Linear actuators, driven with servo or stepper motors, are an effective way to implement accurate automated machine motion.
Chip McDaniel at AutomationDirect wrote an article for the January 2023 issue of Design World’s Linear Motion Tips. Titled A Straight Line to Effective Linear Motion, this article explains linear actuator technologies, and it shows how they can be efficiently integrated with servo and stepper motors to provide accurate motion control.
Linear actuators can also be driven by pneumatic or hydraulic methods, depending on the force, speed, accuracy, and cost requirements of an application. Electrically-driven actuators are the preferred solution for many applications, especially when automated by a PLC, or when IoT data connectivity is desired.
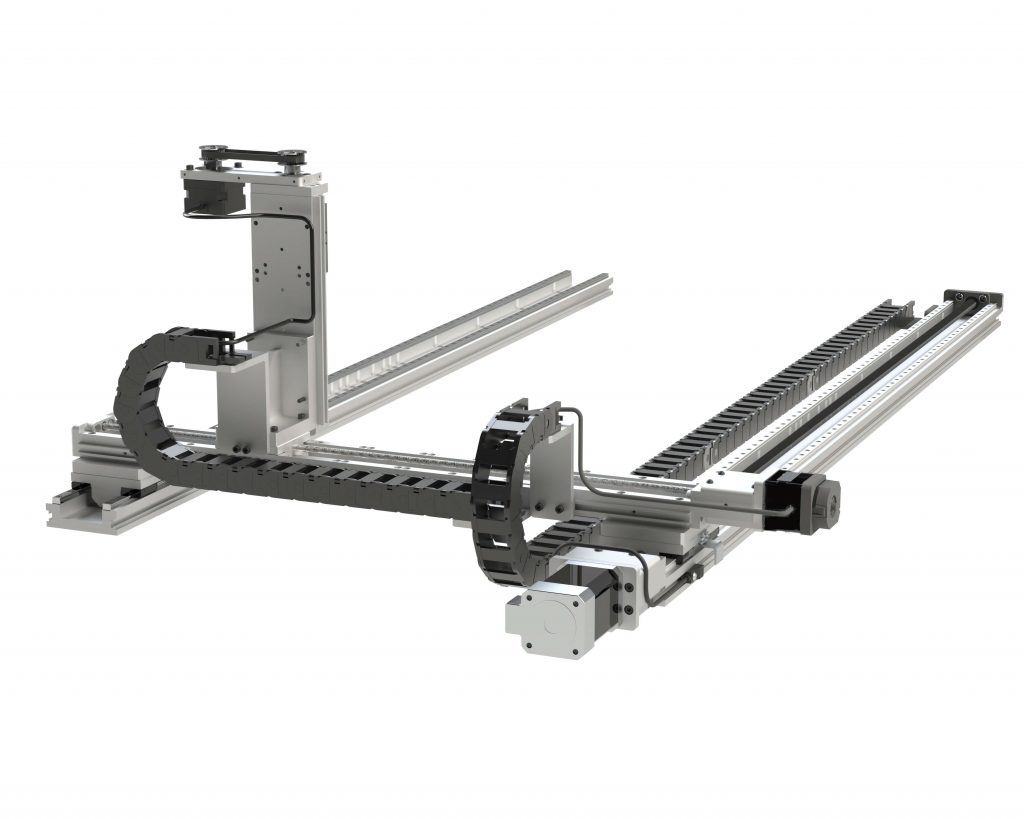
Linear motion basics
Linear motion on machinery is commonly needed for moving products or fixtures for machining and assembly operations, such as drilling, inserting, gluing, and taping. They are also essential for picking-and-placing parts into and out of trays and containers.
For these mechanical systems—sometimes called cartesian equipment or a gantry—the motion might be needed in a single “X” axis, or over an “X-Y” plane, or through a complete “X-Y-Z” area. Tools and grippers are what is typically moved. The design must consider forces, travel distance, end-of-travel (overtravel) provisions, and more to provide a complete solution. For many applications, PLC-driven actuators traveling at distances of a meter or less are ideal.
Actuator types
The most common off-the-shelf actuator types are:
- Lead screw driven: Low-cost option, uses a threaded shaft with a simple nut to move the carriage along a fixed base.
- Ball screw driven: A higher performance design using ball bearings to provide fast speeds and frequent duty cycles.
- Belt driven: Less precise than the other options, but able to travel over longer distances.
