A quick look online for control of fluid power shows many types of pneumatic valves for use in factory automation, most of them standalone and individually mounted. But there are also many valve manifold options, including compact modular valves, which are often the best option in multivalve applications because they simplify selection, installation, use and maintenance.
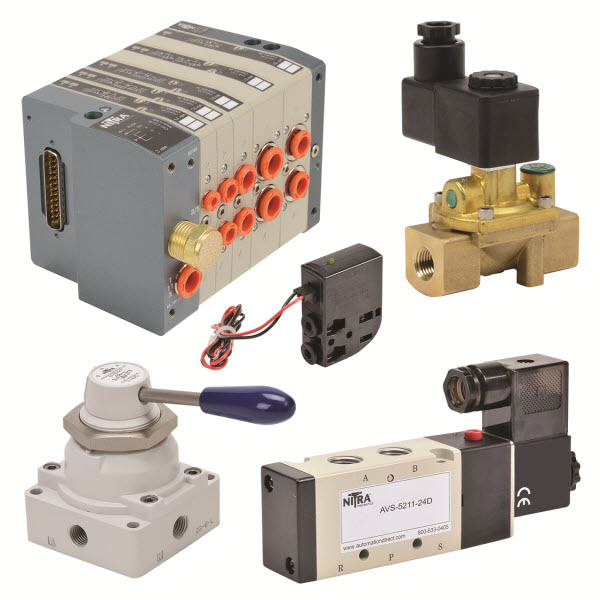
Chip McDaniel, technical marketing engineer at AutomationDirect, discusses in his article, Go Modular to Distribute Pneumatic Valves in the August 2017 issue of Hydraulics and Pneumatics magazine, what valve configurations are available. He also focuses on key design features of compact modular valves and their advantages. Chip starts by explaining available pneumatic valve options when designing an automated machine, with a focus on general-purpose valves:
A general-purpose valve, often called a directional control valve, is the workhorse of pneumatic fluid power. It is available in a wide variety of body styles and configurations. The simplest valves are 2-way, similar to a normally open (NO) or normally closed (NC) relay contact, and 3-way, similar to a single-pole double-throw relay contact. Another common control valve is the 4-way. This valve switches the air supply and exhaust between two outlet ports, and is most commonly used to actuate cylinders and actuators.
Chip also discusses the many mounting options available for general-purpose valves:
A single general-purpose valve can be surface-mounted to a plate or machine leg, or can be directly mounted to a manifold. The valves can also be stacked together using a series of O-rings and various length screws. Other stacking methods eliminate the screws to create modular valve manifolds. If several valves are needed in an automated machine, these manifold-mounted or modular valves are often the best option.
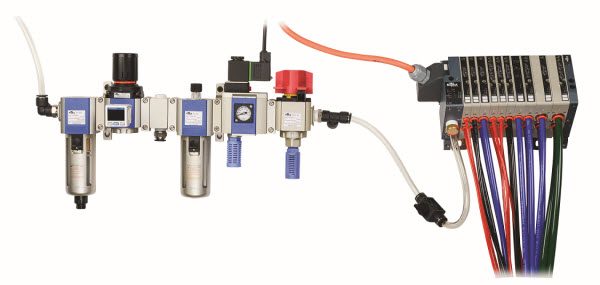
Compact Modular Valve Advantages
In automated machines with multiple pneumatic actuators, compact modular valves are often the best choice. Chip reviews some of the considerations when specifying compact modular valves in the table below and with further comments:
Key Considerations for Compact Modular Valves
- Ease of assembly
- Individually replaceable valves
- Rugged mechanical design
- Protection from dust and liquid protection
- Number of available valve stations
- Different valve sizes and flows in a single manifold
- Pneumatic connections all on one side
- Electrical connections to suit application
- Communication options to match application
Chip’s comments highlight the flexibility, performance and modularity of modular valves.
Ease of assembly is often a driving factor on any machine or piece of equipment. The design of some compact modular valves, whether stacked together or mounted to a multi-position manifold, include built-in captive screws in a valve for easy assembly. Designs where the manifold can be split in the middle, without disassembling multiple valves from one end, speeds adding valves or replacing worn valves during maintenance.
Modular valve banks offer a variety of configurations from 1 to 32 solenoids. This range fills a variety of applications but 8 to 16 solenoids is a more common range. It is best to have valve banks that support mixed valve sizes supporting different tubing and flows as some actuators will require more air flow than others. Common port and tubing sizes on automated machines range from 5/32 to 3/8 in., and 4 to 10 mm.
Connection and Communication
Part of the flexibility of the modular valve includes the connection and communication options. Sometimes changing the endplates provides different discrete and digital communication options, as Chip explains.
As a modular valve assembly is stacked together or mounted to a manifold, the electrical signals need to be robustly relayed from one valve to the next or fed through the manifold. Many designs provide built-in connectors among valves to bus up to 25 or more wires through the manifold. Some even use integral, feed-through contacts for simple and robust electrical connections. Other manifolds may require careful connection within the manifold during assembly or when adding stations, which is not optimal.
Digital communications minimize the number of wires and cables running from the control system to the manifold. It also allows the manifold to report status indication back to the control system. Flexibility is increased because valves or manifolds can be added without running new wires from the control system. Multiple I/O points and possibly entire I/O modules at the controller are replaced by one digital communications port, saving space and money.
Industrial Ethernet is a popular means of connecting to and controlling modular valves. Protocols used include EtherNet/IP, Modbus/TCP, PROFINET, EtherCAT, POWERLINK, CC-Link IE and SERCOS III.
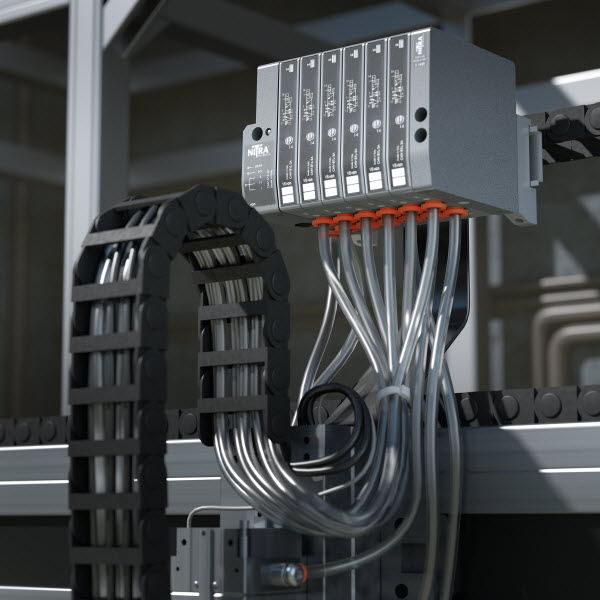
Chip provides some examples on how digital communication, such as Ethernet/IP, minimizes the number of wires and cables running between the control system and valve manifold, as well as providing other benefits.
Flexibility is increased because valves or manifolds can be added without running new wires from the control system. Multiple I/O points and possibly entire I/O modules at the controller are replaced by one digital communications port, saving space and money.
As another benefit, if the modular valve manifold is added to a production line or machine that already has a network, minimal work is required to plug it into the existing network and run a power cable to the manifold.
Once connected the digital communication also provides diagnostic information to the controller, which is not available when discrete wiring is used.
Take Chip’s advice. If you have more than a few valves in an application, be sure to give compact modular valves a serious look. There are many options and features, including industrial Ethernet, to provide a solution easy to install, operate and maintain.