By: Andrew Waugh
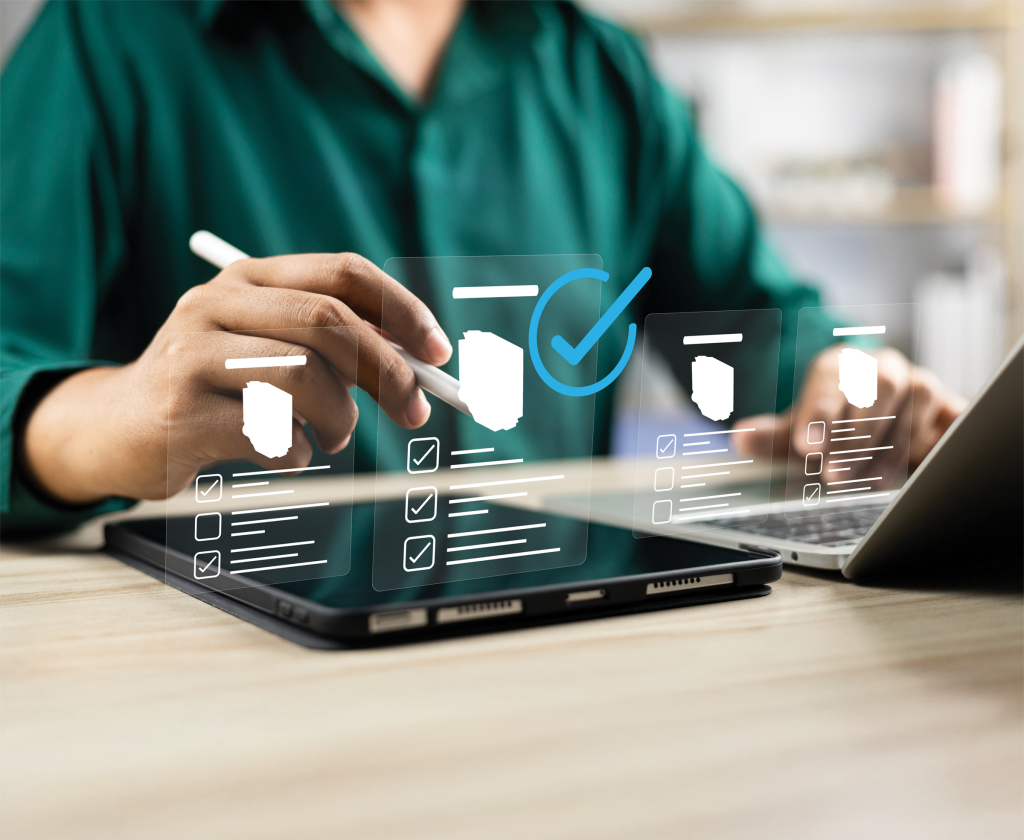
Sensors play essential roles in the modern production environment, capturing data on position, speed, proximity, pressure, temperature, level, flow, current, voltage, and more. There is such a wide variety of sensors on the market that finding the right device for your application can seem overwhelming. It doesn’t have to be. The goal is to find the least expensive, most reliable sensor that will deliver the data you need without breaking the bank. Here, we illustrate the steps of selecting the optimal position, proximity, and distance sensors for the production environment.
Sensor Technology Basics
It’s important to remember that the role of the sensor is to capture data or output a signal. It’s the control system that converts that sensor output into presence/absence detection, a proximity reading, or more sophisticated interpretation such as the water level in a cooling tank.
Choosing the optimal sensor starts with understanding sensing technology.
