The Innovator team at Copley High School in Akron, Ohio needed to design a piece of equipment to snap caps together for Weaver Industries ProPak, a company that has been employing people with disabilities for about 40 years. With the existing assembly method, Weaver was struggling to meet production and contract requirements for component assembly.
As part of the SourceAmerica 2017 Design Challenge, the Copley Innovators from Copley High School partnered with Weaver Industries ProPak to design a machine, called the Delta Snap, to easily and efficiently assemble a grinding capsule and top into a salt and pepper grinder cap for the food industry. The Copley Innovators won 2nd place in this national competition.
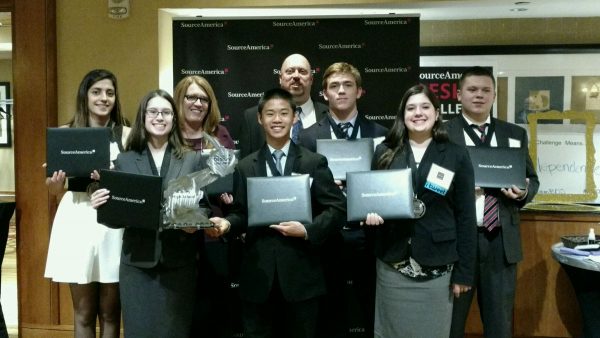
The 2017 Copley High School Innovators team included Colton Murray, Aaron Lampner, Assistant Coach Fiona Casida, Hiba EL Rassi, Coach Kirby Harder, Madeline Wiley, Georgia Shay, Kevin Du.
According to its website (www.sourceamerica.org), the SourceAmerica Design Challenge is a national engineering competition in which participants create innovative workplace technologies for people with disabilities.
The Problem
The original process required snapping together a top cap to a grinder capsule portion of the cap, and gently dropping the completed assembly into a box. The process looked easy, but when snapping the parts together, they would make an audible click as if they were assembled, but another click was often required to fully seat the parts. Also, dropping the part into the box, was causing some of the parts to come unsnapped.
The Copley Innovators visited Weaver Industries ProPak and talked to employee subject matter experts—and to the operation manager in charge of assembling, packaging and quality control of the grinder caps. After this visit, the team got together to brainstorm ideas on how to design and build a semi-automated process to solve Weaver’s production and quality problems. The team decided to split up the work into different jobs such as specifying parts, programming the automation systems, and building the machine.
The Copley team considered fixturing the parts on a pallet and rolling a large drum over the parts to seat the caps, but this prototype roller/press tooling still did not close the caps properly. A prototype press was then designed and built, consisting of an air cylinder mounted to a block to snap the caps together.
The Solution
Although the prototype press worked, it was not safe for operators. Taking what was learned from prototype testing, the team got together and designed a larger, safer and more sophisticated final prototype machine to help Weaver Industries assemble grinder caps. The design of the machine eliminated the need for operator strength or dexterity.
The final prototype machine assembles six caps at a time (Figure 2). The operator preloads the top and bottom caps together into six nests, and presses dual anti-tie-down buttons to start the cycle, assuring that the operators hands are clear of the machine. The machine then extends the part nests under six press cylinders. Once the nests are positioned, the press cylinders extend and press the top and bottom caps together.
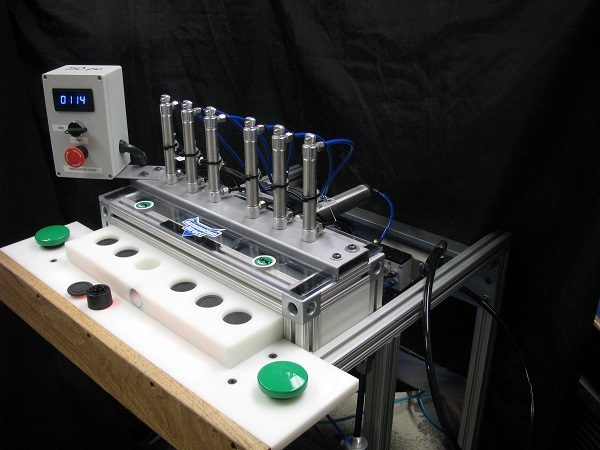
The Copley Innovators solution to the design challenge was to design a manually loaded, six-station, semi-automatic machine they named the Delta Snap.
The press cylinders then retract, and two additional cylinders open a door below the press. This opens the bottom of the nests, dropping the assembled caps into a box. The door then closes and the empty nests return to the load position, completing one assemble cycle of six parts. The operator then repeats the cycle.
Control Hardware, Program and Pneumatics
Much of the control and pneumatic systems used were supplied by AutomationDirect. They have worked with Copley in the past, and were a near single-source supplier for all the controls hardware. Their technical support was also a tremendous help when designing, assembling and programming the machine.
