Basic position sensing concepts take on added importance for precision applications because new issues must be considered.
Andrew Waugh, Product Manager for Sensor and Safety products at AutomationDirect, authored an article for the Nov 2019 issue of Design World titled When Precision Sensing Solutions are Critical. Here’s a summary, click on the link above for the full text.
Position sensing devices are commonly used in industrial automation solutions. Basic products like standard limit switches and proximity switches are excellent for sensing boxes on conveyors and equipment positions.
But for many industries, these types of devices aren’t good enough. High-tech manufacturing often calls for high precision position sensing, measured in hundredths of a millimeter or better. This article examines some high precision sensing solutions and shows how they can be applied.
How Good is Good?
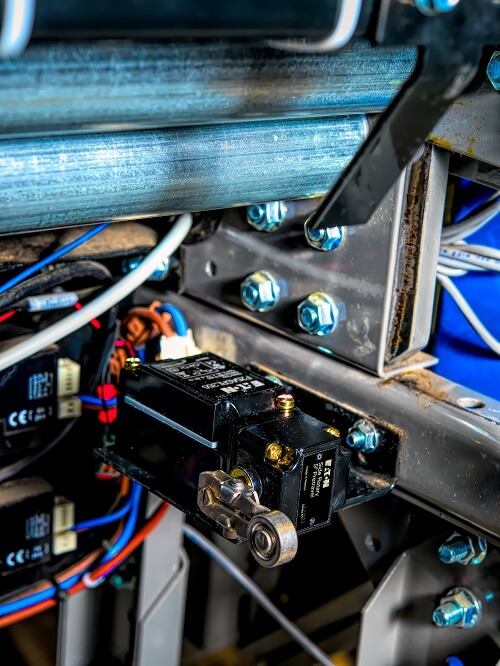
For sensing linear or angular position, designers want a limit switch that will repeatably and accurately respond at the same point when triggered. Standards limit switches, like mechanical NEMA styles, may provide a repeat accuracy of 0.05 mm or better. Non-contact proximity switches have other benefits, but repeatable accuracy is not one of them.
Precision Sensing Situations
Precision sensing applications are more specialized, often calling for a repeat accuracy of 0.0005 mm, which is 100 times better than most standard switches.
Consider any type of machining or milling equipment where the cutting tool is subject to wear. One way to detect this is to program the equipment to accurately position the cutting tool at a test position before or after it performs its typical task.
Parts assembly equipment for placing and fastening small components on delicate assemblies also needs precision sensing due to the very small distances involved.
Making the Right Touch
Physical limit switches, whether standard or precision type, provide a good solution at a relatively low cost but are 100% dependent on physically touching an object through motion. This makes them subject to wear and damage, and for some applications it may not be acceptable to touch a target for safety, temperature, or sanitary reasons.
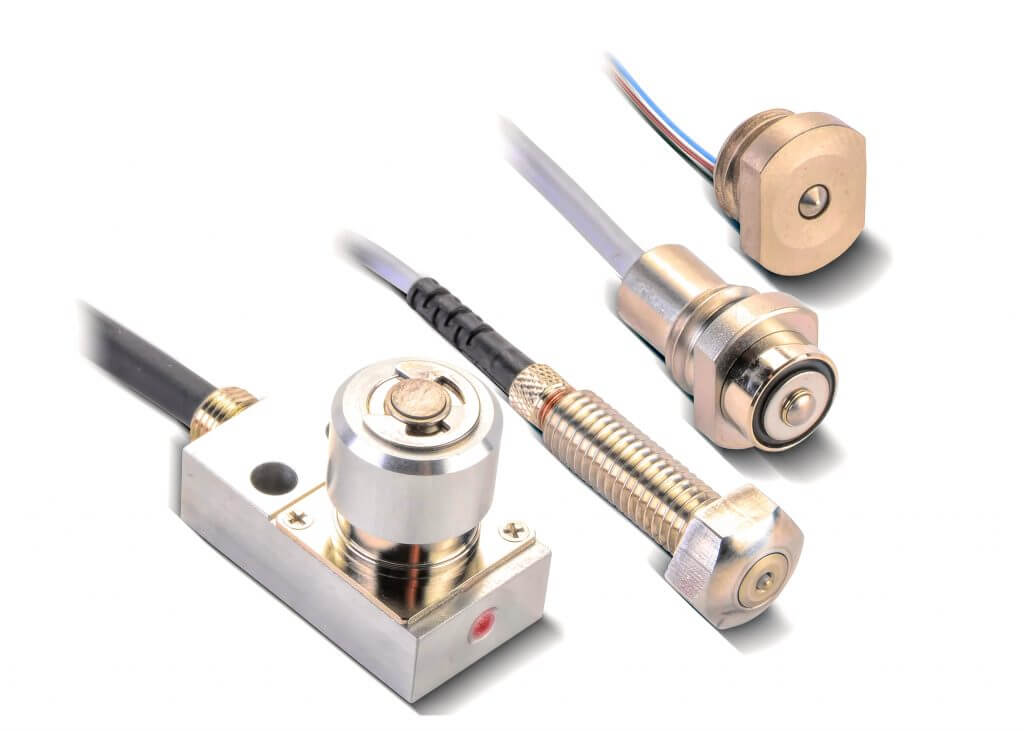
Non-Contact Precision Sensing
Standard non-contact technologies like opto-electronic and ultrasonic sensors excel at presence detecting, but not at repeatable accuracy. For high precision non-contact sensing, laser light sensors provide the best performance.
