In 1917, the United States entered World War I, Germany torpedoed the British ocean liner Lusitania, Albert Einstein applied the theory of relativity to model the structure of the universe, and John F. Kennedy was born. That same year, a Canadian inventor founded a manufacturing company that became known for its excellent customer service and high-quality products which were used in strategic applications throughout the rest of the 20th Century and today.
From Backyard Radio Tube Sets to the Toronto Stock Exchange
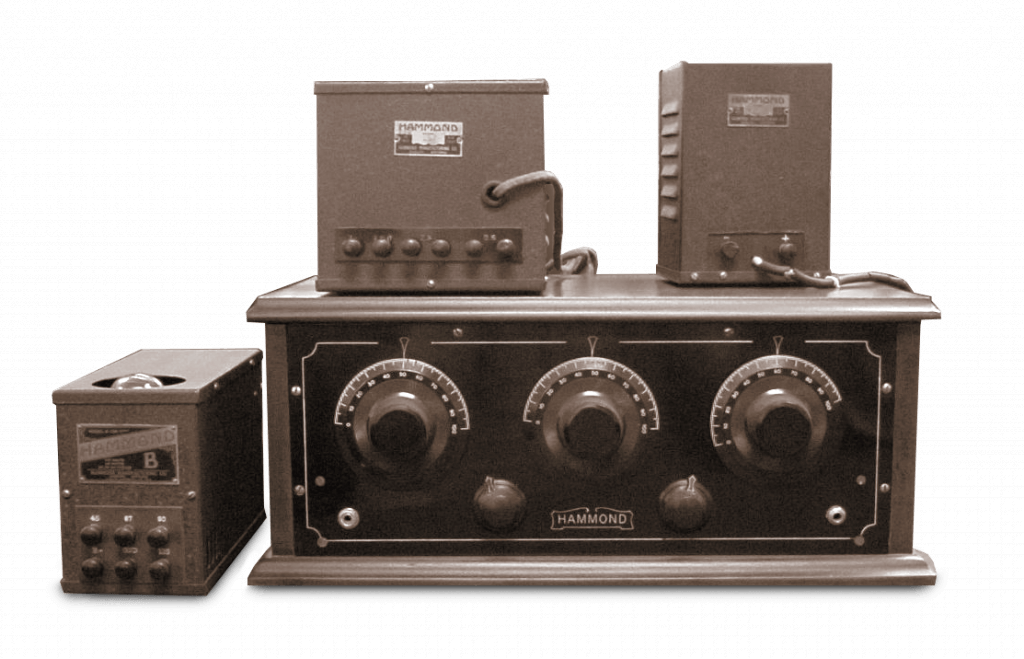
In 1917, Oliver S. Hammond, a tool and die maker, inventor and radio amateur, set up a workshop in the basement of his home in Guelph, Ontario, Canada to build various tools for the foundry industry. Soon, he moved into a small shop in his back yard, and his four sons joined him in the business which became known as O.S. Hammond & Son. The company began making tube radio sets, battery chargers and other related products, progressing from a single tube radio to six tube radios just as radio stations were becoming popular in the United States. Oliver passed away in 1925, and his sons took over the business. Two years later, the company changed its name to Hammond Manufacturing and began making transformers.
As World War II began in 1939, Hammond began building specialized transformers and reactors for military communication and radar equipment. The company quickly grew from less than 50 employees to more than 300 to satisfy the critical surge in demand for transformers. After the War, the need for transformers continued to increase, and Hammond Manufacturing become the industry leader in magnetic transformer design and manufacturing.
The company continued to grow throughout the rest of the 20th Century. The Korean War and Cold War brought the need for military transformers as part of early warning systems in Alaska, Canada, and Greenland. In the 1960s and 1970s, Hammond began making a broader range of specialized and catalog transformers and cabinetry for the electrical and electronic industries. In the later part of the century, the company began trading on the Toronto Stock Exchange.
Growth, Quality, and Service Continue in the 21st Century
In 2001, Hammond Manufacturing officially became two companies, each led by a Hammond family member. Rob Hammond heads Hammond Manufacturing, which manufactures electrical enclosures, electronic packaging, outlet strips, and electronic transformers. Bill Hammond heads Hammond Power Solutions, which manufactures custom and catalog transformers and related magnetics.
Today, the two companies while completely independent employ thousands of people in North America, Europe, and Australia. AutomationDirect carries products from both of these industry leaders. Check out our Hammond Power Solutions profile, and learn more about Hammond Manufacturing below.
Known for Service and Quality – No Matter the Application
Hammond Manufacturing’s more than 800 team members make and service a broad range of carbon steel, galvanized steel, stainless steel, and aluminum enclosure products to protect electrical and electronic applications in a multitude of industries and environments. The company operates a manufacturing facility in its hometown of Guelph, Ontario, Canada and has additional manufacturing and sales locations in Canada, the United States, the United Kingdom, and Australia. It sells to customers via agents and distributors worldwide.