An AutomationDirect CLICK Basic programmable logic controller (PLC) was used because it’s well suited to a machine of this size and complexity. A mating CLICK power supply provided the needed 24 Vdc control power. A 16-point, 24 Vdc discrete input and a 16-point, 24 Vdc discrete output module were connected to the PLC to monitor and control the I/O.
The free CLICK Programming Software was downloaded from AutomationDirect’s online store to program the machine sequence. All team members were involved with the PLC programming, providing a great learning experience. Team members made some mistakes along the way, but in the end, the machine sequence worked as designed.
AutomationDirect supplied most of the pneumatic hardware including cylinders, solenoids, valves, fittings and tubing. Single-solenoid, 4-way, 2-position, spring-return NITRA solenoid valves with ¼” FNPT inlets and outlets are used to control the nine air cylinders on the machine. These valves are operated by 24 Vdc outputs from the PLC, wired through an 11 mm DIN style wiring plug, and the valves operate the NITRA pneumatic air cylinders.
Most cylinders are ¾-inch bore with a 3-inch stroke. These are double-acting cylinders, requiring air to extend and retract, with a magnetic piston. NITRA solid state cylinder position switches detect the position of the magnetic piston within the cylinder to assure a complete press cycle to error-proof cap assembly.
The magnetic sensors are set to the specific cap height (Figure 3). The full stroke of the press cylinders can only be reached if the cap and grinder capsule are both right-side up and correctly positioned in the part nest. All other part positions limit the stroke of the press cylinders, so the sensors don’t detect the piston, triggering an error sequence, and causing the red light mounted on the part nest to turn on.
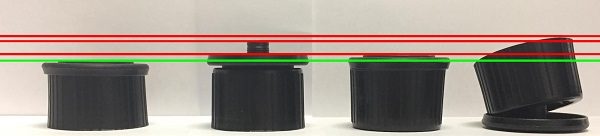
If the cap and grinder capsule were not placed properly in the parts nest, the full-stroke sensors on the press, positioned at the green line, would not sense NITRA cylinders’ magnetic piston.
Operation
The machine is simple to operate, with only minimal training required. It is wheelchair accessible, with both cap parts within reach of the machine operator.
An operator interface panel displays the status of the machine. There is a four-digit display to count parts assembled, along with how many minutes it has taken to fill a box. Red and green lights are embedded in the machine’s part nests. A red light at a nest indicates the cap was improperly placed in the machine, and a green light at a nest indicates the cap was placed properly. When the maximum box part count of 834 is reached, the green lights flash, indicating the full box should be removed and a new box put in its place.
The original process could cause fatigue and there were possible pinch points, but the design of the new Delta Snap machine is safer and much more ergonomic. The machine can only be turned on by a supervisor via a key switch. The machine’s dual palm buttons protect operator’s hands by ensuring both buttons are pressed before the fixture can extend under the press cylinders. There is also an emergency stop button and an air dump valve to stop machine movement.
Impact in the Workplace
The operators really like the machine. It is like playing a game; drop a set of capsules and caps and go. The operators said their hands didn’t get tired, which was an issue when it was necessary to manually snap the parts together.
The machine exceeded every need of Weaver Industries ProPak, and helped ensure the contract to assemble grinder caps remained in place. It solved Weaver’s quality control problem of not properly seating the cap to the grinding capsule. The machine also reduced the defect rate and quality control checks. A supervisor no longer needed to provide a second check of the assembled cap, and the assembly defect rate was reduced from 16% to near zero.
Efficiency was also greatly improved. One operator improved her productivity by 80% the first time she used the new Delta Snap machine, and she had been assembling grinder caps for two years, saving 78 operator hours per order.
The SourceAmerica Design Challenge was a great experience for everyone on the team. They started from ground zero with no knowledge of machine automation, and ended up building build a useful machine for Weaver Industries ProPak and their employees. The team learned how to order parts, program PLCs and work with pneumatics. They also learned how to use tools such as bandsaws and drill presses, and to tap holes and solder wires. Most importantly, the team completed a real-life engineering project where they had to define a problem, brainstorm ideas, and build a machine to provide a solution. See more about the team as well as links and additional images at http://bit.ly/SourceAm and https://www.youtube.com/watch?v=tBdNlCGyTfo.
The big winners were the employees of Weaver Industries ProPak. Instead of bruising and fatiguing the operators with time-consuming manual assembly, each employee now enjoys working with the efficient and semi-automatic Delta Snap machine.
By Hiba El Rassi, 2017 Team Leader of Copley Innovators
To read more articles about programmable control, click here.
Originally posted: Nov 8, 2017