When a new production line is needed, which is the better partner, an original equipment manufacturer or a system integrator? Many production facilities do not have the resources to plan, specify, design, build, start up, and validate new production equipment as it requires a significant number of mechanical engineers, controls engineers and technicians. On large projects, such as a high speed packaging line, a plant manager can select between two main types of partners; a machine builder OEM or a system integrator.
The table compares important characteristics of the two types of partners. Strong points for the system integrator include the ability to easily provide production lines with equipment from many suppliers, often typical of a large project. OEMs are a bit more concerned with the competition and less likely to work well with others. Another strong point to consider is many integrators have extensive control system design and programming capabilities acquired working with a variety of complex automated systems.
If the production equipment includes several machines from a single supplier, an OEM may be a better choice. The OEM will likely have detailed knowledge of specific, specialized processes related to their equipment. The integrator may have to re-invent the wheel where an OEM has already fully developed the process and knows all the secrets. The OEM knows their machines in a way not possible for a system integrator.
Choosing an OEM or System Integrator
Capabilities | OEM | System Integrator | |
Production equipment experience | High | Medium to Low | |
Automated production equipment knowledge | Meduim to Low | High | |
Multi-discipline resource availability, such as mechanical engineering | High | Low | |
Project management | Medium to Low | High | |
Desire to partner with OEMs | Low | High | |
Wide experience with automated production systems and control hardware suppliers | Medium to Low | High | |
Ability to connect plant floor to upper level systems i.e.- MES, ERP | Medium to Low | High | |
Equipment cost | Low for their own | Higher | |
Factory acceptance tests on actual machines | With own machines | Not at all | |
Flexibility on machine selection | Limited flexibility | Maximum flexibility | |
Knowledge of specific production process | High | Medium to Low | |
Knowledge of local facility | Medium to Low | High | |
Manuals and documentation | Good for machine | Good for system |
OEMs – Experts with Specific Equipment and Processes
OEM equipment suppliers typically promote expertise with specific applications and processes as a benefit over system integrators.
In the Control Design December 2014 cover story “Machine Builders Vs. Integrators”, Paul Strebig, controls engineering manager at USNR, is quoted. “The experience and history that OEMs have in their industry is a great advantage, since this knowledge allows them to select the best products and solutions for each individual customer,” he says. “Most system integrators have limited history in a particular industry. Machine builders specialize in their industry, know how to be efficient, and have fast and effective installations and startup.” USNR is located in Woodland, Wash. and manufacturers machines for wood processing, including everything needed to build an entire sawmill with 30 or more machine centers.
The manufacturer’s strong knowledge and experience with their equipment is important. The OmniTurn CNC turning/milling centers are built by NC Electronics in Port Orford, Oregon. And they know their equipment and its interface well (Figure 1).
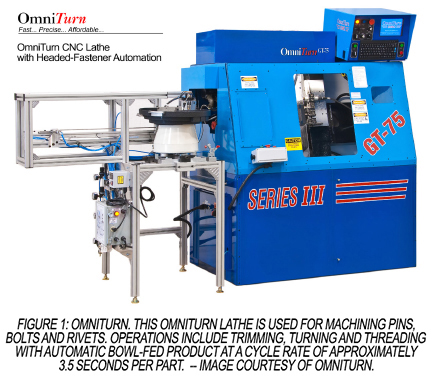
As George Welch, CEO of OmniTurn, explains in the cover story: “We worked directly with one customer to produce the simplest, most cost-effective solution. The OmniTurn CNC can be configured to interface with various controllers, as well as imaging and gaging systems. Because we are familiar with interfacing the Mitsubishi PLC with our CNC, and because we have experience machining parts on the lathe, we saved the customer time and money.”
Welch comments that using an OEM eliminates finger pointing. “We accept responsibility for the entire system’s hardware, and building the complete system,” he says. “In other words, the buck stops with the builder. Additionally, training, service and repair, as required, are handled directly on a one-to-one basis without needing to train and equip a third-party developer.”
In the same cover story, John Martin, VP of Engineering at custom machine builder ARC Specialties in Houston, Texas agrees. “Machine and robot builder OEMs that are vertically integrated hold a unique advantage over traditional system integrators. We take full ownership of a project and drive it from conception, design and manufacture, to integration and production. There is no mix of hands to point fingers in multiple directions, but instead only one responsible company that understands every aspect of the system.” Typical of many OEMs, ARC Specialties has a large facility, allowing factory acceptance testing (FAT) of their equipment and production systems before shipment to their customers.
Often, OEMs have specific resources available to design, modify and support their equipment compared to a system integrator, says Paul Strebig in the cover story. “Machine OEMs are better qualified to provide production line system integration since they are able to have tight control of the mechanical, electrical and controls aspect of a project. This control over design allows an OEM to make changes to optimize a complete solution, whereas a system integrator will be stuck with the equipment they are required to commission.”
The cover story continues with comments from Bob Fung, VP of engineering at Owens Design, a custom machine builder in Fremont, California. “System integrators generally buy existing hardware and put the system together. In general, we have a much stronger skill set and the ability to take on much more complex tools. We can create sections of a tool that a basic system integrator cannot.”
