IIoT projects should begin incrementally at the edge, using proven combinations of fieldbuses and controllers.
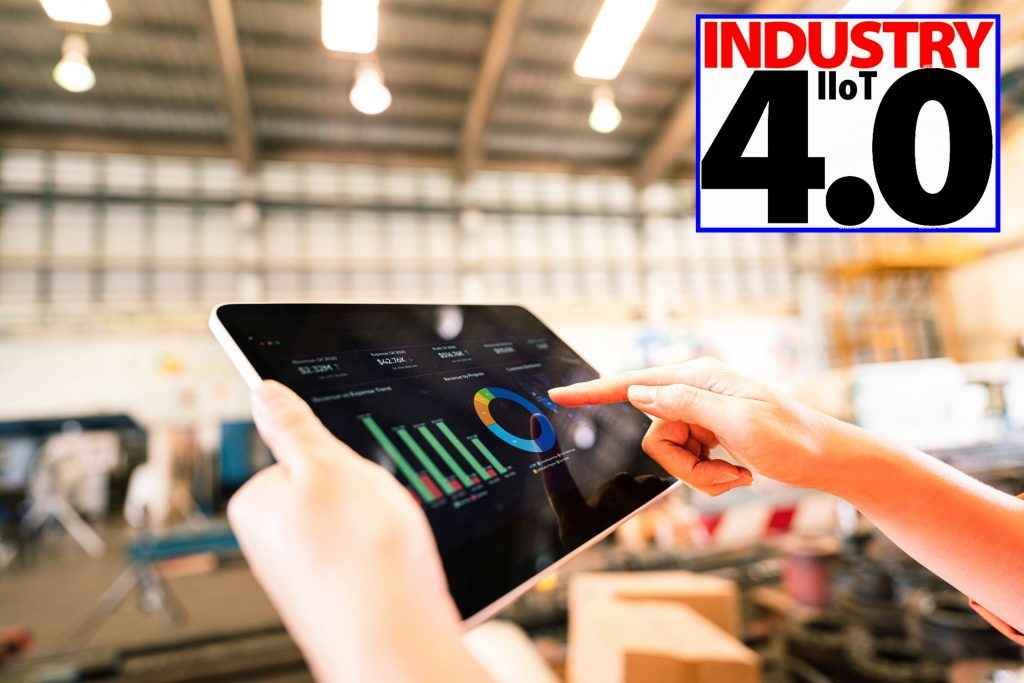
Basic hardwired connectivity has long been typical for automation system designs. However, this approach is shifting as digital transformation and IIoT initiatives are expanding. InTech April 2023 features an article titled Field-Level Comms Improve IIoT Implementations, where Bill Dehner at AutomationDirect describes what is driving this change, and why it is essential to build up from the edge.
Digital drivers
Three of the leading reasons for users preferring digital solutions are:
- Availability of smarter instruments and associated data
- Widespread use of fieldbuses and industrial communication protocols
- An increased need to access data sourced at the edge
Digital transformation, IIoT, and Industry 4.0 mean various things to different end users. Some just want to remotely view data, while others need to perform extensive analytics. But in all cases, an IIoT scheme is only as good as the field-level communications used to obtain the data.
Data everywhere
There remains an important role for hardwired instruments to measure flow, level, pressure, temperature, and much more. But now, all but the most basic field devices are available with some degree of intelligence and digitalization. Smart devices can report much more data and status information, and they can even receive commands and configuration info, but only if they are connected using a digital fieldbus.
A fieldbus is generally considered to be used for operational technology (OT) spaces on-machine or throughout the plant floor, as opposed to information technology (IT) protocols used for higher level communication and computing.
Fieldbus fundamentals
Using intelligent field devices and fieldbuses, users can develop more sophisticated control systems and implement IIoT projects. Some examples of fieldbuses over the years are:
- Modbus RTU: based on serial communications like RS-232
- HART: uses digital communications on top of traditional 4-20mA hardwiring
- Foundation Fieldbus, PROFIBUS, AS-Interface, IO-Link, and others: proprietary or open fieldbuses on various media
- EtherNet/IP, PROFINET, Modbus TCP, HART-IP, and others: industrial communications protocols over Ethernet media
IO-Link
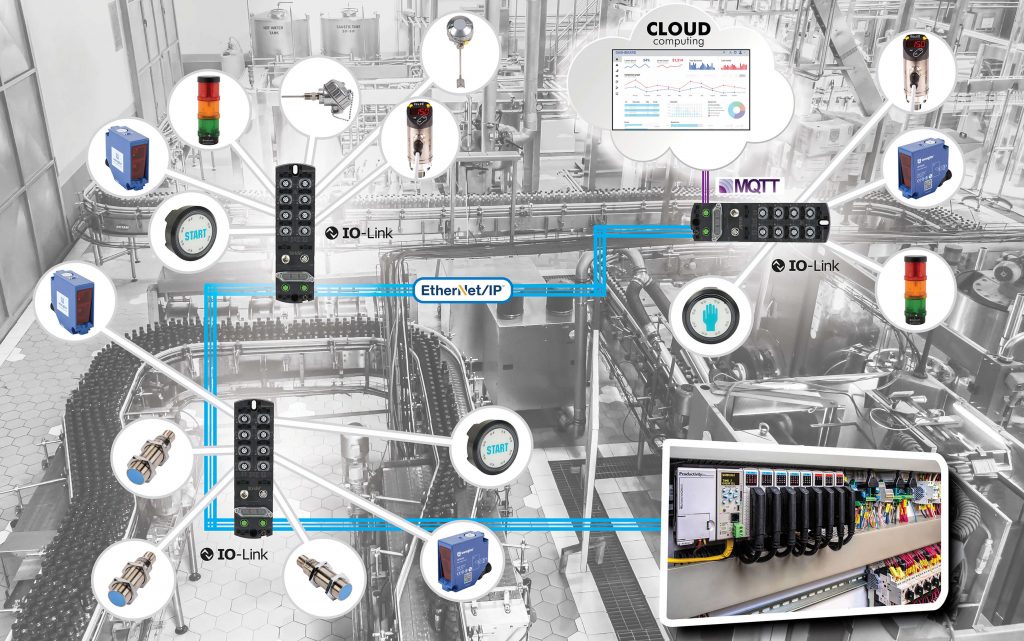
While no single fieldbus reigns supreme, many users are finding great success with IO-Link, which is specified by IEC 61131-9 for point-to-point bidirectional communications over distances up to 20m, and also for providing power.