Touch (e.g., limit switches)
- Mechanism: physical contact with object being sensed
- Pros: simple, compact, cost-effective, insensitive to environmental conditions, good repeatability, economical, unpowered – just breaks a circuit
- Cons: requires physical contact, potentially damaging product; mechanical operation, which brings inherent lifetime limitations
Inductive
- Mechanism: detects magnetic field perturbations caused by ferrous and nonferrous metals
- Pros: Noncontact, solid-state, potentially very high resolution, moderately high switching frequency
- Cons: relatively short sensing distances
Magnetic
- Mechanism: detects magnetic field perturbations caused by specific magnetic targets
- Pros: Can detect magnetic target even when blocked by metal, very high switching frequency, eliminates false positives and interference from other materials in the sensing path
- Cons: requires placement of magnetic target
Capacitive
- Mechanism: detects changes in capacitance caused by the presence of other materials, typically dielectrics
- Pros: Detects solids, liquids; able to detect objects of interest even through nonmetallic barriers
- Cons: low switching frequency, 100 Hz or less; susceptible to false trips by any ambient materials
Ultrasonic
- Mechanism: detecting a reflected or transmitted ultrasonic signal
- Pros: no requirements for physical characteristics of the material (e.g., ferrous, dielectric, etc.); insensitive to material characteristics such as reflectivity, optical transparency, irregular surfaces; working distance on the order of meters
- Cons: low spatial resolution, expensive
Photoelectric
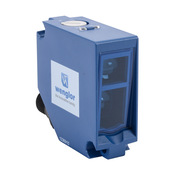
- Mechanism: detecting a reflected or transmitted optical signal, from IR to blue light, typically LEDs
- Pros: optical wavelength can be selected to optimize performance and safety, working distance on the order of meters, high accuracy and repeatability: greater complexity, source wavelength may need to change if application conditions change
- Cons: Susceptible to false reflections or other ambient lights, material surface can alter state
Laser
- Mechanism: distance measurements through time-of-flight or triangulation
- Pros: long distance (meters) for TOF systems, micron-scale accuracy and repeatability; working distances of less than a meter for triangulation systems with micron-scale accuracy and repeatability
- Cons: greater cost and complexity, sensitive to vibration and environmental contamination
And now, we can proceed to the process of specifying a sensor.
Step #1: What material are you trying to sense?
Different sensing technologies respond to different materials (see Table 1). The first step is to identify the material you’re trying to sense and select the technology best suited to it.
Table 1
if you’re trying to sense… | These sensors will work best |
Ferrous metals | Inductive sensors |
Nonferrous metals | Inductive sensor or capacitive sensors |
Dielectric materials (e.g., wood, glass, plastic, cloth) | Capacitive, ultrasonic, photoelectric, or laser sensors |
A variety of material types (e.g., metals, glass, plastic) | Capacitive, touch, or ultrasonic sensors |
Liquids | Capacitive or ultrasonic sensors |
A target that can be touched | Touch sensors |
An uneven surface | Ultrasonic sensors |
Glass surfaces | Ultrasounic or photoelectric sensors |
Objects hidden behind barriers (e.g. the position of the piston in a pneumatic cylinder, the level of liquid in a tank) | Capacitive (nonmetallic barriers only) or magnetic sensors (any barrier) |
Dark or shiny objects | Photoelectric sensor with blue light |
Step #2: What is your working distance?
Once you’ve identified candidate sensors that can work with your materials, the next step is to identify which devices can gather the data you need over the working distances of your application. Notably, touch sensors have the tightest working distance (zero), while laser sensors offer the longest working distances (up to 100 m; see Table 2).
Table 2: Summary of sensor characteristics
Sensor type | Working distance | Switching frequency | Cost | Reliability | Accuracy | Repeatability | Resolution |
Limit switch | Zero | Slowest | $$ | Medium | High | Low to High | Medium |
Inductive | 0-50 mm | Fast (~2 kHz) | $ | High | High | High | Medium to High |
Magnetic | 60 mm | Very fast (~5 kHz) | $$ | High | Medium | High | Medium |
Capacitive | 0-45 mm | Slow (<100 Hz) | $$$ | Medium | Low | Medium | Low |
Ultrasonic | 0-10 m | Very slow | $$$$ | Medium | Low | Medium | Low |
Photoelectric | 0-50 m | Fast | $$ | Medium | Medium | Medium | Medium |
Laser | 0-100 ms | Very fast | $$$$ | Medium | High | High | High |
Steps #1 and #2 will get you to the first approximation of the best sensor for your application, but Table 2 shows where the real fun begins.
Step #3: What are your other priorities?
Engineering is always about trade-offs. Now that you have a starting point, consider additional parameters important to your application. The sensor needs to have a fast enough switching frequency to handle the operating parameters of your system. If you need to do presence/absence sensing for a high-speed conveyor or are trying to monitor the teeth in a pair of meshing gears, you need to either find a sensor that’s fast enough to capture the necessary data, or slow the process down.
Additional factors to take into account are performance metrics such as accuracy, repeatability, and resolution.
As you work your way through the decision tree, don’t forget that your goal is to find a sensor that meets performance requirements while offering the lowest cost and the longest lifetime. As the table above shows, there are many parameters to play with. Knowing your priorities simplifies making the best selection.