For industrial machinery and systems, designers must apply the right products for physical, electrical power, and automation safety.
Kevin Kakascik, Technical Marketing Engineer at AutomationDirect, wrote an article for the May 2020 issue of Machine Design titled Electrical Safety on the Factory Floor. Here’s a summary, click on the link above for the full text.
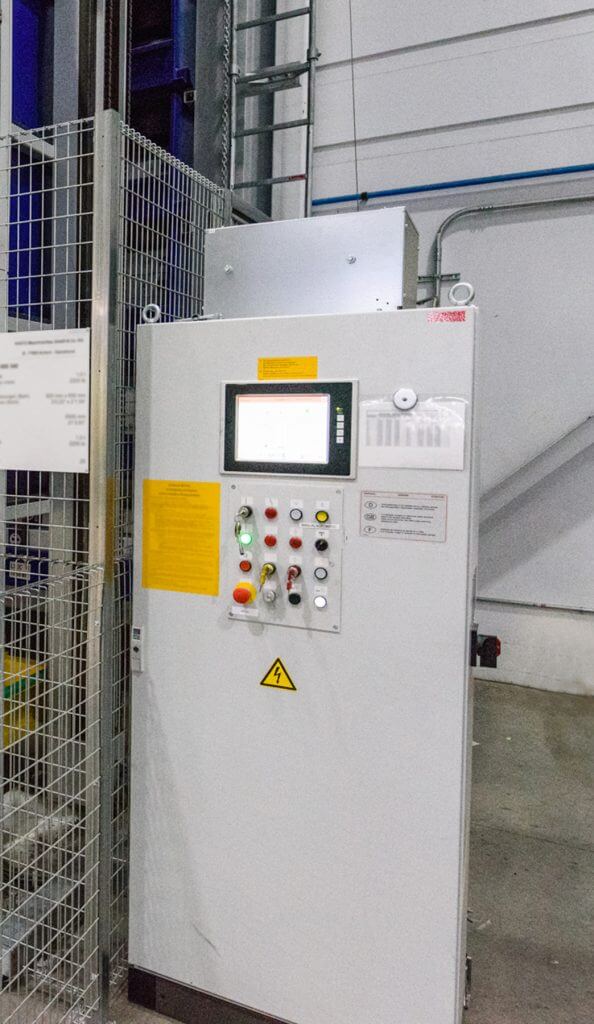
From simple consumer devices to complex industrial machinery, safety features are necessary to protect users from moving parts, high temperatures, electrical shocks, and other hazards. Fortunately, designers have many options at hand to address physical, electrical, and automation safety issues.
Getting Physical
For industrial electrical safety, the best offense is a good defense. Electrical and/or control enclosures protect delicate components from outside contaminants, and also keep workers from contacting those components. Even if the enclosure is open for service, designers can choose wire ducts and products with guards and shields to provide a safer work environment.
On the equipment itself, physical guards and covers protect workers from hazards. But careful designers will include non-contact switches, interlock safety switches, and trapped key interlock switches to limit access and provide the best protection. Additional options for sensing an operator approaching a hazard are safety light curtains, along with safety mats/edges/bumpers, which can be integrated to stop equipment.
Electrical Safety
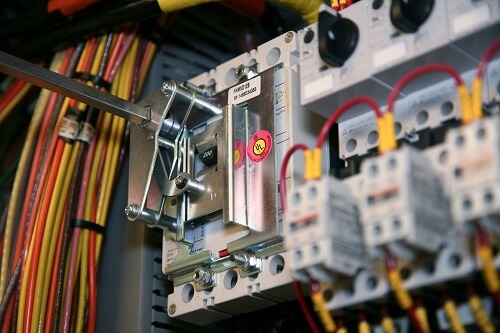
The National Electrical Code (NEC) is the benchmark for safe electrical design and installation practices. Designers include disconnect switches to isolate all downstream systems from power, while circuit breakers, fuses, and overload devices for motors protect downstream conductors from overcurrent and short-circuit conditions.