These devices can be mounted some distance away from the sensed part, avoiding contact with the part and also the environmental conditions. The major characteristics for any laser sensor are sensing range, resolution, and cost.
Basic laser sensors costing around $300 can provide 1 mm resolution at a range up to 3 m. For $600, a laser sensor might deliver 0.05 mm resolution at a reduced range of up to 350 mm, or even better 0.008 mm resolution at an even shorter range up to 80mm.
All in the Details
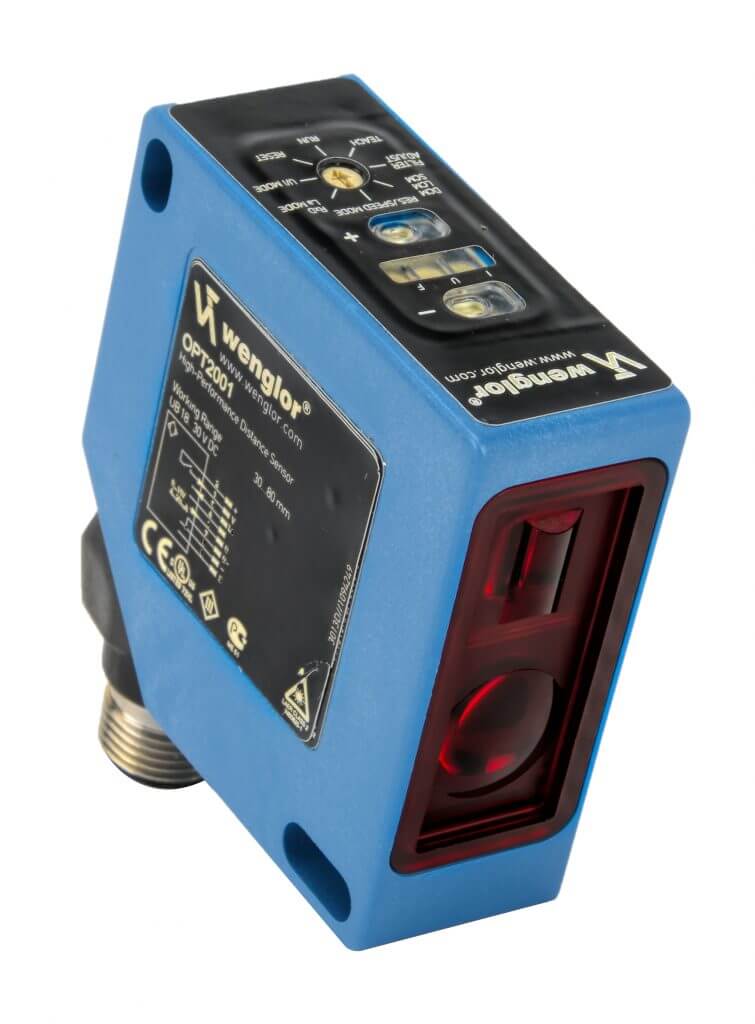
For precision sensing, there are four major areas of specifications to be considered:
- Performance
- Target
- Environment
- Interface
Performance includes previously mentioned items, along with response speed. Target angle, reflectivity, and color may affect measurement. Environmental conditions of temperature, contaminants, and vibrations must be considered or controlled for reliable measurement. Finally, more advanced sensors may provide a local user interface and the ability to transmit extended data using industrial communication protocols.
Combining Multiple Sensors
Laser sensors are often an excellent high precision non-contact solution, and multiple sensors of this type can be combined to determine full three-dimensional sizing information.
Many industries and applications demand high precision sensing. Options are available, but each requires attention to detail due to the delicate nature of the measurements.