New sensors and connectivity devices supporting digital IO-Link communications let users easily gather extended diagnostic and device data.
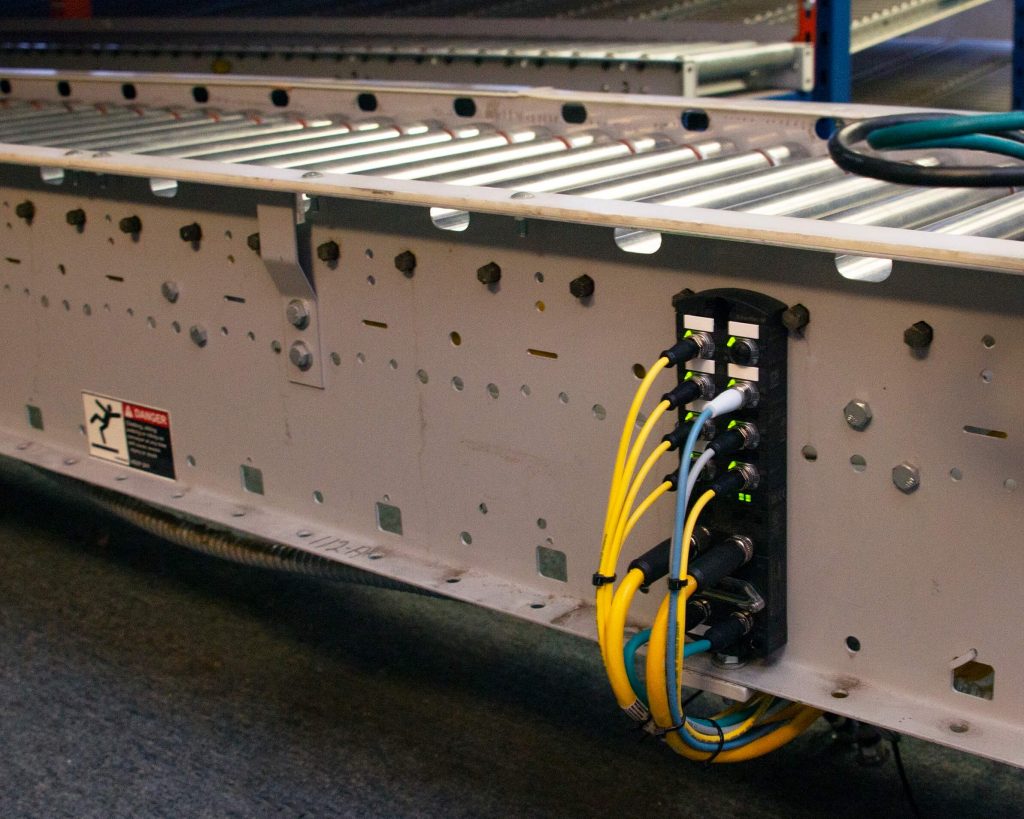
Chris Kregoski, product engineer for AutomationDirect, authored an article posted August 2022 on the Automation.com website titled A Stronger Link for I/O. Here’s a summary, click on the link above for the full text.
A concept called the “last mile problem” refers to the difficulty of completing the last link in a process, such as running internet cables to a user’s home. For industrial automation systems, one aspect of the last mile problem is connecting all the wiring from I/O modules to instruments, sensors, and field devices.
Traditional conduit and hardwiring have been the norm for these connections, but this is a relatively expensive and limited approach. Digital serial communications, industrial fieldbuses, and Ethernet are more sophisticated connectivity methods but are not applicable to the multitude of basic field sensing and actuating devices.
To solve this challenge, the IO-Link protocol has been developed to make it easy and economical to establish advanced connectivity with a wide variety of field devices. This empowers users to gather and analyze data, and therefore improve the performance and maintainability of their systems.
Two-way Transmission
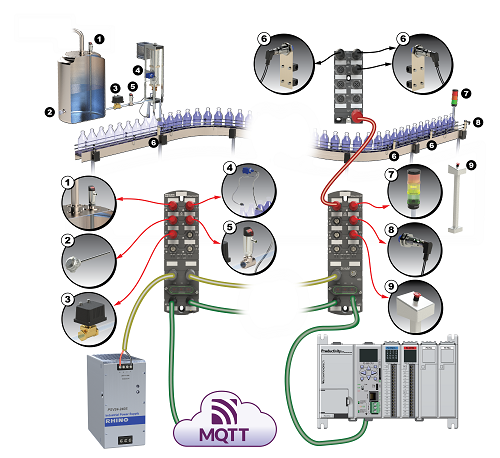
Basic hardwired discrete and analog input and output signals can be connected over great distances but provide only one continuous channel of information travelling in one direction. Digital signaling methods convey much more information in the form of data packets transmitted over a single cable. This type of networking requires more design and installation effort, making it impractical for simple industrial signals.
