Process-enabled motion controllers and motion-enabled PLCs give OEMs the flexibility to optimize design and performance.
By: Kevin McClelion and Joe Scoccimaro, AutomationDirect
There was a time when designing machines that included motion control followed a standard architecture. The PLC handled basic machine control and a dedicated motion controller managed the motion axes. Today, the trend toward smart automation components with increased onboard processing power and memory has blurred those lines. PLCs can now manage multiple axes of coordinated position control, while motion controllers can support a variety of machine communications protocols and I/O points.
This flexibility is a game changer for OEMs and integrators building new platforms. After all, if there is one truism in engineering, it’s that there is no one right solution just the best solution for the application at hand. Modern PLCs and motion controllers streamline design and integration while enabling machine builders to offer customers solutions with higher performance, lower cost, and reduced maintenance.
The Evolution of Motion Controllers
Motion controllers have come a long way from the early days of industrial automation. Motion controllers initially targeted computationally intensive applications like CNC machine control and robot kinematics, or machines with very high axis counts. Due to limitations in computer processing power and memory, many controllers had to be custom designed with hardware for individual applications in order to meet the performance required. Many were PC circuit board based. These controllers had limited communications abilities and no ability to add I/O points.
Today’s motion controllers support OPC UA, the IoT-focused lightweight protocol MQTT, and a variety of industrial Ethernet protocols, including EtherCAT, Ethernet/IP, and ProfiNET. They also have greater I/O capabilities than ever before (see Figure 1). In addition to embedded I/O, motion controllers can now use communications protocols like EtherCAT to connect to as many field I/O points as the CPU can handle. These enhanced capabilities enable motion controllers to perform machine control tasks formerly handled by PLCs, such as PID control of a temperature loop within a motion application.
What are the Process Control Capabilities of Modern Motion Controllers?
High-end motion controllers with augmented capabilities can perform many tasks formerly associated with PLCs, including:
- Process control
- PID control
- Data logging
- Communication messaging
- IEC 611 31-3 programming languages
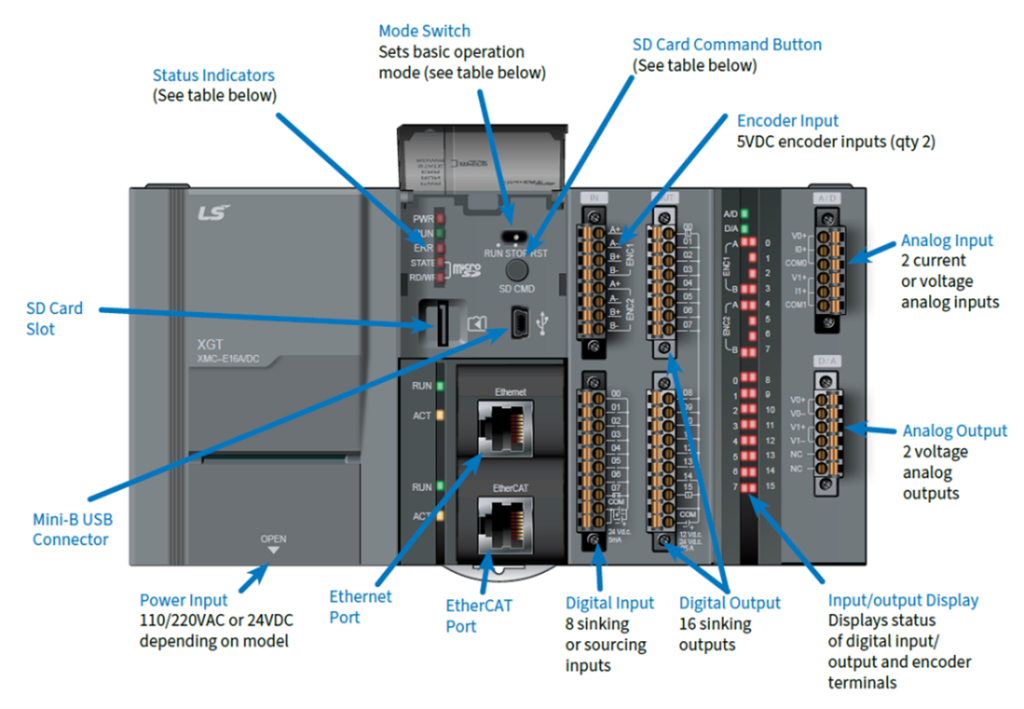
Why Motion Controller-Based Machine Control?
Performing machine control with a motion controller can eliminate the need for a PLC. This reduces costs, integration time, wiring, points of failure, and need for maintenance. For centralized architectures, it also leaves more space in the cabinet.