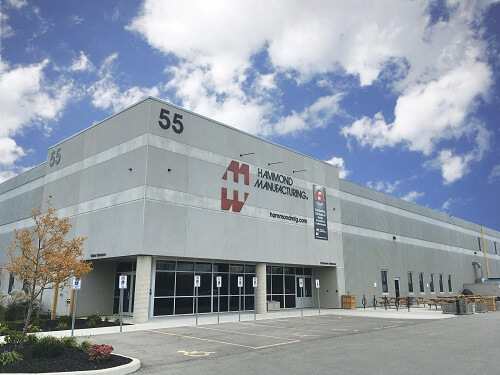
Although its product line has expanded, Hammond Manufacturing’s focus on manufacturing quality products and providing excellent service remains pivotal. “Our customers tell us that our service and quality sets Hammond apart from other enclosures suppliers,” said Robert Hammond, Chairman & CEO. “We work hard every day to continuously offer excellent service and quality in all that we do. We commit our people and resources to ensuring we exceed customers’ needs. These are the cornerstones of our history and our future success.”
Hammond and his employees know that inconsistent quality costs customers valuable time and money. “Fundamentally, enclosures safely house and protect valuable electrical and electronic equipment and are a key component of an Original Equipment Manufacturer’s finished products, so compromising the quality of an enclosure is not an option for us,” he said. “We have a deep-rooted culture of service excellence and a commitment to quality. During our 100+ year history, we have seen many changes to economic conditions, product evolutions, advanced manufacturing capabilities, and more, but the constant from a business perspective is a commitment to adapt and evolve so Hammond remains relevant and sustainable for the long term.”
Enclosures Protect Equipment in Varied Environments
Hammond’s enclosures protect electrical and electronic equipment from whatever environmental conditions exist, including water, dust, dirt, oil, food products, and more. Hammond also offers lighting and other accessories to accommodate special installation needs. The company’s enclosure products are found in a range of applications from desktop test equipment to junction boxes in the ceilings of condominiums to motor controls at a hydroelectrical facility and include:
- Wall-mount enclosures
- Junction boxes
- Pushbutton enclosures
- Floor-mount and freestanding enclosures
- Disconnect enclosures
- Consoles and consolets

Wall-mount enclosures and junction boxes house electrical controls, terminals, instruments, and components and protect them from dirt, dust, oil, and water. Hammond’s Eclipse Series of wall mounted enclosures are its fastest growing product line. They feature quick access, quarter turn latching, and flush cover styling. OEMs and other users now routinely specify this style over more traditional clamp cover designs.
Pushbutton enclosures prevent dust, water, and oil from reaching components. Some types are used for indoor automation control applications, including packaging, material handling, non-corrosive process control, and manufacturing. Others are suitable for industrial or commercial installations where corrosive materials and caustic cleaners are used such as meat and poultry processing facilities where total washdowns with disinfectants occur repeatedly and offshore petroleum sites which are subject to water, wind, and chemicals.
Floor-mounted or freestanding enclosures house large concentrations of electrical/electronic components and are typically found in industrial environments. They are used in machine tool applications to house motor starters, drives, contactors, and PLCs, as well as other electrical and electronic equipment found in automotive, pulp and paper, wood products, and textile industries.Disconnect enclosures protect workers from electrical components when flange-mounted safety disconnect switches are added. Consoles and consolets protect electrical and electronic components and instruments typically used to control a machine or process.
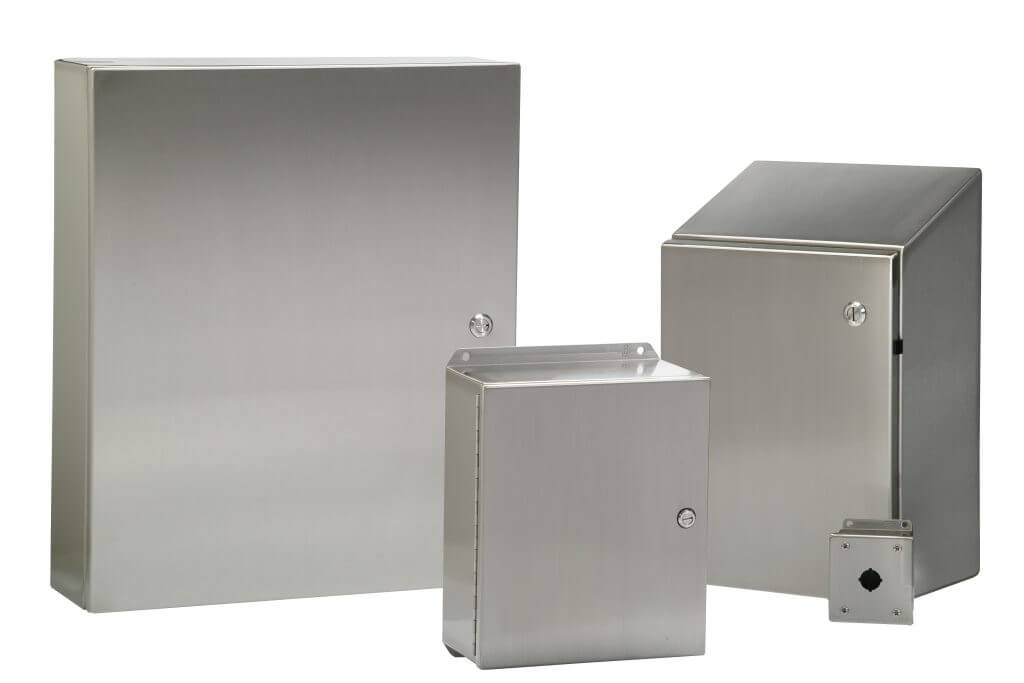
“From a material standpoint, various applications are growing the demand for stainless steel enclosures, so we have expanded our products for those needs. And, we continue to invest in new products and inventory to support the Food and Beverage, Medical, Transport, Infrastructure, and Water related industries. We are excited to continue evolving our company and products to exceed customers’ quality and service expectations throughout this century.”