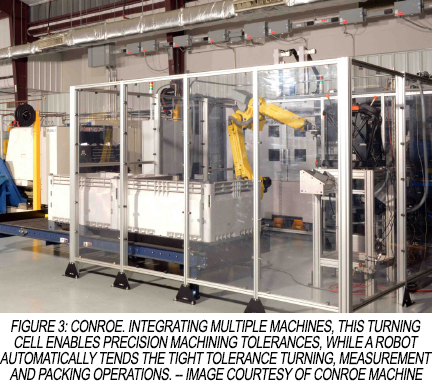
It is common for an OEM to combine their standard machines with equipment from other suppliers to create a cell or complete production line. For example, Conroe Machine is a manufacturer of high precision metal cutting machines (Figure 3), and they often combine their machines with other OEM products to create all or part of an integrated production line. On a recent project, they designed and installed a hard-turning cell for measuring and sorting mud-motor bearings. They also added equipment to box and palletize finished product.
In the Control Design cover story, Matt Wicks, VP of Controls & Software Engineering at Intelligrated, a builder of material handling equipment in Chapel Hill, North Carolina, says, “The argument for independent integrators is they ‘pick the best equipment’ regardless of who manufactures it. On the surface this appears to open up competition and drive down initial purchased prices. In the long run, misapplication of equipment and conflicts between machine builders and integrators can lead to increased costs and project delays.”
System Integrators – Experts with Diverse Automated Systems
OEMs are experts with their specific equipment and processes, and can often successfully integrate their equipment into production lines, but system integrators also have extensive automation knowledge, and the wide variety of equipment and production process they work on extends their experience. Focusing this wide ranging automation experience on select projects has its benefits.
In the Control Design cover story, Joseph Snyder, president of Process and Data Automation, a systems integrator in Erie, Pa, talks about how a system integrator’s experience working with advanced automation systems is a key advantage.
“A packaging machine application that requires a couple of simple infeed and takeout conveyors would normally fall easily within the realm of an OEM”, says Snyder. “But as the system complexity increases along with the number of unique players and parts, a system integrator might be critical to ensuring smooth connection between the pieces. On a very sophisticated system, the system integrator’s experience in connecting to adjacent process areas and business systems might become very important, as most OEMs have not ventured into those arenas.”
“I feel that the chief advantage of system integrators over machine builders when installing new lines is their superior automation system expertise, from using and integrating automation hardware and software from different suppliers, to tying the automation systems to higher level customer software such as ERP systems,” notes Snyder in the cover story.
This automation system expertise can also help when specifying equipment vendors. “On a larger scale, the multi-platform experience of a system integrator will be hugely beneficial when selecting vendors because the overall production system may require multiple equipment manufacturers which, in turn, may mean the introduction of different control equipment suppliers,” he adds in the cover story. “If nothing more, the project management discipline where most established systems integrators excel might be critical for simply keeping the project moving forward.”
The cover story continues with comments from Del Younglas, owner of Texagon Services, a system integrator in Westlake, Texas. “Texagon Services can evaluate the project with the customer and make individual decisions of what component parts are to be retained and what should be replaced,” he explains. “In a majority of Texagon retrofits the customer chooses to retain the existing motors and drives and replace the CNC controller only, which can be a significant savings. Most machine builders and OEMs that do retrofits remove all electrical equipment including the CNC controllers, motors and drives and replace them with their preferred complete system. Economically, this is not the end user’s best choice.”
A Plant’s Point of View
Production facilities have several options when purchasing and installing machines. Essar Steel India in Gujarat, India, has experience with numerous options. As Anil Sharma, general manager, explains in the cover story: “When Essar builds new or adds to a production or packaging line, we’ve used all three methods: in-house expertise, an OEM, and a system integrator or engineering firm. It depends on the project.”
“If it’s a big project, an OEM contributes 90%, while the rest is contributed by in-house expertise and a system integrator. For very small systems, a local system integrator or engineering firm is used,” adds Sharma.
Many facilities have in-house support personnel and use it when they can. Sharma comments in the cover story that there are both advantages and disadvantages to keeping new equipment projects in-house. “If the company uses in-house expertise there is the advantage of low cost,” he says. “Employee knowledge increases, they remain technically updated, and it boosts employee confidence and morale. On the other hand, if we use in-house expertise there are disadvantages. Many times updated technology may not be adopted, the design may not be proper, it may take longer for implementation, and full technical support may not be there.”
Due to their technical knowledge, Essar typically uses OEMs for integration. However, when possible, and commonly for smaller projects, local system integrators are used.
Final Decision
Sometimes the choice between a system integrator or an OEM is straightforward. On simple projects, with a single piece of equipment and related support hardware, an OEM is usually the better option. These types of projects are right in the OEM’s wheelhouse as they have probably installed dozens or more similar machines. The experience and economies of scale are easy to identify.