Tips for Motion-Controller-Based Machine Control
Tip #1: Take Advantage of Remote I/O
PLCs allow I/O to be added directly to the unit, while some motion controllers may not. There’s an easy fix, however. Use high-speed deterministic protocols like EtherCAT to connect the motion controller to remote devices, enabling synchronous I/O control. Remote I/O via industrial Ethernet enables I/O points to be distributed throughout the machine, reducing wiring runs.
Tip #2: Balance Demand on the CPU of the Motion Controller
Even a powerful CPU has its limitations when managing the demanding processes of motion control, network communications, and process control. It is important to ensure that the most critical application, typically the motion control, gets the appropriate amount of CPU time. Managing the cycle rate of the motion network and task scan times of the logic program and network control can make a huge difference in optimizing the CPU. Use the slowest cycle time possible for motion operations and network communications that allows adequate resolution of the application.
The Evolution of PLCs
PLCs started out as machine controllers dedicated to tasks like timing, counting, and managing I/O. As time went on, they gained the ability to control simple motion operations such as uncoupled Y-axis or X-axis movement. Anything more complex, like drawing a circle, required a dedicated motion controller.
Modern PLCs have substantially improved functionality. It starts with more advanced communications protocols, including most industrial-Ethernet protocols, as well as alternatives like ModbusTCP, MQTT, and OPC UA. An increasing number of PLCs are IEC 61131-3 compliant, making them programmable in ladder logic, function block, instruction list, sequential function chart, and structured text.
Additional capabilities include functional safety. This can be implemented either with a dedicated safety PLC in addition to the main machine controller or by using the same PLC for machine control and safety.
From a design perspective, however, one of the key advances is the ability of modern PLCs to manage advanced motion control.
What are the Motion Capabilities of Modern PLCs?
The motion capabilities of modern PLCs include (see Figure 2):
- Pulse direction control mode
- Fieldbus-based motion control
- Linear, circular, helical interpolations
- Homing
- Camming
Gearing support for fieldbus-based motion (e.g., EtherCAT, EtherNet/IP, ProfiNET, Modbus, etc.) in particular, brings significant advantages over pulse-direction control, including simpler wiring, easier system set up and troubleshooting, and better diagnostics.
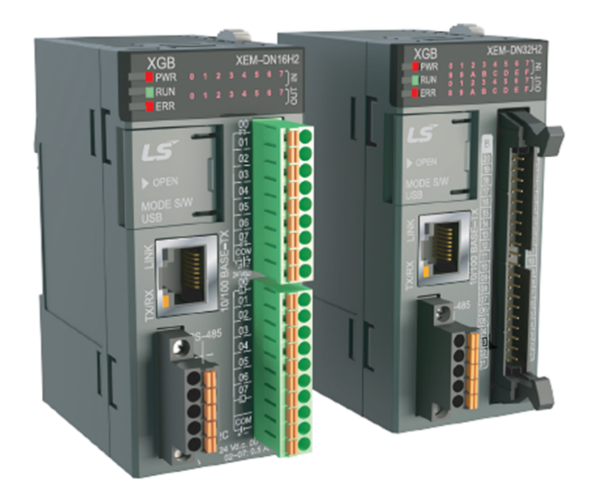
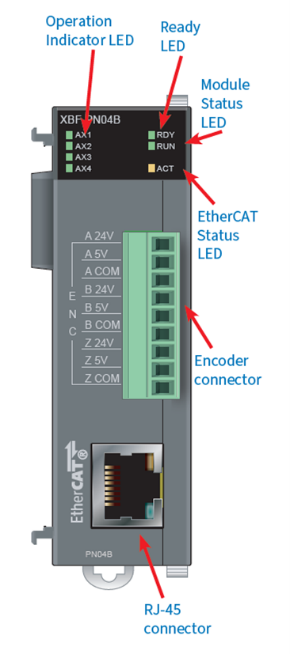
Figure 2: The LS Electric XGB line of motion-capable PLCs features CPU modules with two to six axes of built-in motion control (left). Users can add control of up to 16 additional servo drives using EtherCAT® expansion modules (right).
Why PLC-Based Motion Control?
Performing motion control with a PLC eliminates the need for a dedicated motion controller. That once again lowers cost, integration time, wiring, failure points, and maintenance requirements, as well as cabinet space.
Other benefits are intangible but no less important. Application permitting, some teams are more at home working with PLCs. These additional capabilities let them stay in their comfort zones, where they can operate most efficiently.
Tips for PLC-Based Motion Control
Although the capabilities mentioned above are powerful, the results are only as good as the implementation.
Tip #1: Make Trade-Offs Between Motion and Machine Control
The PLC has a single processor that has to be shared among multiple tasks. Meanwhile, sophisticated motion profiles and high-speed operation require fast cycle times – and lots of CPU cycles. The PLC may be able to accommodate these commands, but the trade-off may be slowing down general communication rates and program code.
