Using readily available AutomationDirect parts, an Auburn University team converted a CPAP machine to a high-functioning emergency ventilator in the midst of the COVID-19 pandemic.
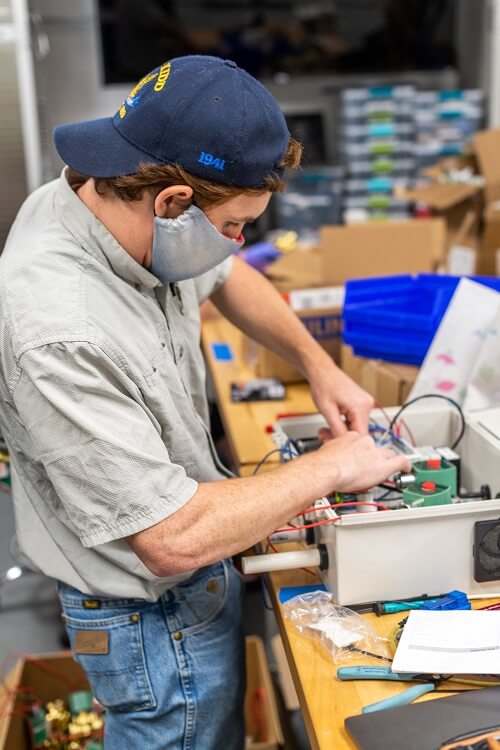
With the threat of ventilator shortages during the COVID-19 crisis, various organizations called on developers to build “emergency ventilators”. A team at Auburn University’s Samuel Ginn College of Engineering went to work, designing RE-INVENT—an emergency room-ready ventilator—over a weekend and developing it throughout the following week. Dr. Tom Burch relates the process in this success story. See the full story from Automation.com titled CPAPs RE-INVENTed into Emergency Ventilators Using PLCs and HMIs. Read on below for a summary.
Several emergency ventilators have appeared recently, but unlike some, RE-INVENT provides warm, moisturized air to help a patient breathe while utilizing proven hardware for the reliability required in life-critical applications. Commercial off-the-shelf (COTS) AutomationDirect components helped make this creation possible.
Quick Iterations
Initially designing in response to an ultra-low-cost ventilator design challenge, the university team determined they could design a ventilator established around a medical-grade CPAP. However, they needed a reliable means to control air pressure, inhalation (inspiration), and exhalation (expiration). First-generation control used a simple circuit to operate valves.
Inspired by promising results, the team continued development, moving to a programmable Arduino prototype board to enable inspiration to expiration (I/E) ratio adjustments. This second-generation configuration enabled refinement of the mechanical, electrical, and controls components of the system, but still lacked the reliability necessary to function in a life-critical capacity.
Along comes the PLC
To deliver the needed reliability, an AutomationDirect CLICK programmable logic controller (PLC) was specified to replace the Arduino. This robust PLC made it easy to program and modify the configuration of the third-generation device and formed the basic automation architecture for the RE-INVENT final product. By adding an AutomationDirect C-More human-machine interface (HMI), users could interact with the automation to adjust settings like the I/E ratio.
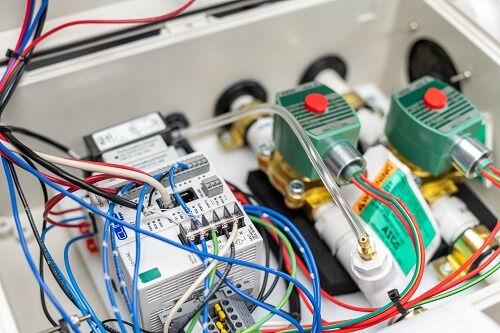
For Critical Applications, use a PLC
Several recently-produced “emergency ventilators” are built using prototype controller boards like the Arduino. Prototype boards are perfect for education and proof-of-concept but are not suitable for critical systems because they simply do not offer the needed reliability.
The CLICK PLC is built to withstand large variations in temperature and other harsh environmental factors. Additionally, it runs a real-time operating system (RTOS), executing all logic and scanning inputs and outputs hundreds of times per second.