As the complexity of the project rises, as when adding multiple production lines and a variety of machines and control systems, using a system integrator often becomes a better option. This is especially true if the system integrator can provide long term, local support after the equipment is installed and running.
By Dave Perkon, an independent industry consultant
SIDEBAR: OEM Benefits
As an OEM machine builder in Appleton, Wisconsin, CMD designs and builds equipment for the blown film and flexible packaging industries (Figure 4). Their expertise includes converting equipment for plastic bags, film and pouches along with packaging automation and line integration services.
In the Control Design cover story, Chris White, project manager at CMD explains, “Our automation systems range from taking finished product from one machine and placing it into another machine, to fully customized automation using Cartesian and SCARA type robots.”
Regarding integration services, White says, “CMD provides integration services ranging from integrating CMD equipment for specific product requirements, to integrating our equipment with various suppliers of upstream and downstream equipment. Types of equipment we may integrate to complete a line include dosing units, extruders, bag making equipment, conveyor systems, cartoners and case packers. We’ll integrate manufacturing lines that contain CMD equipment, or a combination of CMD and other suppliers’ equipment—any combination the customer requires to produce the best solution.”
Chris suggests OEMs are well suited for equipment and process integration. “OEMs typically have a very thorough understanding of the equipment and processes involved to provide the best solution,” he says. “Many times if an outside integrator steps in to integrate multiple pieces of equipment they will not fully understand the manufacturing process.”
Not understanding the process thoroughly, especially during commissioning or servicing, can impact production. “If a production line is cartoning and casing rolls of bags automatically, what happens when the cartoner jams?” he asks. “An integrator without experience in the process may say ‘if the line stops, clear the jam, and start the line back up.’ They may not realize the difficulties of starting the line back up, especially if it’s in line with an extruder, which may take a half-hour or more to get back into production.”
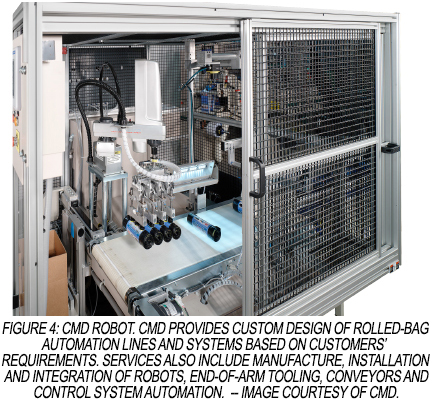
“An OEM integrator very familiar with the process will have provisions to keep the line running and to introduce product back into the system while clearing the jam,” he notes. “Other things the integrator must consider are how to cull defective product; how to handle variances in product size, shape, colors and densities; and how to inspect for some of these items.”
OEMs may also have a wider variety of engineering and technical resources available. “Typically a machine builder OEM is going to have access to machine tools to make mechanical integration parts,” he explains. “The machine builder has purchasing leverage to buy manufactured parts and expedite deliveries of parts. For example, if a controller goes bad during integration, an OEM has access to a wide range of human resources with skill sets in all fields including mechanical, electrical, service and spare parts. System integrators may not have access to as broad of a range of human resources to solve any issues in a timely and efficient manner. These combined resources can be a very powerful tool during the integration/startup process.”
Integrator Advantages
A system integrator in Covington, GA, AAA Absolute Automation and Electrical Services, provides system integration services for production lines and custom machines. AAA ties the machine together with a supervisory control system typically using AutomationDirect products.
Swarner comments that his company starts with customer requirements, or just a concept of how the equipment or process will operate. From the requirements or concept, they generate electrical schematics, build the control panels, integrate the system and provide system start up services. System documentation, operator manual, follow on service and support is also provided. ”Our customer base consists primarily of small to medium sized manufacturing facilities, and we provide system integration services to control machines in integrated production lines.”
In the cover story, Swarner suggests advantages integrators have over machine builders: “Typically, machine builders are very familiar with their machines and standard applications for it, but not with the specific production line where it’ll be installed,” he explains. “Since system integrators normally develop an ongoing relationship with a particular plant, they can be more familiar with the production process and people at a particular plant. This allows us to prevent problems that may arise during commissioning a new machine that’s integrated with the rest of the process.”
Better service and support are also a possibility when using a system integrator. “If an integrator is actively involved in maintaining and upgrading the production process at a plant, they’ll generally be more familiar with any changes that take place that can affect the output from a particular machine,” he says.
“A system integrator can provide better documentation for a system,” he explains. “Typically a machine builder will provide good documentation for their machine, but many times will not spend time documenting how the machine is integrated into the rest of the process. This can cause major problems down the road – especially if the original people that worked on the machine installation are no longer with the OEM,” adds Swarner.
AAA has close relationships with local manufacturers, and usually doesn’t compete with machine builders in these cases. “We haven’t seen machine builders crossing into the system integration territory in plants we service,” he points out. “Typically, the machine is ordered with a standard controls package, and we make all changes and interfaces required to integrate it into the production process.”
Learn more about all of our system integrators here!
Originally Posted: Feb. 2, 2015, Updated: July 2023