Analyze the PLC program processing time and make trade-offs based on what the application requires. If you can slow down the communication rate during motion-intensive parts of the cycle without negatively impacting your process, you can avoid overloading the PLC.
Tip #2: Be Sure to Properly Size the PLC for the Application
PLCs are available with different processing powers. Check the datasheet for the total number of communication nodes, motion axes, and refresh rates and ensure that the application operates within them. If the capabilities of the PLC are insufficient and trade-offs aren’t possible, consider upsizing the PLC to accommodate faster processing speeds.
Making the Choice
The two technologies are not fully interchangeable. Start by comparing the capabilities of a motion-enabled PLC with those of an advanced motion controller (see table). Next, consider the operational requirements placed on the machine by the application and use that to determine the optimal solution
Compares | XGB + PN04/08B | XMC |
Physical design | Compact modular | Block |
On board IO | Up to 16 in / 16 out | 8 in/16 out 2 AI / 2 AO Encoder |
IO modules expansion | Yes | No (remote IO only) |
Pulse direction motion | Yes | No |
EtherCAT motion axes | Yes (option card), up to 16 | Embedded, 8 or 16 |
EtherCAT master | Stepper motor or servo motor only* | Full Master |
Programming: | ||
Main programming | XG5000 | XG5000 |
Motion configuration programming | XG-PM | XG5000 |
EtherNET/IP comms configuration | Table Based | None |
Modbus TCP comms configuration | Table Based | Table (Server) , FB (Client) |
Additional features: | ||
G Code/M Code CNC programming | No | Yes |
Robot controls | No | Cartesian, Delta3, Delta3R and Linear Delta |
When to Choose Motion Controllers
For a machine primarily focused on motion control, with limited focus on communications and machine process control, a process-enabled motion controller might be an ideal fit. Motion controllers use high-performance field-bus protocols specifically designed for real-time communication and deterministic data exchange, making them ideal for applications like robotics, CNC machines, assembly lines, and packaging machines. These applications may require faster cycle times or larger axis counts that make them best suited to a motion controller.
Application Spotlight for Process-Enabled Motion Controllers: Horizontal Flow Wrapper
This horizontal flow wrapper encloses items in a preprinted plastic film, sealing each end with a fin seal. An XMC motion controller controls the entire machine, both motion axes and non-motion tasks, using the EtherCAT protocol with a 500 µs cycle time.
The machine consists of three modules: an infeed module, a film module that wraps and seals the product in the plastic film, and an outfeed module (see Figure 3). The film module includes heaters that form a 2X wide seal between individual items. A rotary knife between the film module and outfeed conveyor cuts that seal in half to separate the product into discrete items, and a second pair of heaters seals the side of the packet before it is released to the out feeder.
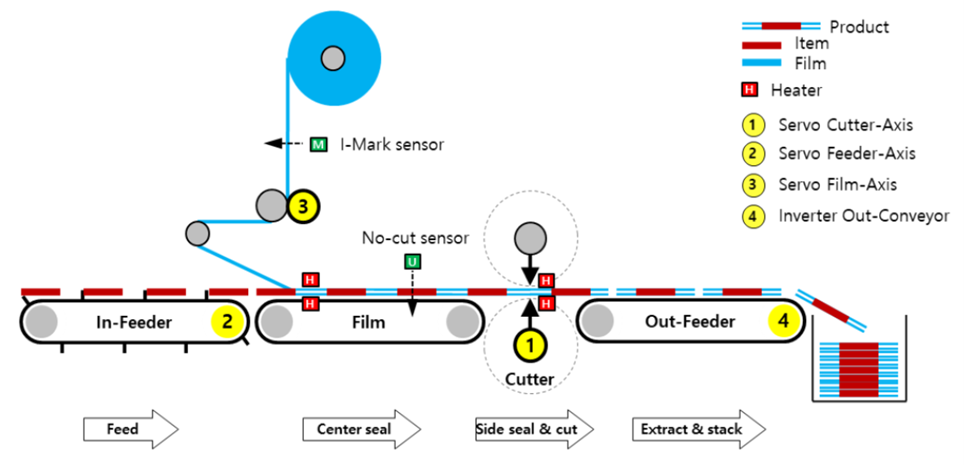
Non-motion components include an eye-mark sensor to synchronize the film feed with conveyor speed, and a “no cut” sensor to prevent cutting if an item shifts or line shafts lose synchronization.
The XMC manages four axes of motion: a servo axis to run the rotary knife, a servo axis to run the infeed conveyor, a servo axis to feed the plastic film into the machine, and a VFD with AC motor for the outfeed conveyor. In addition, the motion controller monitors and controls the heaters and uses input from the sensors to adjust motion operations.