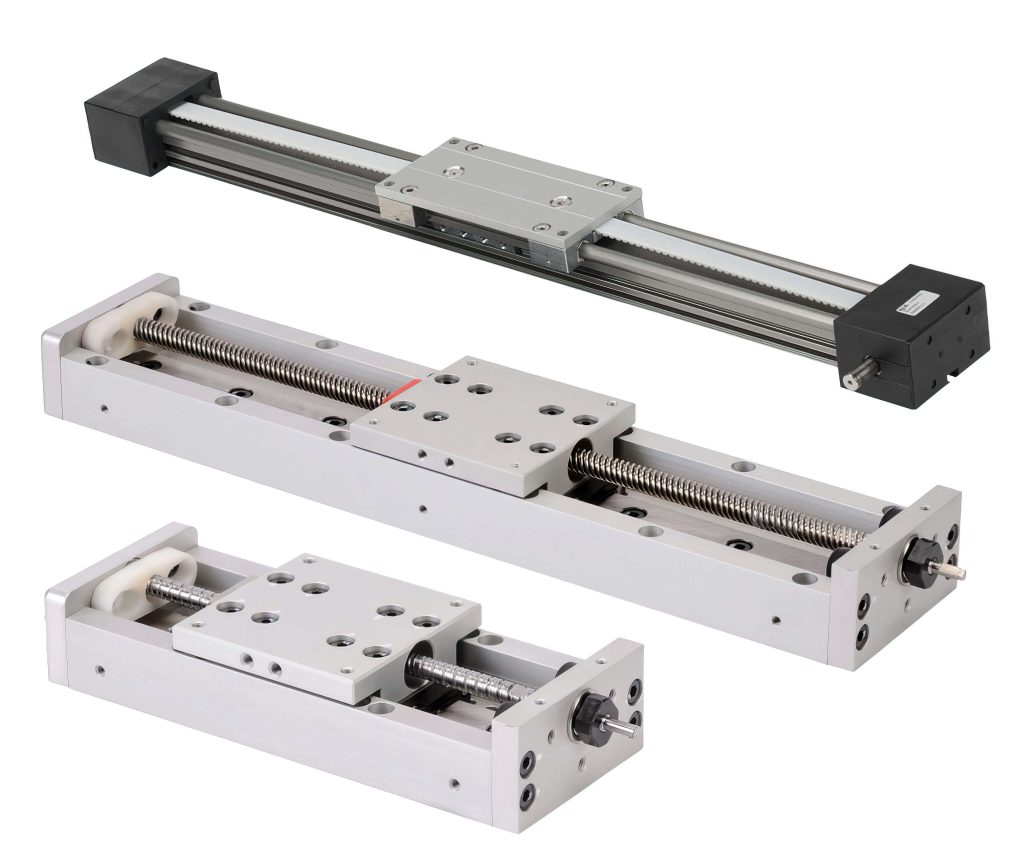
Drive details
Some linear actuators accept standard motor sizes, while others are available as complete packages with the motors. Stepper motors provide good accuracy as they move in small “steps” based on pulses from a motion controller or PLC, but they operate in an open-loop manner. Servo motors can precisely control position, velocity, and torque over complex motion profiles with closed-loop feedback, but they are correspondingly more expensive and complex.
PLC and IoT
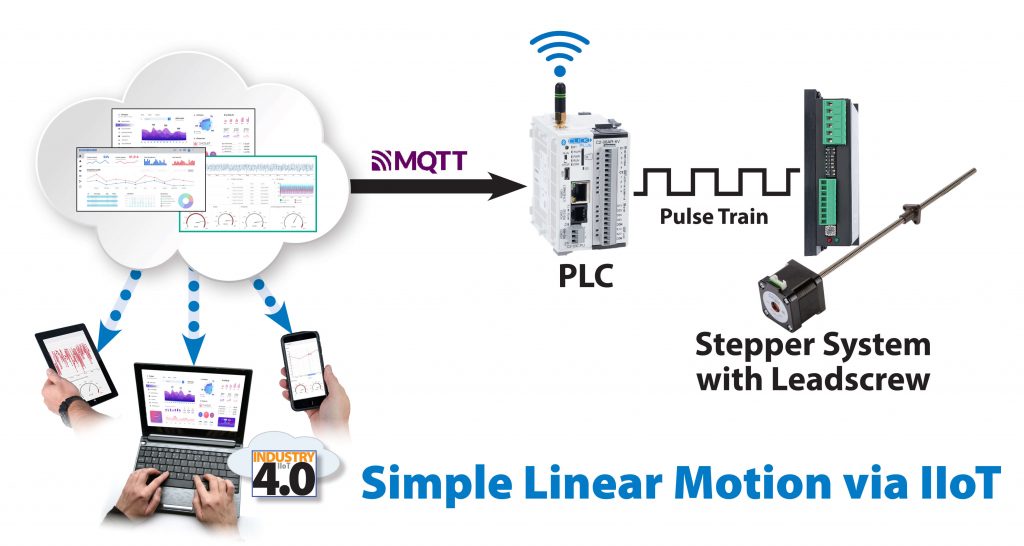
Most linear actuation systems require some other signals, such as overtravel and homing position sensors. “Homing” is the action of driving equipment to a known position to verify system calibration. Dedicated motion controllers are available, and some PLCs include motion control functionality.
Many users are finding that the AutomationDirect CLICK PLUS micro-PLC is a great option for adding comprehensive motion control and IoT communications to applications of all sizes. The CLICK PLUS offers high-speed pulse train outputs and straightforward motion control instructions to automate multi-axis homing, velocity, and position moves.
Linear actuators are essential for automated motion control of pick-and-place applications, industrial-grade machinery, and consumer-grade equipment.
Visit the AutomationDirect website to explore the complete portfolio of linear actuators, servos, steppers, motion controllers, and PLCs for implementing these types of systems.