What is a Proximity Sensor?
Proximity sensors allow non-contact detection of objects. In particular the presence of parts and/or machine elements for the purpose of counting, indexing, verification, end-of-stroke or travel, determining orientation, and many other common automation tasks.
They are used in many industries, including manufacturing, robotics, semiconductor, etc.
Selection Criteria
There are several types of proximity sensors (detailed below) – some common selection criteria include sensing distance, size/shape, switching frequency, ingress rating, flush vs non-flush, housing material, and connection type.
Sensing Distance
Proximity sensors come in three basic sensing distances: standard, extended, and triple distance, but the size of the sensor body and the flush type also greatly impact the sensing distance. In many applications, it might not be possible to mount a sensor close to the sensed object. In those cases, longer sensing distances are needed. For instance: longer sensing distances may eliminate the need to buy more expensive high-temperature sensors. If a sensor is placed too close to a hot temperature source, the sensor will require more maintenance, or fail more quickly. Mounting the sensor further from the detection area may reduce heating of the sensor, which may extend the life of the sensor.
Size and Shape
Proximity sensors are available in a vast assortment sizes and shapes, from tiny 3 or 4mm barrels to 30mm cylindrical and in many rectangular form factors. Most inductive, capacitive, and magnetic sensors are single piece designs while some ultrasonic proxes are a two-piece “thru-beam” design.
Switching frequency
The internal circuitry of a prox always has a switching frequency – this can loosely be interpreted to mean how often the sensor is checking the target area for an object. If you need to detect moving objects at very high-speed, you may have to pay attention to the switching frequency – most sensors are fast enough for routine operations.
Output type
The type of output required must be determined (i.e., NPN, PNP, or analog). Most PLC products will accept either NPN, PNP, output. If connecting to a solid state relay, a PNP output is needed. The need for analog output is determined by the application. Sensors with analog outputs produce an output signal approximately proportional to the target distance.
Do I need 2, 3, or 4-wire discrete outputs? This may be dictated by the device to which the sensor will be connected, or it may be a personal preference. Some simple guidelines to use are:
2-wire
- Will work with sinking or sourcing devices
- Only 2 wires to terminate
- Higher leakage current
3-wire
- Most popular variety – familiar to most users
- Must select between NPN and PNP outputs
4-wire
- Allows configurability in one device.
- May have both NPN/PNP selection or NO/NC selection
- Allows the user to stock one part for numerous applications
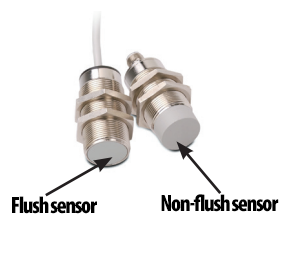
Mounting Options
Non-flush mount (also called non-embeddable, or unshielded)
These sensors have no provisions for shielding the electromagnetic fields used for sensing – and thus require the largest metal-free area around the sensing head. They may also need additional mounting distance from nearby sensors to avoid mutual interference. They typically have the longest sensing distance of the three types.
Semi-flush mount (also called semi-embeddable)
These sensors have some shielding for EM fields and require less metal-free area around the sensing head. They can typically be mounted closer to nearby sensors without interference. The sensing distance is somewhat restricted.
Flush mount (also called embeddable, or shielded)
These sensors are completely shielded from all sides, except the sensing face. The sensing distance is restricted, but these sensors offer the most flexible mounting options and immunity from interference from nearby sensors.
This general info on mounting options should help narrow the choices, but designers should review the specifications for all mounting restrictions (including minimum spacing from nearby sensors) for the specific sensor that is under consideration.
Environmental ratings
All proximity sensors provide excellent protection from environmental factors such as moisture and debris. Ingress Protection (IP) ratings are established by the IEC, and define the protection offered by electrical devices and their enclosures. It is similar to the NEMA rating system. IP ratings of IP65 or higher are very common for proximity sensors. Harsh duty models are also available and can have ratings as high as IP69K. IP69K is often required in the food and beverage industry where the sensors must withstand “washdown” cleaning procedures, often with harsh chemicals. More about IP69K here.
Connection types
Proximity sensors are usually offered with either an attached “axial” cable or a quick-disconnect (Q/D). Both connection types offer a high degree of ingress protection, typically IP65 or higher.
Axial cables
Axial cables are typically 6 feet (2m) in length and are molded into the body of the sensor at the attachment point, exiting axially (inline with the sensor body). They are typically the less-expensive option. The cable can be cut to length, but may not be long enough to reach all the way to the machine controller. Field junction boxes may be required, and numerous sensor signals are often combined into multiconductor cables at such junction points. Lastly, an axial cable exiting from the end of the sensor body may not fit (physically) in all applications.
Quick-disconnects
Sensors with quick-disconnects require the use of a separate cable to complete the installation. These cables typically include industry-standard M8, M12, or micro-AC (for some AC powered sensors) style connections on one end and offer a pigtail (flying leads) on the other end for completing the connection. These quick-disconnects offer several advantages: it’s very easy to replace a damaged sensor without any rewiring, and the cables are available in longer lengths with axial or 90-degree connections at the sensor. Field-wirable quick disconnect connectors are also available for constructing custom cables.