When to Choose PLCs
If the application primarily requires PID control with only limited motion, then a motion-enabled PLC is the best choice. Look for applications that don’t require extremely fast cycle times, such as flying cutoff saws, rotary tables, or small rotary drill machines.
Application Spotlight for Motion-Enabled PLCs: Vertical Cutting Machine
A vertical cutting machine divides a web of Ramen noodle flavoring packets into individual sachets. The XGB PLC controls not just machine operation but three axes of highly coordinated motion in the form of EtherCAT drives operating with cycle times of 1 ms.
The machine can be separated into three modules: an infeed module, a cutter module, and an outfeed module. Axis 1 powers the infeed conveyor. Axis 2 powers the rotary knife that cuts through the sealed sections to separate the sachets (see Figure 4). It must match the speed of the web in order to ensure that it cuts the web at the center of the seals. Axis 3 is the master encoder axis, which is used to phase the feeder axis to correct any slippage in the material.
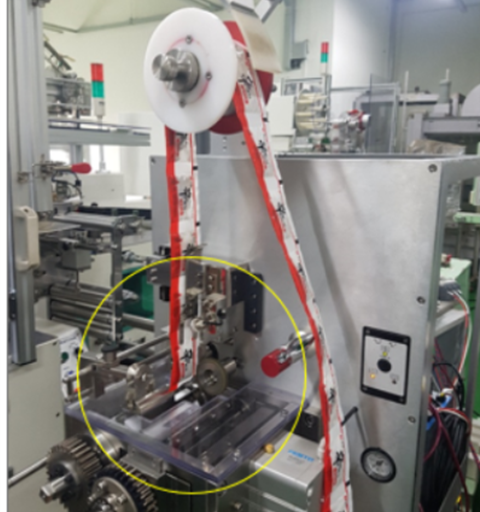
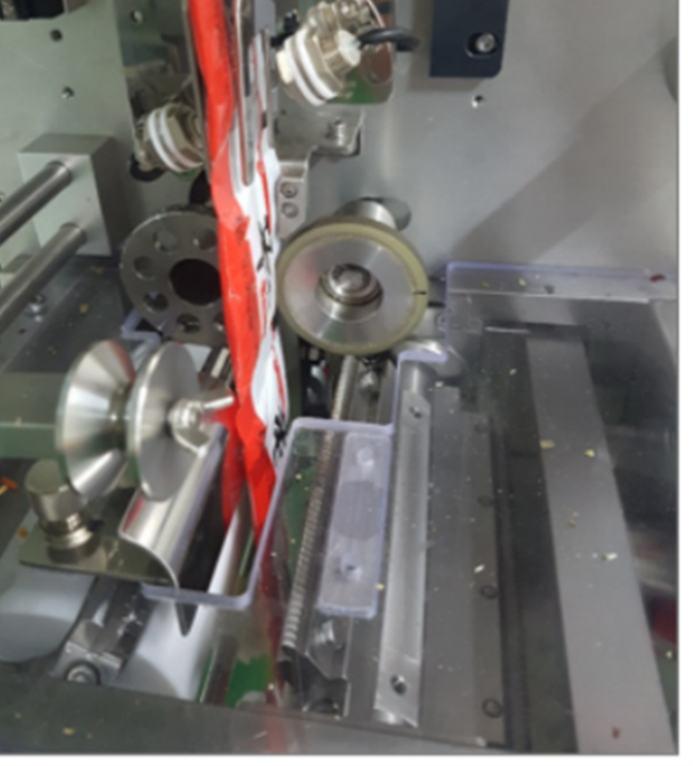
Figure 4: In this vertical cutting machine (left), the motion-capable XGB PLC controls three EtherCAT drives, as well as standard machine controls. Close-up detail (right) shows the cutting axis. (Courtesy of LS Electric)
Conclusion
Integrating machine control, motion and communications into one controller can save in cost and system complexity. Modern motion control provides multiple ways to achieve this goal. Even standard PLCs have very advanced motion control capabilities. Modern motion controllers have added capabilities previously reserved for PLCs, such as communications, I/O points, and data logging. OEMs and integrators have the flexibility to choose the solution that best fits their application and their project.
Sidebar:
Spotlight on EtherCAT
Sidebar text: High-speed communications buses like EtherCAT are the foundation of many of these advances. Moving away from hardwired pulse communications to a fieldbus streamlines commissioning and reconfiguration, adds flexibility, and simplifies maintenance. EtherCAT is a high-performance protocol specifically designed for real-time communication and deterministic data exchange, making it ideal for motion control and I/O expansion. Because of this well-defined standard, integrating different types of components from many different manufacturers is seamless. Designers now have many options when it comes to sourcing parts.