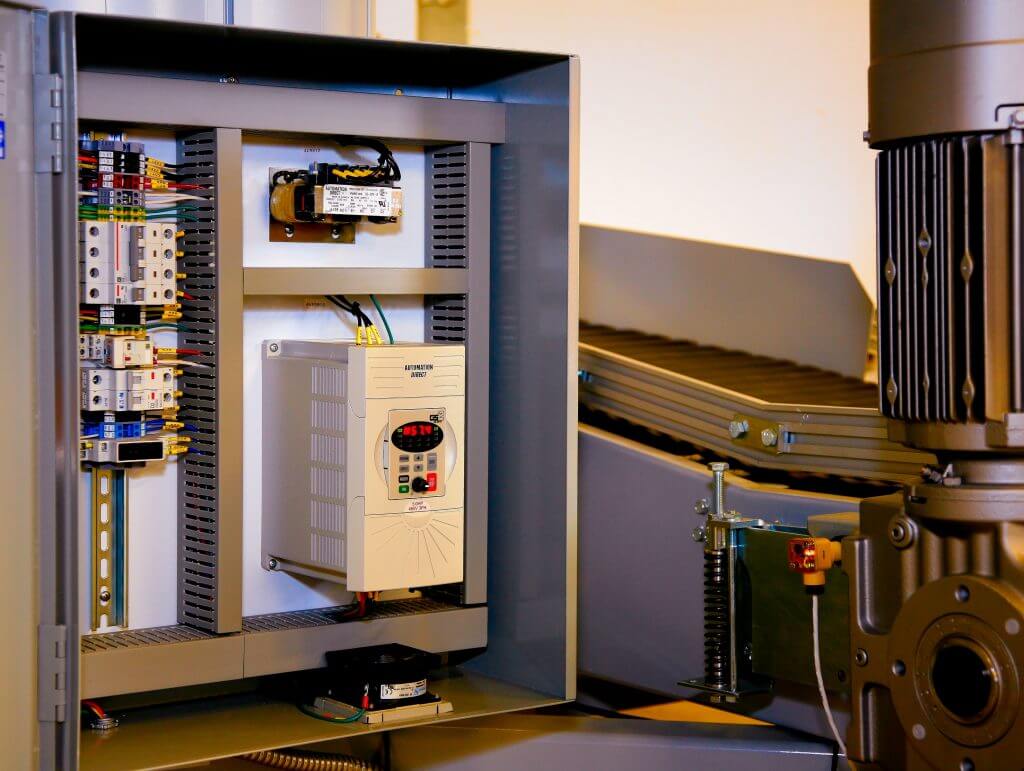
Six Factors to Consider When Choosing a VFD:
- Full Load Amperage
- Overload
- Application Type
- Altitude
- Temperature
- Carrier Frequency
Read below to learn more about the different factors:
Full Load Amperage
The first step in this process is making sure the drive can handle the motors current demands. Check the motor nameplate for the Full Load Current requirement, then find a drive that’s rated for at least that much current. If you are feeding the drive with single-phase power, be sure to use the drive ratings for single-phase. Variable frequency drives are significantly derated for single-phase operation. NOTE: All AC motors used with VFDs must be three-phase motors. VFDs always create three-phase output for the motor, even when the drive is powered with single-phase power.
Overload
Be sure the drive can handle any overload conditions you may expect during startup or intermittent extra loading. You may need to upsize the drive until you find one that can handle it. Many applications experience temporary overload conditions due to starting requirements or impact loading. Most AC drives are designed to operate at 150% overload for 60 seconds. If the application requires an overload greater than 150% or longer than 60 seconds, the AC drive must be oversized. NOTE: Applications that require replacement of existing motor starters with AC drives may require up to 600% overload.
Application Type
There are two application types: variable torque (VT) and constant torque (CT) and separate ratings for each. Use VT ratings for fans and pumps or consult the CT ratings for conveyors and general machine control. It is important to know the application type because the drive specifications are organized accordingly. If you aren’t sure which one to use it’s recommended to go with CT.
Altitude
The altitude at which you’re using your VFD also has an effect on cooling. As the altitude increases, the air becomes less dense. This decrease in air density decreases the cooling properties of the air. Most VFDs are designed to operate at 100% capacity at altitudes of up to 1000m. If you’re at a higher altitude, the drive must be oversized to compensate for the decrease in cooling.
Temperature
AC drives generate a significant amount of heat and can cause the internal temperature of an enclosure to exceed the temperature rating of the drive. Enclosure ventilation and/or cooling may be required. Make measurements/calculations for the maximum expected ambient temperature. NOTE: GS4 drives are ‘flange mountable’. This through-the-wall mounting technique puts the drive’s heatsink fins on the outside of the enclosure. This drastically reduces the thermal load inside the enclosure.
Carrier Frequency
Generally, you want to look for the lowest carrier frequency your motor can handle. Most of the time the default carrier frequency will work fine, but if you need to reduce the audible noise, the heat dissipation or the power consumption, then make sure you are able to modify the carrier frequency for the drive.
For more information, check out the detailed video below on selecting a variable frequency drive or visit https://www.automationdirect.com/drives.
To read more articles about variable speed drives, click here.