Machine safeguarding devices protect operators at points of access and operation. Here’s how they work.
Jim Krebs, Technical Marketing Engineer at AutomationDirect, wrote an article for the April 2019 issue of ISHN titled Bypass-resistant safety devices ensure effective machine guarding, where Jim describes the need for machine safeguarding, and how the various types work.
The most important machine design step is ensuring operator safety, Jim writes.
During the design process, hazards are often identified that can be removed, but when a hazard cannot be removed, then various levels of safeguarding must be provided. These typically take the form of machine access guarding and point-of-operation guarding.
A best practice requires the selection of safety devices that are difficult to bypass. There have been many cases where guarding has been bypassed, often with disastrous results.
Beyond the national and international safety standards, which the design team should be aware of, and the required mechanical machine guarding, it’s important to understand the proper use of these safety devices.
Safeguarding standards of note
OSHA standard 29 CFR 1910.212 identifies a variety of machines usually requiring point of operation guarding. ANSI B11.x specifications apply to all machines and equipment and include many definitions and performance criteria on the use of interlocked guarding and light curtains. NFPA 79 and ANSI/RIA R15.06 also address safeguarding requirements, as does ISO 13849-1 and IEC 62061.
Some end-users also include additional requirements to safely monitor all removable guarding, regardless of the method of removal or opening. This exceeds the requirements of the various safety standards.
Whether the guarding is fixed, removable, adjustable, mounted to a machine, or installed as a perimeter barrier, safety switches are available to detect their presence. The machine cover, screen, Plexiglas window, gate and/or guard door can all be monitored to protect personnel from machine hazards.
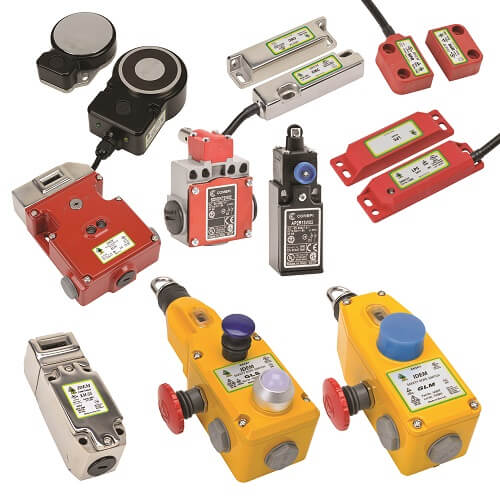
Using these IDEM safety switches from AutomationDirect ensure that even basic machines comply with national and international safety standards.
Using these IDEM safety switches from AutomationDirect ensures that even basic machines comply with national and international safety standards.
Monitor and locking guards
Guard switches on machine guarding provide safety interlocks to stop a machine if an unsafe condition is present. Jim says these guard switches monitor whether the machine guarding is in place, and sometimes lock it in position.
By design, these guard switches are difficult to bypass and must be wired to a safety relay or safety controller to provide reliable monitoring of the defined safety function, such as guarding present and guard doors closed.
Standard limit switches can be easily bypassed by simply tying them down or taping them closed. Safety switches, on the other hand, incorporate design features to resist this kind of bypassing. For instance, tongue interlock safety switches require a specifically related key (tongue) so that they can’t be circumvented by inserting a screwdriver. Some of these devices include a solenoid as well for positively locking the tongue into the switch and preventing it from releasing during unsafe conditions.
Typical non-contact switches can often be circumvented with magnets or metal, Jim notes.
However, safety versions incorporate magnetic coding to operate the switch, so a simple magnet will not operate these types of switches. RFID coding is also available, and it’s even more difficult to bypass. These non-contact switches are a cost-effective method to monitor guard presence. They are easy to mount and tolerate some misalignment, and by nature are not subject to much wear during operation.
Providing appropriate physical guards and defeat-resistant safety switches is crucial, but there are more options available. Using a safety light curtain or safety mat provides a degree of protection from otherwise unguarded machine hazards or access points. These devices can also be used in addition to physical guards. The light curtain itself can be the machine guard.
Safety connections
There are a few approaches when electrically connecting guard presence monitoring switches and safety switches. A basic method is for several guard switches to be connected in series and wired to a single-function safety relay which monitors that the guards are present and closed. In turn, this relay would interlock power contactors or other machine controls to remove hazardous motion and energy.
A better but more expensive alternative is a safety controller, Jim points out.
Safety controllers are more flexible than a relay as they are configured through programming logic. The status of each guard can be easily communicated to non-safety supervisory systems via industrial communication protocols like EtherNet/IP or Modbus TCP/IP.
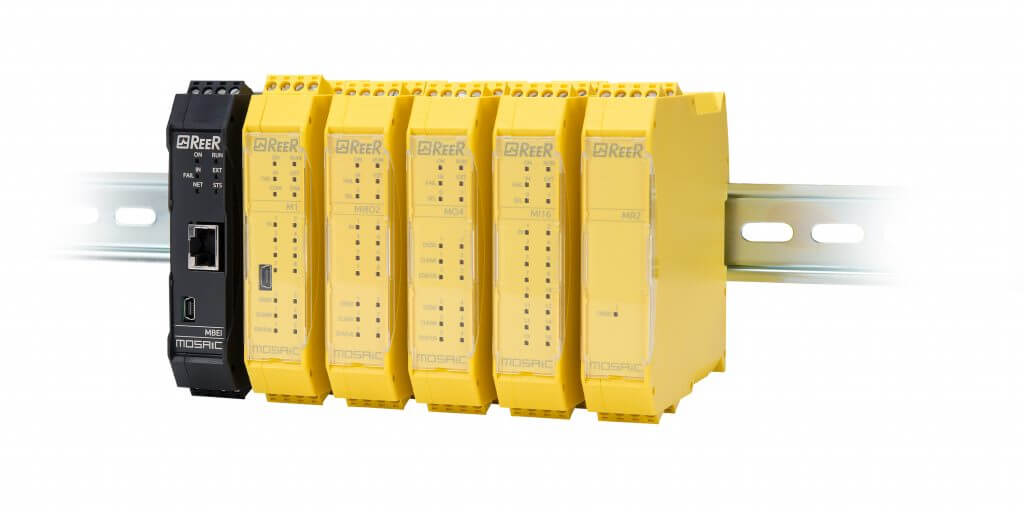
AutomationDirect’s ReeR MOSAIC safety controllers can monitor numerous safety devices and control multiple zones, as well as communicate information to supervisory systems.
Click to read more safety articles.