When selecting a controller, current and future needs should be considered to ensure flexibility.
Winn Paulk is the Automation Controls Group Product Manager at AutomationDirect, and he wrote an article appearing in the September-October 2018 issue of IMPO titled Choosing the Right Controller for Your Industrial Automation Application. Here’s a summary, please click on the link above for the entire text.
With so many choices in the automation world these days, it can be quite the task to choose where to start when looking for solutions. Paulk’s article highlights several things to think about when choosing a platform to meet an application’s current and future needs, and includes some specific application examples. He says the first step is to document the application to detail the scope and size.
A local machine control application may have just a few discrete inputs and outputs, and a few analog points. For a full-blown process control system, remote I/O, PID control and data collection may be required. While these extensive needs can be met by several controllers on the market today, it’s important to set the scope and then check controller specifications.
Scalability, along with the ability to add remote I/O or analog points, should always be kept in mind when designing control systems. What may start as a local machine sometimes grows into a single piece of a bigger system. The versatility to add more discrete or analog I/O—along with timers, counters and/or PID loops—may be very important if the system grows unexpectedly. The ability to stay with a common platform across applications may save time and money, so it’s often best to look for a family of controllers, rather than a single model.
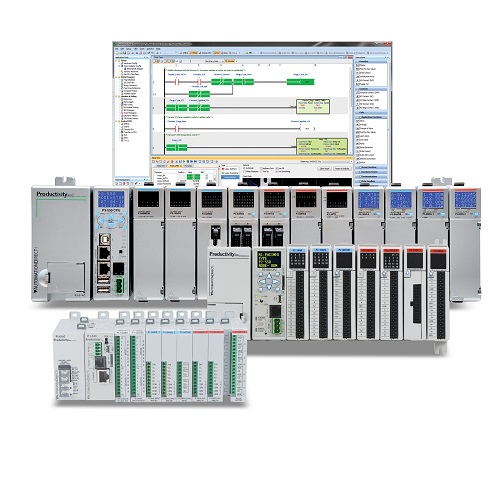
This family of AutomationDirect Productivity series controllers ensures a suitable solution is available for small, medium and large automation applications.
Memory, Communication and Data Needs
Low-cost, brick/stackable controllers often provide only predefined data types and related data tables. These controllers work well for simple automation and monitoring applications, but a tag-based memory with no pre-defined memory addresses is often preferred.
Communication needs should be defined, and more is better in the world of the Industrial Internet of Things. The ability to integrate other control devices with a programmable controller may be a huge factor when choosing a platform.
Communication from a programmable controller to other devices or enterprise systems should be carefully considered, especially if it may be necessary to collect data from a machine or process with the PLC. The data logging feature in some controllers can be accessed via a local USB port or a removeable media storage device. Another option is browser-based access via an Ethernet network and a built-in Web server.
The ability to remotely connect to a PC should also be considered as its often needed for making program changes or fine tuning a process during commissioning. When monitoring a system that is not geographically convenient, or troubleshooting equipment several hundred miles away, being able to connect to a controller remotely may be a required feature.
Simple Software
When comparing industrial automation controller families and platforms, a major factor should be the ease of learning how to use options and features. The availability of a common software platform capable of use on multiple controllers is important if multiple applications are planned that vary in size or complexity.
Ideally, a single programming platform should work with multiple controllers in a product family. This enables existing code from one industrial automation controller to be used in a different industrial automation controller within the family without manual reprogramming.
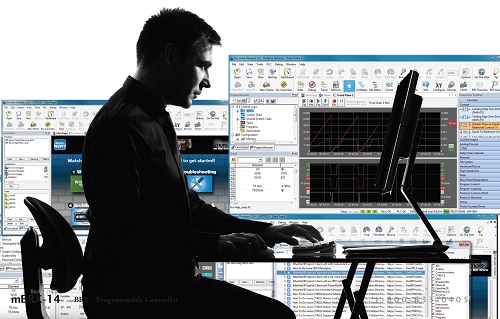
PLC programming software, such as Do-more Designer from AutomationDirect, should be able to program all of the controllers in a product family.
With a common software platform, there are options to scale an application up or down. An abundance of communication options enables remote I/O, control of variable frequency drives and other capabilities. Additional Ethernet and serial protocol options, along with custom protocol setups, adds to communication flexibility.
Paulk says all this research is worth it:
Time and effort spent up front researching controller families and platforms, both the hardware and the programming software, will pay off in the long run with improved ease of use and greater flexibility.
To read more articles related to programmable control, click here.
Originally Published: October 2018