
Fieldbus technology has been around for more than 30 years and has been a great replacement for point-to-point wiring in many cases. It’s widely used for connecting sensors, solenoids and other field devices to PLCs and other controllers. Ethernet is the most popular fieldbus option and it comes in many flavors.
Back in the Day…
Fieldbus started with simple serial communications, using RS232/422/485 standards and defining the world of multi-drop networks. Ethernet was expensive and non-deterministic, so serial networks dominated. RS232/422/485 was just a hardware standard and didn’t define the software protocol, and vendors used many different proprietary protocols to communicate over these serial networks.
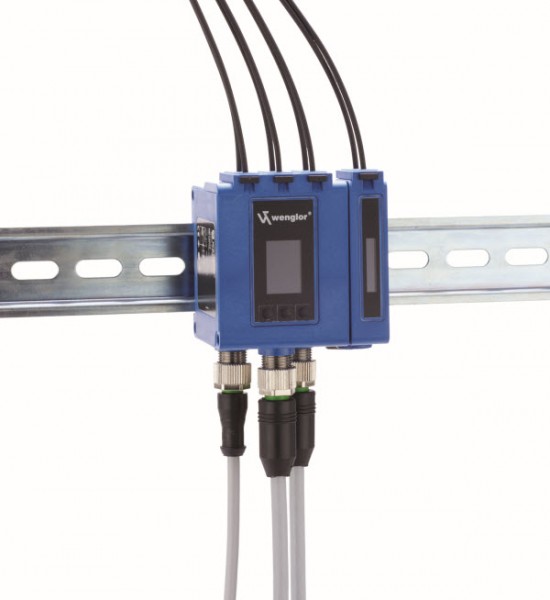
Fortunately, the Modbus protocol emerged as the leader for serial communications. This helped standardize things, and reduced the variety of sometimes expensive and difficult to setup proprietary protocols. These diverse, closed protocols also became more open over the years and became the DeviceNet, Profibus DP and CANopen protocols used today.
These fieldbus technologies have always been good at connecting PLCs to I/O due to their deterministic architecture and ease of expansion. They also have a large installed base and many are still popular today.
These fieldbus technologies have also inspired less complex and more cost effective point-to-point networks such as IO-Link which ties simple field devices, through converters, to PLCs and other controllers. In addition to providing discrete on/off data, IO-Link can also communicate diagnostics, operating parameter and configuration information.
Got Ethernet?
As the technology improved and application requirements increased, Ethernet became an excellent option for connecting motion, vision and other high end hardware to controllers.
Industrialized versions of off-the-shelf hardware, such as managed and unmanaged Ethernet switches, helps improve processing speeds and determinism, and reduces data collisions. Ethernet is fast now and getting faster, and its networking hardware is constantly improving in terms of price-performance ratios.
The technology in Ethernet also allows multiple protocols to operate on the same wire. This is very common in industrial applications, often with a combination of these popular industrial Ethernet protocols:
- EtherNet/IP
- Profinet
- Modbus TCP
- EtherCAT
- SERCOS
- Powerlink
Most of these protocols were originally created by a single vendor and worked only with their products. But now, each of these protocols is administered by its own independent foundation, and each will work with components from many different vendors.
All of these protocols work well in high-speed and synchronized motion applications. To varying degrees, all are optimized for high performance in both common and specialty applications.
And the Winners are….EtherNet/IP and Modbus TCP
In the U.S., EtherNet/IP and Modbus TCP are the most used Ethernet protocols, and it’s common for PLCs to support one or both protocols. Both of these protocols run on standard Ethernet hardware, further promoting their widespread use.
Often the best Ethernet protocol to use is vendor specific, but the application sometimes drives the decision. With EtherNet/IP, a scheduling mechanism, called requested packet interval (RPI), helps optimize data transfer for high speed applications. On the other hand, Modbus TCP, with its wide support and simplicity, is a great choice for multi-vendor applications.

Many industrial applications will have several industrial Ethernet protocols in use simultaneously. Connecting sensors, smart field devices, HMIs and controllers often requires it.
Networking starts at the field devices, which can be connected with a simple and low cost local network such as IO-Link. A gateway can then be used as a multiplexer, connecting eight or more field devices to an EtherNet/IP, Modbus TCP or other industrial Ethernet network. These local networks can connect to larger plant-wide networks through gateways and unmanaged or managed Ethernet switches.
Almost all connections among controllers and HMIs are via Ethernet, sometimes using one network and protocol, and in other cases using different protocols and physically separate networks. Even as the speed and capabilities of Ethernet improve, costs continue to decline.
When it’s time to communicate in industrial automation applications, start with Ethernet. It has great support now along with a superior price/performance ration, and it will only get better.
For more information, please see the Ethernet as a Leading Machine Automation Protocol article in Control Engineering magazine, authored by Chris Harris, Team Lead – Technology Assistance Group at AutomationDirect.
To read more articles about communication, click here.