Design Details
RE-INVENT is built from the following primary elements:
- Unmodified CPAP machine
- Valves, filters, and hoses
- Pressure transmitter
- AutomationDirect CLICK PLC
- AutomationDirect C-More HMI
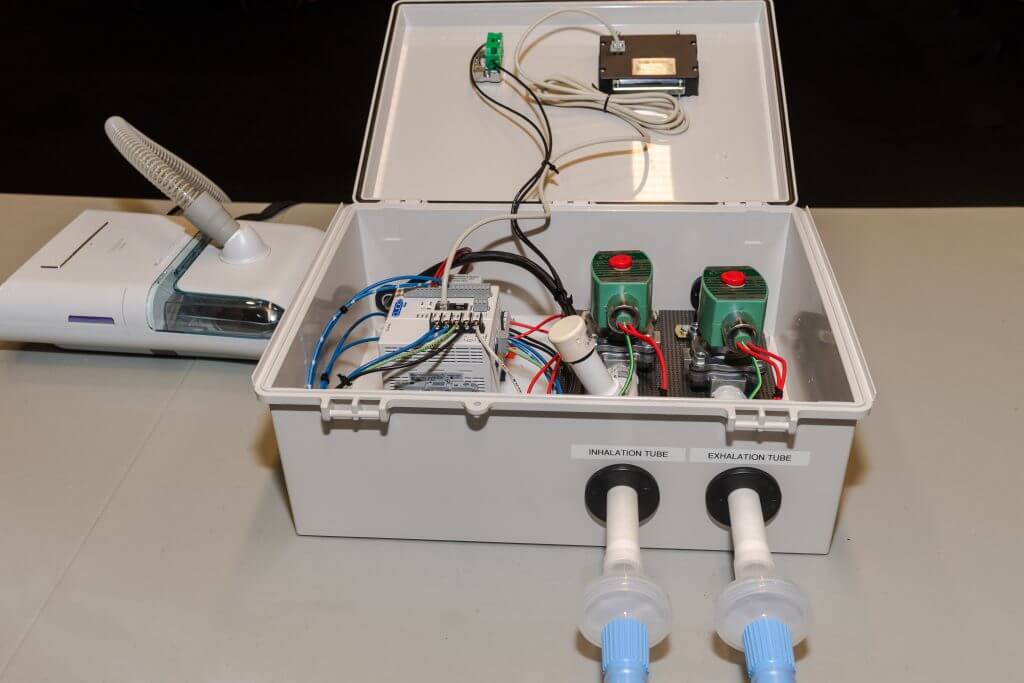
Excluding the CPAP machine, each RE-INVENT unit utilizes about $950 worth of parts. AutomationDirect was an easy choice for the team because it could supply many COTS components quickly and economically. Also, AutomationDirect offers free PLC software, low-cost HMI software, and world-class customer service and technical support.
Through carefully thought-out design and thorough testing, RE-INVENT is ready for the emergency room. Operation is designed to be easily understood by medical staff familiar with CPAP machines and ventilators. The unmodified CPAP runs as normal, and the technician enters the I/E ratio and breaths per minute rates on the C-More HMI. The system also utilizes on-screen alarms to call attention to high or low differential pressure between inspiration and expiration phases.
Next Steps
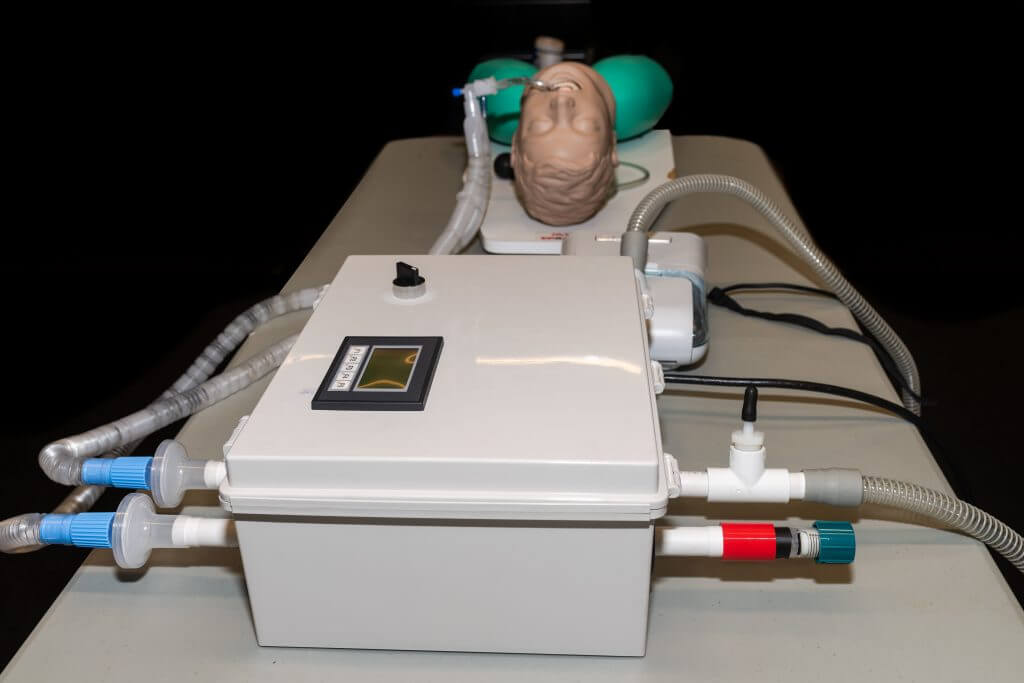
