A better understanding of distance laser sensors helps when applying these rangefinders in material handling and industrial measurement applications.
By Andrew Waugh, Product Manager for Sensor and Safety Products at AutomationDirect
What is a Laser Sensor?
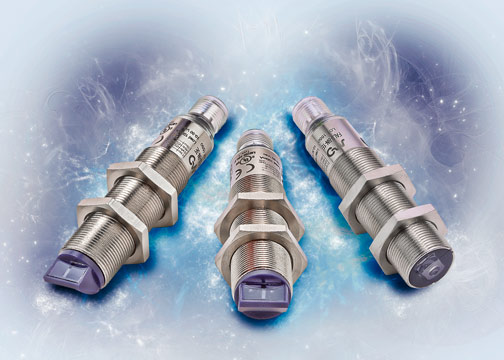
Laser sensors come in several configurations, with some detecting presence and others measuring distance. A proximity type laser sensor, also called a laser photoelectric sensor, is commonly used to detect presence of a part, but is not the focus of this discussion. The focus, figuratively and literally, is on laser distance sensors, that as the name implies, measures distance.
These laser distance sensors use a focused, coherent light to measure distance to a target object. In factory automation applications, the target is usually a product or a machine element. They detect any solid object and produce an output proportional to the measured distance—independent of material, color and brightness.
The high-resolution output provided by laser distance sensors is used to provide position or displacement, usually to the input of some type of industrial controller, such as PLC. The output signal is often highly accurate, and it includes temperature compensation to enhance stability.
There are several types of laser distance sensors including diffuse, background suppression and retroreflective. These sensors use CMOS or transit time technologies, providing accurate distance measurements.
Laser light must be focused, and it must stay narrow over a great distance and at a narrow spectrum (color of light). The emitted light can then be triangulated or pulsed, with each pulse return measured to create distance readings.
Angle Equals Distance
CMOS technology is often used in short-range, high-precision laser sensors. The basic principle is optical triangulation using a CMOS linear imager. A diffuse triangulating laser distance sensor transmits a laser through a lens and to the target, which reflects the light back to the sensor. A lens focuses this reflected light into a small spot onto the CMOS linear imager. The distance to the target object changes the angle of the reflected light and where the light is received on the linear imager.
These CMOS, diffuse triangulating laser distance sensors are available in measurement ranges from about 1.5-60 cm. They are packaged in small housings, about 50 mm x 50 mm, with either analog or discrete outputs—and generally work well regardless of the material, color or brightness of the target object. These distance sensors have high-resolution, in the low µm range depending on the measurement span, and response times less than a millisecond.
Class 1 lasers are eye-safe under all operating conditions. However, Class 2 lasers are visible lasers safe for quick accidental viewing of less than 0.25 s but may damage the eye if deliberately stared into.
Light Speed Measured
Time-of-flight technology is often used in long-range laser distance sensors, also called rangefinder laser sensors (Figure 1). These types of sensors use a transmitter diode to generate a very short pulse of narrow-spectrum red or infrared light which reflects from the target object and back to a sensitive, laser energy detector, also called a receiver diode. The accurate and precise electronics in the sensor can measure the light transit time and use the constant for the speed of light to calculate the object’s distance from the sensor.
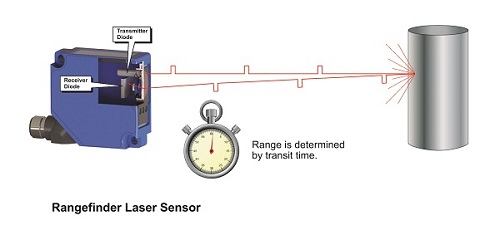
Time-of-flight laser distance sensors are available in a measurement range from a 1 cm to over 100 m and are similar in size, output options and laser sensing capabilities to CMOS sensors. These long-distance sensors have good resolution, from about one mm at close distances, to less than 2.5 cm of error over 100 m. To improve measurement accuracy, multiple measurements are often made, slowing the response time of these devices to several milliseconds.
Laser Applications
Laser sensors generally work well in a dirty environment since the focused light can “burn” through dust. The focused beam also enables long sensing distances, and detection of small objects or targets through small openings.
Laser sensors are often used in process monitoring and closed-loop feedback control systems. Material handling is a popular application to enable positioning of cranes, gantries and automatic guided vehicles (Figure 2). A few of the many other applications include component alignment, height measurement, robot positioning and weld head location.
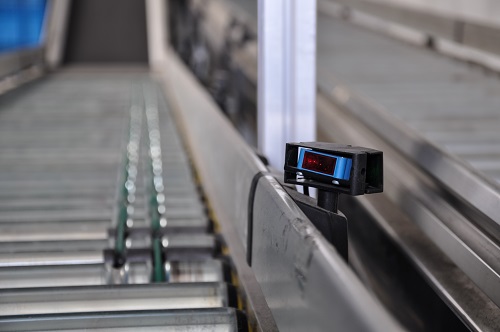
At times, shiny or transparent objects can cause problems. Because the laser distance sensor detects reflected or through-beam light, transparency and surface reflectivity may cause complications. Applications requiring bouncing a laser off a shiny surface or looking through a transparent surface should be carefully tested to make sure the measurement works as required. For example, the laser may need to be mounted at a slight angle to a shiny surface or adjusted to a lower intensity to properly detect a shiny object, while the intensity may need to be increased to burn through a transparent object.
Once testing is completed and any required adjustments make, lase sensors will perform will in industrial applications for years.
To read more articles about laser sensors and related products, click here.
Author Bio
Andrew Waugh is the product manager for sensor and safety products at AutomationDirect. He has more than 17 years of experience with machine sensor and safety devices used in packaging, assembly, material handling and process control applications. Prior to joining AutomationDirect in 2010, he worked at ifm efector as a Product Specialist for 9 years. Andrew holds a BSME degree from Penn State University.
Originally Published: June 2018