By Travis Morris, Safety Administrator, AutomationDirect
As we recognize National Safety Month this June 2025, it’s the perfect time to reflect on how industrial safety has evolved alongside technological advancement. At AutomationDirect, we’ve seen firsthand how the safety landscape in manufacturing and logistics continues to advance rapidly, creating both new challenges and unprecedented opportunities for protecting our workforce—and supporting our customers in safeguarding theirs.
Industrial safety standards have undergone a significant transformation in recent years, primarily driven by the integration of automation and robotics into manufacturing environments. Traditional lockout and tagout procedures have evolved into sophisticated safety systems that incorporate real-time monitoring, predictive analytics, and zone-based safety protocols.
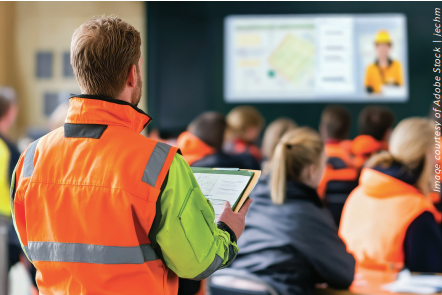
Standards like ISO 13849 and IEC 62061 have been updated to address safety-related control systems, while ANSI/RIA R15.06 has expanded to accommodate collaborative robot applications where humans and machines share workspaces. These modernized standards now emphasize risk assessment methodologies that consider the entire lifecycle of automated systems rather than just physical guarding.
Operator Complacency, A Critical Risk Factor
While automation enhances safety overall, it introduces distinct risks that require careful management. The most common challenges include complacency among operators who develop false confidence in automated safety systems, creating vulnerability during maintenance or unexpected malfunctions.
Complex human-machine interfaces can lead to confusion during critical decision points, while cybersecurity vulnerabilities in networked safety systems represent an emerging threat vector. Additionally, the skills gap means we often have workers interacting with technology they don’t fully understand, raising the risk of improper operation or bypassing safety features.
Consider a typical food processing operation that implements a robotic palletizing system. Such automation could replace manual stacking operations that frequently cause back injuries and repetitive strain issues. A well-designed system would incorporate advanced sensors to detect human presence and automatically adjust the system’s operation to prevent collisions.
In such scenarios, companies can expect to see significant reductions in recordable incidents while also increasing productivity — demonstrating how automation can enhance both safety and efficiency when properly implemented with a strong safety mindset.
Building a Safety-Aware Workforce
At AutomationDirect, we understand that establishing a safety-aware workforce requires more than just hanging “safety-first” motivational posters on factory walls and breakrooms. A true safety culture must go much further than slogans. Leadership, supervisory management, and factory floor workers must own their respective responsibilities for safe operations — and performance metrics and rewards must reinforce their accountabilities.
The reality is that safety isn’t separate from productivity; it’s the foundation that makes consistent productivity possible. While serving customers often drives the operational tempo of a manufacturing or logistics operation, safety’s prioritization is fundamental to sustained productivity, quality, and output. When companies cut corners on safety, the consequences can ripple throughout the entire value chain: reputations suffer; stakeholders lose confidence; customer relationships deteriorate; and most critically, people get hurt.
Balancing efficiency with safety during automation implementation requires careful planning. The principle that “slow is smooth, smooth is fast” applies perfectly here. Rushing high-risk tasks might meet immediate deadlines but creates vulnerability to accidents, injuries, and quality defects — all of which can ultimately slow production more than doing work safely the first time.
Effective implementation starts with comprehensive risk assessments that identify potential hazards early, bringing together cross-functional expertise from maintenance, automation specialists, and operations during planning phases. Mitigating risks through the hierarchy of controls — eliminating hazards where possible, engineering them out, or implementing protective measures — creates systems that are both safer and more efficient.
Training plays a hue role in reducing accidents, but it has to evolve beyond compliance-focused checkbox exercises. Generic presentations rarely engage frontline workers or prevent accidents. Instead, training should be hands-on, site-specific, and directly applicable to real workplace scenarios. Taking workers to their actual workspaces, demonstrating practical skills, and allowing them to troubleshoot realistic situations creates meaningful engagement. With automated systems, this approach becomes even more important —workers need to physically interact with the technology they’ll use daily, building instincts that help them identify and address safety concerns before incidents occur.
