New VFD features and technologies improve the control, safety, networking, and efficiency of motor control for a growing number of applications.
Jeff Payne, product manager for the drives & motors group at AutomationDirect, wrote an article for the June 2021 issue of Plant Services titled Advanced Variable Frequency Drives are Working in More Applications. Here’s a summary, click on the link above for the full text.
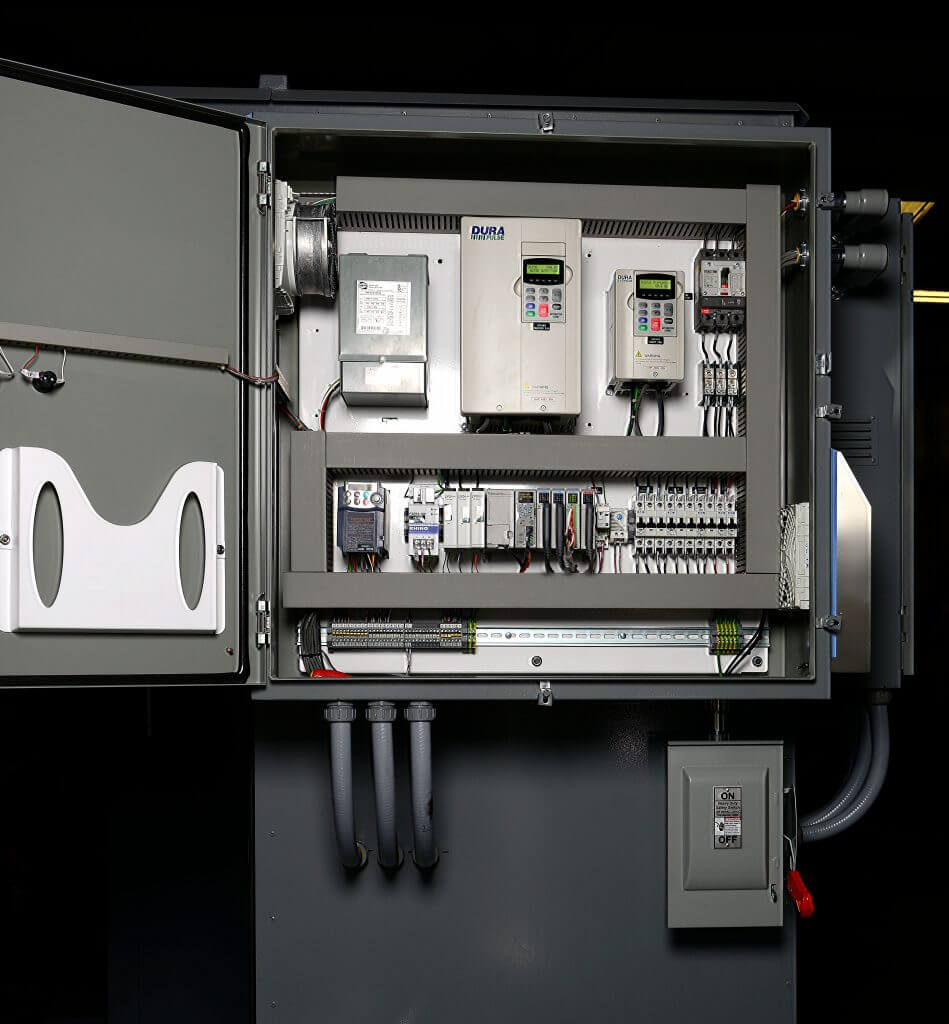
Although the first three-phase AC motor was patented by Nikola Tesla in 1888, it was the DC motor championed by Thomas Edison which remained the king of manufacturing during the first half of the twentieth century. This is because it was more practical to implement DC rather than AC speed control, but this changed as better methods became available to control AC motors.
In the world of alternating current (AC) motors and their associated shaft-turning applications across all industries, no components have made a greater impact than the AC variable frequency drive (VFD). The ability of VFDs to precisely control motor speed and torque, reduce overall energy consumption, and minimize equipment wear have opened the door to many applications that formerly required more complex and expensive electro-mechanical solutions.