Surge protection has recently received increased attention, and the NEC now requires surge protective devices on safety interlock circuits. In addition, phase monitoring relays and vibration/temperature/leak sensors can be integrated to stop equipment when a hazardous or problematic condition is detected.
Automation Adds Safety
The ISO 13849 “Safety of machinery” standard guides designers performing a Risk Assessment to identify hazards and safeguard against them. Safety solutions may include the previously mentioned safety sensors, combined with emergency stop buttons and cable-pull safety switches (which can span large areas and are easily actuated by workers). Both of these can be wired into safety relay modules or more advanced safety controllers. If any trouble is sensed, the equipment is brought to a safe state as quickly as possible.
Good engineering design should also include the following properly configured elements to help users quickly understand the operating state and condition of equipment:
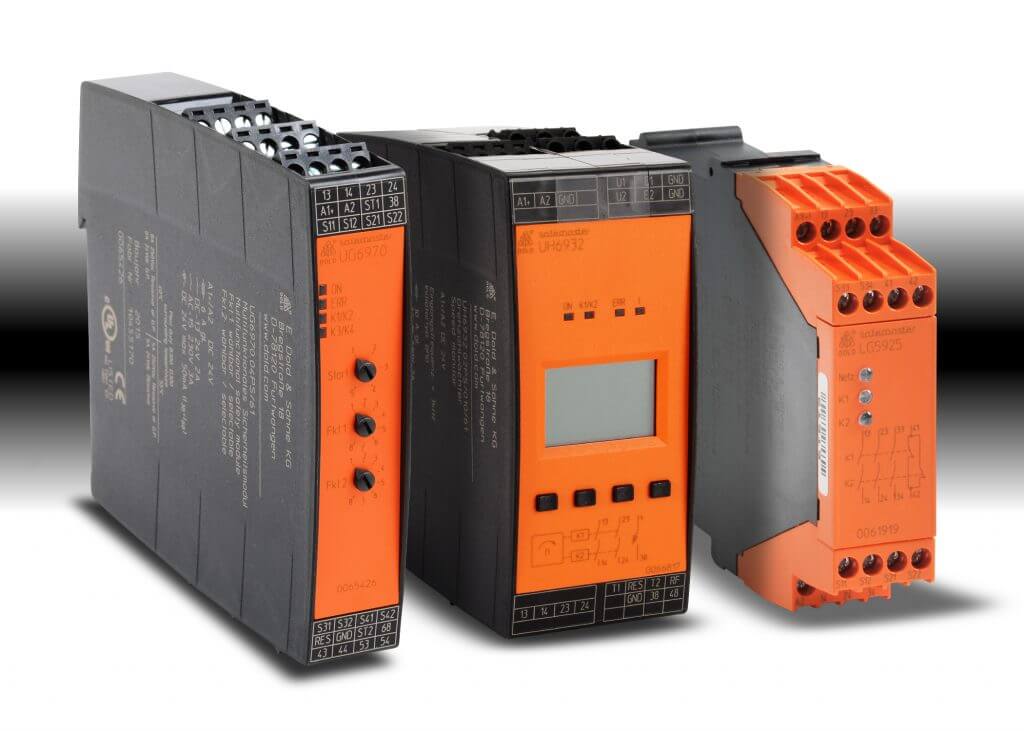
- Stack lights
- Audible signal devices
- Pushbuttons, switches, and indicators
- Programmable logic controllers (PLCs)
- Human-machine interfaces (HMIs)
Design for Safety
Designing safety into industrial machinery and systems is never a “one and done” activity.
Designers can keep safety first for electrical and automation systems by following a layered approach to evaluate conditions and develop designs based on a portfolio of products to address physical, electrical, and automation safety concerns. With the many options available today, designers can deliver the right level of safety to best protect end users.