Cultivating a Strong Safety Culture
Cultivating a safety culture in manufacturing and logistics means going beyond buzzwords to establish safety as a fundamental operating principle. At AutomationDirect, we’re fortunate to have genuine buy-in from senior leadership and executives who demonstrate healthy respect for workplace safety. This is evident in how we manage our automated logistics warehouse — pushing operational tempo to meet customer demand while simultaneously maintaining serious commitment to managing and mitigating risks.
Leadership reinforcement happens daily through visible engagement. Employees and visitors will see our executives, managers, and safety professionals walking the floor, connecting with team members, and asking meaningful questions related to “How can we make your job safer, more efficient, or both?”
After all, safety should never involve intimidation or policing the workplace. Instead, it should be open for discussion and collaborative. In environments where line-level employees often fear speaking up, we’ve cultivated an authentic open-door policy where everyone has a voice in safety matters.
Encouraging employee ownership of safety requires recognizing the right behaviors. Rather than focusing solely on minimizing lagging indicators like Total Case Rate (TCR) or the Days Away, Restricted, or Transferred (DART) metrics developed by the Occupational Safety and Health Administration (OSHA), proactive actions are needed: hazard reports; safety suggestions; and near-miss callouts.
One idea is putting in place a straightforward QR code reporting system that can make it simple for anyone to flag potential issues, even anonymously. This approach can help every team member become a company’s safeyes and ears on the floor, identifying leading indicators before incidents occur.
When implementing new safety protocols or automation-driven measures, resistance to change is natural. The most effective strategy is collaborative problem-solving rather than top-down directives.
When facing a necessary safety issue that needs resolution, companies should start by thoroughly investigating the issue with affected team members, explaining the underlying drivers — whether regulatory requirements or identified risks — and then asking for their input: “What would you do?” This approach guides people toward solutions while giving them meaningful influence in shaping the implementation of those solutions.
It’s a basic tenet of change management: people are far more likely to follow and enforce protocols they helped create. By inviting those affected to participate in developing solutions that balance efficiency, compliance, and practicality, potential resistance can yield into solution ownership. Once new measures are implemented, feedback loops should be in place to check effectiveness and make adjustments as needed. This collaborative approach turns what could be seen as impositions into shared commitments that team members actively uphold and advance.
The Future of Safety and Automation
Emerging technologies are fundamentally transforming the industrial safety landscape, creating both new opportunities and challenges that manufacturers must navigate. Industrial robots, AI, machine vision systems, and collaborative robots (cobots) are reshaping how we approach workplace safety, particularly in automated environments like our logistics warehouse at AutomationDirect.
One significant benefit these technologies offer is addressing ergonomic concerns — the repetitive motions and awkward positioning that can lead to cumulative trauma disorders over time. By assigning physically demanding or repetitive tasks to automated systems, companies can substantially reduce strain on workers and prevent long-term injuries that have traditionally plagued manufacturing and logistics operations.
However, implementing these technologies requires careful planning rather than hasty integration. A comprehensive risk assessment process is essential at multiple stages: during initial planning, throughout system integration, and after commissioning. Without this diligence, companies risk solving one safety challenge only to inadvertently create others, such as introducing unpredictable machine movements or creating new pinch points.
These advanced systems bring unique safety considerations. How do workers safely interact with cobots? What protocols ensure safe maintenance procedures? Training becomes even more crucial in these environments, requiring thoroughness for maintainance technicians, operators, and anyone working in proximity to automated systems. Workers need clear understanding of operational modes, expected movement patterns, and how to interpret system indicators, lights, and sounds that communicate machine status.
When implemented with proper planning and training, automation technologies significantly enhance workplace safety. When deployed without adequate assessment and preparation, they can introduce new hazards. As we look toward the future of industrial safety, the distinction between success and failure will increasingly depend on how thoughtfully we integrate these powerful tools into our operations.
Future Safety Trends
Looking ahead, manufacturers should prepare for several emerging industrial safety trends. We’ll see increased integration of wearable technologies that monitor worker biometrics and environmental conditions in real-time. Digital twins will enable virtual safety testing before physical implementation. AI-powered predictive analytics will identify potential safety issues before incidents occur.
The regulatory landscape will likely evolve to address new technologies, requiring more sophisticated compliance approaches. Remote operations capabilities will expand, necessitating cybersecurity measures that protect both data and physical safety. Finally, environmental sustainability and worker safety will become increasingly interconnected, with greater emphasis on solutions that address both priorities simultaneously.