Solving a Customer’s Contamination Issue
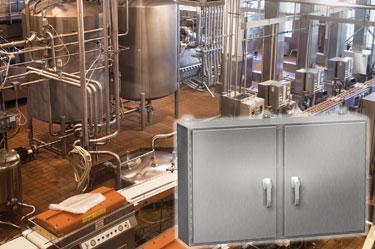
Hammond routinely partners with customers to solve their unique equipment protection challenges. One service company in the oil and gas sector had issues with on-going contamination inside their enclosures. The frequent need for access to the equipment inside the enclosures, combined with improper field door closure practices, turned out to be the problem. While the enclosures being used were appropriate for the environment per NEMA standards, in practical application, the numerous clamps sealing the door were not being properly fixed after every door opening. This left the enclosure box susceptible to external contaminants.
Hammond worked with the customer to identify the issue and then recommended a solution that proved successful. Ultimately, the customer moved away from a traditional heavy-duty clamp cover enclosure to a rugged, three-point handle design that carried all the same dimensions as their original specification. That subtle design change ensured the door sealed properly every time it is closed, virtually eliminating the contamination issue.
A Bright Future
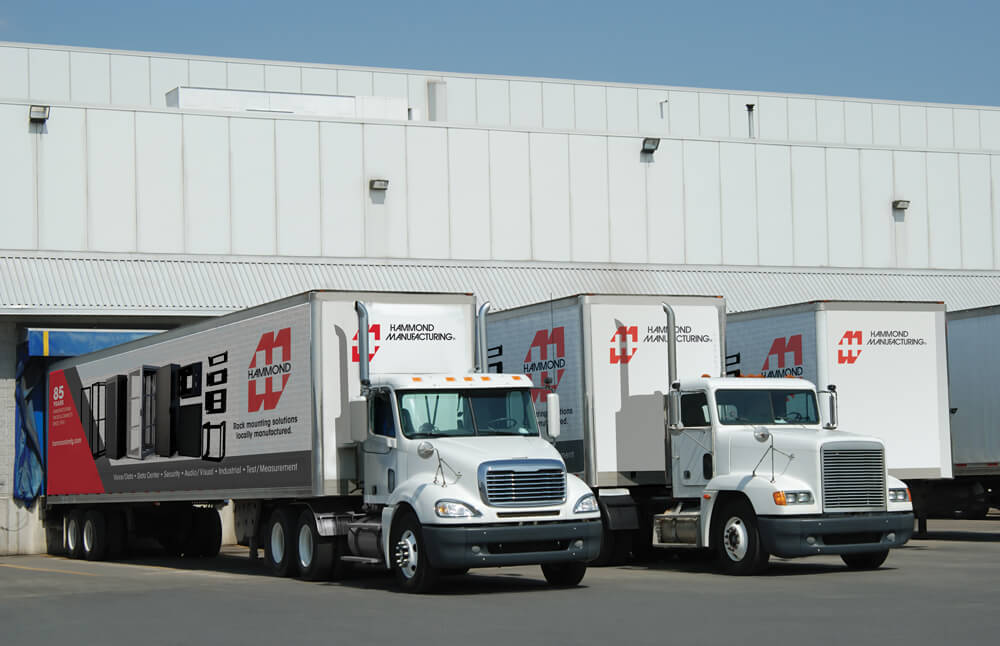
Hammond Manufacturing continues to grow and serve its customers’ evolving enclosure needs and applications in the 21st Century. A 2017 facility expansion added 120,000 sq. ft. of manufacturing space. That addition, along with a warehousing space expansion, has positioned the company well for growth and allowed it to be able to accommodate more than $28 million in inventory. “These expansions provide us with a service position that is almost unequalled in our industry,” noted Rob Hammond.