Following extensive testing with a simulated lung, RE-INVENT’s first “real life” test was taking over respiration for a 200lb male Boer goat. During anesthesia, the test team varied the I/E ratio, breaths per minute, and oxygen supply levels while veterinarians monitored the goat’s vitals. All biological measurements remained normal, and the goat regained consciousness as expected at the test’s conclusion.
Auburn University and close associates have manufactured a total of 101 RE-INVENT machines to date and can produce hundreds more if needed without straining supply chains. As PLC control logic is improved in the lab, code updates are easily applied to field units.
Ready to Answer the Call
This project is an example of ingenuity at its finest during a time of need.
The undertaking demonstrates how resourcefulness and the use of commercially available components can play a key role in product development to successfully address a need.
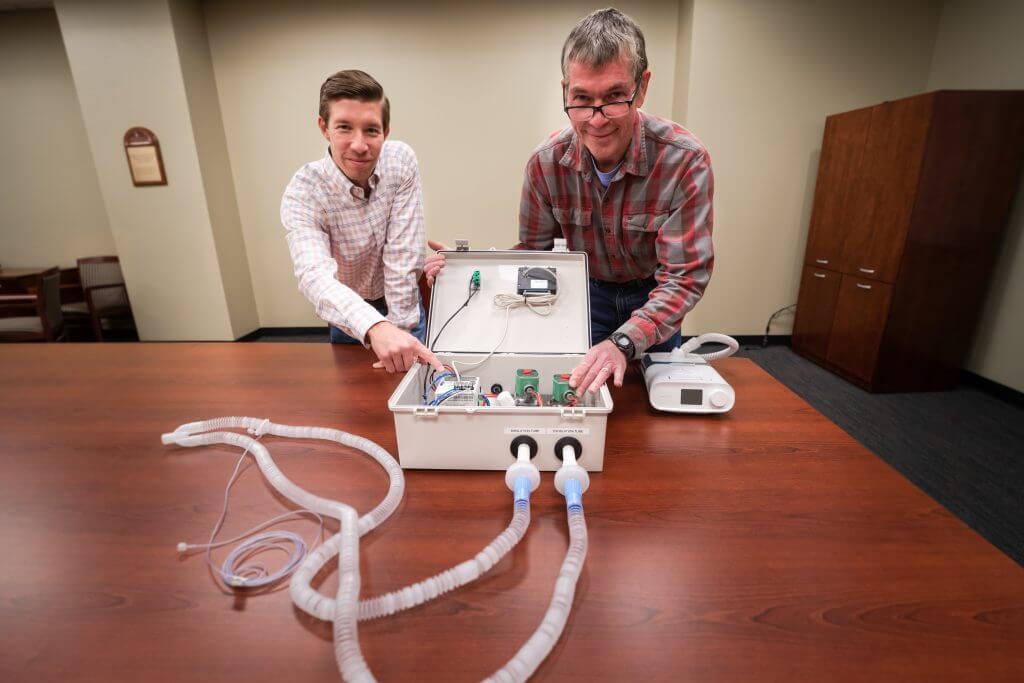
With products like the CLICK PLC and C-More HMI, AutomationDirect supports its customers with all levels of projects, including great innovations like the Auburn University RE-INVENT ventilator.
Check out the AutomationDirect.com website today to explore products that can help your company control its own automation destiny.