Modern VFDs
Due to developments in semiconductor and computing technologies, todays VFDs have improved in many areas:
- More compact form factors
- Ability to operate motors of all sizes, at frequencies from 0 up to 400Hz
- Torque control can be applied up to 200% rated torque, even at low speeds down to 0.5Hz
- Digital controllers include built-in PLC functionality and other advanced functions
- Extensive data communication abilities
Improved Automation
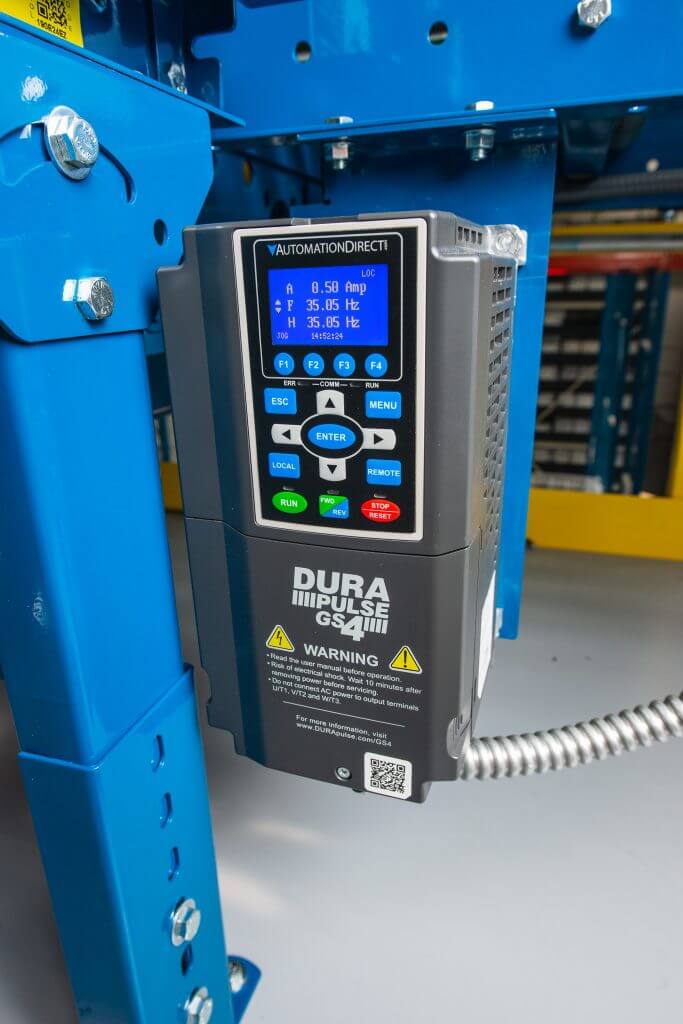
AC VFDs now deliver a wide range of capabilities:
- Performance: Auto-tuning, sensorless vector, field-oriented control, and closed loop flux vector control can be applied as dictated by the application to provide precise and almost servo-like control, at a fraction of the cost.
- Efficiency: Three-phase AC induction motors (IMs) are still the norm, but AC permanent magnet (PM) motors are becoming more commonplace and can provide maximum torque at 0RPM, with a smaller size and with greater efficiency.
- Safety: New VFDs include built-in safety related features like safe torque off, fire mode, safe stop modes, safe brake control, safely limited speed, safe direction, and safely limited acceleration.
- Connectivity: Beyond hardwired signals and industrial fieldbuses, today’s modern VFDs now work with various Ethernet protocols like Modbus TCP and EtherNet/IP. This is useful for command and status signaling, and it enables extensive diagnostics and configuration possibilities.
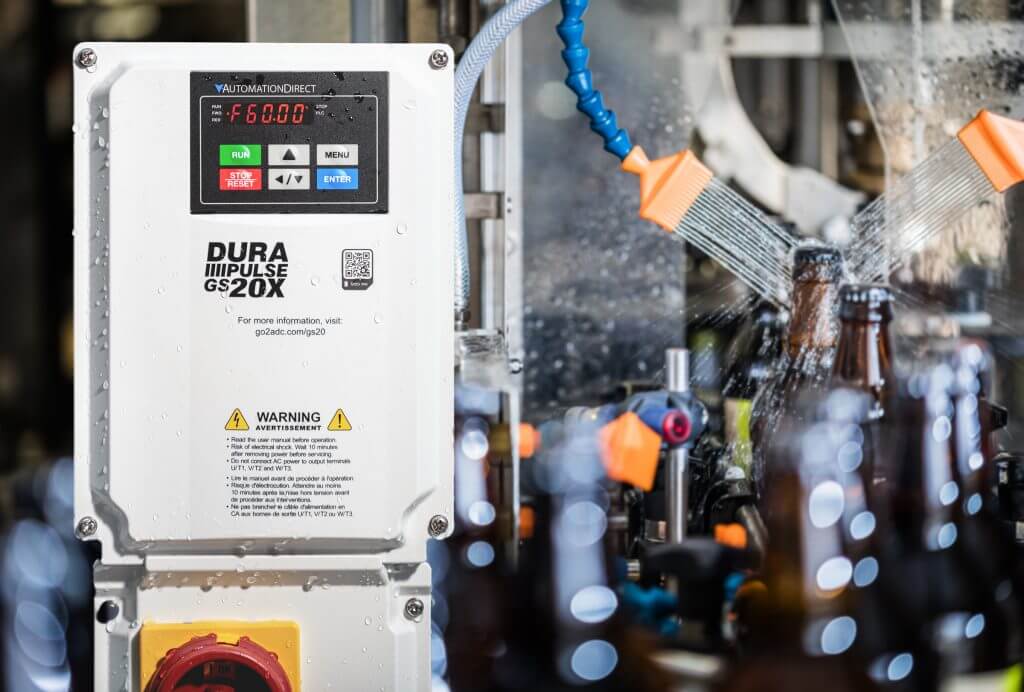
Modern VFDs are the Preferred Solution
Today’s VFDs benefit from decades of steady evolution, transitioning them from simple motor control devices into a comprehensive platform for delivering motor performance, efficiency, safety, and connectivity. Designers should familiarize themselves with these capabilities, and they can connect with AutomationDirect resources and support to learn how to take advantage of modern VFDs in their applications.