IO-Link is a newer and much more cost-effective bi-directional communication standard as specified in IEC 61131-9. It is a fit-for-purpose technology providing point-to-point communications over a useful distance of up to 20 meters using standard unshielded three-wire cabling operating at 24V DC. Every connection can cyclically communicate 32 bytes of data, which can include multiple process values, configuration settings, and diagnostics.
Simple Architecture
AutomationDirect offers STRIDE IO-Link “master modules” and “hubs”, available in IP67-rated surface-mount form factors using M12 plug-and-cord connectors, for networking and power distribution, with auto-sense to work with standard input/output (SIO) or IO-Link capable devices. Users can mix-and-match the wide variety of field devices now available with IO-Link, with some of these devices also providing additional indication/display and other advanced features.
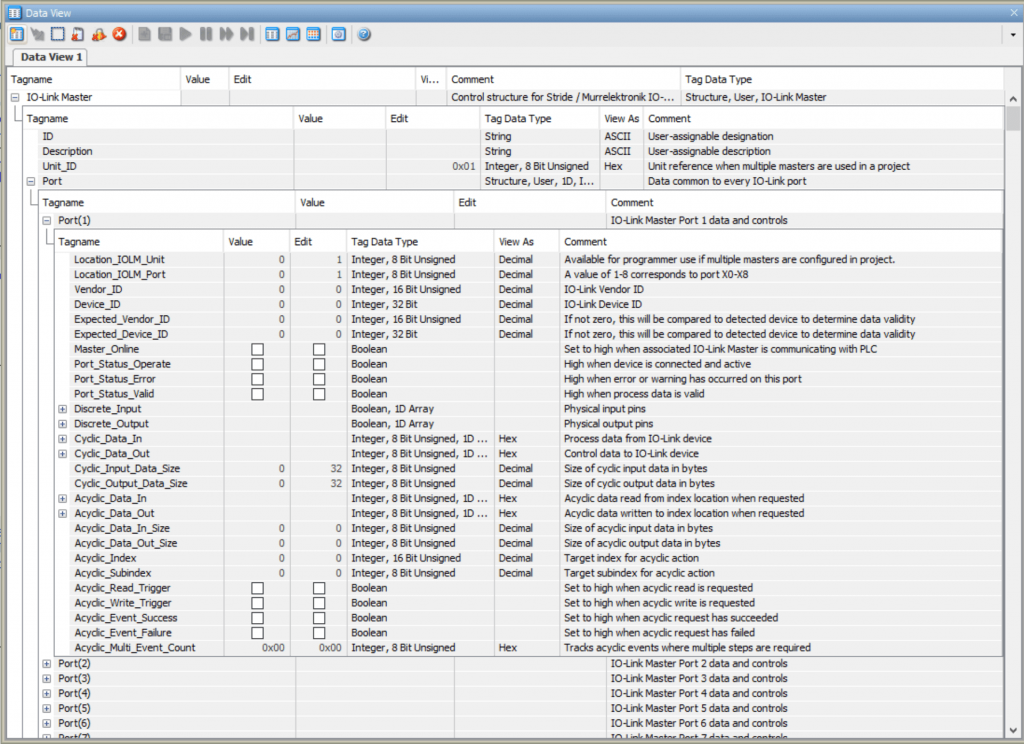
Expandable Options
IO-Link modules communicate field information up to a supervisory PLC using the standard EtherNet/IP protocol, and some modules support protocols like OPC UA and MQTT for IIoT applications, enabling direct connectivity from field sensors to the cloud. AutomationDirect Productivity Suite development software is designed to integrate smoothly with the STRIDE IO-Link master, providing easy tagname access to the extensive data found in field modules and devices. IO-Link enables new possibilities:
While most users are familiar with standard pushbuttons and indicator lights, there is a new style of IO-Link device with an integrated display consisting of a touch button with a central 4-digit display, surrounded by 16 multi-color LED segments. A controller can command all the display elements while monitoring the button. One small device takes the place of many and avoids the need for a full-size human-machine interface.
Smarter I/O
While traditional I/O connectivity remains useful, the new IO-Link system is rapidly becoming the right-sized approach for providing streamlined installations with advanced communications. The AutomationDirect website offers a wide variety of IO-Link master modules, hubs, and field sensors devices to help OEMs and end users easily create modern automation solutions with digital connectivity.