One notable capability is that an IO-Link network can communicate simultaneously with both a supervisory PLC over EtherNet/ IP, and with other site- or cloud-based systems using MQTT. A PLC can be used as a data concentrator, or IO-Link can communicate directly with higher level systems. This provides designers with the flexibility to implement capable local control, provide data directly to other supervisory systems, and progressively implement any number of PLCs and IO-Link fieldbuses to scale up a complete IIoT solution.
An IO-Link network is particularly useful for many industrial applications, and it can communicate simultaneously with a PLC over EtherNet/IP, and with other higher-level systems using MQTT. This provides significant flexibility for designers, letting them initially establish basic control, and then later progressively implement more PLCs and networks to scale up to a complete IIoT solution.
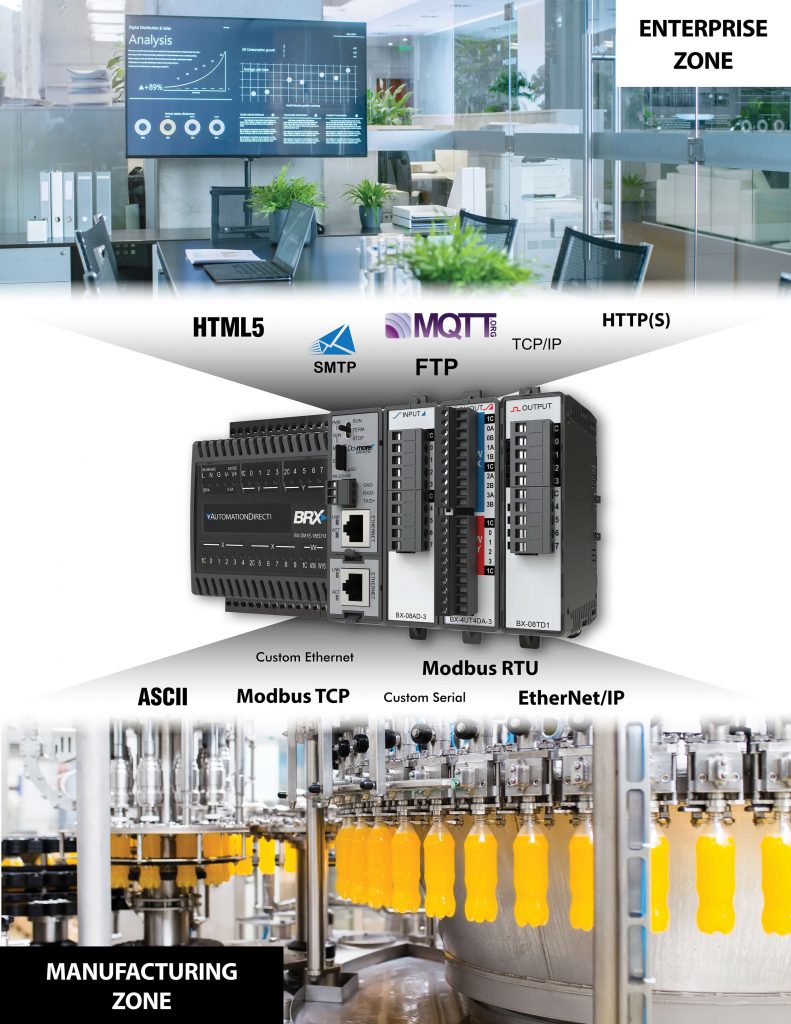
OEMs and end users are leaning into IIoT technologies so they can monitor and analyze valuable edge-sourced data to support optimization, maintenance, and asset management efforts. Check out the complete portfolio of IO-Link devices, sensors, and edge-enabled PLCs at the AutomationDirect.com website.