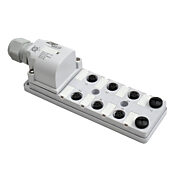
Multiport junction blocks
Cables with quick disconnects on both ends (patch cables) are also offered and can be used with Multi-Port Junction Blocks to multiplex numerous sensor signals back to the machine controller.
Extremely small sensors may have a short axial cable with the quick-disconnect a few inches from the sensor body.
Cable Options
Q/D cables are offered in PVC and PUR jackets for meeting the requirements of all applications. Axial cables typically come with a PVC jacket. PVC is a general purpose insulation while PUR provides excellent oxidation, oil and ozone resistance. PUR is beneficial if the cable is exposed to oils or placed in direct sunlight.
Field-wireable connectors, T-couplers, M8 receptacles, M12 receptacles, and Mini (7/8-16 – UN2) receptacles are also available.
Types of proximity sensors
Inductive
Inductive proximity sensors detect the presence of metallic objects at close range (up to about 1.5 inches typically). Ferrous metals allow the greatest distances to the sensor; other metals may reduce detection range. Low-cost, reliable sensors are available in an array of shapes and sizes for a wide range of applications.
- Standard Industrial Automation (offered in 3, 4, 5, 6.5, 8, 12,18, &30mm cylindrical sizes and rectangular form factors)
- Harsh Duty (8mm, 12mm & 30mm cylindrical sizes and rectangular form factors)
- Analog Inductive
Shop for inductive proximity sensors here.
Magnetic
Magnetic proximity sensors are used for non-contact object detection beyond the normal limits of inductive sensors. Used with a separate damping magnet, they offer very long sensing ranges in a small package and can detect magnets through walls of non-ferrous metal, stainless steel, aluminum, plastic or wood. More information about magnetic proximity sensors is here.
Shop for magnetic proximity sensors here.
Capacitive
Capacitive sensors detect both metal and non-metal objects and can sense through insulating materials such as wood or plastic. They are often used to detect fill levels of liquids, pellets, and powders through container walls. Capacitive sensors are available in cylindrical or rectangular shapes, with sensing distances up to 40mm.
Shop for capacitive proximity sensors here.
Ultrasonic
The principle of ultrasonic sensors is based on the emission of a sound impulse and the measurement of the time elapsing of the return echo signal reflected by the detected object. The ultrasonic beam is well reflected by almost all materials (metal, wood, plastic, glass, liquid, etc.) and is not affected by colored, transparent, or shiny objects. This allows the user to standardize on one sensor for many materials without any extra setup or sensing concerns.
Through-beam pair sensors are often the most accurate and reliable sensor configurations, but can
also be more costly when compared to traditional diffuse or retro-reflective sensors. Ultrasonic sensors (rectangular) are ideal for detecting objects in applications where the use of other types of proxes or photoeyes do not work, such as:
- Level measurement: for tanks containing solid or liquid
- Diameter or loop detection: for materials such as paper, sheet iron, etc.
- Transparent object detection: for plastic or glass bottles, plastic filters, etc.
Shop for ultrasonic proximity sensors Multi-Port Junction Blocks.
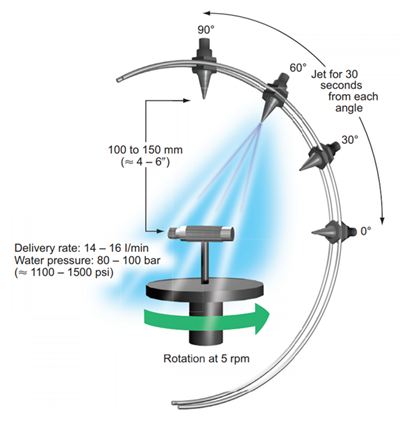
IP69K-rated Proximity Sensors
All Automation Direct Food and Beverage products are tested in accordance with the IP69K standard, according to DIN 40050 part 9. The goal of this test was to duplicate pressure cleaning conditions on a plant floor. In the test fixture, the sensors were exposed to a 1500 psi spray of water at a temperature of 176 ˚F. The duration of each cleaning cycle was 30 seconds. The test was performed at specified angles using a spray nozzle located at a distance of 4” from the switch. The sensors withstood test conditions and were still operable, providing 100%
of sensing range.
Thermal endurance
In pressure cleaning (washdown) environments, proximity and photosensors can be exposed to extreme temperature conditions. A thermal shock test was performed on these proximity sensors by cycling the temperature to ensure their consistent high reliability. All IP69K-rated proximity sensors can withstand temperatures up to 100°C (212°F).
FDA certified Materials
These Food & Beverage sensors are manufactured from materials capable of withstanding solutions used during equipment cleaning. These materials are all approved by the FDA for use in food production environments:
- 316L (V4A) stainless steel
- PMMA (acrylic) • PEEK (Polyether Ether Ketone)
- PPS (Techtron)
Third Party chemical testing companies such as ECOLAB and Johnson Diversey have tested these products with common cleaning agents, such as P3-clint KF and P3-topax 52, to assure continued operation.